Rig electrification drives down emissions, bolsters efficiency while improving onshore drilling economics
Drilling contractors have used electrical power from the utility grid for decades—most often in densely populated metropolitan areas and similarly sensitive locations, where noise ordinance restrictions precluded the use of onsite diesel engines. While using power from the grid is a simple and easily implemented solution, achieving mass field deployment and mainstream status is hampered by the lack of remote, reliable electric infrastructure and high operating costs. The logistics of moving substations from drilling pad to drilling pad and the complexity of connecting the rigs to the power source in a way that provides consistent, reliable power adds to the complexity.
Today, there are multiple drivers for changing the status quo in the drilling sector. One is technology advancement and the industry's commitment to integrating technologies that improve efficiency and streamline operations. Another is a heightened commitment to environmental and social governance (ESG) by drilling contractors and operators, in response to growing public interest in decarbonization.
The parallel goals of improving ESG performance and reliably providing affordable oil and gas energy sources make reducing emissions from drilling operations a top priority. Many new technologies, including rig electrification and power management, aim to achieve those objectives.
As companies evaluate technologies that deliver environmental and performance gains, electrification is often one of the first concepts considered. Electrification is a proven, straightforward way to lower operational costs and reduce the carbon footprint of drilling operations. When renewable fuel sources produce the utility's electricity, the environmental gains increase exponentially.
OUT WITH THE OLD, IN WITH THE NEW
Most of the equipment on a modern oil and gas rig—from top drives and draw works to control systems—is powered by electricity. Traditionally, drillers have relied on diesel-electric generators, but there are drawbacks. Using diesel generators increases operating costs and greenhouse gas (GHG) emissions. A typical high-spec drilling rig burns about 2,000 gal of diesel per day, with annual consumption of a half-million gallons or more. Replacing diesel with utility electricity reduces onsite CO2e by approximately 20 metric tons/day, depending on the region.
Retrofitting rigs to access highline power, using equipment that is easy to install and operate, can replace diesel-electric generators as the primary power source. Operations run cleaner, and they are more affordable and efficient, Table 1.
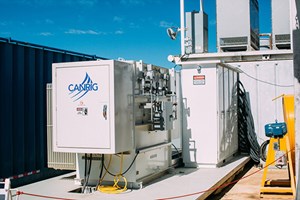
The PowerTAP™ Transformer Module by Canrig (Fig. 1)—a division of Nabors Industries—modifies the incoming highline power voltage, aligning it with the rig voltage and integrating the utility grid with the rig's powerhouse, to significantly reduce fuel usage and on-location emissions.
During a rig move, a crew installs the skid-mounted transformer module. More compact than a standard generator house, the module is positioned next to the rig's powerhouse and connected to highline power, with a medium-voltage, reel-fed cable that sits next to the utility pole, Fig. 2. Interconnected cables for the line power, generator and powerhouse connectivity are run in a cable tray or through the generator houses to the powerhouse. It is not necessary to cut or reconfigure existing cables. Minor hardware and configuration changes in the powerhouse enable the rig to recognize whether it is on highline or generator power.
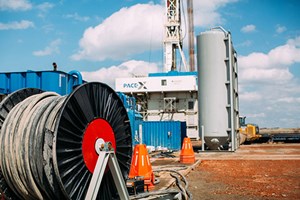
Rig move operations may require a switch to generator power, to account for timing or utility company service activation or deactivation. Additionally, there may be disruptions in the electrical utility service that—while rare—require the rig operations to switch to generator power. The substation allows the existing power generation system to remain integrated with the rig, through the PowerTAP module's electrical transfer switching system, enabling users to toggle between highline and generator power. During the project's initial deployment in 2022, using electricity as the rig's primary energy source and providing a secondary power source reduced drilling downtime and increased reliability.
FIELD VALIDATION AND ONSITE IMPLEMENTATION
Throughout its early implementation and final development, the PowerTAP module was tested and validated by Canrig, during manufacturing and field deployment, to ensure successful rig system integration. Canrig established a multi-step test, to determine the power transformer module's effectiveness and ensure it was straightforward. Canrig connected prototypes in a Magnolia, Texas, manufacturing facility to a high-voltage source, and the unit's performance was closely monitored and measured, following standard QC processes and procedures. After testing under a range of operating conditions, the unit was awarded a COC certificate of conformity and shipped to the rig site, for installation on a Nabors drilling rig.
Designed for compatibility with alternating current (AC) rigs, the first PowerTAP module installation was on a Nabors rig, in March 2022. The successful performance of the unit provided a foundation for integration by other drilling contractors, starting in August 2022.
Field implementation in real-world environments has produced compelling data, demonstrating how electrification reduces fuel consumption and emissions and lowers operating costs.
One notable installation was on a Nabors rig in West Texas, which used 20 MWh/day to 25 MWh/day of electricity. When onsite generators in this region provide power, rigs typically require 3.5 generators online over a well cycle.
Using the equation 22,500 kWh × 0.063 gal diesel fuel/kWh + 3.5 generators using 7 gallons/hour of diesel, running 24 hours a day, a rig's estimated average daily fuel consumption is approximately 2,005 gallons and equals 20.5 mt CO2e emitted daily (2,005 gallons of diesel fuel × 0.01021 mt CO2e/gal diesel).
