Development of gas-tight connection for deepwater drilling and completion operations
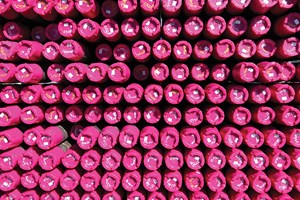
Operators exploring in the Gulf of Mexico are drilling increasingly more complex wellbore geometries, with additional technological challenges that combine deepwater environments with increased hole depths. To safely and efficiently deliver the wellbore requires a high level of engineering expertise, combined with specialized tools and completion technologies. Tubulars used in these deepwater operations provide the required high-tensile and torque ratings.
However, mechanical performance is just a starting point, and other critical criteria must be met to ensure operational efficiency and a safe working environment. The available OCTG-based connections and drill pipe risers meet some of today’s requirements, but operators have challenged the service industry to develop new gas-tight tubular connections designed specifically for the following applications: 1) high-pressure completions/fracture stimulations; 2) drill stem testing; 3) managed pressure/underbalanced applications.
TECHNOLOGY RESPONSE
In response to client requests, Vallourec’s R&D engineering team started working on a new gas-tight connection with a metal-to-metal rotary seal. The engineering process used extensive finite element analysis (FEA), which produced a hybridized version of a premium, double-shoulder, gas-tight connection from a drill pipe riser.
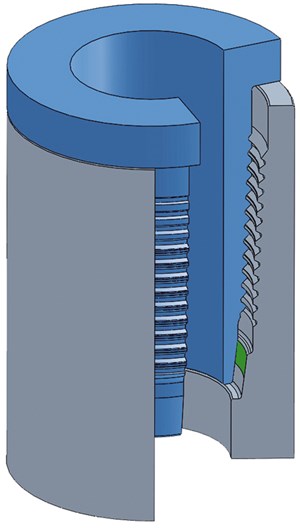
The new connection, called VAM Express-M2M (Fig. 1), provides the high-pressure capability of premium casing connections, coupled with the robustness and increased torsional strength associated with a double-shoulder rotary connection. Qualification testing was performed on the critical sizes and involved standardized make-and-break testing, and over-torque analysis, in addition to combined loading and fatigue analysis. In accordance with the company’s commitment to safety, the connection provides one of the industry’s highest operating margins for a gas-tight connection and is rated to withstand 30 kpsi, internal pressure, and 25 kpsi, external pressure. The connection can be used for both drilling and completion operations, so it can deliver considerable cost savings due to improved
operational efficiency.
DESIGN CRITERIA
The criteria for developing a new gas-tight connection for deepwater stimulation operations was based on the following requirements:
- Safety. Due to the severity of the conditions during completion operations, safety was a primary concern. This would require comprehensive gas-tight sealing capability to eliminate trapped gas when running the string.
- Ease of use. To simplify operations and reduce costs, completion strings should be run by the same drilling crew and rig.
- Robustness. Completion strings are usually run-in on several trips on one rig and will generally be used on multiple rigs. These connections must be strong enough to withstand several runs, which requires resistance to galling, while remaining competent throughout multiple make-ups and break-downs.
The primary objective for the R&D team was to design a connector with a minimum gas-tight rating of 20,000 psi, that has similar operational capabilities to drilling products and is inherently robust by design. The best way to accomplish this objective was to base the new gas-tight connection on field-proven OCTG connectors with metal-to-metal seals that have been deployed successfully in the field for decades. The new joint would also feature a premium double-shoulder drilling connection that has demonstrated good mechanical performance and exceptional longevity in field applications. The main features inherited from the existing double-shoulder drilling connection include:
- Capable of functioning as a drilling connector.
- Capable of high torque, up to 100% more than comparable API connectors provided by the primary and secondary shoulders, and the proprietary thread design.
- Easy stabbing provided by the optimized taper of the stabbing flank of the thread profile.
- Quicker make-up and deeper stabbing provided by the connector taper and proprietary thread design.
- Improved fatigue resistance provided by an elliptical thread root design.
- Reduced risk of wedging, due to the reversed angle on thread crests.
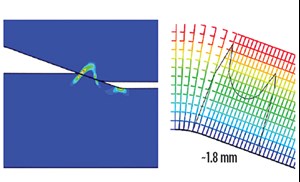
Next, based on historical knowledge and application expertise, the design team concluded that the best place to position the seal was in the non-active cylindrical part of the pin nose. This section is sufficiently thick to provide stable behavior through the loading cycles while guaranteeing a gas-tight seal. Once the location of the seal was selected, additional design criteria were identified to ensure optimized performance and a safe working environment, including:
- Ability to resist high gas pressures. The physical interference between the pin and the box must generate sufficient stress to ensure gas-tight capability.
- Ability to guarantee gas-tight performance throughout the life of the connector. The seal must always work in the elastic zone of the material. It must have sufficient contact surface and contact pressure on the seal throughout the working life of the connector.
- Ability to avoid risks of yielding of the pin nose to avoid a potential safety hazard when breaking out the connection (trapped gas). The connector shall avoid geometries with potential gas-trapping potential.
- Ability to avoid galling. The higher stress on the seal must be lower than the material yield strength at all loading points. The design should prevent sudden contact pressure increases on the seal.
During the development phase, the team experimented with a contact taper/taper design but dismissed the option, since this type interface creates a dispersion of stress repartition and is more sensitive to galling, and increases the risk of losing sealability under tension, Fig. 2. These factors led designers to use a contact taper-on-radius design, because it naturally controls peak stress, allowing for a smooth contact increase on the seal, making it less sensitive to galling, Fig. 3.
