JUSTIN SMITH, Offshore Editor
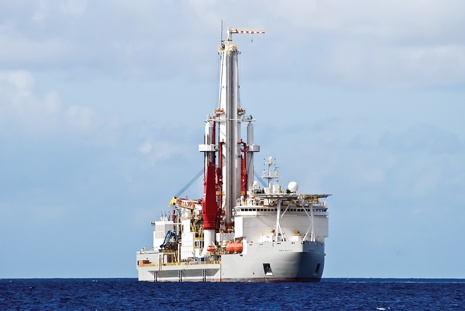 |
Newbuild ultra-deepwater drillship Noble Bully I arrives in the U.S. Gulf of Mexico, preparing for its initial contract with Shell. |
|
A majority of the deepwater rigs that have been ordered in the last few years are traditional drillships and semisubmersibles. However, not all rigs are built alike, as is the case with two drillship models being built for Noble Corp., as well as a unique type of semi being constructed for Norwegian operator Statoil via rig contractor Songa Offshore.
Some of these novel rigs have already entered the market, while others have just barely started being built. Either way, these new rigs are answering the call from oil companies for more efficient operations, as well as for working in areas where demand exceeds the number of rigs available.
NOT ALL BULLIES ARE BAD
One of the more distinctive rig designs that has emerged over the last couple of years is the Bully drillship, which was custom-created in first-half 2007 for Frontier Drilling to fulfill a need for Shell. In 2010, Noble acquired Frontier and the two Bully drillships under construction at the time for $2.2 billion.
Gusto MSC designed the dynamically positioned vessel in concert with Dutch offshore designer Huisman, which was awarded a contract to design and manufacture the drilling tower and related pipe, riser and blowout preventer equipment. The Bully series of drillships can drill to a total depth of 40,000 ft and operate in up to 10,000 ft of water, although the units are currently equipped to work in up to 8,500 ft of water. The vessels are designed to offer a lower-cost alternative for drilling in ultra-deep and, with the ice-class rating, in Arctic conditions.
The selection of Huisman’s in-house-designed compact box-type drilling tower, known as the multi-purpose tower, instead of a conventional derrick, allows for a much smaller-sized vessel, compared to other deepwater drillships of similar capacity. The drilling equipment set is based on the HuisDrill 12000 design and allows offline stand-building. More than 48,000 ft of drill pipe and casing are racked back in two carousel type setbacks. Drill pipe and casing are handled in 135-ft lengths. The 2,400-kip drill tower is fitted with active heave-compensated drawworks mounted inside the tower, according to Huisman.
The remote, changeable reeving of the drill line allows high block speeds at low fastline speed. The application of dual drawworks completely eliminates cutting and slipping of the drill line, so no deadman anchor is necessary. The passive drillstring compensation to the active heave-compensated drawworks provides inherent redundancy.
The first of these two units, Noble Bully I, arrived in the U.S. Gulf of Mexico in December and, according to World Oil’s offshore rig database RigStar, is about to begin a five-year contract drilling on Shell’s Mars B, Olympus development, during which the rig will earn $469,000 per day. The second drillship was recently delivered from Keppel FELS shipyard in Singapore and is en-route to Brazil, where it will work for 10 years at $461,000 per day.
SECOND VERSE, AKIN TO FIRST
In mid-2008, Huisman was awarded a contract by Noble for the new drillship design HuisDrill 12000, with options for an additional three, one of which has been exercised. The drilling equipment is based on the drilling mast and pipe storage in carousels, as delivered for the Bully vessels. The vessel will be self-propelled with DP-3 classification. It is suitable for both marine drilling riser and pressure riser drilling. This modified design is now known as the Globetrotter Class. As opposed to creation of the Bully model, Huisman is not only responsible for the design of the drilling equipment, but also for the concept design of the vessel, resulting in a more compact drilling vessel, and lower building and operational costs.
While smaller than similarly capable rigs, the Globetrotter units are able to operate in up to 12,000 ft of water, although, once again, they are only equipped for 10,000 ft upon delivery, and are able to drill to a TD of 40,000 ft. The design also incorporates a 2,400-kips static hook load capacity on both sides of the mast and 43,000 ft of pipe storage capacity.
