How to keep E&P workers healthy, safe and working while preparing for increasingly remote operations
Covid-19 has brought the world’s economy to such a standstill that some pundits have taken to calling these unprecedented times “The Great Pause.” In less than two months, just about every industry has had to rethink its business model, especially oil and gas. Not only has this industry been among the hardest hit by falling demand, but a savage price war by sovereign players has also made the industry’s financial situation much, much worse.
Short-term, operators must worry about their workers’ health and safety, while also conserving cash via drastic cuts. Longer-term, they must consider ways to keep personnel healthy—especially if waves of COVID-19 infections recur (as expected)—and to stay profitable in almost all pricing environments.
To be sure, the “shelter-in-place” government mandates—requiring home teleworking for millions—are demonstrating and accelerating a fundamental change in how work gets done. For operators, one certainty is emerging amidst all the uncertainty: The future of the entire industry will be increasingly remote.
LEVERAGING AND EXTENDING DIGITALIZATION TO SUPPORT ESSENTIAL PERSONNEL

One strategy to consider, for helping keep essential on-the-job personnel safe and healthy, is for operators to leverage and extend their existing digital infrastructure and deploy remote field services, performance monitoring, and guidance technologies in highly cybersecure environments, Fig. 1. These technologies are available today, to help maintain operations and safety excellence through the industry’s current disruptions.
This strategy can be employed by operators, no matter how limited or advanced their levels of digitalization, automation and electrification may be today. What’s more, cybersecure remote operations are possible to enact within weeks, not months or years. Then, as the pandemic eventually subsides, operators will be poised for a future of increasingly remote operations, with the benefits of greater operational visibility, safety, security, availability, and asset utilization.
Many operators may have been reluctant to deploy remote services and technologies in the past, due in part to cybersecurity concerns. Today, however, they do so while staying secure and cyber-resilient with global security standards IEC 62443, ISO 27001, and NERC CIP—the same levels of data security used in the financial services industry and by governments. Importantly, this security is optimized for the rigorous demands of sophisticated industrial operational technology (OT), including automation and control systems.
SECURE, REMOTE OPERATIONS AMPLIFY STAFF CAPABILITIES
A remote monitoring and guidance strategy can enable personnel, who absolutely must be at a facility to focus on other operational objectives, and not be burdened with the inherent operating and maintenance demands of rotating equipment. This is greatly augmented by the latest wearable communication technology, enabling real-time collaboration (RTC) and virtual over-the-shoulder support, which is commonly referred to as Remote Field Service (RFS). In effect, deploying a secure remote strategy can amplify an essential staff’s overall onsite capabilities. At the same time, it also enhances the operational performance, safety, reliability and availability of extremely sophisticated capital assets with the knowledge and expertise of the original equipment manufacturer (OEM) supplying those assets.
RTC allows remote experts experienced in diagnostics, maintenance and repair of rotating equipment to remotely support and guide on-site personnel to an extent that was never capable before. One of the world’s largest oil services firms has an extensive pilot of RFS underway, with positive results paving the way for its expansion. Another RFS pilot is being conducted at a top global chemical company with major petrochemical operations that provide hydrocarbon feedstocks for its other product segments.
In evaluating partners to provide remote monitoring and guidance services, operators need to consider two types of services available today. One is proactive Remote Diagnostic Service (RDS). The other is reactive troubleshooting technical support that is greatly enabled by RTC.
While reactive troubleshooting supports a break/fix model intending to minimize disruptions that have already occurred, RDS aims to prevent disruptions via remote condition monitoring. Using rules- and physics-based, data-driven analytic methods—often augmented with artificial intelligence (AI) and machine learning—expert engineers can detect deviations of operational behaviors. These deviations can provide alerts and insights to detect failures before they happen, via early warnings of critical changes in the health status of complete trains of rotating equipment.
Ideally, a single supplier, either the OEM or a highly qualified alternate, will provide both necessary and complementary services, Table 1.
PUTTING RDS TO WORK IN DIGITAL OIL FIELDS
In practice, the remote monitoring and diagnostics of rotating equipment provided directly by the OEM can be indispensable to increasing asset reliability and availability, lowering maintenance costs, and providing visibility and continuous awareness about the equipment’s health status. This can pose a challenge to the existing tool landscape, which typically relies on adapting condition monitoring solutions to expert systems. Specifically, OEM engineers need fault detection, fault isolation, failure mechanism definition, and diagnosis definition as part of the system diagnostics, to support their decision-making process, up to and including the corrective action recommendation.
