LEIGH YAKEMCHUK, Penn West Exploration; TED TRYHUBA and KELLY WOOLSEY, Kudu Industries
The combined technologies have extended pump life by maintaining a safe fluid level in the well, while allowing increased production rates.
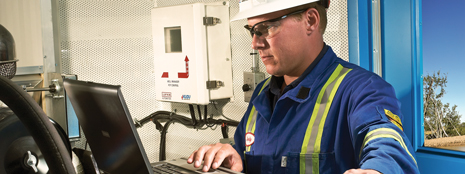 |
An operator logged onto a dedicated supervisory control and data acquisition (SCADA) system analyzes real-time production data to diagnose problems and implement pump adjustments remotely. |
|
A horizontal oil well producing from the Bakken zone in Saskatchewan’s Court heavy oil field had experienced extreme production difficulties primarily caused by sand and inflow issues. The well experienced four pump changes within six months in early 2008 resulting in an operational cost of $198,000. That summer, operator Penn West Exploration installed an innovative progressive-cavity pump (PCP) that it had designed in conjunction with oilfield equipment manufacturer Kudu Industries, as well as a pump-off controller. The well produced 124,390 bbl in the following six months without any workovers, and the pump ran for 14 months before it required replacement due to abrasion. This combination of technologies proved effective for both sand control and production optimization, as well as the prevention of pump-off and extension of pump run life.
GEOLOGY AND WELL HISTORY
The Bakken heavy oil pool at Court field is structurally and stratigraphically trapped in a fragment of a tidal ridge, completely eroded around the perimeter of, and to various degrees over, these sections. The erosional features are infilled with detrital material consisting of a mixture of sand, chert, silica fines and shale. Where it is not eroded, the Middle Bakken sand is underlain by the Lower Bakken shale and overlain by the Upper Bakken shale (both of which are organic, black and fissile); where eroded, the Middle Bakken is overlain by basal Mannville sediments.
Because the Court pool is partitioned by erosional features, the oil-water contact varies from about 490 ft (150 m) below sea level at the south end to about 460 ft (140 m) below sea level in the north. The gravity of the oil also varies from about 12°API in the southern half of the pool to 15–16°API in the northern half.
Reservoir quality ranges from very good to moderate, controlled primarily by the presence or absence of detrital clay material in the pore system. Other reservoir quality control factors are cements (primarily siderite) and, to a lesser extent, grain size. Grain density is variable and controlled by mineralogy, ranging 2,640–2,650 kg/m3 (about 165 lb/ft3) in clean samples, 2,750 kg/m3 in sideritic samples and 2,630 kg/m3 in argillaceous samples.
The horizontal Bakken well discussed in this article, well 91/02-03, was drilled by Renaissance Energy in November 1997, on the northeastern side of the 719-acre heavy oil pool at Court field. The well was drilled to a total depth of 4,300 ft (1,310 m) and a TVD of 2,841 ft (865.89 m). A 7-in. (177.9-mm) casing was installed with a 4½-in. (114-mm) slotted liner in the bottom 1,140 ft (348 m) of the well.
There are now a total of 22 wells in the production zone, of which nine are active. Among these, 19 are oil wells, one is a gas well and two are injection wells. Sample properties from some wells in this pool indicate that clean oil in the area is dark brown in color. Basic sediment and water total 10.8% of the production volume (about 10% water and 0.8% sediment).
Despite the large amount of producible oil reserves in the Bakken zone, it has been difficult to produce historically. Well 91/02-03, which later became the property of Penn West Exploration, is no exception. It experienced difficulties such as inconsistent inflow caused by high gas-oil ratio (GOR), sand issues and pump-off failures. Penn West has used waterflood in Court field as a form of secondary recovery to maintain reservoir pressure and sweep residual oil to producing wells.
The well came online in November 1997, producing 90 bpd of 12.8°API heavy oil; however, the oil rate had dropped to 10 bpd within four years. In April 2000, a water injection well (92/10-03-034-28W3) was brought online, and it arrested the decline of the Bakken oil producer within one year. The oil rate stabilized to a range of 20–25 bpd from 2001 to 2008, and water production remained fairly constant at 100–200 bpd, Fig. 1.
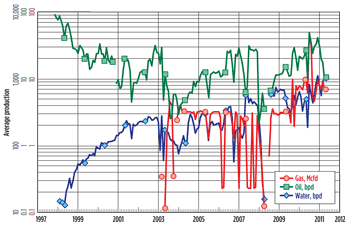 |
Fig. 1. Historical production from the 91/02-03 heavy oil well in Court field. |
|
In early 2008, production suddenly dropped to zero due to water breakthrough from the injection well, which sanded up the pump, resulting in rod wear and a zero-pressure reading in January and burning out of the stator in March. The use of higher-strength rods and PCPs of various geometries were attempted in order to restore production, but the results were not satisfactory. A total of three new pumps that were tried in a few months’ time each lasted between seven and 23 days.
TECHNOLOGY SELECTION
During the downtime in 2008, the operator turned to a technology that it had developed in conjunction with Kudu Industries, the Left-Helix pump, with the primary goal of keeping produced sand from building up in the sump and eventually blocking the inlet of the pump.
The relatively small pump is designed with a reverse geometry intended to produce fluid in a downward direction, and is run below a higher-powered, upward-producing pump that lifts those downward-directed fluids to surface. A pony rod between the two rotors allows them to turn simultaneously, Fig. 2. The left-helix rotor drifts the stator above it, and is landed at the bottom of the tubing string. The downward production of fluid continuously washes the cellar, or rathole, in high-solids wells, preventing the buildup of solids and subsequent premature failures of pumps due to sanding.
