Wellbore seal control and monitoring enhance deepwater MPD operations
Managed Pressure Drilling (MPD) provides a variety of benefits to a drilling operation. MPD isolates the wellbore from the atmosphere, enabling rapid adjustments of wellbore pressure to improve downhole pressure control.
In the closed-loop drilling system, advanced flow metering devices are more readily adapted to measure volumetric and mass flowrates of returns, improving kick detection and well feedback. With better feedback mechanisms, the rig may be able to detect kicks faster, leading to reduced kick response time and total influx volume. Furthermore, upon detecting a kick, the crew may increase the back pressure to stop kick growth prior to closing the blowout preventer (BOP).
RCD SYSTEMS
To implement an applied surface backpressure (ASBP)-MPD system, rigs have historically used passive sealing systems, such as a rotating control device (RCD). RCD systems vary in complexity but share most of the same basic features. An RCD consists of a housing and a seal assembly. The housing includes a latching mechanism to retain the seal assembly and ports for the return flow, and it is integrated into the drilling riser or affixed to the top of a surface BOP stack.
The seal assembly consists, in part, of a bearing assembly and an RCD seal element. The RCD seal element is typically elastomeric, with an opening slightly smaller than the drill pipe body to grip the drill pipe. One or more seal elements are attached to the rotating portion of a bearing assembly, while rotary seals seal between the rotating and non-rotating portions. External static seals are installed on the outside of the bearing assembly, to seal the space between the bearing assembly and the housing. The seal element is specially designed to allow the element to stretch, as drill pipe tool joints pass through.
Similar operating principles govern RCD systems. When circulation commences, the RCD seal assembly obstructs the annular fluid. The seal element rotates with the drillstring, to reduce wear on the element. There are no means to adjust the seal, so if the element fails to maintain a pressure-tight seal, the entire assembly must be replaced. The design of an RCD does not support direct monitoring of the seal condition, so the rig must remain ready to stop operations, to replace a bearing assembly, if required. Furthermore, unexpected failure of the RCD system to maintain a wellbore seal may occur due to a worn seal element, torn seal element or failed bearing assembly.
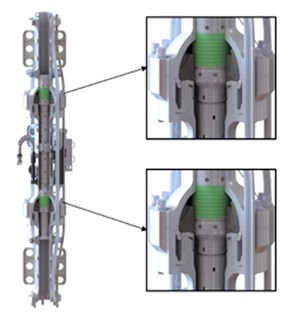
While this general design has the advantage of a short stack height, it has the disadvantage of parallel failure modes between the element, the bearing and all rotary and static seals. In practice, the operation of passive RCDs in deepwater drilling is more complex and costly, due to additional protective sleeves in non-MPD sections and requirements for highly specialized running tools. In the offshore environment, the stack-up height in the riser is much less of a constraint, making the primary benefit of RCDs less pronounced. In deepwater, superior seal life and seal quality are of higher importance, due to higher daily costs.
NOV developed an active control device (ACD) (Fig. 1) to address the limitations of passive sealing devices in deep water. The active control device uses dual spherical annular packer elements—similar to those found in a BOP—to actuate a dual, non-rotating seal sleeve element. An active control system, which enables closing pressure monitoring and optimization over the life of the seal sleeve element, controls the annular packers. Two seal sleeve elements are made up into a seal sleeve assembly, which drillstring-deployed tools run and retrieve. The seal sleeve elements use a unique co-molding construction technique, in which a wear-resistant polytetrafluoroethylene (PTFE) honeycomb insert is molded with a flexible polyurethane buffer material. The system contains no rotating parts and uses a durable polymer seal insert to absorb the wear caused by pipe motion within the element.
The active control device is part of a larger MPD system, as illustrated in Fig. 2. An ACD typically forms a portion of an MPD specialty joint that runs in the drilling riser, just below the termination joint. The MPD specialty joint includes an ACD, a drillstring isolation tool (DSIT), and a flow spool. When the ACD or DSIT annular packers are closed, returning drilling fluid is diverted through a pair of API 17K hoses to the MPD manifold at the surface. Additional support equipment, such as the hydraulic power unit (HPU) and umbilical reel, provides power and communications to the subsea joint.
