Offshore advances: Overcoming the insurmountable
Offshore challenges and victories are diverse, highly specialized and, thankfully, plentiful. Sometimes small and almost imperceptible, other times large and inspirational, the advance of engineering and insight steadily redefines what is achievable and reveals what, for the moment, is not.
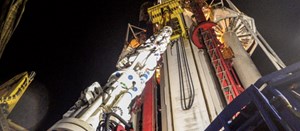
We asked four industry-leading companies to help define the leading edge of the offshore advance—AFGlobal, SNC-Lavalin, BHGE and Halliburton. The innovations they chose describe a wide-ranging array of advances in MPD control and maintenance; virtual reality engineering and training; modular subsea technology and design; and ultra-deep reading LWD.
SEALING A SOLUTION
Changes in demand and advances in deepwater managed pressure drilling (MPD) are producing a major shift in MPD control and ownership, from the service company to the drilling contractor. Integration of the technology with the rig and its crew is a far-reaching change that reduces drilling costs and business models.
An important transitional step came with the recent deployment of AFGlobal’s modular MPD equipment and control system aboard Noble’s Globetrotter II drillship, to drill an exploratory well in the Black Sea. The MPD system, including standardized controls and the first use of a novel, non-rotating sealing element, was fully integrated into the existing rig systems and operated by the rig crew.
Noble said its drillship delivered “improved efficiency and performance with an industry-leading, truly integrated MPD system jointly developed by AFGlobal, NOV and Huisman.” Drilling operations showed increased accuracy in controlling and calculating bottomhole pressure while drilling, said the drilling contractor.
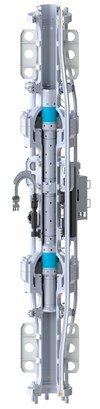
AFGlobal deployed its complete MPD system and worked closely with rig and equipment personnel to seamlessly integrate with the rig and its drilling equipment. The integrated system controlled bottomhole pressure so effectively in the exploratory well’s very narrow pressure window that the hole’s length was extended by approximately 800 m, and the planned drilling timeline was significantly reduced.
The MPD system included the NControl platform, a novel control approach that standardizes key interfaces without imposing limits on specialized drilling systems. The MPD platform integrates monitoring, data, control, analysis and automation. Users access the system through the rig’s control system that interface with surface and subsurface drilling components, including flowmeters, transmitters, sensors and valves.
The MPD system also included the first field application of the company’s award-winning Active Control Device (ACD), Fig 1. The technology is the recipient of multiple engineering honors, including ASME’s 36th Annual Woelfel Best Mechanical Engineering Achievement (BMEA) Award, and the Offshore Technology Conference’s Spotlight on New Technology Award.
Designed for deepwater operations, the device is the industry’s first active, non-rotating MPD wellbore seal. It eliminates traditional rotating control devices (RCDs) and their associated high-maintenance bearing assembly and internally energized sealing element that rotates with the pipe. The hydraulically controlled element pioneers active compensation for wear and enables condition-based monitoring for proactive MPD maintenance strategies. As the seal wears, the active control system maintains closing force to ensure the wellbore seal.
Variations in packer closing pressure and lubrication pressure indicate when an element should be replaced. The ACD control system feeds data to the condition monitoring system, which alerts the crew. The input supports a maintenance-when-necessary approach, instead of relying on a time-based schedule that anticipates the risk of losing wellbore pressure. Condition-based maintenance reduces unnecessary intervention and increases on-bottom drilling time in demanding deepwater applications.
ACD performance in the field reflected the results predicted by rigorous full-scale trials, using a specially built test rig, including a seal life 20% longer than the elements used in conventional RCDs. The device’s first run was highly successful in various modes of operations, and reduced the time to run and retrieve by more than 40%, compared to RCD times.
THE ART OF BEING THERE
Digitalization and immersive visualization tools are still relatively new concepts in the oil and gas industry. However, the implementation of virtual reality (VR) offers significant opportunities to reinvent engineering design and help ensure the successful execution of capital projects.
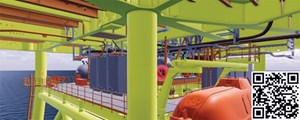
Key VR drivers include the need to reduce costs and shorten project timelines for construction, commissioning and start-up. Engineering, procurement and construction (EPC) companies increasingly see VR as a powerful tool for improving the quality and accuracy of initial design to control and reduce project costs and schedules, said SNC-Lavalin.
VR can be applied to the entire project lifecycle in both greenfield and brownfield projects, but differs significantly in the application. In greenfield designs, a VR review process allows stakeholders, such as project engineers, designers, and even operational staff, to visualize and analyze the facility before it’s constructed, Figs. 2 and 3.
