DEEPWATER TECHNOLOGY
Major deepwater development offshore Egypt continues tie-back expansion
A seven-year subsea field development creates expandable architecture in the Mediterranean Sea.
David Blacoe, David Smith and Graham Taylor, Intec Engineering.
In 1999, a pioneering project, to be operated by the Burullus Gas Co., a joint venture of BG Egypt, Edison Gas and the Egyptian General Petroleum Co., marked the first deepwater development offshore Egypt. The 56-mi (90-km) tiebacks from the Scarab and Saffron fields to shore in Phase I of the project challenged tie-back records of the time.
Since those early days, Edison Gas has sold its interest in Burullus Gas to Petronas Carigali. A FEED study was commissioned for the West Delta Deep Marine (WDDM) concession area offshore Egypt in the Mediterranean Sea, which was completed by Intec, who continues to work alongside joint venture partners to support ongoing development of WDDM. The firm has undertaken the conceptual design and FEED for all phases of WDDM development to date and is presently supplying a technical assurance support team to Burullus on Phase IV, on which the firm is also providing package management for the controls equipment purchase order.
From an area devoid of deepwater development and with little associated infrastructure, the WDDM concession has evolved through subsequent development phases to become Egypt’s premier deepwater oil and gas province, with wells located in as much as 3,360 ft (1,024 m) of water and tiebacks to shore up to 72 mi (124 km) in length.
The WDDM transformation used the following development principles:
- Proven technology
- Design and operational simplicity
- Integrated design with a common basis for offshore/onshore, equipment suppliers, installers, etc.
WDDM BACKGROUND
The WDDM concession directly abuts the existing shallow-water operations in the Rosetta concession, with the concession line closely following the 656-ft (200-m) seabed contour, Fig. 1. Developments are located in water ranging from about 984 ft (300 m) to 3,937 ft (1,200 m) deep, so the diverless subsea technology used was selected from applications in the GOM and North Sea. The first development phase was dedicated to the Egyptian market, but the main pipeline’s core infrastructure-from the PipeLine End Manifold (PLEM) to receiving facilities onshore-was designed to allow for expansion.
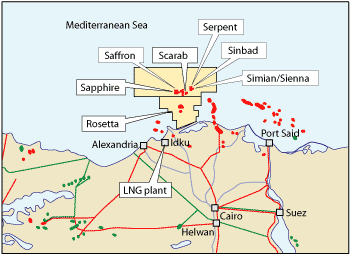 |
Fig. 1. WDDM concession line closely follows the 656-ft (200-m) seabed contour.
|
|
Subsequent phases were dedicated to a new LNG plant built at Idku, near Alexandria, and connecting through expansion connections provided in the PLEM hub location.
Production system. Subsea equipment includes horizontal trees, manifolds and the remote pipeline connection system. With major workovers for tree retrieval not expected, subsea Christmas trees are of horizontal design with the flow loop connector hub mounted directly on the tree body. Remotely installed tie-in jumper spools connect the trees to the manifolds, which are designed to fit the Cameron Vertical Connection (CVC) system. With fishing activity possible in water depths down to about 656 ft (200 m), the larger pipelines are designed for fishing gear pullover loads, and the smaller 4-in. lines are trenched up to this water depth. Subsea structures in the shallower waters are designed to allow trawling over production system components, while in deeper waters the structures are upright.
Pipelines are carbon steel with diameters ranging from 10 in. for well flowlines to 20 in. and 26 in. for infield pipelines. PipeLine End Terminations (PLETs), containing CVC interfaces, are installed integrally with the flowlines. Provision is made for the flowline to slide longitudinally on the PLET foundation to allow temperature expansion and avoid locked-in forces which could result in flowline buckling.
Produced gas is sweet, but there is a risk of hydrate formation due to pressure and temperature. Continuous MonoEthylene Glycol (MEG) injection is necessary; this is achieved through dedicated flowlines from the terminal. In addition, methanol injection is required at startup and shutdown with a methanol storage and injection facility mounted on the controls platform.
