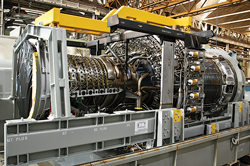 |
The new LM2500 FPSO package is a lighter, smaller-footprint version based on one of GE’s most well-known engines. |
|
World Oil: Could you give us a general overview of GE’s latest technological developments for oil and gas, particularly offshore.
Lammas: We’re working on several new lightweight, small-footprint packages. For the LM2500 gas turbine—originally developed as a ship engine—we’ve got a new oil and gas package, where we’re significantly reducing the weight and footprint. We’re looking at both a power-generation and a compression package for the LM2500, with weight reduced down by 25%, which is significant, and the footprint down by 15% (see figure). We also believe that with the changes we’re making, we can save about 12% of the lead time, too.
We’re working with our Aeroderivative team, looking at a power-gen-only package that is DNV-compliant. The first of them will be available the fourth quarter of this year. The new lightweight, small-footprint FPSO package and power-gen-only package will be available soon. We understand that the FPSO market needs more compact, lighter packages, so we’re actively pursuing those.
Compact compression is another area we’ve been working in for offshore. The first phase of the power density compressor is already on the market. We’ve just released the second step, where we’re continuing to increase the speed of the compressors, and shrink their footprint and weight. In combination with that, we’re also doing a lot of stage technology to develop higher-efficiency compressors. We’re going to higher speeds, which improves efficiency, and putting better aerodynamics into the compressors.
The next step is to develop high-speed compressors, where we’re putting some of the advanced aviation technology into the compressors. We’ll be testing those later this year. Those are a couple of years away from market.
WO: Has the boom in EOR and hydraulic fracturing influenced the direction of GE’s technology?
Lammas: Concerning unconventional recovery in the U.S., obviously we’re not the company that is fracing or working downhole, although we do make some of the instruments through our downhole technology business. We’re looking more at the consumption side, and how we can use the natural gas in the U.S., and better transport it. With CNG, we’re looking at producing some whole units that can supply the truck market, and at compact LNG systems using our recips (reciprocating compressors) rather than the big centrifugal compressors. This is a portfolio of products that help on the usage side as more natural gas becomes available.
In EOR, we’re looking at the wellheads, trying to make the whole system smarter. We bought an artificial-lift business from Wood Group about a year ago. There’s an opportunity to put a lot of technology into those machines from our existing GE motors business and GE Energy Management, and also apply some of the research we’re doing on higher-temperature electronics and insulation. We think we can bring all of that to artificial lift to make a much better product.
Abrasion resistance in ESPs (electric submersible pumps) is important, because we pump sand and other abrasive materials. We have a lot of technologies and coatings that we developed for helicopter engines and that we think can apply to the ESP business.
WO: How about subsea technology?
Lammas: We have a deepwater vertical tree we’re working on. We’ve seen a shift after the Mancondo blowout towards the vertical trees and away from horizontal trees. We’ve just upgraded the control system with the SemStar5 subsea electronics module. This is the leading technology with respect to controls, and that’s just going into service now, with a brownfield upgrade.
Also, with respect to subsea, we’re working on the next generation valves that can take high loads without lubrication for longer periods of time.
Finally, there’s the flexible tubing business that we acquired when we bought the Wellstream business about a year ago. We’re looking at larger diameters and higher pressures—applying our technology to improve durability and life of those components.
WO: You mentioned aviation. How has aircraft technology affected the oil business?
Lamma: I spent 20-plus years in the aircraft industry. GE is in a unique position, in that we’ve got GE Aviation, GE Health Care, GE Transportation, and they’ve all got technologies that can be applied across-the-board. For example, because in aviation they’re going more toward electrical-driven accessories on aircraft, you need high-temperature generators and motors. This leads straight to the high-temperature insulation we’re applying to electric motors in artificial lift.
Also, our first generation of new valves used a coating that was developed for aviation, an extremely dense nano-coating. If you look at most tungsten-carbide hardcoats, they are made up of particles and materials that are stuck together. If you magnify it dramatically, you will see voids and spaces in between them. When you start to get wear, you tear those particles out, and they become abrasives that wear the rest of the surface. So if you can shrink down the size of the particles until they become infinitesimally small, you end up with an incredibly dense, tough coating. We’ve improved wear capability by an order of magnitude, 10 times better, by going to these nano-coatings.
Similarly, non-stick coatings used on aircraft to prevent ice buildup can also prevent hydrates from accumulating in a pipe or valve.
Another recent addition to the portfolio is the measurement-and-control business. They have an inspection technology for subsea pipes that was developed for health care. What was really a medical X-ray detection system is now being applied to pipe inspection in the oil and gas industry.
WO: Are applications developed for oil and gas ever used in other industries?
Lammas: We’ve been looking at some manufacturing processes here that will now be applied in aviation. It’s not a one-way street. For example, in the oil and gas business we developed a process for enhancing surface finish on components. The better the surface finish, the better the performance. The aircraft industries are very interested in applying this to their parts. It’s inexpensive and doesn’t affect the shape of the part, but gives a much improved surface.
WO: In the aftermath of the Macondo incident, has GE done any work with blowout preventers?
Lammas: With respect to BOPs, we’re improving our shearing capability—we’ll be highlighting that at OTC—and also our control systems. We’re taking a control system developed for oil and gas and we’re using it in the topside control system for the BOP. The system is easily configurable, easily programmable, and applying it to BOPs to makes it easier for an operator to maintain and operate them.
We’re also working on problems such as how to detect gas kicks earlier. We need better methods of detection subsea, earlier warnings to the operator that allow him to act quicker instead of just looking at mud level rising. Another thing we can apply to the BOP is a black box, like those used in aviation. So if there is an event, we have a lot of information about what went on, and what went wrong. 
|