The unconventional ship design also has the engine room placed forward, underneath the accommodation section, freeing the ship’s aft portion for drilling equipment or tubular storage. Notably, all of the risers and most of the drilling tubulars are stored below deck, aft of the drilling mast. This leaves a larger deck area free, specifically 45,000 sq ft, which can be used for non-permanent equipment. The variable deck load is 20,000 t.
To lower the center-of-gravity of the drilling equipment, and reduce the sideways motion of the rig, the drill floor has been installed only 16 ft above the main deck. According to Huisman, this is made possible by lowering the BOP through a large hatch, aft of the drill mast before skidding it to the well center, forward of the mast. Also, the top section of the mast can be removed to allow passage through the Panama and Suez Canals, as well as below the Bosporus Bridge in Turkey.
The vessels are being built by STX shipyard in Dalian, China, followed by the drilling equipment being installed and commissioned by Huisman in The Netherlands. According to RigStar, the first of the two rigs, Noble Globetrotter I, was recently delivered and will soon head to the U.S. Gulf to start a 10-year contract with Shell, earning $424,000 per day. The second rig is still under construction in China, but should begin a 10-year contract with Shell, at $410,000 per day.
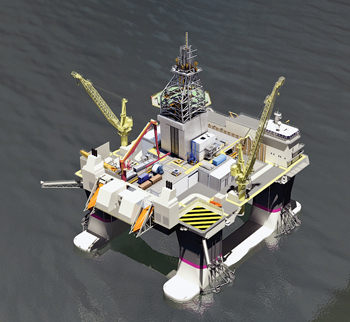 |
Fig. 1. A rendering of Statoil’s newly designed Category D semisubmersible, which can work year-round in the North Sea. |
|
CATEGORY DEVELOPMENT
Discoveries on the Norwegian Continental Shelf (NCS) are getting smaller, forcing operators to increase drilling in mature fields to squeeze more oil. It is, therefore, necessary to reduce rig costs to realize the potential value. According to Statoil, “The key to maintaining today’s production level on the NCS toward 2020 is improved recovery from existing fields, and fast and efficient development of new fields. In order to implement these measures, it is crucial that we secure a rig fleet that is adapted to suit the assignments and can work more effectively.”
Statoil has developed a new mobile offshore drilling unit concept, the Category D (Cat D). These rigs will be customized for year-round production drilling in the North, Norwegian and Barents Seas. The Norwegian operator’s goal is that the new rigs will perform operations 20% more efficiently than conventional rigs. “The rigs delivered to the NCS in recent years were, first and foremost, constructed for operations in deep water,” said Jon Arnt Jacobsen, chief procurement officer for Statoil. “That means that they are big and too costly for our requirements and challenges on the NCS. We are, therefore, taking steps to rejuvenate the rig fleet and ensure that the right rig meets the right requirements.”
The specially-designed Cat D rigs (Fig. 1) will be able to operate at water depths up to 4,265 ft and drill wells down to nearly 28,000 ft. They will be workhorses on mature fields, primarily for drilling production wells and performing well completion work. They also will serve as semis for mid-water segments on the NCS, but still be able to work in other regions. The rig concept can easily be converted for work in deepwater, high-pressure/high-temperature operations and Arctic regions.
The design includes large available deck areas for completion logistics, and motion characteristics that reduce unproductive time, as when waiting on weather. It also reduces time through simultaneous drilling and building stands, as well as a moon pool trip-saver for hanging off the BOP.
Songa Offshore has received a contract from Statoil for two new-build Cat D semis with firm terms of eight years, each, with options that could extend this period to 20 years, to work on the Troll field. The firm part of the contract has an aggregated revenue value of about $2.5 billion, inclusive of mobilization. Statoil has an option to award contracts for two additional rigs to Songa. Mobilization of the units to Norway will take place in direct continuation of the rigs’ delivery from Daewoo Shipbuilding & Marine Engineering in South Korea, in the first and third quarters of 2014. The fixed price is $565 million per unit.
Finnish engineering firm Wärtsilä has been contracted to supply the power and positioning system for these two Cat D semis. This contract was signed in November. It calls for the company to supply, for each rig, six 12-cylinder Wärtsilä 32 engines in V-configuration with ancillaries, and six FS3500 main steerable thrusters, as well as integration of the entire system. Additionally, the engines and thrusters will be equipped with the company’s condition monitoring system. 
|