However, due to the technical complexity from a large number of sub-systems and process flows, diagnosis for rotating equipment can often demand the multi-disciplinary expertise of engineers from diverse domains, such as system mechanics, aerodynamics and thermodynamics, to name a few. Specifically, root-cause analysis, as part of failure analysis within system engineering and diagnostics, is an indispensable feature of the design and maintenance phase. It allows identification of faults, based on their causes and consequent effects that can further propagate at different system levels.
So, for an efficient systems-based, root-cause analysis, conducting failure analysis of rotating equipment applications today must involve an extension of traditional physics-based analytical methods. These must be augmented by rule-based systems and data-driven machine learning for drawing diagnostic insights from multi-dimensional operational characteristics.
This three-step approach, based on physics, rules, and machine learning, formalizes the various and more traditional qualitative models of monitoring the performance of crucial turbine components. With their large manual dimensions, these qualitative models are often highly error-prone, together with their potential failure mode descriptions of different system levels.
Today, this information—drawn from decades of operating data from rotating equipment deployed worldwide—has been compiled into a single, vast knowledge base and regularly processed semi-automatically, using different AI-based reasoning engines. For example, the contents of the Siemens knowledge base are drawn from operating performance histories compiled from available samplings. These samplings represent more than 130,000 industrial rotating equipment installations worldwide, with nearly two-thirds in oil and gas applications.
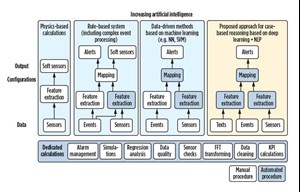
As shown in Fig. 21, this approach thus utilizes all available historical operational data of the rotating equipment to leverage the hidden knowledge accumulated over decades. To make this feasible, all aspects of an operating issue must be addressed: 1) sensor data from instrumentation; 2) sequences of events from control systems; complemented by 3) reports (i.e., textual information) which can be understood as annotations of the raw data. This approach constitutes an extension of existing hybrid diagnostic systems to fulfill current requirements in both failure detection and isolation for industrial operations.
RDS, AN OPERATOR-OEM DATA-SHARING MODEL
At its core, RDS for rotating equipment is a collaborative, data-sharing model consisting of remote data monitoring and diagnostics done in concert between its operators and its OEM. This is done with the notable and critical addition of rigorous cybersecurity to safeguard the operating data while in motion, and at rest. Also, RFS further enhances collaboration, in conjunction with RDS, to maximize troubleshooting support.
RDS effectively establishes an early-warning system that can alert operators to performance anomalies in their rotating equipment, which can reveal maintenance needs before a breakdown occurs. This actionable intelligence also can provide decision support on how best to manage degrading performance until the next planned maintenance outage.
Compared with on-premise, condition-monitoring solutions, which typically depend on data-driven analytics, connecting rotating equipment back to the OEM via RDS can provide these benefits:
- Comparisons between actual as-is and as-designed performance parameters can be performed, using the equipment’s design software packages and its digital virtual twins;
- Avoids false alerts that can distract or confuse onsite operators, because the OEM can filter out false-positives and providing warnings of confirmed anomalous behaviors;
- Accesses as-built equipment knowledge, which only the OEM has and can be critical when a genuine step-change occurs, and this question must be answered, “How can it be mitigated and remediated?”;
- Facilitates comparisons across rotating equipment installed worldwide, leveraging the knowledge of all those units with identical configurations, industry segments, and operational models.
RDS, backed by expert service engineers, supports more proactive approaches that involve condition-based and predictive maintenance. These services can potentially save substantial maintenance costs, when compared to conventional schedule-based models.
The latter are more reactive, triggering unneeded maintenance just because OEM standard schedules might require it. Over time, this can make a huge difference in the total cost of ownership (TCO) of rotating equipment. Also, the additional availability of proactive RDS/RFS-enabled approaches can translate to significant cost avoidance by saving disruptive downtime and related expense. Downtime can send TCO soaring.
Another benefit of more proactive and tailored maintenance approaches is extending the life cycles of components. What’s more, higher asset utilization can boost returns on invested capital, an important consideration given the capital intensity of rotating equipment. Performance optimization can help save OPEX, too. Fouling, for example, can increase throughput pressure, requiring more energy—as much as 850 additional KW per day for every five 5-psi increment in pressure2.