The average CO2e/day produced, using a PowerTAP unit, depends on the utility grid's efficiency. Using the West Texas rig example—where the grid is 53% more efficient† than diesel power generators at producing energy (comparing CAT 3512C gen-sets to the Texas ERCOT Electrical Grid)—this technology can deliver an average emissions savings of roughly 10.3 mt of CO2e per day, saving approximately 2,005 gal/day of diesel.
SHOWING VALUE THROUGH COLLABORATION SUCCESS
Additional field applications of the technology have proven the PowerTAP module's value beyond Texas. Hess Corporation—which has approximately 465,000 net acres in its Bakken, North Dakota, portfolio and is a major operator in this play—recently electrified four Nabors drilling rigs, to decrease the carbon footprint of its operations.
The program aligns with the company's corporate sustainability objectives and goal to meet the world's growing energy needs in a safe, environmentally responsible, socially sensitive and profitable way.
Hess worked closely with Nabors Industries and Mountrail-Williams Electric Cooperative (MWEC) to complete this project. Canrig supplied and installed PowerTAP, to distribute utility power to the rigs. Mountrail-Williams Electric installed highline power to the well pads and assisted in making a final connection to the distribution equipment onsite.
The first step in the electrification process was to ensure grid access at the drilling site. Hess and Canrig assembled the system components in the Canrig Magnolia, Texas, manufacturing facility. Once transported to North Dakota, a team of technicians installed the unit on location. AC drilling rigs rely on four CAT 3512C generators (with a total of 4 MW of electrical capacity), to power the 2,000-hp drawworks, three 1,600-hp mud pumps and other power demands. With the PowerTAP capable of providing electrical capacity equal to 4MW from the grid, the system can support the rig's high-power requirements.
The weather was a consideration for the Bakken rigs. Unlike West Texas—where summer temperatures routinely reach 100°F (~38°C), and winter temperatures rarely dip far below freezing—North Dakota experiences more moderate summers but much colder winters, with -30 °F (-34°C) not being unusual. The design of the PowerTAP module enables reliable operation in extreme temperatures, providing the same functionality in cold and hot ambient environments.
North Dakota's winter storms and freezing temperatures can impact the utility grid's dependability. Block heaters are added to the generators, to ensure quick and easy power transfer from the grid to generators for cold start reliability, enabling them to come online quickly.
On the Hess well sites, the crew follows operating procedures, processes and drill plans developed jointly with Nabors. Familiarizing the crew with the process and ensuring the generators run as expected, in case of a disruption to grid power, helps them switch from highline power to generators. Normally, changing from one power source to another is accomplished in approximately 10 min. Power disruptions, if any, should be infrequent and have minimal impact on operational efficiency.
Over the next five years, Hess expects to reduce the greenhouse gas emissions from these rigs by approximately 50% and to reduce energy costs by nearly 70%. The company found that switching to utility power from diesel generation is attractive for a multitude of practical reasons, ranging from improved operational efficiency to emissions reduction. The change has also reduced noise that results from using diesel generators. The success of a project like this requires a robust grid, reliable power generation and strong collaboration with the local utilities to make it happen. The electrification of its Bakken drilling rigs underscores Hess’s commitment to safely producing oil and gas in an environmentally responsible and profitable way.
THE FUTURE OF RIG ELECTRIFICATION: A PROMISING OUTLOOK FOR EMISSIONS REDUCTION
Oil and gas operations account for 15% of global energy-related emissions—a situation that leading energy companies around the globe are working diligently to change. But to move toward net zero operations, the industry must have viable alternatives to burning hydrocarbons as fuel. Electrifying drilling rigs can expedite that journey.
The PowerTAP Transformer Module installations in multiple U.S. operating environments demonstrate the effectiveness of using utility grid power to decarbonize drilling operations. Grid power is a proven, practical, cost-effective, and reliable energy source that can potentially change the face of land drilling worldwide.
Although the U.S. is a major market for rig electrification today, other geographies and key oil and gas-producing countries and regions are not far behind. Argentina, Colombia and the Middle East seek to implement electrification in their resource development strategies soon. Deploying PowerTAP systems in these territories requires additional engineering and integration development work. Canrig has already developed a suitable solution for Argentina, to convert the native utility grid frequency from 50 Hz to 60 Hz, which is more commonly used by drilling rigs.
To comply with the Argentinian market requirements, Canrig added a frequency convertor module to the existing PowerTAP module, which converts the standard utility power 50-Hz frequency to the 60-Hz frequency required by the rig. As more and more markets’ electric grids develop, so does the potential to electrify rigs, increasing opportunities to meet and exceed operational sustainability goals.
- Drilling advances and where they’re headed (July 2024)
- New technology allays permanent magnet motor safety concerns, enables better ESP performance (June 2024)
- Coated continuous sucker rod lowers RRP and PCP operating costs (June 2024)
- Dawn of a new day in completions (May 2024)
- Extracting resources from the Earth’s crust using multi-stage, fraced horizontal wells: First gas, then oil, now heat (May 2024)
- Dallas Fed: Outlook improves, even as activity little changed; break-even prices increase (April 2024)