Vol. 232 No.7
HENRY TERRELL, NEWS EDITOR
|
From tankards to tankers:
Putting the L in NG
|
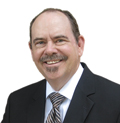
|
The world’s vast and growing liquefied natural gas (LNG) industry owes its existence to the German thirst for beer. That may be a small exaggeration, but it was the refrigeration demands of large breweries that led directly to the first gas liquefaction processes.
The art of beer production evolved in the early 14th century in small local brew houses and monasteries, which brewed and sold beer as a lucrative fundraising tool. As population and demand grew, production moved from cottage and cloister to the factory, and the need for keeping the process cold through the summer months began to outgrow the supply of stored ice, the only known refrigerant. (Previously, lagered beer, the style preferred by Germans, was a seasonal product, brewed only in winter.)
Around 1870, the president of the German Brewers’ Union, Gabriel Sedlmayr, became interested in the problem of year-round brewing, and approached a college professor named Karl von Linde for help. Linde accepted the challenge and, using a method involving the compression of dimethyl ether, built his first prototype refrigerator in 1874. A few years later, utilizing a more efficient method developed in the United States by David Boyle, Linde built his first ammonia-compression refrigerator. While Boyle had been mainly interested in making ice, Linde’s machine was a true refrigerator, and within a decade his systems had been adopted by breweries across Germany and other countries, and by other industries that required large-scale cooling, especially meat packers.
|
Karl von Linde: Father of liquefaction and friend to zymurgists.
|
|
Liquid air. By 1880, Linde had quit teaching to devote his energies to refrigeration research. Along with partners, Linde founded Gesellschaft für Linde’s Eismaschinen AG (Linde’s Ice Machine Company). Linde had a keen interest in the potential of liquefied gases. The phenomenon had been known for decades, but previous experimenters had produced only small, impractical quantities. In 1895, Linde introduced a machine that could liquefy gases continuously and in significant quantities. The device utilized the Joule–Kelvin effect, wherein a gas cools when expanding. Compressed air flows through a heavily insulated orifice (throttling device) and is allowed to freely expand. The cool air is passed through a heat exchanger to chill the air entering the device. This cycle of compression, cooling and expansion, or “cascade cycle,” continues until the air reaches about –195°C (–319°F), where liquefaction occurs. At first, the process took as long as 15 hours, but subsequent improvements reduced the time required by as much as 98%. Linde’s air-liquefaction machine won the Grand Prix at the Paris World’s Fair of 1900.
In 1902, Linde combined liquefaction with fractionation to separate air into its component gases, producing pure oxygen and, a year later, pure nitrogen.
Liquid natural gas. As was the case with liquid air, chemists had successfully liquefied small amounts of natural gas in the 19th century. With the commercial success of liquid oxygen and nitrogen, the potential storage and transport of LNG was obvious, because the process reduced its volume by a factor of 600, from a beach ball to a ping pong ball in size. In some ways, liquefying natural gas is easier, because the boiling point of the gas is a comparatively balmy –162°C (–260°F). The first LNG pilot plant was built in West Virginia in 1912. The first commercial LNG plant, in Cleveland, Ohio, was not built until 1941, with the LNG stored at atmospheric pressure in insulated tanks.
Improvements. Gas liquefaction has seen many advances over the years. The Russian scientist A. P. Klimenko introduced the single-stream mixed-refrigerant (MR) cycle in 1959. The process was further improved with introduction of the propane-precooled mixed refrigerant (C3-MR) cycle, which today is used in more than 80% of the world’s LNG plants. In the early 1960s, Phillips Petroleum developed its optimized cascade liquefaction cycle, a closed-loop cycle of propane, ethylene and methane refrigerants. In 1996, the company introduced an open-circuit variation, which recycles recovered vapors back into the liquefaction train. Improvements in all liquefaction methods have continued at a vertigo-inducing pace.
To the sea in ships. The first attempt to transport a large quantity of LNG by ship came in 1959. The Methane Pioneer, a converted World War ll liberty ship, became the world’s first LNG tanker. The vessel contained five 7,000-bbl aluminum tanks insulated with plywood and urethane. The Methane Pioneer took its LNG cargo from Lake Charles, Louisiana, to an LNG plant on Canvey Island, in the southeastern UK. This proof-of-concept voyage was followed by seven additional shipments over the next year, and the era of LNG was officially inaugurated.
Today there are some 350 LNG carriers plying the seas with their cold cargo. That number may double in a decade with Qatar, Indonesia, Australia, Trinidad and even the US and Canada becoming net exporters of LNG. And now the LNG plants themselves are going to sea. 
henry.terrell@gulfpub.com
|