Data-sharing, analytics, alerting, and the mitigation/remediation processes of RDS-based performance monitoring and diagnostics start with unit sensors that collect operating data on a wide range of parameters, such as speed, temperature, vibration, and so forth. The data are processed with 256-bit encryption, same as the world’s top banks and governments use, and sent hourly or daily, over a highly secure, virtual private network (VPN) connection to the monitoring facility.
Should remote troubleshooting be required, operators can connect their onsite rotating equipment with its OEM by using their VPN network solution. This way, they can retain full control of their VPN connection, used to manage data access. Data streaming at faster intervals will soon be possible, which will enable OEMs to predict performance issues and preempt disruptions even faster and more precisely than is possible today.
Another RDS innovation is a proprietary time-stamping technology that’s already being used in the onshore remote condition monitoring of rotating equipment on North Sea oil platforms. Conventional condition-monitoring methods sample time intervals, such as every third second. While that might catch one anomaly, it could miss another one, especially if multiple events are recorded in one sample. If two or more events occur in a single sample, it’s impossible to know their sequence and therefore determine any cause and effect.
With time stamps, however, the sequence of an event series can be clearly seen, making it easier to identify and distinguish correlation and causation. This can accelerate troubleshooting by making data analysis more precise, reliable and insightful.
IDENTIFYING ANOMALOUS PERFORMANCE BEHAVIORS, PROVIDING ACTIONABLE INTELLIGENCE
In the case of a performance anomaly in rotating equipment, the OEM will notify the operator of it, along with a risk assessment and suggested course of action (i.e., actionable intelligence). The remediation may need to be immediate, to prevent a forced outage, or it can be scheduled to be addressed during the maintenance window of a planned outage. If parts need replacement, spares can be pulled from inventory or, if not available onsite, express-delivered to minimize downtime, due to logistic delays.
Then, when the remediation of a potential or actual problem does take place, engineers in the remote diagnostic centers can tap into the compressor train’s human-machine interface (HMI) and, through RFS, observe and advise the maintenance technician on the proper procedures to follow. This real-time, “over-the-shoulder” engineering support can help to significantly reduce mean-time-to-repair (MTTR) cycles, reducing outages, if forced, and minimizing their disruptive costs. In effect, this approach combines the in-depth OEM compressor train knowledge of the manufacturer, with the extensive onsite operations experience of the customer.
RETHINKING E&P OPERATING MODELS TO ENHANCE HSE
Eventually, the Covid-19 pandemic will subside, and market prices for the world’s oil will stabilize and hopefully rise to much more profitable levels. In the meantime, essential E&P personnel must be kept safe from infection and illness, and operations must continue.
Fortunately, the advanced digitalization of rotating equipment, along with cyber safeguards and highly secure network communications, has enabled RDS from an OEM to monitor performance remotely and conduct diagnostics, as needed. Also, RFS has enabled an even higher degree of OEM support, meaning equipment anomalies are resolved in the shortest possible time.
As mentioned, many operators have had serious concerns about cybersecurity, slowing their embrace of digitalization and remote monitoring models. However, the industrial cybersecurity safeguards used today are considered the most robust available.
Going forward, a closer collaboration of E&P operators and OEMs via RDS and RFS, based on a continuous and highly secure data exchange, will enable functional models that are characterized by real-time remote performance monitoring and diagnostics. The economics will be compelling, especially in terms of ensuring optimal asset utilization, lower TCO, and higher returns on invested capital.
REFERENCES
- Thomas Hubauer, Ph.D., et al. “A diagnostic & corrective action system, based on deep learning and natural language processing.” October 2016.
- Khalaji, Shaghayegh. “Compressor Optimization—1: Energy recovery guides natural gas pipeline system efficiency,” Oil & Gas Journal, Jan. 9, 2012, http://www.ogj.com/1/vol-110/issue-1a/transportation/energy-recovery-full.html
- Digital transformation/Late-life optimization: Harnessing data-driven strategies for late-life optimization (March 2024)
- The reserves replacement dilemma: Can intelligent digital technologies fill the supply gap? (March 2024)
- Digital tool kit enhances real-time decision-making to improve drilling efficiency and performance (February 2024)
- Digital transformation: Digital twins help to make the invisible, visible in Indonesia’s energy industry (January 2024)
- Digital transformation: A breakthrough year for digitalization in the offshore sector (January 2024)
- Quantum computing and subsurface prediction (January 2024)