Automation & Control
Increasing upstream profit through compressor optimization
An Internet-based compressor optimization and fleet management program has resulted in meaningful production and profit gains for several producers
Cavan C. Carlton and Andrew R. Miles, Detechtion Technologies, Houston
A proprietary, noninvasive compressor analysis and fleet-management program called Enalysis is being used by producers to improve performance and reliability of their reciprocating and screw compressors. More than 2,000 compressors are now on the system, from Western Canada to the Lower 48 and the North Sea. The nature and capabilities of this program with specific examples of how using the program has generated substantial compressor efficiency and profitability enhancements for producers is presented.
SYSTEM OVERVIEW AND BACKGROUND
Enalysis is a diagnostic tool that combines individual compressor optimization and total compressor fleet management into one program. For individual compressor optimization, the program relies on proprietary algorithms to thoroughly analyze the operation of both reciprocating and screw compressors based on operating parameters. It then recommends specific actions for improving compressor performance, minimizing cost and avoiding compressor damage.
The program also provides producers with advanced compressor fleet management tools that have been designed to meet the reporting and information requirements of gas producers. Fleet management capabilities include distinguishing between different employee responsibilities and compressor subsets within an organization. This allows all personnel, at any level of responsibility or in any operating division, to completely understand the “big picture” while focusing on their specific areas of compressor concern.
In addition, the program provides for fast retrieval and aggregation of a large amount of data that is generated by management of a compressor fleet. Historical charts and graphs are produced for fast and easy trend analysis of operating conditions and performance levels of each compressor, each field, each district, or an entire fleet. Using the program, several North American gas producers have realized operational benefits, including:
- Increased gas throughput
- Identification of unseen gas production potential
- Enhanced and effective preventive maintenance
- Avoidance of catastrophic compressor failure
- Decreased compressor downtime, operating and maintenance costs.
The proprietary compressor algorithms that drive the program were developed by Detechtion’s founder. Over his 30-plus-year career in the gas industry, Alan Taylor found that compressor analysis tools commonly used in the industry were often overly simplistic and did not accurately reflect real-world field operating conditions. Taylor undertook a comprehensive effort to modify the standard compressor algorithms, conducting thousands of field tests on a broad spectrum of compressor sizes and types. The algorithms that Taylor developed are an interactive network of known and accepted physics equations that have been modified to reflect real-world compressor operations.
Instead of providing theoretical values for compressor design and operation, the program provides a detailed look into how a compressor is actually operating in the field. After nearly 15 years of design and field testing, the program made its commercial debut in the Western Canadian Sedimentary basin in 1998.
CLIENT RESPONSES
Canadian Natural Resources Ltd. (CNRL) was one of the early users of the program. CNRL has realized significant operational and production gains, boosting its compressor utilization to over 96% (measured in terms of both cylinder capacity and horsepower utilization). Before introduction of the program, CNRL estimated fleet efficiency at 85%. This 11% efficiency gain, coupled with reduced failure costs, yielded an annual profit gain to the company measured in the tens of millions of dollars.
Benefits of the program are obvious to Senior Management and field employees. “We saw the return immediately. With this program, I am confident my operations are running smoothly and I’m seeing that value hit the bottom line. It’s the first report I go through,” said Tim McKay, Senior Vice President, North American Operations for CNRL. Upon completing their recent acquisition of Rio Alto Exploration, one of the first steps CNRL took was to place Rio Alto’s compressor fleet on the program, optimizing that fleet.
Casey McWhan, production foreman at CNRL, has operational responsibility for several dozen of his company’s compressors. McWhan found the program to be highly reliable, stating, “We’ve put it to the test. Sometimes I’ve questioned occasional readings that come out, such as some of our blow-bys. But, when we follow the directions and end up pulling a compressor – sure enough, we find a bad valve or we have bad packing just as predicted. This tool will pick it up before somebody with 20 years’ experience picks it up.”
