RSS with resistivity capabilities delivers superior real-time LWD measurements
Geosteering and precise wellbore placement are more important than ever. While RSS is typically used for this reason, the marketplace is sometimes challenged by the high cost of the system, a barrier to entry for smaller and mid-sized companies.
Recognizing that fragmentation generally yields more effective technology innovation and deployment, National Oilwell Varco (NOV) invested in a suite of RSS tools to make previously unavailable systems accessible to independent directional drilling companies. This broadening of the market also makes the technology more accessible to national oil companies, which have historically been limited to several major service providers. In this new scenario, NOV acts as an unbiased, third-party technology provider that enables independent service companies to offer advanced directional drilling services. One new technology that has emerged in this environment is the VectorZIEL system, which is designed for the challenges of more complex 3D wellbores.
TECHNOLOGY ORIGIN
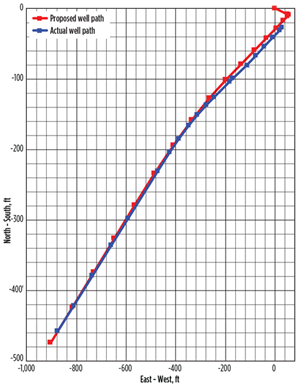
The VectorZIEL is a three-dimensional push-the-bit RSS that provides full directional control of the wellbore placement. This technology has near-bit inclination, near-bit azimuth, and gamma ray, as well as an integrated pulser for real-time data transmission. This includes survey data, gamma ray, tool steering setting, and tool diagnostics. The system is an automatic steering tool for three-dimensional drilling, designed to deliver the industry-accepted benefits of RSS tools, including increased rate of penetration (ROP), improved cuttings removal, and precise trajectory control, in turn allowing creation of higher-quality boreholes at reduced operational costs, Fig. 1. The system can yield 8°/100 ft (8°/30 m) dogleg severity (DLS) under normal drilling conditions. Currently, the system is available for use in 6-in., 8½-in. and 12¼-in. holes
An azimuthal measurement system allows the new RSS system to achieve true near-bit, survey-quality directional measurements. To control toolface, the electronic boards and control system must remain geostationary. The system achieves this using a stationary sleeve that is decoupled from the collar. The sleeve is held geostationary by the directional pads, which push against the wellbore. This sleeve also houses the directional sensors and gamma ray sensor. A generator that uses mud flow provides the VectorZIEL system with power, and the system can be run stand-alone or with a motor for performance drilling.
The system is programmed to the desired inclination, azimuth, and aggressivity setting, and when the programmed target is reached, it will hold that direction until a different inclination and/or azimuth is sent to the tool. Average downlink time is about 7 min., depending on what command is sent to the tool. Once a downlink is sent, the tool will pulse up a confirmation of the setting that was received downhole. Key features of the new RSS include the following:
- An integrated measurement-while-drilling (MWD)
system for real-time feedback while drilling, near-bit
inclination, azimuth and gamma measurements. - Closed-loop trajectory control, which requires minimal intervention from surface and automated downlinking using a surface downlink skid—that is, autonomous drilling.
- The ability to make automatic adjustments to maintain wellbore inclination and azimuth.
- The ability to integrate additional MWD and logging-while-drilling (LWD) components to create a full directional
drilling and logging bottomhole assembly (BHA).
IMPROVING A PROVEN RSS
NOV applied a rapid and comprehensive review of the technology that culminated in the development of the VectorZIEL Mark II system, which is currently being commercialized. The improvements were made at the company’s Research and Development Test Center (RDTC) facility in Navasota, Texas, which is used to test newly developed products in a safe, controlled, and non-hydrocarbon-producing environment. The RDTC includes a fully operational drilling rig and a 31,000-ft² shop used for dynamometer testing of downhole mud motors and flow loop testing of other downhole tools. The test rig is a 375-ton, 1,500-hp Ideal Prime rig, equipped with IntelliServ wired drill pipe.
To help internal stakeholders and interested customers determine the viability of the improved RSS system, NOV began testing at the RDTC with the following objectives:
- Control the test environment, improving safety
and accessibility - Increase the speed-to-market timeline by understanding advantages and challenges upfront
- Decrease commercialization costs and identify ways
to reduce overall system costs for customers.
The new system introduces a number of significant reliability improvements, including vastly improved mechanical components, hydraulic system, electronics boards, and pulsers. Azimuthal gamma ray is also a key feature of the improved system. By using the new system in a trial well at the RDTC, NOV was able to ascertain if it was ready for full commercial deployment, possible improvements, and next steps for system rollout.