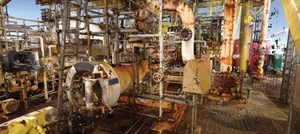
The novel ability to be fully immersed in the environment and view it at a 1:1 scale makes it easier to comprehend complex problems. VR design reviews help discover design issues earlier on, which can reduce risk and limit rework during construction. The immersive environment also presents fewer distractions and improves engagement with tasks, ensuring that projects run smoothly.
In brownfield projects, new designs and upgrades can be validated and executed more efficiently by mixing the existing site condition (via laser scan) with virtual components from the engineering model. The use of VR technology immerses teams in a virtual environment that minimizes time spent in high-risk areas, allowing planning, de-risking operations and maintenance activities to be conducted without traditional onsite access and time constraints.
As a training tool, VR decreases the risks of human error by ensuring tasks are learned and practiced in a controlled, realistic environment. During the operational phase, personnel can be trained in a more effective, efficient and engaging way, using immersive technologies. Operations and maintenance staff can be virtually trained in a multi-person gaming environment, where field activities are integrated with simulated process responses. Not only does this reduce the cost and time of the on-boarding process, but it also increases safety by supplying the staff with the knowledge and expertise on how to respond in emergency scenarios correctly and safely on the first attempt. Additionally, more advanced and comprehensive training reduces the margin for error, as well as increases productivity.
For example, a normally unmanned installation (NUI) platform in the North Sea required equipment upgrades, but the operator wanted to minimize the shutdown duration. SNC-Lavalin applied immersive visualization tools to reduce onsite time, increase productivity and safety, and improve project delivery accuracy.
The process consisted of capturing the asset with laser-scanning techniques to create a digital environment, or a simple digital twin, of the asset. Data were then embedded into the model, so users could virtually interact with the digital twin and visualize an accurate, as-built model of the facility. Users had the option of virtually placing themselves in the environment via VR equipment or interacting as an asset explorer via a desktop application.
Because the platform is a critical production asset, minimal shutdown time with no unexpected outages or delay was essential. Using VR ensured that everything would go as planned during staff operation and maintenance rotations. Personnel became more familiar with the asset, equipment and tasks by immersing themselves in the safe and virtual environment. The VR model dramatically reduced the need for expensive visits to the remote offshore platform and reduced personnel exposure to offshore risks. Remote teams, wherever they were located, virtually visited the site together to explore solutions.
MODULAR THINKING FOR THE LONG HAUL
A significant reduction in subsea project costs can be achieved with a different approach to development, enabled by modular deepwater technologies, believes Baker Hughes, a GE company (BHGE). While the industry has made significant advances in reducing break-even costs for subsea developments, BHGE’s Subsea Connect approach has the potential for reducing the economic development point of subsea projects an average 30%, and adding 16 Bbbl of reserves globally.
The approach, announced last year, will soon be demonstrated in a recently awarded contract to supply production systems for Beach Energy’s Victorian Otway Basin development project in Australia.
Focused on the full life of the field, the approach combines early engagement, advanced technologies, creative commercial models and digital enablement to improve project economics and certainty. Key to its implementation is BHGE’s new Aptara TOTEX-lite subsea system that uses lightweight, modular technologies for easier, more economic installation, operation and flexibility over the life of the field, Fig. 4. The technologies are designed to be more responsive to changing conditions across the life of field, cutting total cost of ownership by up to 50%.
Modular building blocks include a tree that is 50% lighter than conventional designs, a very fatigue-resistant SFX wellhead, compact manifold, composite flexible pipe and risers, a multi-phase boost pump, and fast, multi-function connections. The compact tree includes an innovative flow path that enables high-integrity pipeline protection (HIPPS), and allows production and pumping caps to be switched out, based on changing conditions over the well’s life cycle.
To change project economics, the Subsea Connect approach stresses early engagement at the concept evaluation phase and greater collaboration. It is centered on a workflow process of assess, select, define, develop and operate. The process integrates reservoir and subsurface, lean well construction, topsides and SPS-SURF components. Key features include economic outcome assessment, parallel tracks to compress the assessment phase, dedicated project teams, independent project management, and technology system configuration and project integration.
A flexible partnership model provides alignment with project priorities. Digital solutions to drive greater uptime and productivity include BHGE’s engageSubsea lifecycle management system to enhance execution and remote management of asset maintenance. The solution may reduce maintenance costs by 20%, says the company.