EOG Resources realized substantial compressor performance improvements using the program. EOG’s Canadian division began using the program in November 2002, and the company recently started using it on its Lower 48 compression as well. Using the program, EOG Canada’s compressor performance (measured in terms of cylinder capacity utilization) increased from 88.2% to 97.6% between November 2002 and March 2003, Fig 1.
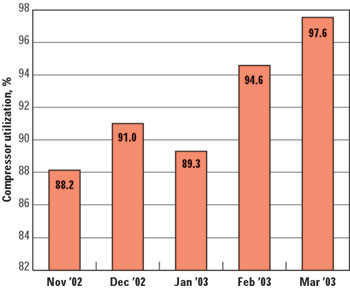 |
Fig. 1. EOG Resources – Canadian division. Compressor fleet performance improvement.
|
|
HOW TO USE IT
The program is easy to use. After an initial one-time collection of manufacturers’ design data and compressor site-specific conditions is entered into a database, diagnostic reports can be generated within seconds by entering key operating parameters into the program. These parameters include compressor suction, discharge pressures and temperatures, pocket settings, speed and running time information. Once this information is entered (via phone, fax, Internet, or SCADA), a diagnostic report is immediately generated, which provides a complete review of the compressor’s operating conditions and highlights specific discrepancies in performance. Each report also includes recommendations for performance improvement.
Individual compressor optimization is not the only function of the program. It also provides for total compressor fleet management, helping all operations personnel, regardless of level of responsibility, to quickly identify the compressors within their sphere of influence that require the most attention. By allowing for the aggregation of compressor data based on region as well as performance, the program makes it easy for any individual, from compressor operator to senior operations manager, to quickly identify and focus on problems within his area of responsibility.
PERFORMANCE FLAGS/OPERATIONAL RECOMMENDATIONS
The compressor optimization and diagnostic reports contain detailed Performance Flags and Operational Recommendations, Fig. 2. The algorithm is predicated on the belief that virtually all compressor operational inefficiencies and maintenance problems can be detected by looking at eight specific operating categories. Every report includes a section that lists these categories and indicates problems that exist within each one (see sidebar).
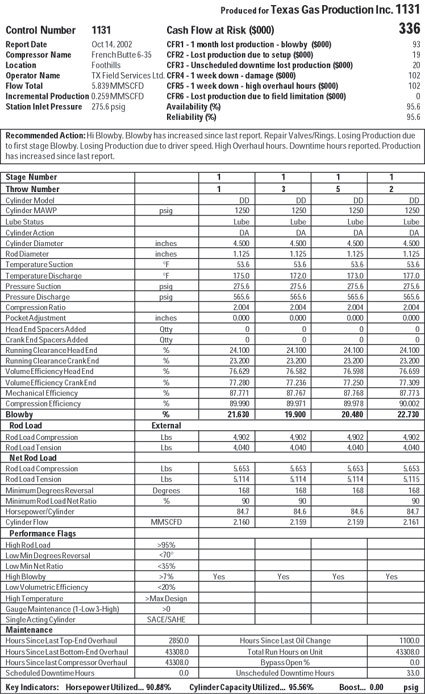 |
|
In addition to highlighting operational discrepancies, the program also provides specific recommendations for improving compressor operation based on its calculations and Performance Flags. Each report contains a “Recommended Action” section that lists specific actions operators can take to see immediate improvement in compressor performance. For example, the Recommended Action section may prompt the operator to increase engine speed, to check compressor valves and/or rings in a particular cylinder, to add/remove spacers, or to adjust variable pocket settings. There are dozens of possible recommended actions that might be suggested, each of which reflects the results of the program’s assessment of compressor performance. Users often comment on how helpful these Operational Recommendations are, since they provide them with clear and specific guidance on how to fix a problem rather than simply providing them with a large amount of raw data.
|
Operating Categories/ Parameters
|
|
|
High Rod Load – Rod loads greater than 95% are flagged as a potential cause for future compressor failure.
Low Minimum Degrees of Reversal – By calculating the percentage of each 360° rotation that the crosshead pin absorbs force upon its front portion, the program can detect possible crosshead pin failure. If the crosshead pin absorbs force upon its front portion for more than 290° per piston revolution, this performance flag is highlighted as a potential cause for compressor failure.
