The Guara and Lula (formerly called Tupi) fields are among the first of the giant presalt discoveries made by Petrobras in the Santos basin. In March 2011, Petrobras awarded Subsea 7 a billion-dollar contract for the subsea work associated with the development of the Guara-Lula NE areas. The engineering, procurement, installation and commissioning (EPIC) project is the largest of its type ever awarded in Brazil. The scope includes four decoupled riser systems with submerged buoys--—27 steel catenary risers with associated pipeline end terminations.
World Oil spoke with Steve Wisely, Subsea 7 Executive V.P., Commercial, and Dr. Stuart N. Smith, V.P. of Technology and Asset Development, about the technology Subsea 7 is deploying in Brazil.
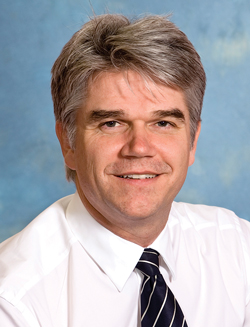 |
Steve Wisely, Subsea 7 Executive V.P., Commercial |
|
World Oil: Can you give us a little background on the Guara and Lula project?
Wisely: Brazil is a very active subsea market, and they’ve got some ambitious plans to develop their pre-salt discoveries. Guara- Lula was one of the initial fields that Petrobras found in the pre-salt area. It’s in deep water—not the deepest water—but just over 2,000 m, which is quite significant. We were successful in winning the contracts for both the Guara and Lula fields.
WO: What are the particular challenges in developing these fields?
Smith: Certainly the deep water, which made for a challenge in terms of riser systems. The fluids are challenging as well—the corrosive nature means we have to use special metallurgies. Technically speaking, it’s not particularly high-pressure or high-temperature. But the scale of the project is just huge.
Wisely: I think the scale is something people don’t fully understand. In this project, we are going to be installing two submerged riser buoys in each field. It’s a decoupled riser system. This system was chosen because of the water depth and the shear number and weight of the risers, 27 in all. The risers are going to be suspended from submerged buoys (Fig. 1), which have the effect of decoupling the loading of all the risers from the FPSO units themselves. Then there are flexible flowlines that go from the top of the buoy to the FPSO, so the vessel doesn’t see anything like we would get if these risers are actually suspended directly from the FPSO.
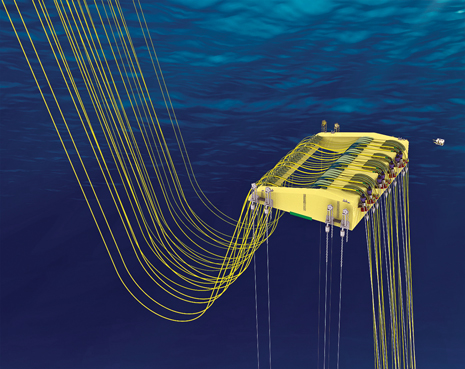 |
Fig. 1. Four submerged buoys, each weighing about 2,300 tonnes, will be installed at about 250 m below sea level. |
|
Smith: The busy system gives a few benefits that derive from the scale of the field and the number of risers. The buoy system was a good method of being able to install all those risers in a small space. Otherwise we would have needed a much larger space.
Wisely: Regarding the scope of the project, we’re doing the engineering, the procurement, installation and the commissioning, an EPIC project. There are four submerged buoys, each in the region of 2,300 tonnes. These buoys will be attached to the seabed—they’re going to sit 250 m or so below the surface of the sea. They are held in tension by tethers.
Smith: Calling them “buoys” is maybe technically correct, but you might think of them as mini-TLPs. They are about the same size as the mini-TLPs that have been used in the Gulf of Mexico. Each buoy is attached by two tethers at each corner, so it is essentially a submerged TLP. The actual size of the buoys is about 50 m across one dimension and 35 m across the other, much bigger than you would normally think of as a buoy.
Wisely: As we mentioned, there are 27 risers along with associated terminations and connectors. There was a great challenge in getting all those risers onto one buoy, with their different connectors and with the flexible risers that go up to the FPSO. There are also ROV interface panels for flooding, installing and ballasting down, plus connectors for the moorings. Individually, the risers are quite straightforward, but collectively the system is just massive.
WO: Are there any new technologies being developed specifically for these fields?
Smith: There are a couple of things worthy of comment. You have about 1,800 m between the buoy and the seabed. We’re connecting these systems after we’ve installed the buoy. The buoy takes up a wide variety of positions, so the connectors have to deal with a wide range of entry angles. None of the standard connectors on the market had the range of entry angles we needed, so there have been some interesting developments in high-entry-angle connector systems.
