Real time field operations solution accelerates oil & gas production accounting
As a sector driven by innovation, the oil and gas industry is no stranger to new products and technologies driving significant change in the way that oil and gas teams do business. Despite digital oilfield transformation, advances have focused on drilling and completions. While progress in this domain has been critical to improving how companies develop their assets, innovation in the energy back office, in general, and production accounting, in particular, has lagged other departments.
The persistence of manual processes in production allocation and the subjectivity inherent in field operations data all too often lead to data delays and decisions based on incomplete or incorrect information. As a result, production accounting and critical financial reporting can take days or weeks, as field staff, production engineers, and production accountants work to ensure accuracy.
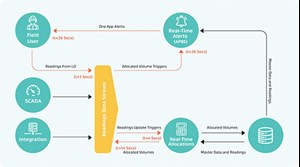
In trying to address this manual data management problem, solutions also tend to be manual, with production accountants quite literally tracking down lease operators to take or retake readings from specific wells. Recognizing the complex field data management challenges that lease operators and the back office face every day and seeking to enable a step-change in production accounting and the allocation process itself, Seven Lakes Technologies (a W Energy Software company) introduced a new technology called JOYN, a cloud native field operations solution purpose-built for field data gathering that is capable of driving hundreds of oilfield workflows, from lease assessments and allocations to HSE and regulatory.
JOYN TECHNOLOGY
The JOYN field operations solution provides operators with a robust production allocation platform for automating daily allocations, spotting data quality problems as they occur using intelligent algorithms, and seamlessly integrating the field and back office with Seven Lakes Technologies’ mobile OneApp offering, Fig. 1. The goal of using the platform is to enable relevant staff at operating companies to quickly troubleshoot issues and easily maintain and manage allocation networks, thereby shaving hours off what was previously a tedious manual process.
The platform’s allocation engine generates volumes much more rapidly from data that are available in near-real time, as soon as enough data have been gathered. These allocated volumes can then be made readily available to operations teams, enabling enhanced “pump by exception” outcomes that are delivered back to the lease operator on its mobile device via application synchronization.
The JOYN platform, by design, can be integrated with any system to pull master data and allocation networks directly into the platform, eliminating manual entries. Allocations are rapidly calculated as data is available, completely eliminating the need to manually chase down missing data. Calculations are performed in the cloud enabling even the most complex allocations to be run in minutes vs. hours with an on-premise server, providing greater scalability, reliability, and data visibility for all stakeholders.
Troubleshooting, which could previously take hours or days, depending on the limitations of disparate technologies and the number of systems needed to translate data into a useable format, now takes minutes using the JOYN allocations platform. At a glance, users can visualize production volumes for any product and the disposition on the allocation network at every node.
The JOYN platform automatically creates formulas for complex allocation scenarios, while analytics capabilities provide users with a personalized dashboard showing data that are most relevant to them.
Leveraging JOYN’s modern mobile app, field staff can validate information on their cellular phones, eliminating the need to hunt down and verify missing or bad data.
With a continuous and validated stream of field data, JOYN creates new opportunities for governance and data consumption. The technology provides self-service access to reliable production data with granular security control over what each user can see. Production analysts can easily edit networks and create new ones as necessary, while users with limited needs can be given restricted, read-only access.
CASE STUDIES
An operator focused on the western portion of the Eagle Ford shale in South Texas wanted to improve the effectiveness of gathering field operations data, in turn allowing the producer to improve operational efficiency. An area that was identified as needing to be optimized was their allocation processes and reporting for production data. To achieve their goals, they evaluated several potential solutions before determining that the JOYN platform was the option that best suited their operational and financial objectives.
The operator migrated more than 1,800 of the 2,300 wells in one of their assets to the JOYN platform, setting the organization up to better manage the critical field data that drive daily allocation and production reporting processes.
At the onset of the program, the operator began a pilot program using the JOYN platform. A challenge that the company had previously faced was consolidating its data-gathering efforts for field operations, leading to time-consuming manual tabulation and overall efficiency in the process. As the operator’s two major assets were acquisitions with their own unique setups from a measurement and data-gathering perspective, they used two completely different and unrelated data systems. These disconnected systems prevented timely data consumption by stakeholders across the value chain, from accounting to management. The company needed to consolidate field and volumetric data into one system that could provide on-demand access to allocations and production reporting with the scalability to handle the complexity and volume of the measurement data streamed from source systems.
During the pilot, the operator migrated more than 400 oil, gas, and water networks into the JOYN platform across more than 5,000 automated meters, citing performance of the allocation engine and speed and ease of verifying results as metrics to be assessed. After the assets had been migrated successfully, the company found that the new platform allowed them to more quickly and accurately run allocation data and view the results and analytics, typically within one hour.
This outcome, enabled by the near-real-time calculation capabilities of the platform, was previously impossible in such a short timeframe, giving the company the advantage of identifying issues faster and providing timely allocations to field personnel and engineers. Furthermore, because of the analytics capabilities of the JOYN platform, the operator was able to review the data, send reports, create custom dashboards, and communicate all relevant information to stakeholders on the project.
The operator’s legacy system for monthly allocations takes approximately 6 to 7 hr to run the allocations. This number does not include the additional time that it takes to then put those allocations back into a viewable format to review them, with background scripting and other complicated processes extending the time further.