Low Minimum Net Ratio – Rod load net ratios less than 35% are flagged as a potential cause for compressor failure.
High Blow-by – Blow-by, due to faulty valves or piston rings, is the leading operational inefficiency detected by the program. Every unit of gas that must be recompressed is lost revenue. The program flags blow-bys of more than 7% as operationally inefficient, and blow-bys of more than 15% as a potential cause for compressor failure.
Low Volumetric Efficiency – Volumetric efficiencies of less than 20% are flagged as operationally inefficient and could result in suction valve damage.
High Temperature – The program flags high operating temperatures, based on manufacturers’ designs, as a potential cause for compressor failure.
Gauge Maintenance – The proper execution of the optimization program depends on accurate data inputs. The program flags potentially incorrect data inputs in its Gauge Maintenance category, indicating that data inputs and/ or gauges should be checked for accuracy.
Single-Acting Cylinder – Compressors with designed double-acting cylinders can exhibit the characteristics of single-acting cylinders. The program flags this scenario if it exists.
|
|
|
CASH FLOW AT RISK
The program also quantifies financial risk to the producer related to each compressor’s operational status and condition. Each report contains a “Cash Flow at Risk” (CFR) section, which is divided into six separate categories (see sidebar).
By including these six CFR categories in every report, the program provides its customers the ability to quickly determine which compressors require the most operational and/or maintenance attention. This has proven especially useful for producers managing a large fleet of compressors or for producers who have third-party compressor service providers and are seeking a clear way to gauge the severity of compressor problems.
The economic interests of third-party compression providers and operators are sometimes at odds. The program enables the operator to assure his economic best interest is being met in an efficient, cost-effective manner. With gas prices projected to stay above $4.00/Mcf for the foreseeable future, the payout via lost production or wasted fuel is rapid and can be justified on nearly any well where compression is warranted. Gas producers are currently using the program on over a hundred different makes and models of compressors, ranging from leased 40 hp slow-speed wellhead units to company-owned 4,000+ hp high-speed gathering units.
In summary, by improving compressor performance and providing the tools to better manage a compressor fleet, the program efficiently and reliably increases upstream profit. 
|
Cash Flow at Risk Categories
|
|
|
Blow-by – This category calculates how much revenue is being lost due to blow-by on the first stage cylinder.
Incorrect Set-up – This category calculates how much revenue is being lost due to incorrect compressor set-up (i.e., incorrect speed, pocket settings, etc.).
Unscheduled Downtime – As the operator collects data for executing a report, he must input any unscheduled downtime that the compressor experienced since the last report. This unscheduled downtime is then converted to a lost revenue figure.
Damage – This category determines how much revenue would be lost if the compressor experienced a catastrophic failure. The trigger for this category is high rod load, low minimum degrees of rod reversal, low minimum rod load net ratio or excessively high blow-by.
High Overhaul Hours – As the operator collects data for reports, he must input the number of hours the compressor has been run since last being shut down for maintenance. If the elapsed time exceeds the company or manufacturer’s recommended maintenance schedule, this will determine the revenue at risk should the compressor fail and be down for one week.
Lost Production Due to Field Limitation – This category indicates when the amount of compression for a particular application is larger than necessary.
|
|
|
THE AUTHORS
|
 |
Cavan C. Carlton earned a BS in civil engineering from The University of Texas at Austin, a Masters in environmental engineering and an MBA, both from Rice University in Houston. He joined Detechtion Technologies in June 2002 after spending seven years in various engineering and business development roles in the gas gathering and transmission industries. He works at the company’s Lynchburg, Virginia office.
|
 |
Andrew R. Miles earned a BE in marine/mechanical engineering from The State University of New York at Maritime College, an MBA from Rice University in Houston, and is a licensed professional engineer in Texas. He joined Detechtion Technologies in February 2002 after spending three years in various engineering and business development roles in the gas marketing and compression industries and nine years in applied engineering design and operations roles. He works at the company’s Houston office.
|
|
|
|