The other thing that has been successful is with the mechanically lined pipe. The fluids in this field are corrosive, so you can’t use plain carbon steel, you need some sort of corrosion-resistant material. Normally you might use a solid corrosion-resistant alloy pipe. But that would be hugely expensive, especially with the lengths required here.
WO: Could you explain mechanically lined pipe?
Smith: First, consider carbon steel pipe, which is not corrosion-resistant. That won’t work in this case, so you might consider making the entire pipe out of corrosion-resistant alloy, which will give the material properties we need. That becomes hugely expensive. Then you might say, okay, we know we need corrosion-resistant properties on the inside of the pipe where it contacts the fluids, so we’ll make a thin corrosion-resistant pipe, say 3 mm thick, and we’ll place that inside the carbon steel pipe. The carbon steel gives it the strength, and the alloy prevents corrosion.
We’ve been working for years with a firm in Germany called BUTTING, who make this mechanically lined pipe called BuBi pipe (Fig. 2). You take your thin tube and insert it inside the carbon steel tube, then form it into place with a hydroforming process. You pressurize it with water, and as you pressure it up, the thin pipe expands until it makes contact with the outer pipe. You then pressurize it a bit more, and the outer pipe starts to expand as well. You then release the pressure, and the inner pipe is mechanically held in place as the pipe retracts to its original size.
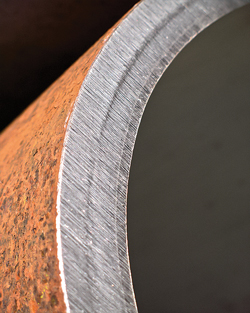 |
Fig. 2. The production and water-injection lines will be constructed from mechanically lined pipe, developed jointly by Subsea 7 and BUTTING. |
|
The concept is comparatively simple—we’ve used it before in our bundles that we use in the North Sea. Here the technology development was being able to install it by the reel-lay method.
WO: Tell us something about the reel-lay method.
Smith: On the ship itself, (Fig. 3), you have a large-diameter reel of 18-m hub diameter. The reel can take 3,500 tonnes of pipe. So we fabricate lengths of pipe that we call stalks, 2-km stalks. We fabricate them in our bases. The ship comes along, and you wind the rigid pipe around the reel. When you get the first 2 km on, you weld the next stalk onto the first, and you keep going until you have 15 or 20 km of pipe on the reel, up to your payload capacity of 3,500 tonnes. When you get out to the location, you reverse that process, remove it from the reel and straighten it to get it down to the seabed.
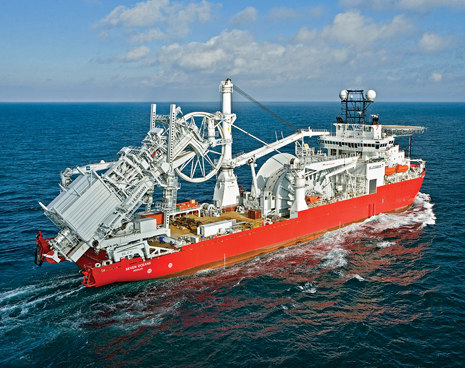 |
Fig. 3. The 27 steel catenary risers will be reel-laid and hooked up to the subsea buoys. |
|
The general technology is quite well developed, but with the mechanically lined pipe, we had to do a lot more work to ensure that we didn’t affect the integrity of the liner in any way. If you get a crack in the liner, then fluid comes into contact with the carbon steel.
WO: How do you ensure integrity with that many kilometers of pipe?
Smith: It’s a combination of the manufacturing process and the inspection processes that we go through.
Wisely: Well, we have a good track record, and we’ve used this BuBi pipe in other subsea projects. It was the trials and testing program that we did with the involvement and support of Petrobras that got us to the position where we we have the confidence to do this, and it was approved by the Brazilian authorities.
We have an exclusive arrangement for use of this particular pipe in this application. As you know, Brazil has very ambitious plans for their pre-salt development.
WO: Looking forward a few years, where do you see the technology going?
Smith: We’re working on a portfolio of things. We have developments like our autonomous inspection vehicle, the AIV, and there are a number of pipeline-related projects. We’re developing an enhanced thermal performance pipe-in-pipe system, a high-specification insulation system that is good for working with waxy crudes or fields prone to hydrates. We also have an electrically heated version of that technology.
Elsewhere, we see more in terms of high-strength steels, high-pressure technologies for up to 15,000 psi. Some operators are looking at 20,000 psi. So, obviously high-strength steel will play an important role. Also we will continue to make incremental improvements of everything we do, more effective foundations, piles, etc. We are always looking for a better understanding of the hydrodynamics, and vortex-induced vibrations.
Wisely: The important point is that, on the majority of these initiatives, we are working in close association with our client base. We want to ensure we stay focused on the same areas that our clients are focused on. 
|