JAMES M. PAPPAS, P.E., Ultra-Deepwater Program, RPSEA
The goal for well testing in the early reservoir appraisal stage is to gather information, to help determine the economic potential of field discoveries and provide insights to safely commercialize fields. A project (Project 08121-2501-02) to evaluate deepwater testing concepts in the Gulf of Mexico (GOM) was recently undertaken through the Research Partnership to Secure Energy for America (RPSEA) Section 999 Program by Nautilus International and several partners. The research objectives included reservoir modeling of three major deepwater GOM reservoir plays and simulations of a variety of well tests (long/short-term, injection/production testing). The result of this project includes options for deepwater well testing of GOM reservoirs.
STUDY RESULTS
The study concluded that most operators do not know the size of their newly discovered reservoirs and in general have done a poor job of initially estimating reserves (i.e., using electric/wireline logs and MDT—modular formation dynamics tester—results only provides information in close proximity to the wellbore, and seismic information cannot distinguish reservoir heterogeneity). Without knowing the size, production potential, and reserves associated with a discovery, the consequence is that vast amounts of hydrocarbon resources may not be produced, due to high risks and uncertainties. Operators realize that the sole method to zero in on reserves and productivity is to conduct a series of early appraisal, short-term and long-term well tests. By doing so, they can integrate the reservoir properties away from the wellbore to provide permeability and net producing intervals (true kh), reservoir boundary effects, compartment volumes, reservoir energy, and initial reservoir pressure. For deep water and ultra-deep water, early reservoir appraisal challenges include operational and environmental risks, multi-disciplinary coordination, and prohibitively high costs.
Detailed reservoir analysis and well test modeling on Middle Miocene, Lower Tertiary Paleocene, and Lower Tertiary Eocene GOM plays was conducted. Historical production data and expert assumptions were used to develop a catalog of the reservoir and fluid characteristics for each deposit. Well test simulations, utilizing short-term, long-term, interference, and injection testing, were performed on each reservoir. Nodal analysis, which estimated the temperature and pressure, not only at the wellhead but also at the surface, was performed for both the short-term and long-term tests for various rates and reservoir parameters. The goal was to understand the reservoir characteristics, the duration of different well tests and pressures, flowrates, and fluid production properties during well tests. The information gathered proved valuable for industry professionals to design well test scenarios. The differences in water depth, rock formation, permeability, viscosity, gas-oil ratio (GOR), and bottomhole pressure (BHP) are just a few parameters that have significant impact on the selection of a well test method, and downhole, subsea and surface well testing equipment.
The common assumption, it was found, has always been that high production rates are needed to test the three aforementioned types of reservoir plays. This assumption proved not to be true.
The simulation and modeling analysis produced results that provided cost benefits and environmental safeguards. The simulation results from conventional well testing (short-term, long-term and interference testing) showed that a substantial reduction in flowrate during well testing produced the same results as using maximum flowrates. Well test simulations indicated that production rates of between 1,000 and 2,000 bopd provide necessary pressure-vs.-time results to perform classical pressure transient analysis. The lower flowrates equate to lower produced fluid volumes returned to the surface, thus reducing disposal requirements. Furthermore, this discovery suggests that smaller facilities are required than commonly thought. It leads to the conclusion that deepwater well testing can be performed less expensively and, perhaps, in less time than previously believed.
The injection test simulation results were very encouraging, Fig. 1. The final data correlated well to the results of the conventional production tests, and the injection tests required less time compared to the duration of conventional tests. One of the most important advantages of the injection test simulation was that there is no live oil (i.e., oil with dissolved gas) produced to the surface, which reduces environmental concerns regarding gas flaring and eliminates the need to store or off-load produced oil. The findings of the injection test warrant further investigation, to ensure that these tests can be used as a viable alternative to conventional well tests.
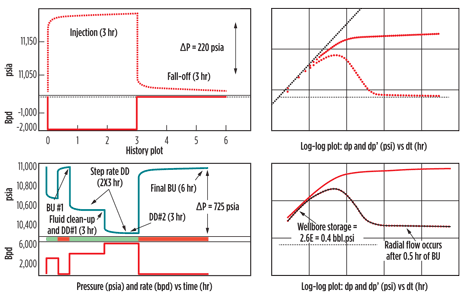 |
Fig. 1. Injection well tests (top) for Middle Miocene and comparison to production tests (bottom). |
|
-
The Middle Miocene was assumed to have the highest-permeability rocks and lowest-viscosity fluid. Its reservoir size was moderate, and sand quality was better than the other two reservoirs. Well test designs were, thus, most favorable in terms of test duration and fluid production.