The Beach Energy brownfield contract was announced during May 2019. The contract includes medium-water horizontal trees and subsea control Semstar5 systems. Beach’s operation in the Otway basin involves natural gas production from multiple fields. The operator plans to start seabed assessments during September 2019, and drill up to nine exploration and production wells that will be connected to the existing platform or pipeline. The Project Connect workflow has enabled a short project cycle, with a lead-time of less than 12 months.
The Subsea Connect approach also will be applied to a project with Siccar Point Energy Limited, announced in 2017. The long-term agreement for development of Cambo field in the North Sea began with the appraisal and early production phases of the project.
RESISTIVITY REVELATIONS RUN DEEP
Identification of reserves and formation boundaries while drilling is central to geosteering and formation evaluation. The need is particularly acute when placing wells in complex geological structures, especially in deepwater and mature fields.
While LWD resistivity measurements have been used for many years to help place wells and evaluate reservoirs, their small depth of investigation (DOI) limits their usefulness in complex reservoirs. Ultradeep, azimuthal, electromagnetic LWD tools have been developed to bridge the gap between the large-scale perspective of surface seismic data, and the detailed view available from conventional well logs.
Halliburton’s EarthStar ultra-deep resistivity service dramatically increases the range of real-time reservoir and fluid boundary mapping, with a DOI proven up to 225 ft (68 m) from the wellbore. The gain more than doubles the range of earlier electromagnetic LWD logging tools, said the company.
The EarthStar service comprises a patented deep-reading resistivity tool (Fig. 5) and the industry’s only 3D inversion process that estimates the position, resistivity and orientation of formation layers around the wellbore, along with the position of hydrocarbons within them. The information provides geologists with a clearer understanding of the surrounding geology, enabling timely geosteering decisions, accurate well placement, and more efficient field development.
The technology also helps reduce geological uncertainties in three distinct applications: identifying zonal boundaries early to land the well accurately and avoid costly pilot holes and sidetracks (geostopping); by making well-placement decisions while drilling to place the well accurately in the target zone (geosteering); and by identifying bypassed pay and mapping the extent of the reservoir to enhance understanding for future well planning (geomapping).
The tool’s high signal-to-noise ratio yields measurements of complex geological structures within a very large volume of investigation. The accompanying inversion process is capable of revealing sufficient structural detail while maintaining a large-scale, rather than a local, perspective. The standard inversion process yields two-dimensional (2D) cross-sectional views of the reservoir along the wellbore, showing features above and below the well but ignoring structural features that may exist to the left or right.
Two methods, both of them unique to the EarthStar service, can shed light on complex, three-dimensional (3D) structures that might not be fully represented in a 2D visualization. The first method is to present 360° images of the resistivity distribution around the borehole. This supplements the 2D image from the inversion, and offers an all-round view that can often reveal 3D structural features that the 2D visualization may overlook. The measurements are available in real time and are integrated into Halliburton’s RoxC geosteering software.
The second method for visualizing complex, 3D structures is the industry’s first truly 3D inversion process, said Halliburton. The process works in a similar fashion to the standard inversion, but instead of producing a simple 2D image, it generates a full 3D representation of the surrounding geology, giving a much more realistic view of the structure. The process makes it possible to see structural features and fluid distributions to the left and right, as well as above and below the well, allowing for much better control of the well trajectory in three dimensions, and helping place wells in zones that might otherwise be overlooked or misinterpreted. Knowledge of the 3D structure also helps improve completion designs and to plan better for subsequent production sections.
In one case, an operator in the Norwegian sector of the North Sea deployed the EarthStar service in a complex turbidite channel structure. 3D inversion was used to visualize the detailed structure around three production sections in a multilateral well. The resulting visualization showed features, such as erosion channels, and complex distributions of hydrocarbons, that would have been difficult or impossible to see or correctly interpret from conventional data. WO
- Advancing offshore decarbonization through electrification of FPSOs (March 2024)
- Subsea technology- Corrosion monitoring: From failure to success (February 2024)
- Driving MPD adoption with performance-enhancing technologies (January 2024)
- Digital transformation: A breakthrough year for digitalization in the offshore sector (January 2024)
- Offshore technology: Platform design: Is the next generation of offshore platforms changing offshore energy? (December 2023)
- 2024: A policy crossroads for American offshore energy (December 2023)
- Applying ultra-deep LWD resistivity technology successfully in a SAGD operation (May 2019)
- Adoption of wireless intelligent completions advances (May 2019)
- Majors double down as takeaway crunch eases (April 2019)
- What’s new in well logging and formation evaluation (April 2019)
- Qualification of a 20,000-psi subsea BOP: A collaborative approach (February 2019)
- ConocoPhillips’ Greg Leveille sees rapid trajectory of technical advancement continuing (February 2019)