Digital transformation: Putting people in the driving seat of digital uptake and scalability
The introduction of digital technologies, such as automation, machine learning, and AI, to the oil and gas industry is accelerating the pace and promise of achieving enhanced productivity and profitability. However, low rates of adoption prevail, putting digital maturity stubbornly below benchmarked industries.1
A stark example is that as recently as 2019, all 28 UKCS project sites under analysis depended on traditional paper-based processes to manage and monitor day-to-day activities. A recent survey report by OEUK identified three drawbacks holding back a full digital revolution: the prevalence of legacy systems; complexity of the industry; and a risk-averse culture.2
Using the introduction of Advanced Work Packaging (AWP) software across 28 brownfield project sites as an example, Petrofac and MODS deployed ADKAR, (Awareness, Desire, Knowledge, Ability, Reinforcement), a proven change management tool, to better understand and overcome the obstacles, preventing the acceptance and optimized use of this cloud-based solution. Two case studies clearly demonstrated that the willingness of personnel to embrace progressive innovation is at least as influential as the merits of the technology itself.
THE DIGITAL ADOPTION DILEMMA
Countless companies have initiated digitization projects to streamline workflows, improve construction and operations, and advance maintenance efficiencies. However, while many digital technologies have been introduced, only around 30% successfully passed the pilot phase and are firmly entrenched in the workplace.3 Research points to cultural and organizational barriers that may deter uptake and scalability of viable and proven solutions. These include:
- Digital technologies and their use cases do not consistently demonstrate clear value.
- Employees using the technologies may be resistant to change, even if managers support digitalization.
- The actual integration of new digital tools into dated, dependable work practices is given little consideration.
Overturning trusted, tried and tested ways of working into advanced, digital practices can only be achieved through alignment of people, processes, and technology.
The issue lies in the fact that organizations, particularly in the oil and gas industry, focus on the technological impact more than the human impetus. Yet, the people component is a pervasive pressure point. As the ultimate users of new technological tools, people need to work hard to change mindsets, develop new skills, embrace new processes, and alter established working practices. Without the right incentives, motivation and support, employee buy-in becomes challenging; adoption rates will be low, and ROI will be poor.
A prime example is when drivers started adopting SatNav as a replacement for cumbersome, outdated navigation methods, such as paper maps. The turning point came when a desire to be more efficient trumped fear of change.
To maximize the ROI of new technologies, there should be as much focus on how the end-users adapt to the technology, as there is on the development of the technology itself.
DIGITAL DIVIDE: BROWNFIELD VS. GREENFIELD
Digitalizing brownfield project delivery at an organizational level has historically proven elusive, particularly during the construction phase.
As brownfield project execution is typically smaller in both scope and capital, compared to greenfield, it is often constrained to employing in situ methods, systems and processes. With the requirement for more predictable project execution, existing AWP solutions are, therefore, not easily translated or implemented across brownfield assets. In addition, when trying to amalgamate archival installation and construction information with new, advanced technologies, the approach tends to be more piecemeal and less holistic.
Regardless, as an agnostic technology, AWP software is now considered an industry best practice for EPC projects, as it can integrate with any archival digital system, whether off-the-shelf or proprietary, to import any, and all, legacy information. The potential benefits, in terms of productivity and project performance, make it worth considering.4 Adopting new ways of overseeing, managing and executing construction and maintenance workflows can help tackle around 40% of global greenhouse gas emissions and save the global economy $1.6 trillion every year.5 It also could increase the construction sector’s efficiency by 60%.6
The overall transition from manual to digital can be supported by applying the ADKAR Change Management Model to ensure the human element is emphasized in partnership with the introduction of technology.
ANALYZING DIGITAL ADOPTION
The ADKAR model provides businesses with a roadmap for the successful uptake and scalability of any new technological solution. It is focused on outcomes across a five-step process for continuous improvement:7
- Awareness: Emphasize the need to change and convince users that this is positive
- Desire: Cultivate support and persuade personnel that this transformation is necessary
- Knowledge: Educate the workforce on how to adopt and adapt to the changeover
- Ability: Empower employees with the skills to adapt to and accept the new system or process
- Reinforcement: Create a positive feedback loop where user input is valued and actioned.
The first two steps, “awareness” and “desire,” apply to the current status quo situation, while the following two steps, “knowledge” and “ability,” relate to the transition phase. The final step, “reinforcement,” concerns any future scenario.
Continuous improvement in a digital transformation journey would view ADKAR as a continuous loop: when the future scenario is achieved, a new set of outcomes is identified, as demonstrated in Fig. 1.
