Chemical management goes digital
Since the industrial revolution, the oil and gas industry has played a fundamental role in global economic development, fueling power for heat, light, mobility and industrial operations. Over the last few decades, the industry has supplied key raw materials for a vast range of consumer products. Consistently at the forefront of new technological developments, operators are able to venture to new frontiers—inhospitable regions, deeper reserves, more remote locations and unconventional plays—traditionally thought to be beyond reach. Today, this same industry is on the cusp of overcoming boundaries and practices to, once again, redefine its future, Fig. 1.
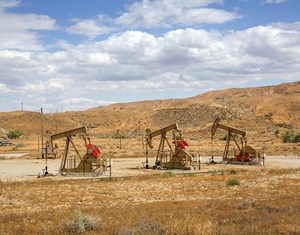
THE NEW ECONOMIC LANDSCAPE
After demand from emerging economies pushed oil prices to an unprecedented high in 2008, they went into a devastating free-fall when the global economic crisis curbed demand for energy, forcing oil and gas companies to rethink their operations, Fig. 2. This resulted in aggressive and wide-ranging cost-cutting, capital efficiency and ultra-lean operations.
Though oil prices have shown recent signs of recovery, analysts consider the business mechanics of oil and gas production deeply changed. Added to this, many companies have experienced only moderate operational gains involved in the extension of existing wellbores, extraction from harder-to-reach or declining reservoirs, environmental accountability and even knowledge transfer issues through the retirement of the current labor force. This has created an incentive, a mandate even, for producers to manage their assets smarter and more efficiently.
To survive and stay profitable, producers—who have focused primarily on high output to take advantage of strong prices and demand—are now more focused on efficiency and costs. The standard approach to downturns is no longer adequate. Ongoing pressures are prompting companies to speed up the adoption of digitally-enabled solutions, tackling challenges head-on while providing value to their stakeholders. The transformational shift is demanding dramatic changes in business models, workflow, and technology investment, which have given rise to what is now known as the digital oilfield.
OILFIELD CHEMICALS
The period over which oil is produced from a well can last several decades. During the drilling and throughout well life, chemicals play a vital role in hydrocarbon recovery. However, insufficient chemical management and supervision also can lead to malfunctions, leaks and spills that result in environmental or contractual fines, as well as conflicts with authorities and landowners, thus adding to the economic and production challenges already noted.
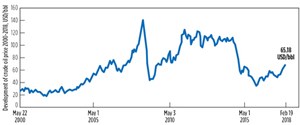
The chemicals being referred to are production chemicals. Unlike many other oilfield chemicals, they are mostly specialty chemicals that serve very precise purposes and are used in comparatively small volumes. They find application as important aids during the actual separation phase of crude, water and gas, and eventually transportation to the refinery.
Among the most important production chemicals are scale inhibitors, which are injected into the well to prevent the deposition of mineral scale on downhole casing, tubing and other equipment. Inhibitors that suppress the formation of gas hydrates and waxy or asphalt-like deposits are injected for similar reasons, keeping the well and its fluids free from materials that could hinder recovery. Corrosion inhibitors reduce the effects that flow stimulating acids may have on downhole pipework and above-ground components, while oxygen scavengers serve to mitigate corrosion in water injection equipment.
Other important production chemicals include demulsifiers, clarifiers, foamers, defoamers and biocides. For enhanced oil recovery (EOR), well service additives, also referred to as flowback aids, can be used to improve extraction from mature reserves and difficult formations. The mix of chemicals applied is usually designed specifically for each oil field and well. They can be dosed in large batches for single interventions, small regular batch additions or continuous injection. As the volume of produced fluid and other operating conditions changes, the selection and amount of chemicals used must be adjusted accordingly, and well conditions are monitored closely to assure optimal flow.
When compared to other economic factors, oilfield chemicals and related services make up a small part of so-called lifting costs—or the total cost of operating and maintaining a well after the reservoir has been found and made ready for production. According to estimates, the cost of chemicals and chemical services averages between 20 and 40 cents per lifted barrel, depending on the field.
However, oilfield chemicals can have a very large impact on total operating costs and profitability when their supply and application are not optimized. Failure to efficiently treat wells against corrosion or hydrate blockage, for example, can result in production downtime, causing losses in revenue and profit, as well as the substantial costs for repair and workover. The small decreases in flowrate, caused by scale, wax or other deposits, can translate into large losses of produced fluid over time, which may ultimately determine the viability of operations.
