LUIS A. GONZALEZ, Marathon Oil; EDDIE VALVERDE and TOMMY LAIRD, Weatherford International
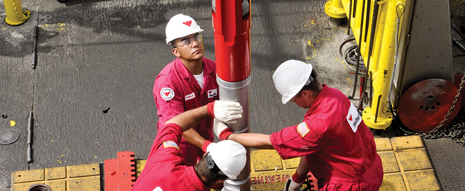 |
The RFID tool has been tested extensively under laboratory and test rig conditions, and in a Marathon well in North Dakota. |
|
There is a critical need in the industry to advance the technology in underreaming, specifically in operations where simultaneous drilling and underreaming take place. Hurdles have existed for several years for underreaming that could not be overcome by a simple, reliable, mechanical apparatus to activate or deactivate the tools. Activating a tool on demand offers options and underreaming techniques that will improve the way wells are drilled.
Traditional underreamers are activated or deactivated by dropping a steel ball down to the tool via the drillstring. The dropped ball creates a restriction in the drillstring, allowing nothing else to pass through the drillstring except drilling mud. RFID (Radio Frequency Identification) offers several key advantages. It creates an option to improve the performance of the underreamer by allowing multiple activations or deactivations without restricting the drillstring ID. The operator may elect to underream only specific sections of the well, where swelling formations cause stuck drillstrings, or perform full circulation in deactivated mode to clean out sections of the wellbore. RFID tools also provide full-bore access, which allows the wireline to be run through the reamer. Additionally, RFID capability allows for multiple tools to be run in the drillstring, and activated or deactivated on demand. Improved control of downhole tools provides opportunities to improve borehole quality.
Activation is controlled by pumping small tags through the bore of the tool, Fig. 1. RFID tags transmit commands as they pass through the tool; an electronic reader embedded in the tool reads the commands. All commands are stored into memory and may be downloaded, as well as other stored data, after the job is complete and pulled from the well. Extensive lab and field testing have been completed, and the data are presented here to demonstrate the value of RFID to enhance drilling and underreaming applications.
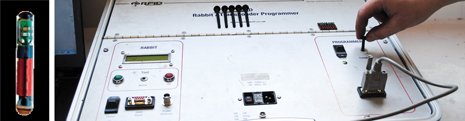 |
Fig. 1. Bare RFID tag (left) and the transponder and programming tool used to assign a unique ID to the tag. |
|
TECHNOLOGY BACKGROUND
Underreaming wellbores has been a normal operation in the drilling industry for many years. There are several types of tools designed to enlarge the wellbore after passing through a restriction. There are fixed-diameter tools, such as bi-center bits or fixed-diameter, eccentric tools placed in the drillstring above the bit. These tools have minimal opening diameters, because they must pass through a restriction before contacting the formation. Some of these tools are referred to as eccentric reamers. Several years ago, a concentric reamer was introduced, which allowed the tools to pass through the restriction and then be opened mechanically or hydraulically to enlarge the wellbore above the bit. For many years, these tools have provided reliable service to the drilling industry.
As wellbores have become more complex, the tools used to drill these wells must be adapted to fit the requirements. Concentric drilling reamers, for the most part, have been the same for the last 20-plus years. The tools have been operated mechanically by dropping a ball or dart to unlock the tool, allowing the arms or blocks to extend. Some tools on the market work strictly on hydraulics, which use fluid power to activate the tools to extend arms or blocks for cutting the formation. These hydraulic tools are still available in the market and offer reliable underreaming in most applications.
About seven years ago, some of the concentric reamers were redesigned, to allow the tools to be locked closed. The reasons for locking a tool vary from only wanting to ream a specific section of the wellbore, to having full circulation while coming out of the hole and not having the tool open. In most cases, once the tool is unlocked, it is always open when the hydraulic pumps are on. This prevents mud circulation when the tool is in the casing, an important requirement for many applications. Having the ability to circulate while pulling out of the hole (POOH) and not create any more cutting from the reamer being open, is important for hole cleaning. Some applications require only certain sections of the wellbore to be enlarged, such as salt sections. Now, many tools can be locked in the closed position by dropping a second ball or dart. In some cases, this deactivates the tool permanently. All of these tools require a ball or dart to be pumped down the drillstring ID and land in the reamer ID. When this is done, a permanent restriction is now in the drillstring ID, preventing wireline access to any of the tools below the reamer. There are LWD tools that run in the drillstring and have retrievable sources. Sometimes, it becomes necessary to pull these sources to the surface.
