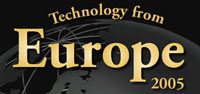 |
Belgium, Germany, Spain |
|
Enhanced production data and problem detection
One challenge for a production engineer who wants to optimize production is to obtain accurate and reliable assessment of fluid balances. This is essential to efficiently deal with detecting and anticipating problems in production facilities. Well production monitoring and optimization using water and/or gas injection further complicate the task. In subsea applications, flow assurance and avoidance of hydrate formation alone can divert substantial resources. Finally, when there are partners involved, which is often the case, accurate well allocation, including production facilities, must be determined. And of course, accurate production data must be kept.
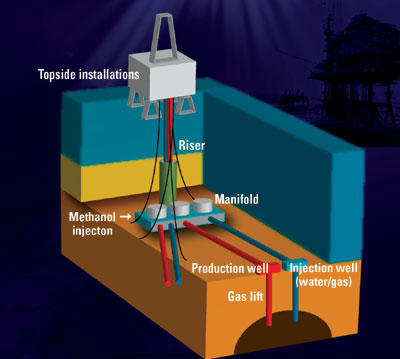 |
A small sample of some of the elements that must be taken into account to optimize production.
|
|
The traditional approach to these challenges is to design and to use a set of measuring equipment and procedures. Accuracy and reliability are critical. This approach has its limitations due to equipment characteristics, procedures difficult to implement, potential tool malfunctions, and possible fluid leakage. Three-phase metering and virtual metering have emerged, but remain a challenge, especially in deepwater subsea applications, where the repair or the replacement of equipment involves huge costs.
Belsim, a Belgium-based company, innovates by bringing its proven downstream technology to the upstream arena. By implementing advanced data validation and reconciliation techniques, the company contributes to enhancing the management of offshore oil and gas production systems, especially subsea and deepwater applications. This software technology does not require additional production hardware and can significantly assist in the design of any new systems or in the location/ setup of new or additional equipment.
In upstream systems, the following measurements are commonly used on wells: Pressure and temperature – downhole, upstream and downstream of the production (or injection) choke and tree; choke valve position; differential pressure and flowrates on the flow meter or multiphase flow meter on the dry or subsea tree.
On topside installations, the following measurements are commonly used: Pressure and temperature at numerous places (separators, pumps, compressors, etc.); liquid and gas flowrates; multiphase flow meters and various analytical data (produced water quality, injection water quality, gas dryness, etc.)
Belsim Data Validation technology uses: the above measurements and their estimated accuracy; a model to represent knowledge of the production system structure, equipment (wells, choke valves, pipes, risers, separators, etc.) and their connections; and advanced statistical methods using full accounting of material balances (compound based), energy conservation laws, thermodynamic equilibrium constraints and momentum balances. This results in a single consistent set of data representing actual process operation.
This technique – proven for several years in refineries, petrochemical plants and power plants – has been applied with success in the upstream sector. VALI is a suite of software comprising an equation-based structure that is coupled to a powerful, reliable and robust solver. It can handle even the most complex processes.
The software enables validation of the data by using redundancy in subsea and topside measurements, when available. It provides: calibration of flow meters (choke, P & T models) using other flow meters; an alarm when the difference between measured and validated values of any measurement exceeds a given threshold; a backup for multiphase flow meters, and other sensors, in case of sensor failure; flows through the entire network (wells, flow lines, risers, etc.); and estimated values for any unmeasured value. And it helps the diagnosis by detecting and quantifying water or gas breakthrough.
Practical case. The software was successfully implemented in an upstream offshore production facility on the West African coast. It validates the performance of a water injection system every day online. The application should be extended soon to the gas lift system. The company has developed the model and commissioned the system on site. The validation system has been integrated with an Oracle production historian database to extract the measured data, and is essentially used through an Excel interface.
Production engineers use the system daily to: produce accurate and coherent production balances; detect and quantify bypasses; detect and quantify water leaks; detect drifting and erroneous sensors and correct them when necessary; and compare actual water injection rates to set points and take corrective actions. The system has also been used to locate where additional counters should be placed for further improving the balance quality.
The overall project led to numerous benefits, including increased data accuracy; detection of leaks of about 2,000 tons/day of injection water, which enabled the operator to bring production back to its nominal level; optimization of water injection for a better distribution among the wells; diagnosis on equipment performance; improved maintenance scheduling and response; and better placement of new sensors. It also simplified the daily work of the reporting crew. 
|