The seal sleeve elements run relaxed in the hole. In contrast, passive RCD elements use an interference fit to create a seal, meaning that the element is subject to wear from the moment the drill pipe is inserted. When the annular packers close on the outer surface of the elements, the element elastomers bend inward, and the wear-resistant PTFE insert makes contact with the drillstring. The polyurethane supports the PTFE insert and provides a buffer material between the packer and the seal insert.
A closed-loop, direct-hydraulic active control system operates the active control device. All control valves reside at the surface, within reach when service is necessary. An umbilical system combines control and communications functions, using a single termination head. The closed-loop design allows the use of optimal hydraulic fluids to function the subsea joints while reducing the risk of contamination.
With the seal assembly in place, closing the active control device annular packers closes the seal sleeve elements against the drillstring. The upper and lower packer closing pressures adjust independently. Initial closing pressures are prescribed for each packer, based on the expected wellbore pressure at the surface, and the closing pressure applied to the seal sleeve elements is adjusted, as needed. The active control system maintains the required closing force, while the PTFE seal insert gradually wears. As a seal element wears, a higher closing pressure is applied to maintain seal integrity, as the annular packer operating it moves to a more closed position.
CONDITION MONITORING
The combined use of the active control system with the co-molded seal sleeve insert enables the system to detect and alert the crew when the PTFE seal insert is worn away. The seal wear state indicator alerts the rig crew that the seal assembly should be replaced soon. A lubrication system is provided to enable seal condition monitoring. The lubrication system draws drilling fluid from the active mud system for injection into the cavity formed between the upper and lower seal sleeves.
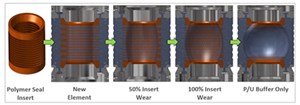
During drilling operations, the packer closing pressures are precisely controlled, to maintain the lubrication chamber pressure just above the wellbore pressure. Fluid lubricating the lower seal sleeve element joins the well returns, while fluid lubricating the upper seal sleeve element collects in the trip tank. As the seal material wears away, the seal element geometry changes, reducing the wall thickness of the element from the inside out, as shown in Fig. 3.
When the PTFE insert wears through, the PTFE’s contribution to closing pressure fades. The PTFE insert and the polyurethane buffer material have notably different material properties; whereas the PTFE is more rigid, the polyurethane is more flexible. Once the PTFE is worn away, the polyurethane makes contact with the drillstring. The greater flexibility of the polyurethane requires the application of higher closing pressure to contain the same lubrication pressure as the PTFE. This sudden loss of lubrication pressure and the shift in the required closing pressure inform the system that the PTFE has worn away. However, it is noteworthy that even when the element reaches a worn state, it can still seal the well.
TESTING
The API Specification 16RCD provides a standardized approach to testing RCDs. However, API 16RCD tests are designed to test different aspects of rotating pressure-containing devices separately, so the seal assembly is often replaced between stripping and rotational tests. This provides limited information on how the system should perform in the field. Before field operations, design verification testing of the active control device was performed, in accordance with the rating test requirements specified in API Specification 16RCD. Under the 16RCD licensing testing requirements, the active control device holds a 1,500-psi dynamic pressure rating, at 160 revolutions per minute (RPM) drillstring rotation, and a 1,000-psi stripping pressure rating.
Further design verification testing and system optimization of the active control device were performed at a fit-for-purpose, full-scale test rig in Willis, Texas. The test rig facility enables the performance of advanced drill mode testing and stripping mode testing protocols, which far exceed the standard testing requirements. The performance of these test protocols enables clients to define an operating envelope and measure system performance and seal wear, prior to going to the field. This ability helped reduce adoption risks and improve confidence in the active control device performance before field deployment, ensuring the equipment was project ready.
Furthermore, drill mode testing provides a standardized and pragmatic approach to quantifying and optimizing seal performance. The seal life optimization program uses the drill mode test format to trial alternate control system modes against previous baseline trials. Drill mode testing also enables validation of control system functionality and testing of automation against established benchmark tests.
