Collaboration drives subsea innovations and efficiency gains
The award in March 2019 of the front-end engineering and design (FEED) contract for Australia’s Jansz-Io offshore compression project marked a milestone in the history of subsea compression technology. This development will be the first application of this type of subsea system outside the North Sea and Norway.
Several years earlier, ABB partnered with Aker Solutions to combine their respective expertise in subsea power distribution and automation solutions for such a project. While the technology alliance was not awarded the contract directly, the two companies will be working together to make this project a reality.
As lead contractor, Aker Solutions was awarded a master contract by the operator and will be working closely with technology partners—ABB and compressor manufacturer Man Energy Solutions—to achieve what is expected to be a step change in efficiency, compared with conventional seabed compression systems. This installation has the additional challenge of being in much deeper waters of up to 1,300 m (4,265 ft), but it is still within the power equipment’s depth capacity of 3,000 m (9,843 ft).
Deploying subsea technology in Western Australia. In the initial phase of the proposed, expanded development, a low-risk subsea compression system is being proposed, which might seem noteworthy, considering the inherent complexity of such a system and the environmental challenges. The system will allow the continued plateau production rate of gas, despite a declining reservoir, which is converted to 15.6 million tons of LNG per annum, plus domestic gas to be supplied to customers.
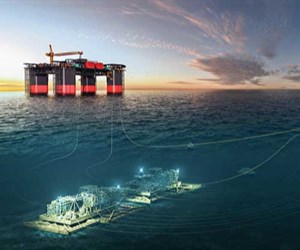
The compression modules, initially proposed to be three in the project’s first phase, will be located close to the existing seabed production system and supported by a semi-submersible utilities platform moored nearby, Fig. 1. The semi will be located roughly 120 km (75 mi) from the Barrow Island field control center, which operates as the LNG processing facility for Western Australia’s Greater Gorgon subsea gas development, which includes Jansz-Io.
The decision to include a normally unattended platform as part of the overall system will allow the deployment of topside variable speed drives (VSDs), to run and control the compressors. Phase 2 of this enhanced recovery system will include additional seabed compressors.
Environmental challenges. While the use of a platform reduces some of the subsea system’s technical complexity, it provides its own challenges. The environmental conditions, where the semi will be moored, are extremely harsh, with extremely high daytime temperatures. They will require special consideration of materials selection used on the support facility. In addition, there will be a power cable running from Barrow Island to the facility, which also will have to be designed to withstand the degradation effects of the high temperatures and dynamic behavior.
COLLABORATIVE DEVELOPMENTS
Prior to the Australian project, Aker Solutions and ABB were involved in three important Norwegian subsea processing systems installed during the last 15 years.
Ormen Lange pilot project was the first underwater compression project. Initially conducted in an onshore test pit filled with seawater, it was initiated by Norsk Hydro in 2006. Operations for onshore testing were assumed by Statoil (now Equinor), following the merger of the two companies in 2007. It was then handed over to license partner Norske Shell, which saw it through to completion in 2016.
After testing Orman Lange onshore, the development was moved 120 (75 mi) northwest of Kristiansund, Norway, where water depths vary between 800 m (2,625 ft) and 1,100 m (3,609 ft). The reservoir is approximately 3,000 m (9,843 ft) below sea level, covering an area 40 km (25 mi) long and 8-10 km (5-6 mi) wide. Three subsea templates, positioned on the ocean floor, are connected directly by two 30-in., 120-km (75-mi) pipelines to the onshore process terminal at Nyhamna.
ABB delivered a subsea transformer for pilot testing for the Ormen Lange development. The subsea transformer at Ormen Lange is designed for up to 100 MVA filled with mineral oil. The subsea transformer pressure compensator is composed of a double inner metallic bellow—made by SMO— and an outer bellow made of rubber. ABB uses a two-barriers design for the compensators that are qualified for 30 years of operation.
Aker Solutions was also the main contractor on this trial and was integrally involved in many aspects of the compressor station system, including: 1) the separator and slug catcher module; 2) an anti-surge cooler module; 3) the compressor module; and 4) the pump module. ABB installed the all-electric power-and-control system, one of its core technical competencies.
Tyrihans field. Before subsea compression moved beyond research and development into a commercial project, Equinor approved the first-ever subsea raw water injection system for Tyrihans field in 2006. In a preview of what would become the newly formed alliance, Aker Solutions and ABB once again worked hand-in-hand on this development.
