Technology from Europe:
France/Belgium
Rubber material developed for SCR flexible joints
Jean-Pierre Chaumieau, Techlam S.A., and Jacques Rey, SNECMA Propulsion Solide, Cernay, France
TECHLAM is developing and qualifying a new flexible joint concept, FSDB (Fail-Safe Double-Barrier), which requires adapted cover rubber materials. Due to stringent deepwater specifications for single catenary riser (SCR) flexible joints, The company and its parent company, SNECMA Propulsion Solide, are developing a new, specific HNBR (Hydrogenated Acrylonitrile Butadiene Rubber) compound. This compound handles a wide range of high-pressure/ high-temperature (HP/HT) applications, including oil and gas with H2S and CO2 content.
RUBBER COMPOUND
For safety margins, the rubber material must sustain a minimum, 400% shear at break (for a 1-MPa shear modulus) and a suitable fatigue resistance at the operating temperature. Operating temperature ranges between 4°C (on the seabed) and 130°C (extreme level in production risers), and a radial temperature profile is created inside the rubber layer. Because the rubber will age, one must predict its mechanical behavior during a typical, 25-year operating life.
The rubber may come in contact with oil, gas, injection chemicals (methanol, corrosion inhibitors) and seawater. In all cases, some fluid making contact diffuses into the rubber, up to an equilibrium point. This leads to local modification of properties (which may be physical) but it may also generate a chemical transformation (due to an H2S presence, for instance). A fast pressure drop may occur in the risers, so it is necessary to investigate the explosive decompression (ED) effect inside the rubber.
Manufacturing requirements. Rubber formulation includes a mixing operation and a calendering phase (a phase of pressing the material between rollers). In turn, prior to curing, viscosity is adapted to the molding process, to achieve a curing behavior compatible with the mold's thermal inertia. This also satisfies bonding requirements, per the curing cycle's thermal conditions.
HNBR material. HNBR compounds have been developed over the last 25 years, formulated from total or partial NBR (acryloNitrile butadiene rubber) hydrogenation. Use of HNBR rubber compounds increases the range of potential applications:
- Higher operating temperatures, for new production risers
- Better physical-chemical resistance, to enhance service life
- Use of either the conventional flexible connection (single flexible joint) or the proprietary FSDB concept.
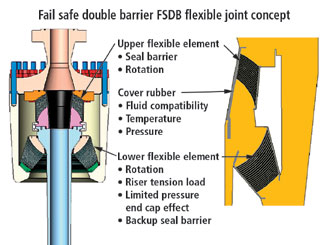 |
The FSDB concept relies on new rubber compounds to address stringent, deepwater specifications for SCR flexible joints.
|
|
DEVELOPMENT/QUALIFICATION
Evaluation of explosive decompression behavior relates to the field-proven HNBR compound used for development projects (as in 16-in. FPSO export lines and loading buoy, flexible connections at Total's Girassol field, offshore Angola). A series of fast decompressions was performed on 1-mm and 3-mm-thick, 60 x 55-mm cover rubber samples. Samples were pre-stressed in compression, to simulate the shear rate on sample edges closest to the rate realized on the full-sized, flexible component rubber layer.
Samples placed in the aging reactor were 85% CH4 (methane) and 15% CO2, at 80°C operating temperature and 15-MPa operating pressure. Then, 20 decompression cycles were performed at a minimum decompression rate of 7 MPa/min. Samples were sheared at break, at room temperature during the initial stage. Other samples were sheared after five, 10, 15 and 20 decompression cycles.
After 20 cycles, the cover rubber's integrity was preserved, and bonding to steel shims was maintained at 100%. Only some micro-porous blisters appear in the cover rubber. After 20 decompression cycles, shear properties at break were lowered 25% to 30%. This deterioration occurred after the first five cycles, but then it stabilized.
RUBBER OPTIMIZATION
Placed in direct contact with liquid and gaseous hydrocarbons, the cover rubber must resist the most severe environments typically found in production risers, particularly accidental de-pressurization and sour conditions (H2S content). Meanwhile, compared to active rubber layers in the laminated component, large deformations are not found at the cover rubber level. Therefore, one can separate the functions and optimize the HNBR cover formulation when maintaining compatibility with the rubber layer compound.
ED resistance of the HNBR compounds to various production riser fluids is optimized. Although it originally had a limited rupture value at break, the optimized cover rubber shows an excellent mechanical resistance after ED ageing, maintaining its features. Thus, the opportunity to optimize the HNBR compound's local properties is used profitably for the new FSDB concept. This makes it suitable for the HPHT applications under development. 
|