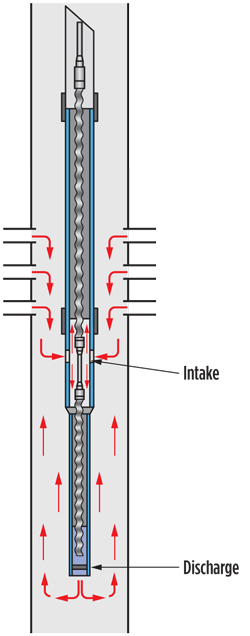 |
Fig. 2. Schematic of the downhole pumping unit consisting of a left-helix PCP below a higher-powered upward-producing PCP. |
|
Kudu’s PCP Well Manager pump-off controller was also installed at the well. Pump-off, in which fluid no longer enters the pump, is a common cause of premature pump failure. In PCPs, where the produced fluids lubricate the pump, the lack of fluid entry leads to extreme temperature increases that ultimately burn the elastomer in the pump. The rubber surface of the stator becomes hard, brittle and cracked. In severe circumstances, the stator contour is completely torn up, producing rubber at surface. Plugged pump intake, poor inflow or production rates exceeding inflow are typically to blame.
Prior to installation of the pump-off controller, operators were monitoring torque, using manual fluid-level monitoring equipment, and manually setting the pump speed in an effort to maintain substantial fluid above the pump and thereby protect it from pump-off. This was a very time-consuming process, involving shooting the fluid level, adjusting the pump speed, allowing the well to stabilize and then shooting the fluid level again. Additionally, this manual process reacted slowly to changes in inflow, and the production rate had to be kept artificially low to maintain a safe fluid level.
The pump-off controller combines wedge flowmeter technology and microprocessor control of electric and hydraulic motors to prevent pump-off by controlling the production rate, resulting in extended run life and increased cumulative production. The system sustains optimum fluid inflow by maintaining the lowest possible bottomhole pressure. The hydraulic control system makes pump speed changes using proportional-integral-derivative (PID) loop control on the proportional control valve without adding heat to the system. The automated technology is combined with a web-based system that feeds back real-time data to a dedicated supervisory control and data acquisition (SCADA) host, allowing technical experts to diagnose problems and operators to respond quickly to changing well conditions.
In wells with significant sand production, the pump-off controller’s sand blowout feature accurately detects torque and/or production issues in real time and responds immediately to slow the pump and build up a fluid level above it. After a predetermined buildup time, the pump speed is increased to a sand blowout speed, increasing the velocity of the fluid sufficiently to carry the sand with it to surface.
APPLICATION
On July 1, 2008, a 920-psi left-helix PCP with a 97-bpd displacement rate (at 500 rpm and zero head) was installed in the well as a pilot project, along with a 1,700-psi, 1,887-bpd standard PCP (placed above the left-helix pump) and a hydraulic pump-off controller with a wedge flowmeter. The bottom of the pump assembly was landed about 330 ft (100 m) above the top of the slotted liner. The assembly, from the bottom up, consisted of a slotted tag, the left-helix PCP, a slotted 7.6-ft (2.33-m) pup joint, the standard production PCP, and the 2⅞-in. (73-mm) production string.
The installation was fairly uneventful, and operation of the pump was smooth even at the initial stage. During the six-month period prior to installation, the well had experienced four workovers due to sand and inflow issues, at considerable cost to the operator, while producing a mere 17,050 bbl (about 23 bpd) of fluid. These workovers were the direct result of the pump being starved of fluid due to sanding. In the two months following installation, the well produced 124,410 bbl (about 2,000 bpd) of fluid and incurred no workover costs. The use of the pump-off controller allowed the well to pump more aggressively than had previously been the case, increasing the fluid production rate. The pump ran for 14 months before it needed to be replaced due to wear and tear from abrasion.
The well produced for 7,658 hours in 2009 (87% of the year), compared with 4,806 hours in 2008 (55%)—a 72% reduction in downtime. In terms of oil produced, the total 2009 volume was 5,522 bbl, nearly three times the 1,975 bbl produced in 2008. The well is currently producing heavy oil with a 96% watercut, 2–5% sand and a GOR of 2.8 Mcf/bbl. 
THE AUTHORS
|

|
LEIGH YAKEMCHUK is a Production Engineering Technologist with Penn West Exploration, responsible for managing oil fields in the Hoosier area of west-central Saskatchewan, Canada. The Hoosier area’s primary production is Bakken heavy oil. Mr. Yakemchuk earned a degree in petroleum engineering technology from Southern Alberta Institute of Technology, and worked in the field for Trican Well Service as a data van operator before joining Penn West.
|

|
TED TRYHUBA began work with Kudu Industries in 1992 as a Field Technician based in Provost, Alberta. He subsequently worked as a Store Manager and Area Manager before advancing to his current position as New Business Development Manager for Canada.
|

|
KELLY WOOLSEY is the Automation Business Manager for Kudu Industries, having joined the company in 2008. Trained in the electrical field, in 1988 he partnered in a company focused on artificial lift automation and optimization. In 1994, he joined Delta-X Corp. as the Canadian Operations Manager, and began developing the PCP controller. When Delta-X was sold to Lufkin Industries in 2000, he followed the product line and managed the automation services group for Canadian operations.
|
|