FluiDeep: An innovative subsea storage and injection solution for chemicals management
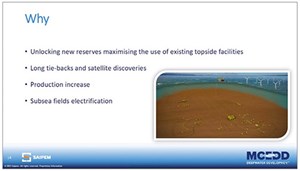
In deepwater scenarios, the expansion of an existing major field—via tie-back of satellite fields—is one of the most attractive solutions for operators. This approach to field development maximizes the use of the existing topside assets, prolongs the lifecycle of the production center and ultimately increases its production. Oil discoveries located in deep water have increased in recent years, and the opportunity to unlock the new reserves—via increasingly longer tie-backs—has become the foremost interest of the operators, Fig. 1.
THE CHALLENGE
Very often, the existing production center (e.g. FPSO) on brownfields is heavily congested, and the bearing capacity is very limited. Therefore, interfacing satellite production clusters can pose additional burden to the facility. In those scenarios, the typical outcome of the feasibility analyses shows that the additional equipment required to support the increased production is very critical and—if the tie-back had not been initially planned—it can be even a showstopper for the expansion project.
In addition to the topside concerns, the distribution of the production chemicals to the subsea consumers poses additional challenges, as the tie-back distance becomes longer. In fact, the length of the conventional umbilicals for chemical, power and control distribution is responsible for both technical and cost issues: the viscous friction of the chemical fluids, pumped through tenths of kilometers, greatly increases the pumping pressure from the topside and, consequently, increases the design pressure of the umbilical tubing and equipment, as well as the required pumping power.
On the other hand, the cost of the longer umbilical increases up to a threshold that endangers the project’s economics. In addition, longer tubes typically need larger diameters, to keep the chemical fluids friction low, with a negative impact on installation, too.
THE SOLUTION AND VALUE PROPOSITION
Saipem, an energy services contractor, has developed FLUIDEEPTM—a new solution for subsea chemical storage and injection that moves the chemicals from topside to subsea locations, close to the wells and to the other subsea users where the chemicals are needed. The chemical tubes are removed from the umbilical, as FLUIDEEPTM requires only an electrical power and communication link to the topside, providing tempting savings to tie-back development cost, thus adding value to the project.
Operators have evaluated that the contribution to the reduction of the initial investment for the tie-back development is close to 8%, with the sole adoption of subsea chemical storage and injection, and it is even more attractive for all-electric tie-back scenarios (i.e., all-electric XTs). In such contexts, the conventional hydraulic tubing, devoted to the control fluid distribution to XTs, also can be removed from the umbilical, which is then replaced by an electrical cable.
FLUIDEEPTM also can be implemented to serve subsea processing units that need chemicals provision, as well as subsea carbon capture, utilization and storage (CCUS) applications, to prevent scaling of the injection reservoir.
TECHNOLOGY HIGHLIGHTS
FLUIDEEPTM handles a large variety of production chemicals and can be deployed in deepwater projects of up to 3,000 m. Conceived around a modular design philosophy, it can be configured to form bespoke solutions to cope with a wide range of chemical volume, flowrate and injection pressure requirements.
Two subsea storage solutions have been developed: the first solution, which is common to other systems, is based on a deformable bladder for the primary barrier. In the second solution, the primary solid barrier between the chemical and sea water is replaced by a liquid layer, forming a liquid stacking tower. The pumping of chemicals is carried out by reciprocating units that can cover a dosing range, from a very low dosage rate up to thousands of liters per hour.
The underlaying power and control distribution architecture is fully redundant. The typical storage unit size is approximately 30 m³, but storage tanks can be configured as a cluster, to increase the capacity and fit the project requirement, with the appropriate refilling strategy. Refilling is based on tank change-out—i.e., the empty units are retrieved and transported onshore for refilling operations; hence, no chemicals handling is required on the vessel.
The typical storage system weight is less than 70 mT, to limit the MSV craneage requirements, thus expanding the marine spread to light vessels for the refilling interventions. The system architecture modularization is such that no injection downtime is due for tanks’ change-out operations, Fig. 3.
INDUSTRIALIZATION PROGRAM AND THE BUILDING BLOCKS
Saipem has framed the industrialization of the solution within a dedicated program that involved the construction of prototypes and the execution of a qualification campaign—dedicated to each of the key building blocks—to reach the Technology Readiness Level (TRL) 4, according to the API 17Q.
The basis of the industrialization was set following a products application range approach, aimed at standardization, to meet the future requirements of a variety of subsea projects efficiently and timely—as opposed to the conventional, project-driven development. A core part of the industrialization was to establish, qualify and secure the supply chain, through dedicated joint developments and collaborations with key industrial partners and suppliers.
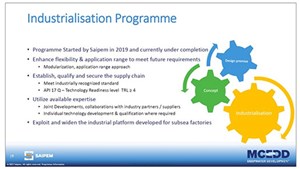
This would widen the industrial platform developed for the subsea factories’ portfolio, Fig. 4. The key building blocks included the subsea storage units, the pump and motor unit, the electrical valve actuator and the flow metering devices.
CHEMICAL STORAGE
Two different double-barrier technologies have been developed and qualified. The first solution, which is common to other systems, is based—for the primary barrier between the chemical and sea water—on a deformable bladder. In the second solution, the primary solid barrier is replaced by a liquid layer, forming a liquid stacking tower. Both solutions have been tested successfully for chemical compatibility and correct functioning, respectively, through lab testing and prototype testing.
BLADDER STORAGE SOLUTION
The bladder is typically made of elastomeric materials, and one of the primary challenges is selecting elastomers that are suitable for storing fluids. A specialized procedure for testing chemical compatibility has been developed, to perform specific tests, based on applicable international standards. The selected elastomeric materials were then qualified through a thorough testing campaign against the target chemical fluids.
