Holistic optimization approach improves coring efficiency, sample quality
To improve initial production and ultimate recovery, we must first fully understand the reservoir rock. Full-gauge coring is the first line-of-sight into a reservoir. The actual formation samples recovered at the surface are the “ground-truth” that provides the basis for accurate reservoir evaluation and modeling. Cores are almost always acquired—and in many countries are required—for exploratory wells. They also are taken in development wells, even in well-known areas, to help operators better understand or confirm that the reservoir rock in one well exhibits the same characteristics as in previous wells.
The larger the core size, the better for core analysis, because more information about the formation can be gathered in less time. Additionally, a core with larger dimensions means less, easier-to-mitigate invasion into the zone of interest, so better plots can be made.
It is often argued that cutting core is time-consuming and results in high costs per foot of core recovered. As tougher conditions are encountered more frequently, coring operations become more challenging and expensive. In deepwater applications, for example, temperature, pressure, depth, mud weight, and other parameters directly affect and diminish core barrel length and reliability, which results in increased cost for core acquisition. Interbedded and fractured formations on land, or offshore, can cause the core to become jammed, Fig. 1.
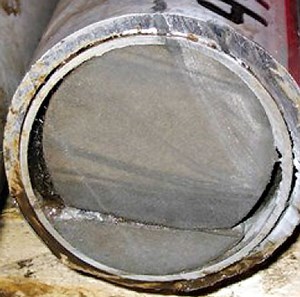
When jamming occurs, several feet of core are usually damaged. The damage can be mitigated with an anti-jamming or jam mitigation system. Concentric inner core barrel sleeves automatically telescope if a rock sample becomes jammed in the core barrel, allowing operations to continue without interruption.
Depending on the barrel size, the system can accommodate three to four successive jams before requiring POOH, reducing coring trips necessary to recover the same amount of core. However, core diameter is often sacrificed.
HOLISTIC APPROACH
Improved core barrel. Core barrel limitations, particularly the risk of collapsing inner tubes, typically limit the barrel length and, with it, the core that can be acquired in a single run. To overcome this limitation, a new core barrel design targeted the optimizing of hydraulic capacity and mechanical integrity, Fig. 2. By delivering greater overall total flow area between inner and outer assemblies, and providing inner tubes with higher rating against collapse, the new core barrel maximizes operational thresholds. Higher flowrates and/or longer barrel lengths can be used with the new design, while ensuring a reliable operation and reduced risk of collapsing the tool’s inner tubes, even in difficult conditions.
The new tool dimensions accommodate larger-diameter core samples. The core barrel is capable of delivering a 4-in. sample for specialized coring operations that require the use of a jam mitigation or on-site core access system. A large-diameter, 4½-in. core can be delivered for conventional operations. The larger core samples improve core integrity, recovery, efficiency and analysis.
The system offers heavy-duty outer barrels; double-shouldered, and high-torque connections, spiral-blade stabilizers; and application-specific bits. Combining the core barrel with non-rotating inner tube stabilizers prevents mechanically induced core fracturing during long coring runs, and enables quick, efficient surface processing. The system also can be combined with the company’s CoreGard low-invasion coring system, to reduce filtrate invasion of the core for improved laboratory analysis.
Successful coring operations are supported with hydraulics modeling in the planning stage, where the target run length can be compared to the theoretical maximum barrel length. During job execution, these hydraulics models are used to safeguard the coring operation against the risk of inner tube collapse.
Jam mitigation. For fractured/interbedded formations and when coring through faults, a jam mitigation system is used incorporates telescoping inner-core barrel sleeves into the core barrels, to eliminate the effects of core jamming, Fig 3. The system works as follows: 1) the first jam enters the sleeve and shears the pins; 2) the freed inner sleeve then telescope up the core barrel, and the second sleeve receives new core; 3) the second jam releases the second telescoping inner sleeve; 4) coring continues until the third jam occurs. Several successive jams can be alleviated before needing to pull out of the hole, reducing the number of coring trips required to recover the same amount of core.
Purpose-built bits. High-efficiency PDC core bits have been designed with enhanced hydraulics and cutter efficiencies for longer core runs, higher ROP and improved sample quality, Fig. 4. Although the core bit has optimized hydraulics, its main goal is to cut formation. Extensive simulations were performed to ensure bit stability, to maximize ROP without compromising core quality.