Following a collaboration between Petrofac and leading software developer MODS, ADKAR was applied to understand the challenges of adopting and integrating AWP tools across 28 brownfield assets in the UKCS, as well as recommending remedial next steps, Fig. 2. The 28 brownfield sites had achieved varying levels of digital transformation, and two case studies from both sides of the spectrum were selected for discussion.
The study began by examining the existing digital approaches to four key workflows within a typical brownfield project execution model: work packages, materials management, completions, and reporting.
Case study 1: Desire for change stalls. At the outset, higher-level, strategic decision-makers identified which projects and assets would initiate their digital transformation journey. Initial conversations with upper-level management were promising. On the surface, “awareness” of, and a “desire” for, the benefits of digitalization to improve brownfield construction efficiency was apparent. However, for ADKAR to advance fully over five steps, all impacted parties must be active and willing participants.
The stumbling block in this instance was in cultivating the same motivation amongst middle management and engineering personnel. They demonstrated far less willingness to change their current way of working relative to their upper-management counterparts, because it affected and altered the way they would normally work. By putting up barriers to change, this reverberated back to Petrofac and MODS and, paradoxically, created more inefficiencies by changing their preferred processes to suit the client/owner. The engineers’ and middle management’s resistance to change resulted in negligible uptake of the digital tool and manual/paper processing resumed.
To cultivate an eagerness for change, a dual top-down and bottom-up approach is best. This needs to be an active process, whereby a case is made for how the change will make people’s jobs easier and improve their performance. It is downstream middle management through to the end users who will become ambassadors for uptake of a new system. Granting agency and choice can go a long way toward generating the will to change.
Case study 2: All for one and one for all. Like case study 1, initial client discussions were well-received by upper management. However, this time, the client gave more control to middle management, who were brought in and adopted the recommended standard.
Unlike the first approach, “awareness” and “desire” were cultivated earlier in the process. This created an ecosystem of trust in the change management process and the wider benefits of the digital and technical overhaul. All parties were included in the consultation to improve understanding, thereby instilling confidence in adapting to and transferring to the new system. This resulted in the final stage of the process being achieved, “reinforcement.” The client was ultimately prepared to invest in the totality of the solution to optimize ROI. While small customization changes were made to the software to help with overall team integration, the partners are now looking at the next phases of what can be achieved together.
DIFFERING DIGITAL JOURNEYS
The two case studies represent opposite ends of the spectrum, with regard to successful uptake under the ADKAR Change Management Model, Fig. 3. The first failed at Stage 2 as “desire” for change was not felt by all users. The second case study, in contrast, succeeded in digitally transforming brownfield project execution with AWP because of the ability to cultivate enthusiasm and readiness thereby advancing the ADKAR model.
About 70% of initiatives fail to implement digital change because of what, on the surface, appear to be obvious requirements, such as management support, clearly defined and achievable objectives, and transparent communication.8 As case study 1 demonstrated, this is not an easy process, and user needs are often taken for granted and thus, overlooked. The ADKAR model helps avoid these pitfalls, shepherding organizations through successful uptake and upscaling of digital solutions. Giving careful consideration of lessons learned from other sites, and with other teams, will increase the potential for a truly sustainable, value-added transition.
While the second case study was considered a success, it is important to note that successfully managing change through a digital transformation has no endpoint. In fact, “reinforcement” will cycle back to “awareness,” creating a positive feedback loop built on continuous improvement to the new system and processes. This is how digital change can be upscaled from one asset and/or project to a portfolio of assets and/or projects.
For those sites where uptake of the new technology was less advanced, ADKAR and subsequent feedback surveys helped identify why this was the case. The resultant ADKAR improvement plan helped accelerate adoption by both office and site personnel, ensuring scalability and extracting lessons learned for successful EPC brownfield project execution in any context.
Ten modifications to maximize the user interface and experience were identified and acted upon. This enabled the “knowledge” and “ability” stages of the model to be performed effectively with the project teams. When coupled with “reinforcement” strategies, these user-initiated changes enabled a continual learning loop that maximized technology adoption and ROI across the 28 brownfield sites.
