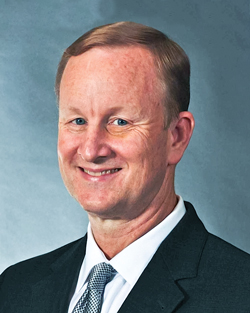
DR. D. NATHAN MEEHAN, Senior Executive Advisor, Baker Hughes
The Baker Hughes rig count is widely seen as a business barometer for the drilling industry and its suppliers. When rigs are active, they consume the products and services produced by the oil service industry. The rig count is also a leading indicator of demand for products used in well completions, production and processing of oil and natural gas. For these reasons, it is published by major newspapers and trade publications (including World Oil); frequently referred to by journalists, economists, security analysts and government officials; and included in many industry statistical reports. Because it has been compiled consistently for more than 60 years, the Baker Hughes rig count is also useful in historical analysis of the industry.
This rotary rig count has been issued as a service to the petroleum industry since 1944, when Hughes Tool Company began weekly counts of US and Canadian drilling activity. The monthly international rig count was initiated in 1975. The rig counts are available on the Baker Hughes website at investor.shareholder.com/bhi/rig_counts/rc_index.cfm and can be accessed by an app for Apple iPads and iPhones. The North American rig count is released weekly at noon, Central time, on the last day of the workweek. The international rig count is released on the fifth working day of each month. The website and app allow users to visualize drilling activity geographically, by state, county, basin, water depth, oil or gas and many other categories. Perhaps most importantly, they allow users to visualize horizontal vs. vertical drilling.
In the 1980s, the bulk of onshore drilling in North America consisted of vertical wells targeting natural gas. Horizontal drilling commenced in earnest in the early 1990s, and by March 2009 there were more rigs drilling horizontal wells in North America than there were drilling vertical wells. Service intensity (the total expenditure for the goods and services typically provided on a given well) is higher for horizontal wells than vertical wells because of the demand for both geometric and geological steering, the use of measurement while drilling (MWD) and logging while drilling (LWD), the need for more sophisticated liners and other completion gear, and the requirement of greater reservoir characterization efforts.
The use of hydraulically fractured horizontal wells to tap shale reservoirs further increases the demand for oilfield services because of the need for geomechanical services; multistage fracturing; microseismic monitoring; special core analysis in the early wells drilled during delineation of a play; closer lateral spacing (due to smaller drainage areas away from stimulated zones in ultra-low permeabilities); more sophisticated bits enabling higher penetration rates and shorter radii; and high levels of responsiveness in geosteering and reservoir analysis.
Historically, vertical tight gas wells in North America, such as in the Cotton Valley of East Texas, might have been treated by three or four hydraulic fracturing stages each. The vertical well would be cased and cemented, and frac stages would progress upward from the bottom of the well with a variety of relatively straightforward and low-cost methods to isolate the stages. Although differences of opinions exist as to quantitative values, generally created, propped and effective fracture lengths and geometries are well understood and have been used routinely to model the efficacy of reservoir drainage. This has led to increased well spacing and lower well costs. Fluid chemistry has been simplified by the move to water fracs, and the overall level of reservoir characterization measurements has decreased. Geophysics as a production tool is infrequent.
In contrast, a typical horizontal well in a liquids-rich shale play has anywhere from a dozen to more than 40 frac stages. Reservoir characterization and steering efforts involving geophysics are common, and logging and coring efforts seek to quantify not only conventional petrophysical measures but also total organic content, vitrinite reflectance, gas content, detailed mineral composition of up to 20 separate minerals, geomechanical indicators and more. For effective geomechanical models, wellbore imaging tools are essential. The effective integration of these technologies has enabled operators to explain the high variations in performance between nearby wells and develop strategies to optimize future development. A full understanding of critically stressed fractures and characterization of naturally fractured shales require fully integrated characterization and modeling efforts.
Horizontal multistage completions typically use either cemented liners and the plug-and-perf method or openhole packer systems. The plug-and-perf approach uses pump-down perforation and plugs to isolate each stage. Composite plug materials must be milled out after the frac stages are complete. Openhole packer systems run a series of packers with pump-down balls activating the appropriate sleeves for fracture initiation and zonal isolation. Some methods require flowing back the balls and milling up any balls that are not recovered. As the number of stages increases, the likelihood of requiring such milling increases for a variety of reasons. These include the fact that the stimulated zones near the heel of the well may clean up quickly, leaving little pressure drop available for the earlier, more distant stages. Advanced solutions using nanotechnology have enabled operators to replace elastomer balls with balls that are as light as aluminum and as strong as steel, and can be machined with high precision. Nanomaterials function as a high-tech glue holding powdered metal material together. These balls are able to dissolve in a kinetic reaction with the frac fluids over a pre-engineered timeframe.
Multistage frac treatments require a substantial volume of relatively fresh water and many surface pumping units. For these and other reasons, operators and service companies must collaborate to minimize environmental impacts. Advanced fluid chemistry and optimal designs allow the use of more saline waters and smaller volumes. Multiple laterals requiring advanced liners and longer horizontal laterals with more stages minimize the number of surface wellheads and total footprint.
Liquids-rich shales warrant a disproportionately higher level of optimization than do dry gas shales, for both technical and economic reasons. Flow through the extremely small pores and microfractures in shale reservoirs is much easier for the more mobile gas molecules, allowing drainage at substantially greater distances away from a given fracture than for an oil or liquids-rich gas. Thus, liquids-rich shales require closer spacing of wells and of frac stages. This level of optimization means more micro- seismic monitoring should be conducted for liquids-rich shales along with more reservoir modeling and analysis. A pure statistical approach will not optimize reservoir development.
The relative prices of oil and gas in North America for many years reflected a barrel of oil being worth 6–10 Mcf of gas. By early 2009, that had increased to 20 Mcf, and the desirability of drilling for oil vs. gas was higher than ever. The greater service intensity is economically justified given high liquids prices.
Other technical reasons for higher service intensity in unconventional oil reservoirs include the greater added value to be gained by proper well placement. This warrants additional pre-drilling characterization and greater focus on LWD-based geosteering. This improved placement can not only boost hydrocarbon recovery, but also improve drilling performance and the efficacy of created fractures. 
THE AUTHOR
|
DR. D. NATHAN MEEHAN is Senior Executive Advisor for Baker Hughes, where he supports executive management in the areas of reservoir technology, emerging technologies and E&P business trends. He was previously the founder of CMG Petroleum Consulting, Ltd., Vice President of Engineering for Occidental Petroleum, and General Manager of Exploration and Production for Union Pacific Resources. He holds a BS degree in physics from the Georgia Institute of Technology, an MS degree in petroleum engineering from the University of Oklahoma, and a PhD in petroleum engineering from Stanford University. His blog on reservoir and production engineering topics is blogs.bakerhughes.com/reservoir. Dr. Meehan is on leave from his position at Baker Hughes until February 2013, while he and his wife perform humanitarian service as Asia area welfare coordinators. |
|