Technology from Europe:
Norway/Finland
Semisubmersible heavy transport ship expanded to carry larger rigs
Originally built at CSBC in Kaohsiung, Taiwan, the Blue Marlin semisubmersible heavy transport ship (newbuilding 726) was first delivered to owner Dockwise in 2000. Dockwise is a Dutch company specializing in heavy transport shipping for the oil and gas industry. Jackup drilling rigs and production platform topsides are examples of the vessel's typical cargoes.
However, Dockwise determined that it needed additional capacity in its fleet to carry even larger cargoes/ structures. After considering newbuild and retrofit options, the firm decided to convert Blue Marlin to a larger vessel. A structural conversion contract was awarded to South Korea's Hyundai. In turn, a contract for a significant propulsion upgrade was given to Finland's Wärtsilä.
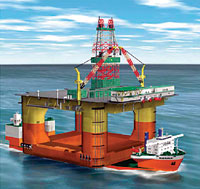 |
Fig. 1. Shown in this artist's impression after conversion, the Blue Marlin can now transport the largest offshore rigs and structures used by the upstream industry, up to 73,000 t.
|
|
Vessel conversion was carried out at Hyundai's Mipo Dockyard in South Korea. The project required increasing the vessel's breadth to 63 m from 42 m. With an impressive, unobstructed deck area of 11,227 sq m, Blue Marlin is now the largest semisubmersible heavy transport vessel in the world, Fig. 1.
The ship's deadweight is 78,000 t, enabling it to transport heavy structures weighing up to 73,000 t. With its new dimensions, Blue Marlin can transport heavier and ultra-large floating production and drilling platforms, as well as larger semisubmersible drilling vessels.
Greater propulsion required. The vessel was originally equipped with one open Lips controllable-pitch propeller (CPP), with a 6,200-mm diameter. This CPP was directly driven by a low-speed diesel engine that delivered 12,640 kW at 127 rpm. Furthermore, one transverse thruster was installed in the ship's bow.
Propulsion requirements for the much larger, converted vessel were investigated in model tests at MARIN in the Netherlands. In the sea-keeping tests, it became clear that the vessel required more thrust to operate safely, especially in adverse weather.
To obtain extra thrust, two new retractable thrusters were proposed for the bow. However, they could not, alone, supply all the extra thrust needed for the vessel. It was also necessary to upgrade the existing CPP installation.
Wärtsilä won the contract to supply three 8L32 generating sets and two electrically driven Lips retractable thrusters in September 2002. The order to supply a large Lips HR (high-efficiency) nozzle with new propeller blades for the main propulsion was subsequently placed in October 2002. This work also included model testing of the new propeller design at MARIN.
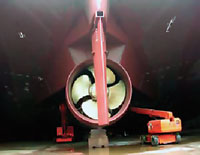 |
Fig. 2. CPP, HR nozzle and tunnel construction after modification.
|
|
Nozzle increases thrust. An HR nozzle was installed around the existing propeller to increase thrust without changing engine power, Fig. 2. The existing main engine, shaftline and propeller hub remained in place.
A key reason for choosing the HR nozzle was to maximize the benefit of its installation. Compared to a conventional nozzle profile, the HR nozzle differs considerably in shape. A curved outer profile, and an inner profile that flares out to the trailing edge, increases mass flow handled by the propeller. This leads to a larger pressure difference between the nozzle's inside and outside, resulting in greater thrust. The HR nozzle has proven to provide up to 10% more thrust compared with a conventional 19A nozzle.
New blade design. Wärtsilä's hydrodynamic department designed a completely new blade to fulfill the vessel's requirements. The new blade design was challenging, because many parameters were outside the nozzles' normal range. To limit the propeller's tip speed, the diameter was reduced to 5,200 mm from 6,200 mm.
The wake field at the ship's aft was investigated by measurements and tuft tests. It is important for propeller design, because it determines the propeller's inflow and, therefore, cavitation behavior, hull pressure fluctuations, and changes in thrust and torque during each propeller blade revolution.
Improved maneuverability. Two large, retractable thrusters were installed forward in the vessel. These thrusters, each with an input power of 4,500 kW, are equipped with 3,400-mm controllable pitch propellers running in HR nozzles. Each thruster is powered by a horizontal electric motor. To generate the electric power, three generating sets were supplied. Each engine, rated at 3,840 kW, runs on HFO. The two thrusters can generate extra thrust of 160 metric tons in bollard condition. 
|