RFID BENEFITS
RFID (Radio Frequency Identification) has been used for many years outside the oil and gas industry to keep track of many applications in our daily lives. Since as early as the 1940s, RFID has had uses in automotive vehicle identification, automatic toll systems, electronic manifests, vehicle routing, electronic checkbooks, electronic credit cards, personnel identification, automatic gates, surveillance, and medical identification and patient history. For instance, toll collection is an everyday occurrence, where a passive tag is attached to your vehicle. As your car passes through the toll booth, an active reader senses the tag and deducts a toll charge from your account. The toll collection RFID is a reliable system that reads tags at a very fast pace, as vehicles pass through at 30 to 70 mph. There is now available a RFID reamer to offer the operator expanded operational capabilities not previously available:
Multiple activation and deactivation. The RFID capability provides multiple, on-demand activation/deactivation reliability to underreaming while drilling, limited only by the battery life of the tool. Multiple activation/deactivation becomes important, where selective reaming is required; for instance, only to ream salt sections each time that the tool is pulled into the salt. Continuously reaming these sections could be the difference in keeping the drillstring moving or having a stuck-pipe situation.
Mud conditioning. Mud can deteriorate when long sections are drilled and reamed simultaneously. By the time TD is reached, circulation is required for long periods of time, to get the mud condition back to proper properties that will hold back the formation. Drilling and reaming short sections, then deactivating the tool and working the string to circulate all the cuttings before drilling ahead, can preserve mud properties and improve circulation and drilling time.
Full-bore access. The RFID tool preserves the full bore without any restrictions. As such, there is minimal pressure drop, due to zero restrictions. The full bore allows wireline access to any tools located below the reamer.
Control of multiple tools. The RFID tool allows multiple tools to be run in the same drillstring, because tags may now be programmed independently to control the tools downhole. For instance, two reamers could be run in the drillstring, Fig. 2. First, a tag could be pumped down the string to activate bottom Reamer No.1. The tool could be used for reaming until the drilling parameter indicates the cutters may be worn. A second tag would then be pumped to de-activate Reamer No. 1, followed by a third tag to activate Reamer No. 2. Drilling and reaming could continue without pulling the drillstring to change out the reamer. This feature could save hours on an extended reach well. At section TD, a fourth tag would be pumped down the drillstring to deactivate Reamer No. 2 and allow full flow of the mud for circulation and wellbore cleaning without the reamer adding additional cuttings to the mud system.
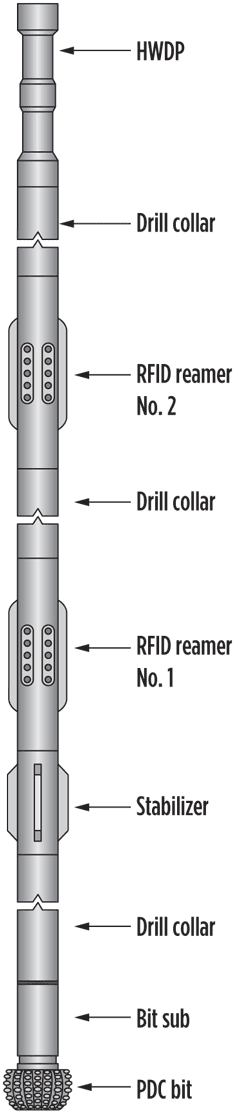 |
Fig. 2. Reamer BHA with two RFID reamers. |
|
DURABILITY TESTING
During development of the RFID controller, significant testing was done to validate its use in the drilling reamer. The tool had to be sufficiently heavy duty to withstand the rigors of drilling. Normal drilling activities create vibration and shock that can be detrimental. Battery longevity tests were conducted to evaluate the battery life at 20°C and 150°C for 96 hours, each. Multiple activation and deactivation tests were completed at various temperatures to test the drain on the battery and to evaluate potential downhole usage. Vibration testing was conducted on a vibe machine at levels up to 10 g’s, a level at which tool failure and/or tool destruction can happen.