Variable reservoirs. Accommodating production streams from different reservoirs is a challenge. The deepest of the three reservoirs is Sapphire, which lies underneath the Scarab and Saffron reservoirs, Fig. 2. With Sapphire’s higher reservoir pressure, there is the potential for the interconnected flowlines to be subjected to higher pressures than originally designed when the inlet valve closes at the terminal. To prevent this from happening, an autonomous protection system was included within the controls. Pressures are continuously monitored and the flows are automatically controlled to ensure safe operation.
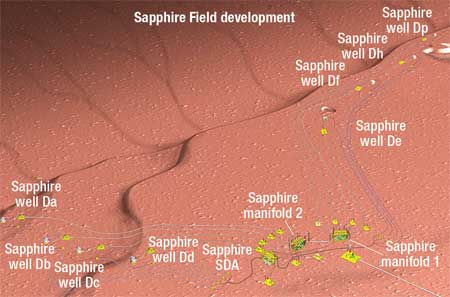 |
Fig. 2. Relief map for Sapphire Field reservoir.
|
|
A further challenge is presented by the steep seabed slopes in some areas. The seabed at Sapphire is characterized in some areas by slopes steeper than a 1:10 grade, and seabed instability from seismic events is a concern. The main controlling variables are well position and flowline routing into areas of less severe slopes, where risks are reduced.
While the overall system design generally used proven technology, there are several other challenges associated with the development, including:
- Hydrate avoidance
- Chemical injection control
- Modern controls system
- Large-diameter diverless connectors
- High-production-rate trees (greater than 150 MMcfd).
The key to reducing the risk of seabed interface problems involves the use of an exhaustive System Integration Test (SIT) to simulate the mechanical mating and control loop testing of all the components in the subsea production hardware. Figure 3 shows the Subsea Distribution Assembly (SDA) alongside two of the production manifolds at the SIT site.
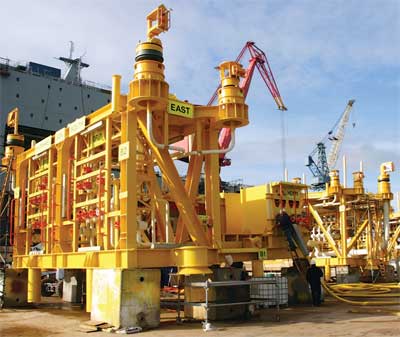 |
Fig. 3. Subsea Distribution Assembly (SDA) alongside two of the production manifolds at the System Integration Test (SIT) site.
|
|
DEVELOPMENT PHASE I
The twin 20-in. main export pipelines begin at a water depth of 1,362 ft (415 m) and run for 19 mi (31 km) to the PLEM hub at a depth of 312 ft (95 m), where the pipeline diameters increase to 24 in. and 36 in. to provide expansion capacity for other fields. A 4-in. pipeline conveys MEG from shore to the infield umbilicals for hydrate inhibition by direct injection at the trees. Scarab and Saffron fields started producing in 2003 at a rate of about 700 MMcfd of gas.
DEVELOPMENT PHASES II AND III
Simian and Sienna fields (Phase II) and Sapphire field (Phase III) were selected as the first two expansions of WDDM to provide the feed gas to the new LNG plant. To meet market commitments, a decision was made to develop these projects. Concurrently, there are six wells at Simian, two wells at Sienna and eight wells at Sapphire. The production streams from the new fields are brought together at the Phase I PLEM, where gas from all the fields is commingled into the export pipelines to shore. The Simian wells are designed to handle up to 150 MMcfd.
The subsea wells, in more than 3,281 ft (1 km) of water, are controlled from the beach through an electro-hydraulic multiplexed system, with controls, hydraulic power and methanol-injection equipment mounted on a control platform, strategically positioned in shallower water close to the Phase I PLEM. Phase II started producing in the second quarter of 2005, followed by Phase III in third quarter 2005, adding production capacity of 1.4 Bcfd of gas, allowing overall WDDM production to exceed 2 Bcfd.