-
The Lower Tertiary Paleocene reservoir was assumed to be very deep, and had the lowest rock permeability and highest viscosity fluid among the three reservoirs. Well tests will likely be challenging and require longer test durations. For this reason, certain well test methods may not be practical in terms of time and cost. Its low permeability, high viscosity, and depth will necessitate the need for additional equipment to push production fluids to the surface (i.e., may require electric submersible pump, subsea pump or gas lift).
-
The Eocene reservoir has moderate permeability and viscosity, which places it second in terms of well testing feasibility. Higher GOR fluid properties in this reservoir will require careful management in terms of equipment selection, operational procedures, etc.
WELL TEST SYSTEM DESIGN
The project’s second aspect was to design the architecture of well test systems that can be used in the GOM. Two examples of the systems can be found in Fig. 2. Many multi-disciplinary subject matter experts were involved in this aspect of the project. The goal was to determine the operational feasibility of the well test systems, with a major focus on ensuring environmental and equipment protection, and personnel safety. Three criteria were used to develop the well testing systems—subsea connection type (wellhead or subsea tree); riser type (conventional riser, flexible riser or self-standing risers); and vessel type (mobile offshore drilling unit; floating production, storage, offloading vessel; floating production unit; intervention vessels; installation vessels; or a combination of vessels). From these three criteria, eight well test systems were envisioned and assessed.
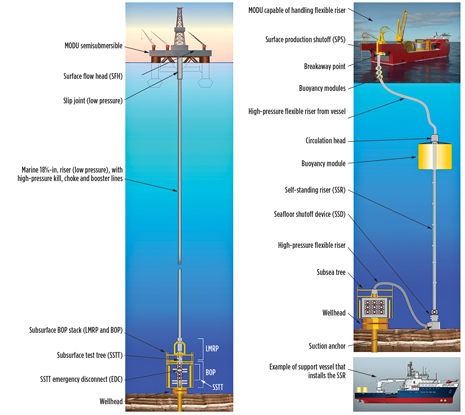 |
Fig. 2. Examples of possible well test systems: MODU with subsea BOP (left); and MODU, flexible to buoy and riser to seafloor (right). |
|
The base case assumptions for the study included the following:
-
The well is not connected to a fixed production facility.
-
The well either has only a wellhead (no production tree), or it has a vertical or horizontal tree.
-
The riser will connect either directly to the production vessel and the wellhead or production tree, or it will be free-standing with a flexible pipe to the production test facility.
-
The facility or vessel will handle the production fluids, including separating the oil, gas, water and sand.
-
The facility or vessel will store the fluids and treat the gas.
Feasibility analysis for each of the eight systems included downhole, subsea and surface safety mechanisms to shut in the well, provide emergency disconnect capability, and ensure environmental and personnel safeguards. Detailed operational procedures, issues, control philosophies, and emergency disconnect sequence (EDS) descriptions and flowcharts, were developed for each system. Required vessel deck equipment was analyzed for each well test system, based on particular reservoir parameters. It included safety analysis for emergency shutdown (ESD) and pressure relief devices, pressure and velocity analysis for produced fluids (oil, gas and water), Pipeflo program schematics for produced fluids traveling up from the wellhead through the vessel equipment, deck loading capacity for the equipment, and Flaresim program models to define the noise, radiation and temperature effects under various wind conditions.
The different components in each system were rated, and recommendations were made, based on safety aspects of the feasibility analysis. A technical readiness level (TRL) analysis was conducted for each of the eight systems via a workshop that included 14 subject matter experts from different disciplines. The TRL level information, based on levels 1-7, formed a convenient, rational basis for the management of operating companies to determine which well testing system might be best suited to employ in their early reservoir appraisals. Through this workshop, five of the eight systems were rated at the top of the industry-accepted TRL scale. The remaining three systems had lower scores based on cost and greater requirements for operational readiness, Table 1.