The final design of the connection seal includes a soft taper on the pin nose’s outside diameter and a seat with a large radius on the box. The taper provides the connector with a smooth contact increase during the make-up phase (Fig. 4), and the seal radius helps distribute stress, thus reducing the risk of galling.
QUALIFICATION PROCESS
A review of standard drilling practices and fracturing operations was performed, using the new VAM gas-tight connection to assess performance. Preliminary testing was based on calculations using finite element analysis (FEA), before actual physical tests were performed. Based on the above listed evaluations, the qualification program was defined as follows:
- Evaluation of sealability and stress distribution, as well as load test (pressure, tension, bending and compression).
- Evaluation of fatigue resistance-resonant fatigue bench test.
- Evaluation of torque capacity.
- Evaluation of galling resistance and pressure after several make-ups and break-downs.
This intensive qualification program was intended to confirm expected performances and validate field applicability for the new connection. All of the qualification tests were performed using calibrated test devices, and samples were machined/prepared to reproduce the most critical configurations.
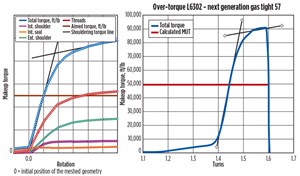
For each size, the most extreme cases of tolerances and make-up torque were chosen to ensure that the critical combinations were tested: 1) The combined load configurations tested were manufactured with the minimum interference and contact pressure, which assessed pressure in the critical configuration; 2) The make-and-break configuration tested was manufactured with the maximum interference and contact pressure, and therefore assessed the degree of galling in the critical configuration.
TORQUE CAPACITY EVALUATION
The FEA evaluation gave precise data concerning the connector’s behavior during make-up. After FEA analysis, the testing was confirmed by physical tests. Figure 5 shows the make-up curve comparison between FEA and physical testing. These tests confirmed the joint’s torque capacity, up to 100% more than API, and that over-torque behavior meets the required specifications.
GALLING RESISTANCE EVALUATION
FEA verified that the higher stress pressure on the connector was lower than the material yield strength at all load points, and the design prevented sudden contact pressure increases on the seal. This behavior will mitigate the risk of galling on the seal. The joint’s resistance to yielding and galling was confirmed by performing 100 actual make-and-breaks, Fig. 6.
GAS-TIGHT EVALUATION
FEA testing confirmed that there is sufficient contact pressure on the seal at all loading points of the working envelop of the connector to achieve the sealing objectives, and guarantee safety during operations. The physical load testing was performed with nitrogen at a third-party laboratory to guarantee the impartiality of the results.
The tested envelope corresponded to 90% of the Von Misses ellipse performance of the gas-tight connection. The pressure rating achieved during the cycle was up to 30 kpsi, internal pressure, and 25 kpsi, external pressure, for the smallest size, and 25 kpsi, internal pressure, and 20 kpsi, external pressure, for the largest size. To more accurately simulate well conditions and increase test severity, the cycle included combined internal/external pressure in tension or compression and bending up to 15°/100 ft. Figs. 7 and 8.
FATIGUE EVALUATION
An accepted industry fatigue performance standard maintains that a drill pipe connector should always be stronger than the welded pipe. To confirm the gas-tight connection met this standard, fatigue resistance was verified, using FEA and a stress concentration factor (SCF) methodology. SCF tangential located in the critical point of the connector was compared to the weakest point of its associated pipe. The results indicated the connector would have long fatigue life.
Next, resonant fatigue machines were used to bench test samples at a frequency of approximately 28 Hz. All of the samples were filled with water and tested at one atmosphere, with a constant 200-psi internal pressure. Axial strain gauges on the outer diameter of the pipe body indicated the new gas-tight joint would provide superior fatigue resistance.
OPERATIONAL BENEFITS
The new VAM Express-M2M connection is a cost-effective gas-tight connection that combines the capabilities of a high-pressure drill pipe riser with the robustness of a premium double-shoulder rotary connection. The combination of features gives operators and drilling contractors the flexibility to use the same tubular string for both drilling and completion operations, without compromising performance or safety. The connection is optimized to prevent gas entrapment and provides a high margin of safety. It also has the ability to complete multiple fracing jobs without repair, and is easy to fish from a wellbore, due to its slim-connection design.
ACKNOWLEDGMENT
This article is derived from IPTC paper 18568, “Development and Qualification of a Next Generation Gas Tight Connection Incorporating Metal-to-Metal Technology.” It was originally presented at the International Petroleum Technology Conference, Doha, Qatar, Dec. 6–9, 2015.
- Coiled tubing drilling’s role in the energy transition (March 2024)
- Advancing offshore decarbonization through electrification of FPSOs (March 2024)
- The reserves replacement dilemma: Can intelligent digital technologies fill the supply gap? (March 2024)
- What's new in production (February 2024)
- Subsea technology- Corrosion monitoring: From failure to success (February 2024)
- Using data to create new completion efficiencies (February 2024)
- Applying ultra-deep LWD resistivity technology successfully in a SAGD operation (May 2019)
- Adoption of wireless intelligent completions advances (May 2019)
- Majors double down as takeaway crunch eases (April 2019)
- What’s new in well logging and formation evaluation (April 2019)
- Qualification of a 20,000-psi subsea BOP: A collaborative approach (February 2019)
- ConocoPhillips’ Greg Leveille sees rapid trajectory of technical advancement continuing (February 2019)