ARRIVING AT A DIGITAL DESTINATION
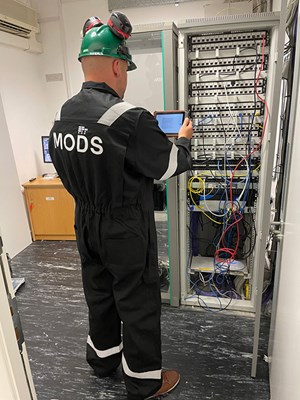
Without the desire for a digital roadmap, advancement stalls. Like the SatNav analogy, even if a driver has the most advanced digital navigation system installed, if it isn’t wanted or understood, it won’t be used. The driver will simply carry on using their crumpled, paper maps, though they are clearly less efficient and effective for their journey.
This metaphor and investigation by Petrofac and MODS should make it clear to digital leaders in the oil and gas industry that even the best invention or innovation can fail to make an impact, if the intended user isn’t fully involved and engaged. Furthermore, according to a recent report by McKinsey & Company, an equal share should be spent on developing technology and the means to integrate it and grow it across a business.9
The novel application of ADKAR in the digitalization of brownfield project execution using AWP solutions carries transferrable lessons to the digitalization of global project delivery. If the users are so important to the uptake and scalability of technological advances, so it goes that a tried and tested organizational change management model is useful to identify and rectify stumbling blocks to fully align technology, people and processes.
Note: Other change management models should be considered by the reader. ADKAR was adopted by the digital partnership responsible for this article, as it offered the most suitable framework.
REFERENCES
- Deloitte, 2019. A Middle East point of view, digital transformation – Fall 2019. https://www2.deloitte.com/content/dam/Deloitte/xe/Documents/About-Deloitte/mepovdocuments/mepov30/standing-still-is-not-an-option_mepov30.pdf.
- OEUK, 2023. Offshore Energy Data & Digital Maturity Survey, Survey Report 2023. https://oeuk.org.uk/wp-content/uploads/2023/05/Offshore-EnergyData-and-Digital-Maturity-Survey-Report-2023.pdf
- Hansmann, T., K.Tee Tan, Y. Zhou, et al., 2022. “Harnessing volatility: Technology transformation in oil and gas,” McKinsey & Company, Sept. 1, 2022. https://www.mckinsey.com/capabilities/operations/our-insights/harnessing-volatility-technology-transformation-in-oil-and-gas.
- https://www.construction-institute.org/resources/knowledgebase/best-practices/advanced-work-packaging
- Fairs, M., “How can we reduce the construction industry’s carbon footprint? World Economic Forum, July 13, 2021. https://www.weforum.org/agenda/2021/07/construction-industry-doesn-t-know-where-it-stands-when-it-comes-to-carbon-emissions/
- Barbosa, F., J. Woetzel, J. Mi, et al., “Reinventing construction through a productivity revolution,” McKinsey Global Institute, Feb. 27, 2017. https://www.mckinsey.com/capabilities/operations/our-insights/reinventing-construction-through-a-productivity-revolution
- Malhotra, G., “ADKAR Model: What Is It and How To Use It?,” Whatfix Blog. 21, November 2019.
- https://whatfix.com/blog/adkar-model-what-is-it-and-how-to-use-it/
- Bellantuono, N., A. Nuzzi, P. Pontrandolfo, et al., “Digital transformation models for the I4.0 transition: Lessons from the change management literature, Sustainability, 2021; 13(23):12941.
- https://doi.org/10.3390/su132312941
- Lamarre, E., K. Smaje, and R. Zemmel, R., “Rewired to outcompete,” McKinsey Quarterly, McKinsey & Company, June 20, 2023. https://www.mckinsey.com/capabilities/mckinsey-digital/our-insights/rewired-to-outcompete
Lead image: A new change management tool is transforming EPC brownfield project execution in the UKCS.
- Digital transformation/Late-life optimization: Harnessing data-driven strategies for late-life optimization (March 2024)
- The reserves replacement dilemma: Can intelligent digital technologies fill the supply gap? (March 2024)
- Digital tool kit enhances real-time decision-making to improve drilling efficiency and performance (February 2024)
- Digital transformation: Digital twins help to make the invisible, visible in Indonesia’s energy industry (January 2024)
- Digital transformation: A breakthrough year for digitalization in the offshore sector (January 2024)
- Quantum computing and subsurface prediction (January 2024)
- Applying ultra-deep LWD resistivity technology successfully in a SAGD operation (May 2019)
- Adoption of wireless intelligent completions advances (May 2019)
- Majors double down as takeaway crunch eases (April 2019)
- What’s new in well logging and formation evaluation (April 2019)
- Qualification of a 20,000-psi subsea BOP: A collaborative approach (February 2019)
- ConocoPhillips’ Greg Leveille sees rapid trajectory of technical advancement continuing (February 2019)