COMPLEXITY OF OILFIELD CHEMICAL MANAGEMENT
The various associated activities involved in oilfield chemical management also have the potential to add up, especially on large fields if not executed in the most efficient manner. This can apply to the long hours that chemical drivers and field technicians spend behind the wheel on service rounds (or so-called “windshield time”), but also to many other routine activities, such as documenting deliveries on paper or computer spreadsheets, or processing orders and invoices at the office.
If they want to remain viable, chemical service companies have no choice but to pass on such costs to customers. Additionally, the potential risks for staff and the environment that are inherent to the logistics of supplying a large network of wells with chemicals—as well as the manual labor involved in injecting or restocking them—can increase with each visit to a site.
On the production site, the complexity of chemical maintenance and order fulfilment results in the need for highly-competent personnel, to constantly monitor and verify the performance of services. Lack of visibility into these services and the data brings additional challenges for the producer, when needing to make the necessary decisions and measuring the success of the chemical program.
Decision-makers in oilfield chemicals management are looking to innovation and technology to improve efficiencies and cut costs. Using newly-available enabling technologies, such as low-cost sensors, big data analytics and cloud computing, companies are increasingly adopting innovations that range from digital fleet management and predictive maintenance to enhancements in field productivity.
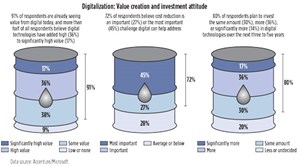
A new study by the International Energy Agency (IEA) estimates that just with the increase and widespread use of digital technologies already in existence, oil and gas companies could lower their production costs 10% to 20%. The agency bases this projection on assessments shared by upstream operators and service providers. IEA sees potential for even bigger cost reductions, if technologies that are only now emerging, especially those enhancing connectivity and monitoring, are working and find general acceptance.
In a joint Accenture and Microsoft survey among upstream companies during 2016, more than 90% stated that digital technology was already adding value to their business, and more than 70% saw cost reduction as an important, or even the most important, challenge that it could help address. About 80% of respondents said that despite the low-price environment, they planned to invest the same amount, or more, in digitalization in the near future, Fig. 3.
However, oil producers are trying to resolve a multitude of inter-connecting issues across the value chain by investing in a digital alternative that provides better efficiency, control and transparency. They are often faced with a perplexing myriad of separate hardware and software solutions that are difficult to integrate into existing systems. The traditional approach of selectively adopting a set of technologies and unsystematically implementing digitalization is no longer suitable.
DIGITIZATION: THE NEW ENABLER
Oil and gas companies have been employing stand-alone technologies to improve production operations for the past couple of decades. Clariant was one of the first companies to recognize the potential to develop a digital chemical management system, introducing its first iteration of VERITRAX almost a decade ago. Since then, the company has availed of the latest smartphone and Internet of Things (IoT) technologies available to fully digitize all field processes, Fig. 4.
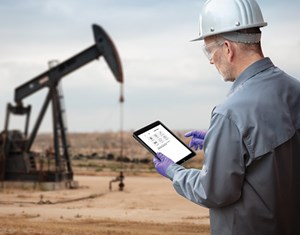
The system is a suite of hardware and software solutions that substantially increases efficiency and cost-effectiveness, while improving well integrity through predictive maintenance and mitigating risk through lower hazard exposure. By integrating all essential elements of production surveillance, control and analysis into a fully digitized, remotely operable and intelligent system, it optimizes processes on every level of oilfield management. A streamlined and fundamentally enhanced version of its field-proven 2009 predecessor, it has been informed by the experience of hundreds of oilfield chemical managers, who identified over 600 discrete processes that represent the best practices in Chemical Oilfield Management. The system represents a multi-million-dollar software investment and has been demonstrated to increase total oilfield performance by up to 15%.
It is used to schedule, monitor and report all aspects of oilfield services. This includes the scheduling and performing of deliveries and the posting of analytical tests, in addition to other multiple types of reporting. To fulfil its many different tasks, the system uses sensors and Industrial Internet of Things (IIoT) telemetry equipment installed at the oil well, in combination with highly sophisticated software for data entry, processing and distribution. This can be accessed via smartphones and many other cloud-connected devices. The security of the cloud-stored data is managed by a leading third-party cloud service provider, whose data centers are effectively safeguarded against cyber risks.
Clariant drivers and field technicians are equipped with smart phones and other mobile devices that help manage job lists and activities. When chemical deliveries are made or services are performed, the smartphone records date, time, GPS position and user ID, as well as details about the treatment and associated metadata, such as a well’s API number. For each visited site, the metering devices on the delivery trucks measure the exact amount of chemicals delivered. This information is saved and added to the delivery record for verification purposes, and is also provided to the oilfield operator, along with invoices.
