What's new in production
The birth of the Digital Oil Field (DOF) could arguably be fixed as the date, about 15 years ago, when BP introduced its “Field of the Future” program. The company has used the time to apply it widely, within its own operations, including Thunder Horse field in the deepwater Gulf of Mexico.
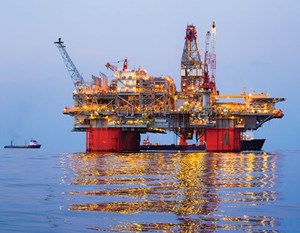
DOF for small operators. That’s certainly no surprise, given the company’s copious horsepower, but is DOF capability beyond the reach of the small operator driving a four-cylinder econobox? It turns out, no. An interesting paper, “A small operator’s implementation of a digital oil-field initiative,” (Eldred et. al., 2015) describes initiatives by companies operating in the San Joaquin Valley (SJV) to have a basic surveillance system in place for their assets.
But first, the authors outline the problem: “Many operators have made significant implementations of digital oilfield (DOF) technology and processes. DOF has focused on objectives to increase operational efficiencies and production. The technical literature has many references to DOF from major operators, national companies, and service providers, which cover a number of different engineering workflows, e.g., production surveillance, artificial lift optimization, waterflood management. A small, independent company faces many of the issues of large companies, but often has fewer resources and a shorter time horizon than larger companies. So, identifying and developing DOF processes pose particular challenges.”
The authors note that various initiatives have been undertaken in the SJV since the mid-1980s, to monitor and assess the magnitude and progression of surface subsidence, reservoir compaction, and wellbore damage. These initiatives used numerous tools, such as tilt meters and microseismic imaging. But, as always, operators benefit only if the right information, in the right context, is presented to the right person, at the right time.
That’s a lot of stuff to get right. The paper describes one small, independent production operator’s “digital oilfield journey,” which they labeled the “Reservoir Surveillance Initiative (RSI).” The goal was to develop DOF workflows to increase production efficiencies, reduce downtime, increase production and reduce risk.
This involved a several-year plan to move from, as they put it, the “current state”—technical professionals working in their specialty, using specialist applications—which inevitably disregards or minimizes such things as interdependent data and boundary conditions.
The destination was to the “desired state,” collaborative workflows, best illustrated by a philosophy that data—e.g., production, completions, reservoir analysis—are available to all stakeholders, all the time, in the right context.
Results. Space limitations prevent describing how the RSI process evolved, but the solution has key components:
- GI-based visualization: This brought disparate data into one common framework that integrated information about wells, steam-and-soak cycles, worker and drilling reports, downtime and historical production, and measurements captured from multiple sources. This is all presented in an easy-to-use, GIS-based visualization map.
- Data-driven diagnostics: Steam-driven production techniques were automated, replacing manual, analytic spreadsheet calculations. A diagnostic engine, called the “Steam Candidate Picker,” was developed that runs pre-defined business rules to identify prime candidates for steaming.
- Pump-data alarm rationalization and management: A key metric in any steamflood operation is how the lift system or pumps are working. Pump downtime has a direct impact on production. Pump diagnostics from a third-party application were integrated within the tool and combined with real-time measurements. These are presented to the engineers through the unified web portal as an alert in nearly real time.
According to the paper, the RSI fully leveraged digital oilfield processes and technology, to increase operational efficiencies and enable much-higher-value operational decisions. For a small independent production operator, the focus was on delivering high value, at reasonable cost, and in a relatively short time. The RSI process gained internal credibility by identifying “low-hanging fruit” to generate “quick wins” and “quick value.” Nonetheless, careful project management was essential to achieving milestones—on time, on spec, and at projected cost.
The authors note what could be called the X-factor in most carefully laid plans: people. Specifically, the challenge was to change how they work. They all point out that for a small operator, there is no redundancy in professional staff responsibilities. Thus, implementing a collaborative work environment supported by cross-discipline workflows has become a necessity to meet ever-increasing demands and targets.
Correction. In my February column, a layout error deleted the name of the company that has deployed what it calls the world’s first fully electric, fully mobile well stimulation system. The company is U.S. Well Services.
- Applying ultra-deep LWD resistivity technology successfully in a SAGD operation (May 2019)
- Adoption of wireless intelligent completions advances (May 2019)
- Majors double down as takeaway crunch eases (April 2019)
- What’s new in well logging and formation evaluation (April 2019)
- Qualification of a 20,000-psi subsea BOP: A collaborative approach (February 2019)
- ConocoPhillips’ Greg Leveille sees rapid trajectory of technical advancement continuing (February 2019)