TABLE 1. SUMMARY OF AVERAGE TRL RATINGS |
 |
RATING THE SYSTEMS
A summary of comments on each system follows. System 1, MODU and subsea BOP, was universally accepted as doable and very well proven. System 2 was a MODU with a surface BOP. Most of the elements had been used before, but showing that they had been used as a system was difficult. It was felt that Unocal may have used it in a well in about 1,600 ft of water (“deep water” back then!) offshore Indonesia, about 10 to 15 years ago, but no one could substantiate it during the meeting.
During the discussion of System 3, a MODU with an offloading vessel for produced fluids, the participants agreed that it was more realistic to split it into two categories—System 3a, which was similar to System 1 (MODU with a subsea BOP), but with a separate production vessel; and System 3b, which was like System 2 (MODU with a surface BOP), but it had a separate production vessel. System 3a, MODU with a subsea BOP and an offloading vessel, was felt to be very well proven. System 3b, a MODU with a surface BOP and an offloading vessel, received the overall lowest TRL assessment of all. It was qualified with comments and suggestions on additional testing necessary to improve its rating.
System 4, a Seillean-style FPSO, with a drill pipe riser, is straightforward and well proven. The Seillean story, with some reservations regarding its drill pipe riser being a single barrier system and subject to regulatory concerns in the GOM, has merit. System 5, an FPU/FPSO with an intervention vessel and deployed riser, caused debate, because the components are well-proven. Yet, they have not been used together as a system much in shallow water and have been used even less in deep water. The sense of the meeting was that enough shallow-water experience has occurred, so that the system can be made to work in deep water.
System 6, a MODU or intervention vessel with a subsurface BOP, was universally thought to be well-proven and did not stir any comments. Similar to System 1, it was “a perfect TRL 7.” System 7 is a MODU with a flexible riser to a buoy, and a separate installation vessel-deployed subsurface riser to a wellhead. The system caused similar reactions as System 5, i.e., the parts have been used separately but not as a system in shallow water. It has not been proven in deep water. The group thought it can readily be made to work, based on its shallow-water history.
System 8 is a MODU with a flexible riser to a buoy and a separate installation vessel-deployed subsurface riser to the seafloor. This system was deemed to be well-proven, but it has only been used for short periods of time in deep water.
CONCLUSIONS
This project provides options and related information necessary to make informed decisions about deepwater well tests. Operators can use this information to conduct early reservoir appraisal/deepwater well tests to rapidly assess geological and reservoir attributes, and to determine production capacity and field development economic feasibility. The full report can be found online at http://www.rpsea.org/attachments/contentmanagers/2730/08121-2501-02-FR-Early_Reservoir_Appraisal_Well_Testing_System-05-20-11_P.pdf.
A future deliverable resulting from this project includes a computer-based modeling tool to determine optimum well test methods based on reservoir type, subsea and surface equipment, and vessel(s) criteria. 
ACKNOWLEDGMENT The author thanks Dr. Keith Millheim, Nautilus International LLC, as well as representatives from participants, including IntecSea, GMC, Knowledge Reservoir, Marecsa, Expro, Tidewater, Petrodin, The University of Tulsa and Mr. Peter Lovie for their contributions. RPSEA is a 501(c)(3) organization that is entrusted with managing research and development projects for the U.S. Department of Energy’s National Energy Technology Laboratory, which was established pursuant to Title IX, Subtitle J, Section 999, of the Energy Policy Act of 2005.
AUTHOR
|
 |
JAMES PAPPAS is vice president of Ultra-Deepwater Programs for RPSEA, the Research Partnership to Secure Energy for America, in Sugar Land, Texas. Previously, he held the positions of global technology coordinator, facilities engineer and deepwater project coordinator for Devon Energy, as well as production engineer in the Gulf of Mexico Division for Devon and Santa Fe Snyder prior to their merger. He has also held drilling, completion and production postions with several other operators. Mr. Pappas is a 33-year member of SPE. He is both the immediate past SPE International Production and Operations Technical Director and SPE Technical Programs and Meetings Committee Chair. In addition, he has served on several technical program committees, including OTC. Mr. Pappas is also the immediate past Private Industry Practice Chair of the Texas Society of Professional Engineers. He is also active in API, National Society of Professional Engineers, AADE and Marine Technical Society. He earned a BS degree in chemical engineering, as well as a BA in chemistry from the University of Texas at Austin in 1979. He graduated with an MBA with highest honors from the University of Texas at Tyler in 1993. He has been a Registered Professional Engineer in Texas since 1985. |
|