FIELD OPERATIONS
The integration scope for the MPD project included equipment and control system integration with the rig’s drilling control system and the driller’s chair. Upon arriving at the rig, the lubrication system feeding the ACD was arranged in an open loop circuit, in which the lubrication system draws directly from the active mud pits. Mud is then injected into the chamber between the ACD seal elements. The operator and drilling contractor selected multiple equipment and service providers for the project, requiring cooperation between various parties.
Upon completion of the systems integration and commissioning scope, responsibilities for operation and maintenance were handed over to the rig. As the crew became more familiar with the system, the commissioning support crew head count gradually reduced to zero. The framework in Fig. 4 illustrates the general roadmap for control system integration.
The ACD system helped the operator reach the deep success case, allowing the crew to navigate a narrow and uncertain drilling window, while drilling close to the maximum permitted depth of the well with zero recordable safety incidents. The ACD sealing system held annular surface pressure as high as 500 psi while drilling and 600 psi during connections, as required by the well plan, performing in line with passive RCD equipment on the first well. In the first well, the longest single run included 20,000 ft of stripping pipe and nearly 4,000 ft of drilling in the open hole, with the seal sleeve closed. Also, during the first well, the crew became familiar with the running and retrieval tools, so replacing the seal assembly took less than 30 min.
The after-action review identified lubrication pump life as a focus area. Although the lubrication was deactivated during portions of the drilling operation, the ACD system was able to seal the well and allow operations to continue without downtime. After the first well, alterations to the lubrication system were implemented. To prevent fluid bypassing the lubrication pump, the lineup of the lubrication pump was adjusted to gravity feed clean fluid from a trip tank, while the returns were lined up to the opposite trip tank. This method is referred to as the closed-loop method.
As the supply tank drains, it is periodically refilled, whereas the return tank is periodically drained back to the shakers, to recycle the mud. The short packer life of the lubrication pump was also observed in the first well. Between well testing was performed at the test rig, but it could not replicate the shorter packing life observed. Instead, emphasis was placed on testing existing off-the-shelf triplex pump packing designs in the field.
Additional emphasis has been placed on providing a real-time indication of the remaining seal sleeve life. A new approach to tracking seal performance uses electronic drilling data to account for the combined effects of pipe motion on the seal elements in context with the applied closing pressure. This approach compares current operating conditions to past runs, to provide the rig with an estimate of the seal element’s remaining life.
CONCLUSION
Since the introduction of the ACD in 2019, multiple systems have been deployed globally in basins in the Black Sea, Gulf of Mexico, and South Atlantic. The ACD has been used to perform a variety of drilling operations including drilling, stripping tapered strings, sidetracking, running liners, and cementing. While passive RCDs are near peak technology after decades of modification, the ACD system is at the beginning of the development cycle, realizing performance gains with each new well drilled. The adaptability of the ACD technology makes it an ideal candidate for closed-loop drilling operations, including controlled mud level (CML) dual-gradient drilling, and it enables other next-generation drilling technologies.

- Advancing offshore decarbonization through electrification of FPSOs (March 2024)
- Subsea technology- Corrosion monitoring: From failure to success (February 2024)
- Driving MPD adoption with performance-enhancing technologies (January 2024)
- Digital transformation: A breakthrough year for digitalization in the offshore sector (January 2024)
- Offshore technology: Platform design: Is the next generation of offshore platforms changing offshore energy? (December 2023)
- 2024: A policy crossroads for American offshore energy (December 2023)
- Applying ultra-deep LWD resistivity technology successfully in a SAGD operation (May 2019)
- Adoption of wireless intelligent completions advances (May 2019)
- Majors double down as takeaway crunch eases (April 2019)
- What’s new in well logging and formation evaluation (April 2019)
- Qualification of a 20,000-psi subsea BOP: A collaborative approach (February 2019)
- ConocoPhillips’ Greg Leveille sees rapid trajectory of technical advancement continuing (February 2019)