DEVELOPMENT PHASE IV
Burullus is progressing with Phase IV which consists of an eight-well brownfield expansion to the existing 24 wells centered on additions to the Scarab-Saffron production hub, shown Fig. 4.
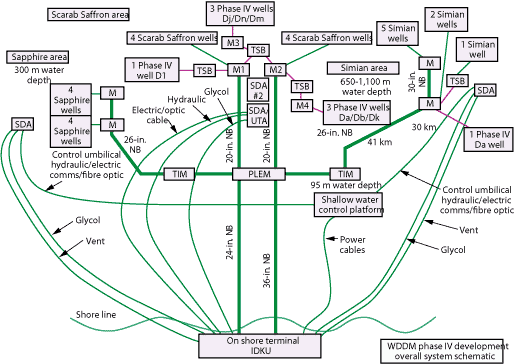 |
Fig. 4. Phase IV development expansion to the Scarab-Saffron production hub.
|
|
The initial Scarab-Saffron control system was designed with the capacity to control future wells; seven of the Phase IV wells in the Scarab, Saffron and Serpent areas will use this capacity. The eighth well will develop the Sinbad field in the Simian area, to be controlled via the Simian control system.
The scope of Phase IV includes 10-in. flowlines from each well to two new manifolds, jumpers and connectors, a new SDA which links to the existing SDA, Subsea Control and Monitoring (SCM) systems, umbilicals to each well and subsea trees.
The contracting strategy involves an EPIC contract for the majority of the work, but subsea trees, control system and flowline connectors were ordered earlier by Burullus because of the tight project schedule.
Plans are under way for continuing expansion of production capacity. Concept and FEED work scope on development Phases V and VI has recently been done.
CONTROL SYSTEM CHALLENGES
The subsea control system had to overcome several technical challenges, including long distance step-outs, the MEG-injection delivery network and interfaces to multiple control system vendors.
For the initial Phase I development, Aker Kvaerner supplied the subsea control system. Communication is achieved using the vendor’s proprietary protocol through a copper-based cable network. However, repeater modules to improve the signal level are installed at the SDA, located 51 mi (82 km) from shore.
Phase II involved eight wells and two manifolds, with the furthest well 77 mi (124 km) from shore. Although developments in communication technology indicated that using a copper-cable based system was feasible, the lack of proven subsea installations and the benefit of increased local content dictated the use of a dedicated, unmanned controls platform 37 mi (60 km) from shore. This approach increased the complexity, particularly with a shore-to-platform link. This link processed all the platform communication, in addition to the subsea system data. The design is sufficient to support the development of Phase III, also with eight wells and two manifolds, together with the future Sequoia and Saurus fields. Table 1 shows the overall WDDM development elements that can be supported by the controls platform.
TABLE 1. Controls expansion capability |
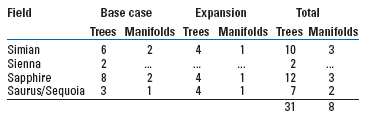 |
|
Communications networks between the platform and subsea control system, supplied by Vetco Gray, are built using the vendor’s proprietary protocol through a copper-based cable network. However, platform-to-shore communication is achieved through optical fibers using modbus over ethernet. The umbilical supplies the platform electrical utilities from onshore power. In addition to the data link through the subsea power and communications umbilical, the platform is also equipped with a satellite communications network to maintain control during an umbilical failure. The reduction in bandwidth from multiple parallel optical fibers to a single 64 kbs satellite channel highlighted the need to be specific in controlling the devices that access the network. During satellite link commissioning, IP addresses assigned to test laptops and other devices no longer on the network were repeatedly polled by the host, resulting in a level of network traffic that swamped the actual data. This additional traffic was not apparent on optical fiber, due to its wide communications bandwidth.
