Transforming during the downturn: How energy companies can thrive after Covid-19
From upstream to downstream, oil and gas markets are facing a triple threat of upheaval: 1) declining demand due to Covid-19; 2) global oil and gas oversupply; 3) and, for the first time, uncertainty around simply accessing, maintaining and staffing facilities to ensure business continuity. Energy companies, as a result, are capital-constrained, with many selling assets and cutting costs in response.
In Texas, alone—the largest oil-producing state in the U.S.—land rigs have decreased by more than 75%, compared to this time last year. Amid these historic challenges, companies must adapt in ways that support not only their businesses’ viability, but also the increasing importance of economic, social, and environmental sustainability.
Regardless of which area is the largest threat to a company’s operations, lean times provide an opportunity to analyze business operations and make smart, strategic investments in new technologies and processes. These items drive efficiencies to help meet revenue targets and set the stage for long-term success. In fact, digital transformation in the oil and gas industry could unlock approximately $1.6 trillion of value, according to the World Economic Forum. Many organizations don’t have to look far to find new efficiencies and quickly address the issues facing their business, as an effective digital transformation strategy makes business and operational sense.
It’s possible, now more than ever, for organizations to achieve cost-effective operations that respond with agility to market fluctuations and position the company to not only come out stronger from the downturn, but to also set the stage for the next decade in energy. The path forward to success through adversity looks different for every organization, but there are four strategic levers that energy organizations can pull in their operations to help them weather the lean times and prepare for the rebound.
Connected and collaborative workforce. The industry was facing the challenges of a shrinking workforce long before the Covid-19 pandemic. Energy companies find it increasingly difficult to hire an adequate number of workers for the difficult and demanding tasks that oil and gas require—a growing obstacle, as more skilled workers with the expertise to work these jobs retire every year.
While remote capabilities have always been a priority to keep workers safe, the social distancing required, due to today’s pandemic, combined with fewer skilled workers on the ground, has made them a necessity. There are several areas where companies can invest to help bridge the workforce gap and keep facilities operational from afar. Wireless sensors gather necessary data and keep workers from dangerous areas, while wearable devices help with social distancing and contact tracing.
Technologies are also helping companies attract digitally savvy employees and get new workers up to speed more quickly and efficiently than ever before. Digital twin solutions, for instance, deliver foresight through dynamic simulation software that models physical environments like reservoirs, processing facilities and pipelines. Digital twins enable companies to perform advanced testing and train operators, all without affecting running processes.
For example, a real-time digital twin of a liquid and gas pipeline can be used to detect leaks, automate forecasting of events, and train operators. Digital twins, along with virtual and augmented reality, are helping companies upskill their workforces and fill the expertise gap with lower costs and risk to operations, safety, and the environment. Once workers are trained and ready to work on the ground, digital transformation tools also help foster collaboration and provide insights to encourage better decision-making.
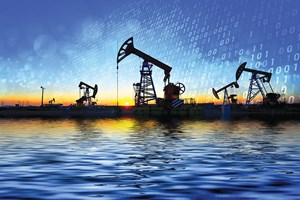
New technologies make safe, remote operations a reality, Fig. 1. With secure cloud-based supervisory control and data acquisition platforms and mobile app-based monitoring tools, operators can access production data, trends, and alarms in real time—from anywhere in the world. Using remote monitoring and well integrity technologies, for instance, companies can access accurate and reliable well data, identify and prevent integrity issues, and optimize well production. These wireless solutions provide real-time data analysis to eliminate time-intensive and costly manual operations, unnecessary workovers, and prevent safety or environmental incidents.
Wireless sensors, mobile apps, and data analytics software make the industry not only more appealing for new workers, but also safer. By making data accessible securely via cloud platforms or mobile apps, workers across the oil and gas industry can control and monitor operations as if they are in the field, all while safely seated in an integrated operations center, or even their living room.
Prescriptive maintenance and reliability. Over the past 20 years, predictive maintenance has been deployed across the energy industry to help companies reduce operational costs, optimize maintenance schedules, and reduce costly unplanned downtime. Now, as technologies become smarter, the industry is moving from predictive to prescriptive maintenance, which can not only detect issues ahead of time, but also prescribe the solution to mitigate the problem.
However, in large facilities, data are often spread across the enterprise and isolated in silos, making it difficult to identify issues impacting asset availability. To address this issue, more companies are implementing asset and plant optimization software platforms that combine data from multiple applications into actionable information, available across the enterprise. All of the insights and analytics can be accessed from anywhere, using a mobile device. This helps operators spend less time collecting and analyzing data, and more time applying it, allowing them to make informed decisions about asset health to improve reliability and performance. These technologies can be deployed over the cloud and as a service, ensuring expertise is ready on demand so companies can quickly and easily ramp up or down based on market dynamics.
Smart logistics and supply chain technology. At the onset of the Covid-19 pandemic, oil and gas producers were hit with a sudden and dramatic fall in demand, resulting from reductions in business operations and travel around the world. These trends have continued, as fuel consumption remained well below its pre-pandemic levels into September 2020. For many companies confronted with oil production far greater than the world’s requirements, this has presented challenges to track supply chain logistics and control flaring for fields, along with oil spillage from tanks and terminals.
These shifting circumstances bring into focus the importance of terminal management for coordinating resources, information and assets to ensure optimal efficiency. Tank management technologies—such as real-time inventory
monitors, tank gauging technologies, field measurement devices, and automated valve and lineup tracking—are helping operators avoid costly overfills, equipment damage, and product contamination, while increasing terminal capacity.
In addition, inventory management software is providing operators with complete online visibility into all the above and more, so they always have a real-time overview of what’s happening in, and between, tanks. This is helping to enhance product quality, safety, and inventory calculations, especially important now, as companies work to manage supply overages.
Cybersecurity. It’s difficult to talk about digital transformation without mentioning the importance of cybersecurity. This is more relevant now than ever, as remote operations increase, due to Covid-19. Industrial organizations are vulnerable to cybersecurity threats. In fact, according to industrial cybersecurity firm Dragos, 66% of the incidents they responded to in 2019 involved adversaries directly accessing industrial control system networks from the internet.
Oil and gas companies must follow best practices and have the right systems in place to protect their operations. By leveraging the right expertise and technologies, companies can build and apply robust defensive strategies to ward off attackers. This is about people, processes and products. It is necessary to empower workers with knowledge, behaviors and tools to identify and prevent cyberattacks, and to ensure processes and technologies with cybersecurity-layered protections are in place, to keep companies in control of their facilities.
Digital efficiency gains key to future success. Digital transformation was once a futuristic concept for performance improvement. Now, due to new and unforeseen challenges in market demand, staffing, and worker health and safety, it has become the only path forward. By strategically investing in the right technologies that enable efficient remote operations and help oil and gas companies meet metrics and revenue targets, the industry will be better off in the long run. Digital transformation is a requirement to keep businesses alive while ensuring the most efficient and sustainable use of resources. After all, the smarter the operations, the more reliable, clean and safe they will be.
- Aramco's upstream digital transformation helps illuminate the path toward excellence (June 2024)
- Adopting a holistic approach to cybersecurity (March 2024)
- Embracing automation: Oil and gas operators leverage new operational efficiencies (May 2024)
- The five A’s on the road to completions automation (May 2024)
- Digital’s influence on drilling and production keeps growing (March 2024)
- Taming the red zone with automation (April 2024)