Using JOYN, the company was able to house everything in one place, with a month’s worth of allocations run in approximately 30 min., Fig. 2. With an estimate of a maximum of 30 more minutes for the analytics to be run, the company found that within 1 hr, they had useable grids, dashboards, and reports for reviewing the data and allocations automatically, no longer held hostage by batch production data loaded manually into the legacy production accounting application at the end of each shift.
In translating this success to business objectives, the operator is driving accountability to new levels with the JOYN platform. Having undergone rapid organizational transformation over a two-year period, the operator wanted to improve the integrity and accessibility of data from the wellhead to the corporate office, aligning with operating goals and values. A cross-functional effort from field personnel to office staff, it was critical that all be held accountable for their roles in the process.
Lease operators were of particular importance, as they followed daily well routes, performed inspections, conducted well tests, and safely ensured that production was stable and continuing to improve. Supporting the boots on the ground and enabling their success meant providing the right tools and data to make the right decisions and have full visibility into their production.
Gaining clear visibility into the performance of each well was the key to production optimization, backed by a reliable field operations data management system to drive collaboration and data integrity. The result of implementing the JOYN platform set off a chain reaction, with engineers able to optimize well performance daily and report volumes on time, and transparently, to operations downstream of the field, and production accountants able to refocus on critical tasks.
As it continues to use the JOYN platform, the operator has set expectations for future benefits. These include further streamlining of data gathering, analysis, and reporting to eliminate more inefficiencies in existing processes; increasing production via improved field situational awareness and overall production data; and achieving new levels of operational excellence through a commitment to digital innovation.
California case study. A leading independent oil producer in California was exploring innovative energy production methods to meet the state’s growing energy needs. Like many oil and gas companies, the operator relied on manual production accounting workflows that saddled engineering and accounting staff with time-consuming data management. The operator took a grassroots approach to building databases and bringing data together more efficiently.
While partially successful, the production team realized the limitations of homegrown solutions to scale as the number of assets under management grew. The operator set out to find a commercial data management solution that could accelerate the flow of field operations data from the front-line pumpers and lease operators into back office business systems. Criteria for success included the ability to automate field data capture and processing, eliminating the need for field staff to manually input data.
With so much data being presented in bits and pieces, it would be critical for the solution to bring that information together into something coherent. The operator needed a platform that would allow them to look behind the data to know what it is actually doing and quickly unravel complicated information to understand errors or inaccuracies. Missing or inaccurate data were largely the result of human error, data management roles that were not clearly defined, and the inherently fractured nature of manually entered information. Understanding these issues led to the operator concluding at the end of its evaluation that the JOYN production allocation platform would be a fit for its needs.
Once implemented, the operator found that the platform’s data management structures allowed the company to capture field data in a consistent, scalable way, building a foundation for more effective production allocation. In addition to delivering information to relevant users in a timely fashion, the company was able to join the myriad IT structures—servers, storage, infrastructure, and Wi-Fi in the field—necessary to bring data from the field to the office. The JOYN platform, then, was able to leverage its foundational abilities to support an entirely different functional discipline at the company.
Another two aspects of the JOYN platform that the operator found beneficial were the speed of calculation, which was higher than comparable platforms and magnitudes faster than data input manually, and cybersecurity, with the onus of data stewardship taken away from the company and put into the hands of Seven Lakes Technologies.
On-demand data from the JOYN platform allowed the operator to provide necessary parties with accurate information, required to make proper decisions with production allocation, in a timeframe that was dramatically faster than anything the company had previously achieved with other solutions. The time from when the field personnel input the allocation information to it being processed for analytics was reduced to approximately 25 min. or less using the JOYN platform, a task that previously took two days—and, in worst-case scenarios, up to a week, Fig. 3. Additionally, obstacles with issues like inventories were almost eliminated, and backend components were consolidated into user-friendly dashboards. The operator is also leveraging the JOYN platform to capture and retain corporate knowledge, enabling new employees to quickly get up to speed and ensure critical allocation processes.
Additionally, accessibility for all parties empowers everyone involved in the allocation process with visibility into the results of the work, putting information on trending production data or other important performance metrics in the hands of stakeholders throughout the process and across sites.
With sustained global demand for hydrocarbons and new complexities from the energy transition , the industry will be increasingly called to adopt new solutions as it evolves to meet society’s needs. In this journey, much work has already been done to improve drilling performance and recoverable reserves from oil and gas wells, accelerated by the advent of digital technology throughout the value chain.
DIGITAL SOULUTION
Digital oilfield transformation is bringing new efficiencies to field operations and the energy back office and enabling operators to automate field data capture, allocation and production accounting processes while seamlessly bringing disparate data sources together into a single platform for rapid consumption. Through its JOYN production allocation platform, Seven Lakes Technologies has introduced one solution to a set of problems that empowers today’s workforce with the modern technology needed to navigate daily allocation complexity, reduce operating costs, and optimize production.
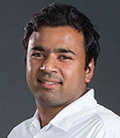
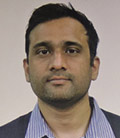
- Digital transformation/Late-life optimization: Harnessing data-driven strategies for late-life optimization (March 2024)
- The reserves replacement dilemma: Can intelligent digital technologies fill the supply gap? (March 2024)
- Digital tool kit enhances real-time decision-making to improve drilling efficiency and performance (February 2024)
- Digital transformation: Digital twins help to make the invisible, visible in Indonesia’s energy industry (January 2024)
- Digital transformation: A breakthrough year for digitalization in the offshore sector (January 2024)
- Quantum computing and subsurface prediction (January 2024)