The initial Phase I control system was designed for a four-well and one-manifold expansion. The requirement for Phase IV was for seven wells and two manifolds to be connected to the Phase I system. To maximize process flow monitoring and minimize the MEG injection, Wet Gas Flowmeters (WGFM), Fig. 5, and surface-controlled Glycol Control Units (GCU) have been added. Judicious work by the engineering firm and the Phase I control system vendor ensured that the expansion could be accommodated. Phase I Kvaerner control system serves seven wells and two manifolds while the Phase II Vetco Gray control system serves one Sinbad well. The control of these eight wells and two manifolds, currently being installed as part of Phase IV, is an expansion of these fields.
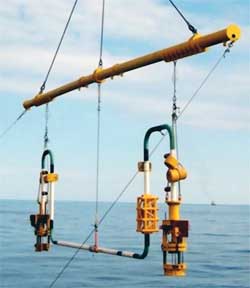 |
Fig. 5. Wet Gas Flowmeter (WGFM) used to maximize process flow monitoring and minimize MEG injection.
|
|
CHEMICAL INJECTION CHALLENGES
To prevent hydrate formation, the development uses MEG dosed with corrosion inhibitor to protect the pipeline. To control wellhead injection, adjustable chemical injection rate devices were selected. For Phase I, the GCUs were adjustable by ROV. To accommodate the field requirements, a range of 55-to-500 bpd was selected, together with a bypass orifice. These units are beneficial because they are simple. However, there are drawbacks:
- A GCU provides no feedback to the onshore operator, hence no confirmation that the unit is functional
- The injection rate is set high, to avoid expensive intervention, which wastes MEG and places additional load on the onshore recovery units.
For subsequent phases of the WDDM development, the firm took advantage of GCU technology improvements and selected electrically-operated units to be part of the offshore system, providing onshore operator control. In addition, the firm required that the units have a suitable range for the field’s life. The onshore MEG delivery system has a finite limit and cannot supply all the wells at the predicted water production levels later in the life of the development. To accommodate the early-life, low-water production and to reduce MEG usage, the adjustment range was reduced to 10-to-240 bpd with the ability, if required, to change out ROV-adjusted units later to electrically operated units with a capacity of 55-to-500 bpd. These surface-controlled units enable the operator to trim MEG supply in line with the well water production, provided by the WGFMs and also indicate the actual MEG injection rate.
However, there are disadvantages. The units are fairly slow in operation, taking 20 minutes to complete an adjustment cycle. The operators expected virtually instant changes, resulting in several commands to a unit before the adjustment was completed. This caused the unit to stop working, requiring a reset. The firm identified this problem and later versions of the vendor’s SCM software prevented the unit from receiving more than one command. Also, the inability to observe MEG injection in realtime prevents the operators from knowing when the units stop working, either from supply pressure falling below required differential pressure or from volume rate reduction. The advantage is that the operators are now aware of any shortfalls in the chemical injection system.
The WDDM onshore element, including the integrated control system (ICS) and the MEG delivery network, was provided through a different contractor. Viewing the actual subsea injection allowed the engineering firm to fully review the network, including the onshore element, which produced some interesting findings. First, the lack of correlation between the onshore flowrates and the offshore demand often led to a shortfall as operators increased subsea injection without considering what was being delivered. Second, there was no units correlation between the onshore flowrates, measured in cubic feet per hour, and the subsea tree’s flowrate in barrels per day. One additional issue involved the delivery network’s initial design of the two pump sets feeding the three separate offshore flowlines. The Simian-Sienna field had to share from either the Scarab-Saffron field or the Sapphire field. These issues are now being resolved. However, it emphasizes the need to verify an interface between contractors while at the same time requiring a clear understanding how it is being implemented.
FLOW ASSURANCE CHALLENGES
Due to the large pipeline capacity, managing offshore liquid holdup is crucial to the success of future production operations. The firm developed a model to simulate the impact of changes in offshore supply and onshore demand on the pipeline network and the onshore facilities. Using OLGA software, the firm incorporated the entire subsea network into the model, together with the onshore receipt facilities, including slug catchers and high-pressure and low-pressure separators, Fig. 6. Due to the limited control system functionality within OLGA, an innovative link was developed between OLGA and MATLAB-Simulink to produce a detailed model of the onshore terminal control functions in Simulink, including a DCS-style controller function written for the project. This approach has allowed a variety of control system options to be evaluated without changing the OLGA model and without the need for a separate process modeling package for the onshore facilities.
