When it comes to evaluating automated well construction opportunities, the industry is an unabashed copycat with few disciplines or industries off-limits. In keeping with the spirit of inter-industry technology transfer, developers of automated drilling processes could learn a thing or two from Australian miner Rio Tinto, which likewise is dealing with a miserable commodities market at the moment.
“It took Rio Tinto about five years to turn a pit in Western Australia into an autonomous operation with autonomous drilling machines, autonomous trucks and trains, all of which are run from a remote control center,” John de Wardt, oil and gas management consultant, told the IADC Drilling Engineering Committee (DEC) during its quarterly technology forum in September.
Not surprisingly, a former Rio Tinto technology manager and mechatronics expert has been pegged as an advisor to a proposed joint industry project (JIP), aimed at accelerating the completion of an initial look-ahead report on a Drilling Systems Automation Roadmap (DSA-R). In pitching the JIP via a video hook-up from the Colorado headquarters of his namesake consultancy, de Wardt said, with 10 sponsoring companies each paying $10,000, the initial version of a “comprehensive overview of a drilling systems automation roadmap” could be available within six months. As the project manager, de Wardt said the proposed roadmap, adapted from the structured process developed at Sandia National Laboratories, is being engineered to describe potential automation development over the next 10 years.
“There is a desire and need in the drilling industry to develop a highly automated system, but the question is, what is a highly automated system? Different people have different opinions, and the roadmap with its vision provides an opportunity to define what the future can look like and, therefore, develop a common understanding of where we’re going as an industry,” he said.
“The industry has a significant need for a roadmap, as our efforts have been fragmented. We have a lot of areas of automation being developed, like with rotary steerable systems and MPD, but as an industry we struggle to integrate these things together, because of the fragmentation.”
The footprint of the initiative, he said, has broadened through affiliation with the SPE Drilling Systems Automation Technical Section (DSATS) and the IADC Advanced Rig Technology Committee (ART), as well as the Association of Unmanned Vehicles Systems International (AUVSI). However, what began as an all-volunteer initiative in 2013, with myriad participants in and outside the oil and gas industry, has progressed “at a much slower pace than typical funded industry roadmap initiatives,” according to de Wardt. While not the best of times to ask companies for any extra cash lying about, he said without funding the project could take more than two years. “Phase One will create a product for the industry that will enable the industry to receive the benefits from drilling systems automation sooner, rather than later,” he said.
“Other industries have definitely realized the significant business value of comprehensive automation,” says de Wardt, once more singling out miner Rio Tinto. Complementing its autonomous operations in the remote and resource-rich Philbara area of Western Australia, Rio Tinto’s “Mine of the Future” project also encompasses automatic wharf operations, featuring human and autonomous machine interfaces for lifting and handling containers from ship to truck or rail—again all controlled remotely. “By actually creating an autonomous wharf, they found productivity went up 18%, while maintenance dropped 27%, and field consumption was down 22%.”
And, though it may come off as somewhat contradictory, automated systems do not de-value the human role in the process, de Wardt said. “One thing we’ve discovered is that there is an element of fear that automation means replacing people, and that’s not true. As we explain this out, we can show the role of people in the future, and how they will be integrated with automated systems,” he said.
Disassembly not required. The third-quarter DEC forum, which was devoted exclusively to automation and instrumentation, also included updates on the SPE- and IADC-sponsored DSATS and ART programs, as well as the latest on GE Oil & Gas’ development of in situ non-destructive BOP inspection technology with 4D digital fingerprinting.
Noting a definitive example of leveraging technology proven elsewhere for use in oil and gas, Martha Saker, GE senior product manager for non-destructive testing technology, said the genesis of the BOP inspection tool and associated software can be traced to the non-invasive imaging techniques used routinely in the medical industry. From there, she said, non-destructive inspection technologies were developed, and now used, to monitor nuclear reactors, aircraft engines and power generators, before eventually making its way to the E&P sector.
According to Saker, the primary benefit of the emerging inspection and condition-based maintenance technology is reducing the downtime and hazards associated with BOP inspection and certification events. Digital fingerprinting, she said, also allows monitoring throughout the life cycle of the equipment with traceable records.
“The primary benefits of this technology is that it allows us to inspect a BOP from the rig floor without having to tear down and then reassemble the equipment. Tearing down the BOP is hazardous and difficult to perform, and it usually must be taken off the rig for inspection,” she said. “It makes inspections less painful and costly, while also being very accurate and reliable.”
Saker said the in situ inspection technology must still clear regulatory scrutiny before full-scale commercialization can proceed. “Since they (regulators) say it is okay for nuclear reactors, it should be okay also for BOPs,” she said.
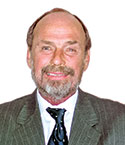
- Coiled tubing drilling’s role in the energy transition (March 2024)
- Using data to create new completion efficiencies (February 2024)
- Digital tool kit enhances real-time decision-making to improve drilling efficiency and performance (February 2024)
- E&P outside the U.S. maintains a disciplined pace (February 2024)
- U.S. operators reduce activity as crude prices plunge (February 2024)
- Drilling advances (January 2024)
- Applying ultra-deep LWD resistivity technology successfully in a SAGD operation (May 2019)
- Adoption of wireless intelligent completions advances (May 2019)
- Majors double down as takeaway crunch eases (April 2019)
- What’s new in well logging and formation evaluation (April 2019)
- Qualification of a 20,000-psi subsea BOP: A collaborative approach (February 2019)
- ConocoPhillips’ Greg Leveille sees rapid trajectory of technical advancement continuing (February 2019)