In late second-quarter 2019, NOV began testing the VectorZIEL Mark II system at the RDTC. The well plan involved successfully building a curve section from 11 to 86° inclination and 240° azimuth at an average of 5.6°/100 ft. The section drilled was from 3,542 to 4,876 ft (a total of 1,333.65 ft) for 36.4 drilling hours and 50.7 circulating hours. Drilling parameters were set as follows:
- Weight on bit (klb): 4 to 10
- Flowrate (gpm): 550 to 600
- RPM: 60 to 80
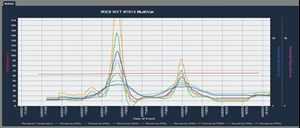
A key feature of the new RSS system and primary purpose of the test was successful integration of a symmetric propagation resistivity (SPR) tool with the RSS BHA. The SPR tool was designed to provide integrated LWD measurements via high-quality resistivity logs, obtaining real-time phase and attenuation measurements at multiple depths of investigation, Fig. 2. The secondary purpose of the test was to prove the effectiveness of the new system’s upgraded features.
Testing followed several phases. Surface testing including validating the successful electrical connection between the RSS and the SPR tool on the rig floor, confirming that the SPR tool was powered up, and communication between tools. There were no issues, with smooth makeup procedures on the rig floor, as regards the system’s mechanical interface. Proper power and data communication between the RSS and the SPR tool was provided. On the software side, proper functionality and recorded data with timestamps from the SPR tool’s eight resistivity sectors were also achieved. All surface systems decoded the real-time data successfully.
The second testing phase confirmed the potential of the upgrades to the VectorZIEL system to improve performance versus that of the original unit. This was considered secondary, as the main goal was to prove the viability of measurements from the integrated SPR tool. New generator parts were designed to improve erosion resistance, while a higher-pressure downlinking valve was installed. A new hydraulic pump and motor, ruggedized contact ring, stronger piston/plunger housings, and locking nut/shaft locking device were all implemented to improve equipment life and reliability. Wiring was modified to be harder to ensure continued communication, and new hardware was added for the electronics board in instrumented stabilizer. The test successfully proved that the high-pressure downlinking valve operated successfully.
The testing phases confirmed that SPR tool integration into the RSS was successful. Performance-wise, the drilling curve was built from 11.32° inclination/244.51° azimuth in to 85.79° inclination and 240.69° azimuth out. Average DLS during the run was 5.6°/100 ft when running the tool at 30 to 100% aggressivity, and maximum DLS was 9.1°/100 ft at 100%.
FUTURE DEVELOPMENT
Another important feature of the VecorZIEL Mark II will be streamlined steering ribs. The new ribs will offer a 50% reduction in contact area with the wellbore wall, thereby minimizing the risk of stuck pipe incidents, and the new ribs will have no detrimental effect on the steering capabilities of the tool. The ribs were tested successfully in the 12¼-in. configuration in June, with no issues observed. A new drill-out mode and reaming mode also will be added. The drill-out and reaming modes are largely software developments designed to increase stabilization and damping of the non-rotating housing on the new RSS tools. The system successfully entered and exited drill-out mode via pump cycles and provided a clear indicator at surface.
Real-time optimized telemetry will also be necessary, since increased LWD options require the VectorZIEL Mark II to have more flexible telemetry schemes. Real-time optimized telemetry allows for higher-frequency LWD data update rates relative to other, less critical parameters. The telemetry schemes with the system will be very flexible, with user-selected options and configured datasets matching whatever BHA configuration is necessary. Enhanced schemes will provide survey QAQC metrics, allow increased gamma update rates, and will include simplified tool diagnostic data, such as shock and vibration.
Downlink reliability improvements are also being made to the system. NOV’s new high-pressure downlink skid has been tested successfully at high standpipe pressures. High-frequency recordings of system turbine speed have helped improve understanding of dominant factors, with data showing that the majority of downlinking issues are the result of insufficient flow at the bypass skid and lower-than-required RPM drop at the downhole turbine. NOV has designed a new valve and actuator for the new RSS system that allows more predictable and reliable downlinks. Also, software algorithm improvements will result in large increases in downlink pulse amplitude.
CONCLUSION
In a challenged market, a new type of thinking was necessary. NOV combined RSS technology with decades of downhole drilling tool experience to design, test and launch an improved version of the VectorZIEL system with integrated SPR capabilities. Benefits include near-bit resistivity and azimuthal gamma, higher operating limits for greater performance, reduced erosive wear for lower operating costs, decreased non-rotating contact area, and reduction in tool parts for faster servicing. With rapid engineering development, this technology combination will further evolve, helping both small, independent directional drilling companies and larger operators in search of a solution that provides RSS performance, together with integrated LWD measurements.
- Coiled tubing drilling’s role in the energy transition (March 2024)
- Digital tool kit enhances real-time decision-making to improve drilling efficiency and performance (February 2024)
- E&P outside the U.S. maintains a disciplined pace (February 2024)
- U.S. operators reduce activity as crude prices plunge (February 2024)
- U.S. oil and natural gas production hits record highs (February 2024)
- Drilling advances (January 2024)
- Applying ultra-deep LWD resistivity technology successfully in a SAGD operation (May 2019)
- Adoption of wireless intelligent completions advances (May 2019)
- Majors double down as takeaway crunch eases (April 2019)
- What’s new in well logging and formation evaluation (April 2019)
- Qualification of a 20,000-psi subsea BOP: A collaborative approach (February 2019)
- ConocoPhillips’ Greg Leveille sees rapid trajectory of technical advancement continuing (February 2019)