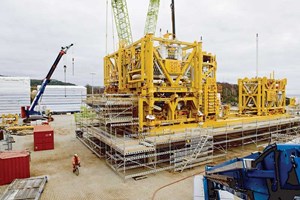
Aker Solutions was contracted to deliver the pump module system skid, capable of delivering 125,000 bpd of raw water for pressure support into the wells, with ABB handling the electrical power system. This project would see an ABB ACS1000 frequency converter installed on the host Kristin platform, 31 km (19 mi) away, linked to a pump motor module adjacent to the subsea production templates. The frequency converter was deployed to ensure that the optimum voltage is supplied to the pump motor. A subsea transformer, from ABB, was used as a step-down transformer close to the subsea pump.
Åsgard field development sets new subsea benchmark. The arrival of subsea compression, as a qualified development, came to fruition in December 2010, when Equinor awarded Aker Solutions the contract for a subsea system for Åsgard field in the Norwegian sector of the North Sea. The Åsgard long step-out power system consists of two compressor strings and two pump strings, Fig. 2. The subsea power system for the compressor string transmits 15 MVA of electric power at 34 kV/120 Hz over a 43-km (27-mi) subsea cable. This is a world record for distance, voltage, power and frequency between a drive on a floating production facility and a seabed compressor.
The 1,800-t system, which Aker Solutions delivered to boost production from the Midgard and Mikkel satellite fields, is a “wet-gas” compressor. This technology is fully redundant, meaning it consists of two identical compression modules made up of a compressor, pump, scrubber and a cooler, Fig. 3. ABB played a critical role in this development, having been contracted to supply the power system for the compression skid, which is located 43 km (27 mi) from the host platform. The power requirements were 18 MVA at 120 Hz, a record at the time for distance, voltage and frequency between a host facility.
To overcome the challenge of supplying high power over such a long distance, ABB carried out an extensive program of dynamic simulations to better understand system behavior. The simulations revealed that the power system would meet the requirements of the pump and compression module. The modeling also identified that new transformers and control software were needed for efficient operation of the frequency converter and the overall system. On this development, ABB supplied the largest subsea transformer ever installed on the seabed at that time.
Value delivered. The confidence that an operator has in any technology is confirmed, when it delivers measurable economic benefit. By using subsea compression on Åsgard field, an additional 306 MMboe could be added to recovery, a claim that exceeds the figure used to justify the use of subsea separation on Tordis field. From a technical perspective, the system installed at Åsgard is a significant success, with confirmation of 99% availability over four years of operation.
Collaboration continues. The successful delivery of the Åsgard system set in motion a series of events that would lead to several new collaborative ventures the following year. The two companies delivered additional equipment for Åsgard field in September 2015, nearly five years from contract award. The following month, Aker confirmed a new alliance with Man Energy Solutions to develop the next generation of subsea compression systems.
In the spring of 2016, ABB and Aker Solutions, who had been working in conjunction on several subsea and conventional projects, formalized a relationship with a strategic alliance agreement. It combines the companies’ strengths to develop more effective, efficient and reliable subsea process systems. The target objective for the alliance was to achieve a reduction in weight, dimensions and step-out length for a future subsea compression systems.
There would be technical, as well. Incorporated into any future design would be the use of Aker Solutions’ latest version of its advanced control system, Vectus. The system has been upgraded with fiber optics and wider bandwidth for faster data transfer. The increased efficiencies are a major improvement over previous control systems. Additionally, Vectus was designed and developed specifically for subsea processing applications.
Western Australia application. The importance of the Vectus system to the future of the Western Australian operation was emphasized earlier this year, when the operator filed an environmental plan with oil and gas regulators for expansion of production facilities for the Gorgon and Jansz-Io complex. The operator plans to include additional production wells and gathering manifolds, plus infield flowlines to carry new gas production to the subsea gas gathering network.
The subsea gas compression system—to be supplied by Aker Solutions and collaborators ABB and Man Energy Solutions—will provide support for new and existing gas production for the foreseeable future. Going forward, the two companies plan to build on the system proposed for Jansz-Io, offering a complete subsea solution that employs the seabed-to-host technology developed and qualified under the JIP.
WORLD-CLASS SOLUTIONS
The subsea technologies developed by ABB and Aker Solutions will help companies extract oil and gas more safely and cleanly from their offshore operations. This objective will be accomplished by employing state-of-the-art subsea technologies and engineering expertise, to support offshore producers on their journey toward more autonomous and sustainable operations.
Powering the seabed
To remain profitable, offshore operators are exploring in increasingly remote locations and in ultra-deep waters. Previously, these environments were too challenging and/or expensive to consider. However, the development of new smart, reliable and cost-efficient technologies is enabling operators to produce safely in the harshest subsea environments.