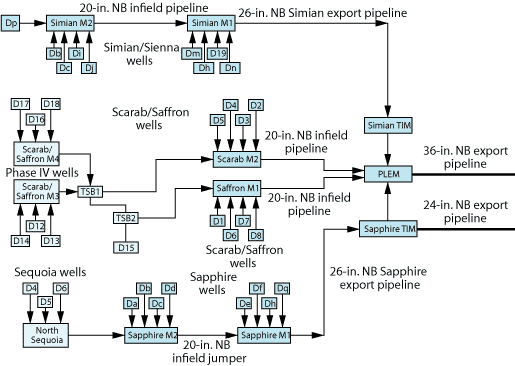 |
Fig. 6. Entire WDDM subsea network was incorporated into the process-modelling software package.
|
|
The model takes a holistic approach, while modeling the two main 24-in. and 36-in. trunklines flowing from a common PLEM into two different slug catchers. With the addition of the downstream equipment, such as the high-pressure and low-pressure separators, and slug catcher pressure and liquid distribution control, the model can correctly predict liquid outflow from the low-pressure separators, rather than just accumulation flow from the slug catcher. The use of MATLAB-Simulink allows complex control systems to be modeled into the OLGA model’s details.
By employing this combined model, the engineering firm analyzed the behavior of the onshore pressure controls and liquid handling systems across the full range of operating conditions and flow disturbances anticipated throughout field life. The information from the model defines an operating envelope for the pipeline network, including limitations on the rate at which demand changes can be handled. This proved important during early operation of the LNG plant, where limitations on ramp-up rates were dependent on time spent operating at low rates, due to liquid accumulation in the pipeline network.
The model verifies the slug catcher’s capacity, taking into account the downstream equipment’s maximum liquid handling rates. This resulted in modifications to the liquid distribution control system design to maximize the available capacity of the four low-pressure separators under liquid surge conditions in the trunklines and their respective slug catchers.
The modeling also gave insight into the interactions between fields and between trunklines. This has led to initial operational strategies for field restarts, enhancement to the pressure control strategy, and to consideration of field segregation at the PLEM when turndown in the 36-in. line is no longer an issue.
The WDDM project developments to date have delivered the following results:
- On-time delivery--first gas from Phases I, II and III delivered on schedule
- High system availability-four years with no major unplanned shutdown
- Expansion flexibility-the original eight-well development was expanded to 32 wells and WDDM development expansion continues.
|
THE AUTHORS
|
|
David Blacoe joined INTEC Engineering (UK) Ltd. five years ago as a Senior Project Manager and has worked as the Project Manager of several WDDM phases of development. Blacoe began his career in the early 1970s working on conventional developments in the North Sea and moved in the early 1980s into subsea completions. He has more than twenty years experience with subsea and floating production projects.
|
|
|
David Smith is a Senior Controls Engineer and Lead Controls Engineer of a number of WDDM Phases for INTEC Engineering (UK) Ltd. He was involved in the development of control systems for several Norwegian and UK companies. Smith joined INTEC in 2001 to work on the conceptual subsea controls and umbilical design for the next phase of a major gas development offshore Egypt in the eastern Mediterranean.
|
|
|
Graham Taylor is Managing Director of INTEC EAME and PM for Phase II Concept/FEED. A Civil/Structural Engineering graduate with a career spanning more than 27 years in the oil and gas industry, he initially specialized in subsea structures/pipelines and general subsea before moving into project management of subsea projects. He joined INTEC in August 2001 as an Engineering Manager with an initial role as the Project Manager for the Simian/Sienna and Sapphire concept selection followed by FEED, before assuming his present position at INTEC in 2005.
|
|
|