Next level optimization: Zero NPT
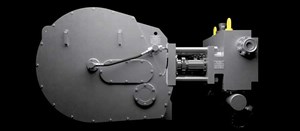
While battered oil prices had already placed extreme pressure on operators and oilfield service providers before Covid-19, the pandemic has created seismic shifts. The new climate that we find ourselves in has intensified the focus on critical keys to success in the oil patch; minimizing NPT and operating costs. Even as so much has changed in our world, these two success indicators remain the same.
Lowering operating costs and reducing NPT is an ongoing challenge for oilfield service companies. There is always interest in moving the needle from good to better as technology evolves. It is the commitment to continuous improvement that gives companies a competitive edge.
As pumping hours have increased, regularly clocking in 18–22 hr/day, the complexities and costs to perform a job also have increased. With frac fleets today consisting of as many as 20 pumps, that is also 20 sets of expendables to maintain and replace. Service companies cannot afford to lose pumping time to unplanned NPT, and even planned maintenance can prove to be an obstacle, due to the demands placed on these companies.
Reliability is a necessary focal point when trying to reduce NPT and costs, as long pumping hours and brutal operating conditions take a toll. These extremes can cause problems with the pumps operating in the field, such as internal welds that crack under the stress, worn gear sets, and fluid ends that require such significant maintenance that NPT is unavoidable.
Haynesville case study. The extreme operating conditions that service companies place their equipment in are compounded by the nuances of each basin. This becomes the true test of a pump’s reliability and can be a crucial factor in a job’s bottom line. We witnessed this recently, as the SPM® EXL frac pump was deployed in the Haynesville shale over the last few months. An oilfield service company was running 20 pumps and had been experiencing above-average NPT. This was cutting into the company’s pumping hours and, consequently, profits. The operating conditions were brutal, with pressures over 13,000 psi and some of the worst sand quality we have seen.
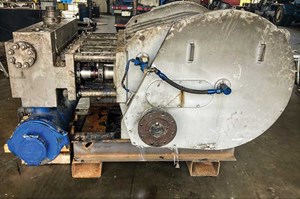
The company installed an SPM® EXL on-site to run with the rest of its fleet. Even with the Haynesville’s harsh environment, the service company experienced zero NPT over the test period with the EXL, while consistently pumping over 13,000 psi. The EXL logged over 2,000 hr without NPT and was the only pump on location to not get pulled during the few months it was there. Pumps are normally pulled due to reliability issues commonly experienced when pumping in that environment. Extrapolating the NPT decrease experienced, it is conservatively estimated that a fleet of EXL pumps could save the company one hour of NPT per pumping day, for a cost-savings of $1 million+.
With zero NPT, in the Haynesville especially, the service company was able to truly maximize its pumping hours. More pumping hours equates to more profit, so maxing out uptime—especially in the current climate—helps service companies thrive.
Minimal maintenance under extreme conditions is a major advantage. The service company was able to reduce planned maintenance, due to the pump’s rigid construction, fewer internal welds and potential leak point paths. The chance for a packing blowout was neutralized, due to the use of the SPM® Everbore™ hardened steel packing bore, which eliminates the threat of washboarding and the added downtime associated with re-sleeving, allowing the company to continue pumping at max rod load.
Another cost-saving advantage that the service company experienced was the elimination of the need for separate fleets for high-pressure and low-pressure environments, due to the EXL frac pump’s flexibility and rod load capabilities. All of that reduces a company’s capex significantly.
Even in challenging times, reliability should not be overlooked when focusing on decreasing NPT and operating costs. Rugged durability and equipment that’s engineered specifically to minimize routine maintenance can make a significant difference in reducing downtime and costs. When seeking to carve out a competitive advantage in today’s climate, service companies should look for equipment that can provide them the durability of running at maximum rod load in any basin and the ability to reduce maintenance to maximize pumping time.
- Advancing offshore decarbonization through electrification of FPSOs (March 2024)
- Digital transformation/Late-life optimization: Harnessing data-driven strategies for late-life optimization (March 2024)
- The reserves replacement dilemma: Can intelligent digital technologies fill the supply gap? (March 2024)
- What's new in production (February 2024)
- Digital tool kit enhances real-time decision-making to improve drilling efficiency and performance (February 2024)
- U.S. operators reduce activity as crude prices plunge (February 2024)