The tool was function-tested periodically during the vibe test. Function testing and hydrostatic tests with oil and water to 20 cycles from 500 to 10,000 psi were also conducted. Many of the tests included multiple parameters. For instance, the tool was tested to 150°C while in the vibe machine for 24 hr. Flow loop testing consisted of flowing tags through the tool at rates from 5 to 20 bpm. Multiple activation/deactivation was conducted during the flow loop tests. These tests also included runs with only water and with drilling mud. Mud was circulated through the tool for 18 hr without any activation cycles. A successful activation/deactivation was accomplished after this flow test. Over 32 individual tests were completed on the RFID products prior to field testing.
TEST RIG EVALUATION
Pumping and reliability tests were conducted at the Weatherford lab in Houston, where a test rig was available. The test well is 1,000 ft deep with full rig capabilities. The tests included multiple activations and deactivations of the reamer. The tests were conducted by initially varying the number of tags pumped and the rates at which they were pumped through the tool. Figure 3 shows the results of the activation and deactivation of a pre-determined number of tags pumped. This test was conducted with and without nozzles in the reamer, which explains the variation in pressure when the tool was opened. When the nozzles in the tool were blanked, the pressure did not drop as it would if the nozzles are installed and available for flow. The nozzles were blanked at the beginning and end of the test, so that opening and closing could be visually verified. The test showed consistent activation when activation tags were pumped through the tool with a pressure reading of 825 to 850 psi. The test showed consistent deactivation when deactivation tags were pumped through the tool with a pressure reading of 435 to 450 psi. Each time a deactivation tag was pumped, a low pumping rate was used to move the tags through the controller. Tests were also conducted to determine the best mode for the tags to be pumped: bare tags, tags in plastic protector sleeves, or a dart type assembly (Fig. 4) to control how the tags flowed through the mud.
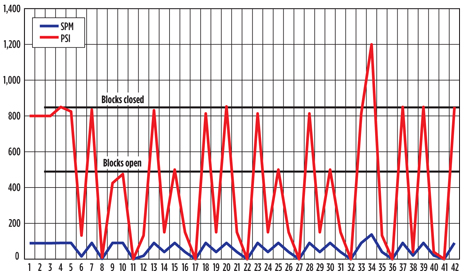 |
Fig. 3. Rig test data (pump strokes and pressure) shows multiple activations and deactivations of the RFID reamer. |
|
FIELD TESTING
Field testing was conducted on the Casey Edward well in North Dakota, drilled by Marathon Oil. Multiple activations and deactivations were conducted during the drilling of the well. At the surface, the RFID tool was activated and deactivated to demonstrate the system to the company man and rig crew; visual confirmation was available below the rotary table. The surface test also set a benchmark pressure differential between activated and deactivated for additional indications downhole. A 300-psi difference was recorded between the activated and deactivated mode of the reamer. At 300 ft into the well, the tool was de-activated. The section was drilled ahead a few feet to create a bench for a pull test. The reamer was activated by pumping tags, with activation confirmed by a pressure drop at the surface. A confirmation of tool activation was conducted by an overpull test at the bench. The well was drilled to TD where another deactivation/activation sequence was conducted. A pull test and pressure drop confirmed that the deactivation/activation were successful. At surface, a complete activation/deactivation sequence was conducted to visually see the tool function. Eight complete cycles (activation/deactivation) during the drilling process were conducted to validate the tool. Figure 5 shows a typical BHA used for the North Dakota field testing and Table 1 shows the data captured at the wellsite.
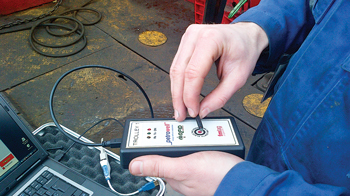 |
Fig. 4. RFID tag programmer used in the field. |
|
 |
Fig. 5. BHA used for RFID reamer field testing |
|
CONCLUSIONS
The RFID reamer has perform successfully during each phase of the development project. The addition of the new technology has allowed more freedom for the operator to drill the section and perform other normal functions previously impossible to do with standard, hole enlargement tools. RFID will play a significant role in the drilling tools upon further development. 
Table 1. Engineer’s report for the RFID reamer field test |
|
NOMENCLATURE |
RFID |
Radio frequency identification |
HEWD |
Hole enlargement while drilling |
HWDP |
Heavyweight drill pipe |
BPM |
Barrels per minute |
SSP |
Standpipe pressure |
SPM |
Strokes per minute |
POOH |
Pull out of hole |
ID |
Inside diameter |
LWD |
Logging while drilling |
TQ |
Torque |
|