Constructing fully functional facilities on the seabed, which will eliminate the need for heavy fixed or floating installations on the water surface, is a highly efficient means of producing oil and gas from reservoirs located far from shore. With subsea pumping and gas compression, energy resources can be utilized more efficiently to increase recovery rates, lower production costs, enhance safety and further development of deepwater operations. Removing the topside installation will also result in fewer persons onboard, decreasing risk and expenses.
ABB’s first-of-its-kind subsea power distribution system, which passed a viability test in November 2019 (Fig. 1a), can supply electricity to the seabed via a sleek cable extending up to 600 km (373 mi) and going as deep as 3,000 m (9,843 ft). Supplying power directly to underwater pumps and compressors near the reservoir leads to energy and cost-savings, as well as reduced carbon emissions.
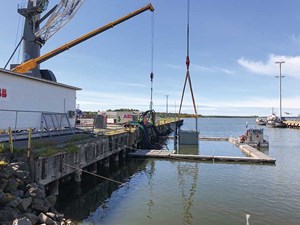
How it started. As part of a five-year joint industry project (JIP) between ABB and Equinor, with its partners Total and Chevron, ABB has expanded the boundaries in design, development and testing of subsea power distribution and conversion technology. The result is the world’s first fully qualified subsea medium voltage (MV) power distribution and conversion system. These technologies enable all production operations to be moved to the seabed for the first time.
System Technologies
The collaboration led to the development of ABB’s flagship control system, ABB Ability System 800xA. The comprehensive subsea power distribution and conversion technology includes a step-down transformer, medium-voltage variable-speed drives/switchgear, control and low-voltage power distribution and power electronics and control systems.
The medium-voltage (MV) subsea switchgear distributes 11-33 kV to the motors driving the compressors and pumps, via the VSDs. The switchgear supports up to six feeders, or a tie-breaker to support cascading of two switchgear assemblies. The unit connects to a subsea stepdown trans-former, or directly to a subsea power cable from topside to shore. This new switchgear is sufficiently powerful to supply electricity requirements for a small town.
The MV subsea switchgear is based on ABB’s widely used vacuum breaker technologies, which have a long record of reliable operation and established quality control and obsolescence strategies. All components are designed to operate at 300 bars.
Variable speed drive. From the subsea switchgear, a transformer steps-down the 11-33 kV input to the 2.3 or 7.2 kV required by the VSD. The VSD typically controls a subsea compressor’s motor with 6 to 7 kV. Subject to water temperature and application requirements, even higher output voltages may be needed. The modular VSD ensures that two units in parallel can run a load of at least 18 MVA. Mounted on a common subsea frame, multiple VSDs can be combined, thereby avoiding any increase in the number of wet-mate connectors needed. The VSD is packed with diagnostic sensors, which track the performance of the driven load, as well as the on-going performance of the drive, itself. This ensures the highest system resilience by helping operators to predict behavior, optimize operations and track key performance indicators.
Moving toward a sustainable future. The technology provides an oilfield environment that is completely free of surface infrastructure on the oceans. By powering pumps and compressors on the seabed, closer to the reservoir, ABB’s subsea power distribution and conversion technology can significantly reduce power consumption. There is also potential for substantial energy savings, with reduced carbon emissions using power from shore. ABB’s subsea power technology can connect to any power source, enabling future integrations with renewable energy, such as wind and hydropower.
Value proposition. Based on a specific field development case, the new technology could offer capital expenditure savings of more than $500 million, if eight consumers, such as pumps or compressors, are linked through a single cable over a distance of 200 km (124 mi) from other infrastructure.
From the outset, the JIP was aimed at developing a number of technologies that would enable future subsea gas compression, pumping and separation systems—which, along with raw water injection make up the quartet of technologies that fall under the umbrella of subsea processing. ABB believes that one of the main results of the JIP was the optimization of cost, which would allow the new technology to be suitable for low-power (3-4 MW) applications and for high power (10 MW+) systems. This is important, because the marketplace will need to be even more efficient for upcoming projects planned in the North Sea and offshore Brazil.
- Advancing offshore decarbonization through electrification of FPSOs (March 2024)
- Subsea technology- Corrosion monitoring: From failure to success (February 2024)
- Driving MPD adoption with performance-enhancing technologies (January 2024)
- Digital transformation: A breakthrough year for digitalization in the offshore sector (January 2024)
- Offshore technology: Platform design: Is the next generation of offshore platforms changing offshore energy? (December 2023)
- 2024: A policy crossroads for American offshore energy (December 2023)