Chemical tanks—both those used to supply delivery trucks and those for dosing at the well itself—are fitted with special sensors, so that the system can monitor the inventory. If tank levels are low, the system automatically places orders for replenishment and generates corresponding invoices. All chemical deliveries, including batch deliveries injected into pipelines or dosing points, are scheduled automatically by the system, which continually calculates the most efficient job lists and itineraries. Alerts can be configured individually and can interact intelligently with the recipient.
Aside from chemical needs, the system also forecasts service requirements, such as pump repair and calibration. VERITRAX can be linked to the producer’s SCADA system or time-based process recording program, allowing the coupling of chemical data with production data to provide accurate, total performance correlations.
Through integration with SAP, the system also can provide precise warehouse forecasting. It automatically sends invoices to the enterprise resource planning (ERP) system of the serviced oil and gas producer. The VERITRAX Customer Dashboard is updated every five minutes from the Cloud, allowing customers to access data in real time through this web application, specifically developed for chemical management.
The system also integrates the analytical testing performed on well fluids, to determine the need for chemical adaptations and anticipate potential well failures. Field technicians attach a barcode to each sample taken at a wellhead, pipeline or oil and gas separator. They enter the sample into the system by scanning the code, as well as other data, like photos or comments. Samples are then tracked to the laboratory. Test results and analyzed reports are then made available to both the technician and customer via the dashboard.
BENEFITS IN THE FIELD
VERITRAX reduces the driving hours and manual handling that chemical management has traditionally involved by providing the time- and effort-saving convenience of digital supervision and control. Replacing weekly drives out to well sites to measure chemical tank levels and monitor proper functioning of pumps, field technicians can now perform these tasks remotely.
Similarly, if remotely controlled chemical pumps are used, visits for adjustment purposes can be reduced significantly. The system also prevents over-frequent chemical deliveries that drivers often undertake to be on the “safe side.” Field personnel are also relieved of laborious record-keeping.
All of this reduces risks of gaps in chemical treatment programs, which can lead to production shutdowns and increased workover costs, as already stated. Staff safety is reduced by mitigating exposure to potential hazards, such as chemical, mechanical or driving accidents. At the same time, the enhanced transparency and reliability of chemical programs lowers the risk of well failures, due to chemical stockouts or equipment malfunctions, helping to maximize production uptime and profitability. Easier monitoring also reduces the risk of leaks and spills, and the potential environmental, regulatory and contractual consequences that can result, Fig. 4.
OFFSHORE SOLUTIONS
Targeted to be part of an oil and gas company’s digital transformation journey, Clariant is also introducing VERITRAX for applications in both onshore and offshore operations. Logging incoming data and processing them through a series of KPI evaluations, the system provides a comprehensive and real-time overview of the risk profile for subsea and wells, chemical handling, and facilities and export, allowing personnel to focus on problem resolution and optimizing operations, rather than data collection.
CONCLUSION
Digital transformation is altering the way that industries operate, on a scale comparable to major industrial revolutions of the past. While it has tremendous potential to benefit the industry, to unlock its full value, companies need to work with experienced and trusted partners that have proven digital system solutions.
Out in the field, VERITRAX greatly reduces the need for time-intensive, risk-increasing well visits and laborious manual data collection, while also minimizing the economic and environmental hazards associated with leaks, blockages and equipment malfunctions. In the lab, it provides near real-time analytical data and production histories that offer unprecedented insight into the effectiveness of chemical maintenance programs. In management and accounting offices, the solution affords a new level of control over all aspects of chemical servicing, supply and billing that puts provider-client relations on a more transparent, mutually profitable basis.
- What's new in production (February 2024)
- U.S. operators reduce activity as crude prices plunge (February 2024)
- U.S. producing gas wells increase despite low prices (February 2024)
- U.S. oil and natural gas production hits record highs (February 2024)
- Dallas Fed: E&P activity essentially unchanged; optimism wanes as uncertainty jumps (January 2024)
- Enhancing preparedness: The critical role of well control system surveys (December 2023)
- Applying ultra-deep LWD resistivity technology successfully in a SAGD operation (May 2019)
- Adoption of wireless intelligent completions advances (May 2019)
- Majors double down as takeaway crunch eases (April 2019)
- What’s new in well logging and formation evaluation (April 2019)
- Qualification of a 20,000-psi subsea BOP: A collaborative approach (February 2019)
- ConocoPhillips’ Greg Leveille sees rapid trajectory of technical advancement continuing (February 2019)