The storage unit design is based on a dual-barrier principle, with an elastomeric bladder installed inside a rigid metallic vessel. The qualification plan for the equipment has been developed, according to the outcomes of the technology assessment and the results of a dedicated interdisciplinary FMECA. The plan has been mainly focused on the fabrication of a prototype bladder storage unit, to test the behavior of the whole system during simulated operations and the influence of bladder mounting configurations. The qualification of the bladder storage solution to TRL 4 was completed in first- quarter 2022.
LIQUID BARRIERS STORAGE SOLUTION
The liquid barrier storage is an unconventional solution that was conceived and qualified as part of the industrialization program. The system operates by stacking different fluids into a container, based on their specific gravity, and ensuring that mutually immiscible fluids are not in contact with each other. The barrier fluid is placed between the working chemical and the sea water, to keep them separated, while maintaining pressure boundaries and volume compensation.
A key aspect to achieve a stable barrier is the chemical compatibility among the involved liquids. The liquid barrier storage design is beneficial to the application scenarios, where large volumes of chemicals need to be deployed subsea, and the capability to scale up the tank volume provides a competitive advantage. Also, the inherently simple design makes the integration of a direct volume monitoring device easier.
A unique technology qualification plan was carried out, including: the definition of a peculiar test methodology, to select and test the liquid barriers, the execution of compatibility testing with the commercial chemicals and the fabrication and testing of a prototype unit, to test the fluid-dynamics of the system and the stability conditions for the separation interfaces between the liquids. The qualification campaign of the liquid barrier storage solution to TRL 4 was completed, with the end of the prototype testing in Q4 2021, Fig. 6.
PUMP AND MOTOR UNIT
Positive displacement pumps—which have been a proven technology for decades—are normally used for pumping chemicals on topsides. However, subsea pumping of chemicals is quite new, since most of the subsea pumps are designed to manage control fluids and are intended for temporary applications. The additional requirements brought by the subsea chemical distribution applications (e.g., a large variety of chemicals and aggressive fluids, the need to operate permanently) introduce critical elements of novelty and technological gaps.
As the candidate technology was selected, the first step of the engineering phase was to specify the power rating of the system. The pumping unit requirements were elaborated, to identify the most challenging operating conditions, in combination with possible pump configurations and characteristics. The pump design is highly modular and can be properly configured (e.g., number of pumping heads) to cope with flowrate and pressure requirements, according to the typical project needs. The qualification activities are underway and were due to be completed within third-quarter 2023, Fig. 7.
ELECTRIC ACTUATOR FOR SMALL-BORE VALVES
Process valves are required for the proper and safe functioning of the system. They need to be remotely actuated, but conventional hydraulic actuators technology was not adequate, as the control system of FLUIDEEP™ has been conceived as all-electric. No qualified commercial solution was available on the market; hence, a dedicated industrialization program was launched to bridge the gap.
The qualified actuator has the capability to operate several types of valves and features a fail-safe function, based on supercapacitors. The outline of the qualification program, which was carried out according to recognized industry standards, included the construction and qualification testing of a prototype unit that achieved TRL 4 at the beginning of 2022, according to API 17F.
FLOW METER
The chemical dosage requires precise control of the flowrate being pumped throughout the operations. This information is used to confirm that the pumped flowrate is compliant with injection requirements, to calculate the residual volume of a chemical and integrate the data set provided to the topside, for condition monitoring purposes.
A dedicated qualification program was set in place, to bridge the market gap on qualified instrumentation for low flowrate applications. The flowmeter technology was selected, based on the intended application envelope and by assessing several evaluated candidates. The most critical requirements that drove the decision were the flowrate envelope of the chemical fluids to be pumped—as well as the corresponding viscosity span—combined with the required final accuracy of the measurement.
The team focused on devices, based on positive displacement technology, which provides high-measuring performances at both very low and high flowrates and is suitable for a wide range of fluids. A prototype of the instrument was designed and built, to qualify the whole application envelope in terms of flowrate, pressure, chemical fluids to be pumped, and installation water depth. The new integrated design was also qualified, through a specific hyperbaric test at 300 bar, by means of a pressure cell, to simulate the actual ambient pressure subsea. The qualification to TRL4 was completed in first-quarter 2022.
WAY FORWARD
Subsea chemical storage and injection technology is one of the key components enabling the all-electric subsea tie-back. Development schemes based on this technology are particularly attractive, as the distance from the topside increases, because the umbilical—which is an expensive part of the infrastructure—can be simplified to reduce cost.
In addition, the system has the potential to debottleneck congested topsides, providing opportunities to unlock new reserves. The industrialization program has been conceived following a products range approach—as opposed to the conventional, project-driven development—to leverage standardization and increase delivery efficiency. Qualification of TRL 4 has been successfully achieved, setting the cornerstone for the industrial application of the first industrial pilot, to increase the TRL to 5 and 6.
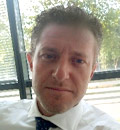
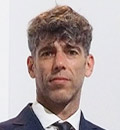
- Regional report: Guyana-Suriname: Rapid expansion of production continues (July 2024)
- Annular safety valves advance flexibility, reliability and safety in completion operations (July 2024)
- Well decommissioning: Simple solutions to complex problems (June 2024)
- Rethinking sand management for optimized production (June 2024)
- Can an offshore drilling rig run on green methanol? (May 2024)
- Custom-made blueprint for optimizing late-life assets (April 2024)