Technology from Europe:
France
ROV/AUV concept cuts subsea IRM costs
Traditionally, inspection, repair and maintenance (IRM) of deepwater fields is performed using work ROVs deployed from DP ROV support vessels. These vessels are expensive, and they may not be available when they are needed most. In deep waters, ROVs become heavy to handle from these vessels, because of long umbilicals; and they become prone to breakdowns. Weather downtime is also an issue for ROV support vessels when working in harsh and hostile environments.
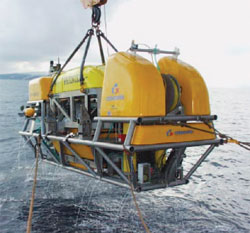 |
Swimmer ROV is transported to subsea station in AUV mode where it docks and connects to a power and control facility to complete IRM work.
|
|
The Swimmer concept, developed by Cybernetix, together with several European partners (Ifremer, Liverpool University, TotalFinaElf), and with support of the European Union, aims at reducing the costs of IRM of deepwater subsea fields while maintaining the intervention capability of the traditional work ROV. Swimmer comprises an AUV shuttle in which a work ROV is fitted (see accompanying figure). The shuttle can be deployed from a permanent surface facility (FPSO, TLP, etc.) or from a simple vessel of convenience, e.g., AHTS. After deployment, it transits in AUV mode to the subsea site.
Field umbilicals – between FPSO and subsea trees, manifolds, etc. – are equipped with an ROV power and control umbilical and when the system arrives at the subsea field, it docks into a docking station and connects the ROV to its power and control. The ROV can now be operated from the surface facility (FPSO) in real time, like a normal ROV with unlimited power supply.
Regarding technical features: 1) the shuttle has fully electrical propulsion; 2) power supply is from a high energy density battery pack; and 3) it uses a low-speed/high-reliability/long-range acoustic bi-directional telemetry system for AUV control and monitoring from the surface unit. Its long-range hybrid LBL/dead-reckoning positioning system (metric precision) provides an autonomous transit trip to the target location. The short-range sub-metric positioning system uses 3D sonar image processing for automatic docking on the subsea station. And the docking station is part of the field's permanent equipment. It is linked to the surface by an umbilical, allowing powering and real-time ROV control after wet connector mating.
The fact that the DP vessel is not needed for the ROV support makes Swimmer an economical way of doing the subsea IRM, especially considering cost savings during full field life. Swimmer, as shown in the accompanying figure, is a prototype used to demonstrate the technology. The industrial version will be more streamlined, including the latest equipment/technology developments. Oil companies are interested in the concept because of the potential cost savings. Sea trials of the first vehicle were successfully performed offshore in late 2001. 
|