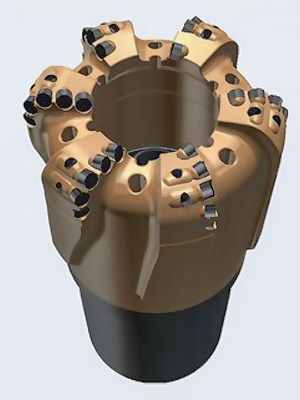
The bit’s premium polished cutter technology stays sharp in abrasive formations and resists vibration-induced impact damage. Optimized cutting structure methodologies are employed to fully customize the bit profile and cutter layout to a specific application. This results in higher ROP, longer runs with improved stabilization and lower risk of core jamming.
To maintain stability and coring efficiency throughout the run, all the cutters engage with the formation uniformly and consistently, virtually eliminating destructive bit whirl and damage to the core.
Safe surface handling. Similar to sample acquisition, handling, processing and transportation of the core can impact the quality of information that can be obtained from recovered formations, Fig. 5. Additionally, proper handling at the surface improves efficiency along the critical path at the rig site, Fig. 6.
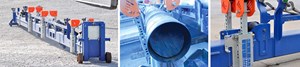
To facilitate best practices, the company developed a universal wellsite kit, to ensure core handling and processing are fully integrated into the overall recovery service. It covers a full range of topics, from recovery to the laboratory. It is structured with modular solutions that can be combined to satisfy varying operator needs, and to match different operational settings.
CASE STUDIES
Middle East offshore. An international oil company operating offshore in the Middle East required a high-efficiency coring system capable of delivering good core quality in a single run. The objective was to acquire a 4-in. core sample in as few runs as possible in a limestone section interbedded with anhydrite, without compromising core quality.
To maintain core quality, non-rotating stabilizers were used to steady the inner tube downhole and improve surface handling. Applying the system’s fully integrated, efficient, surface handling equipment and procedures and following the highest HSE standards, pristine core samples were recovered, processed, and protected as the basis for accurate formation information from laboratory analysis.
All of the operator’s coring objectives were met, with the following results:
- 270 ft of core recovered in one run
- 100% core recovery
- 100% barrel efficiency
- Excellent core quality
- 150% ROP improvement over previous wells
- Additional core run saved through a longer barrel set-up
- The operation saved 1.5 days of rig time and approximately $375,000.
Middle East onshore. In Kuwait, an operator required a system that could deliver excellent-quality cores from fractured, medium-hard clastic formations. In one well, a conventional system extracted 60 ft of core at an ROP of 6 ft/hr. The operator wanted to improve recovery and ROP. The provider recommended switching to the new HT30 Max coring system and combining with the jam mitigation system. The results were good, with ROP increasing gradually to 40 ft/hr. The core was delivered in four runs rather than eight, saving two days of rig time. In the next well, the new BHI system was run with jam mitigation activated on all runs, which led to 377 ft of high-quality core being delivered in three runs versus six, saving four days of rig time.
West Texas. In the Permian basin, an operator planned to recover 1,020 ft of core in four runs, then drill ahead between the two zones of interest between runs two and three, Table 1.
However, based on the success of the first run, the well team decided to core straight through the planned 160-ft drill-ahead to save a trip. The extra footage was cored, resulting in 1,160 ft of core in four runs. The same-style 8¾-in. PDC bit was used for all four runs. Since the plan was exceeded, core recovery was 100%, and the amount of sample was more than was originally planned, after the decision to core the drill-ahead footage. Eleven days of rig time were spent for all four runs. The methodology saved two trips and five days of rig time, totaling approximately $250,000.
This was the first well of a two-well planned project. Yet, because of the success, the operator added a third well to be cored with the new high-efficiency system.
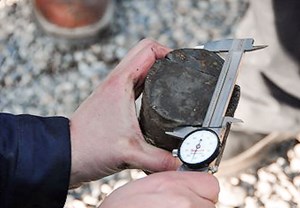
TOOL/PROCEDURE BENEFITS
With advances in coring, it has become less time-consuming and costly for operators to gain a direct line-of-sight into their producing reservoirs, Fig. 7. The recovery leads to better decision-making earlier in the field development process.
- Applying ultra-deep LWD resistivity technology successfully in a SAGD operation (May 2019)
- Adoption of wireless intelligent completions advances (May 2019)
- Majors double down as takeaway crunch eases (April 2019)
- What’s new in well logging and formation evaluation (April 2019)
- Qualification of a 20,000-psi subsea BOP: A collaborative approach (February 2019)
- ConocoPhillips’ Greg Leveille sees rapid trajectory of technical advancement continuing (February 2019)