Executive viewpoint
Remanufactured parts have been part of the supply chain serving the oil and gas industry for decades. Operators have traditionally viewed the benefits of purchasing remanufactured parts and equipment from an economic perspective. Maximizing utilization helps improve total cost of ownership (TCO), and remanufactured products can play a notable part in achieving that goal. With quality control, testing and certification similar to their new counterparts, remanufactured parts are especially attractive, as they are priced competitively when the core products are returned for remanufacture and could be available faster, compared to new parts.
In recent years, I have noticed that oil and gas companies have increased their purchases of remanufactured products across all sectors. I believe this increase is driven not only by time and cost-savings but also by recognition of the sustainability benefits of remanufacturing parts. As oil and gas companies adopt business practices that can improve sustainability, participating in a circular economy through using remanufactured components is a meaningful part of building a better, more sustainable world.
What is a Circular Economy? A circular economy separates economic activity from the consumption of finite resources. It focuses on eliminating or minimizing the waste of reusable materials and resources to reduce what is sent to landfills. It keeps products and components in use for as long as possible, which remanufacturing supports. With this model, waste is reduced, and the value of the components and products is maintained.
The oil and gas industry has been an active participant in a circular economy, given its heavy use of remanufactured components. It turns out that a tactic to optimize TCO—utilizing remanufactured parts and equipment—helps the industry be more sustainable.
Remanufacturing in a sustainability-focused world. As with many industries, the emphasis on sustainability continues to grow in oil and gas. Evolving expectations of customers, investors and employees have spurred more activity to identify ways to lower greenhouse gas (GHG) emissions and decrease the amount of raw materials and energy used in business operations. The disassembly, reassembly, testing and certification of parts that re-enter the supply chain and return to the oil field with like-new quality can reduce GHG emissions, raw material consumption and energy used in the manufacturing process.
We’ve witnessed these positive outcomes within our own remanufacturing group. Cat® Reman reclaims used parts and components—known as core—and inspects, disassembles, cleans and salvages these end-of-life cores before remanufacturing and reassembling them to match the quality and performance specifications of new parts. This effort has grown in recent years to offer additional remanufactured oil and gas components to the industry, including turbochargers, advanced electronics, nozzles and injectors. When taking all the remanufactured components offered across the industries we serve into consideration, we estimate our remanufacturing process uses 65-87% less GHG emissions, 80-90% less raw materials used and 65-87% less energy used, compared to manufacturing new components.*
Predictive and preventive maintenance processes represent another way that oil and gas companies are quietly advancing sustainability. For example, high-speed data analyzed from onboard sensors on pumps can detect cavitation and valve leaks. Scheduled oil sampling can reveal excessive wear, contaminated fluids or other “unseen” issues.
Mitigating issues in the field before they occur can help prevent catastrophic failures that could severely damage equipment and require the replacement of components. Such events increase costs, as well as place a greater demand on raw materials and the energy required to manufacture parts, not to mention the GHG emissions involved in making the parts. Through extending the life of their equipment, oil and gas companies not only maximize their investments, uptimes and efficiencies, but also minimize the amount of components that could be discarded as waste. Sustainability is further enhanced when parts and components that have reached the end of their initial serviceable life are returned to the OEM for remanufacturing, and returned to the oil field once more.
Do well by doing good. We took back 140 million pounds of material in 2022, which illustrates how much of a sustainability impact remanufacturing can have. As interest in oil and gas remanufactured products grows, it’s an opportunity for the entire industry to make a collective impact on the environment—and contribute to the availability of affordable, accessible energy. Participating in a circular economy isn’t just good for business—it helps companies advance sustainability goals. Utilizing a single remanufactured component might seem insignificant; however, with the industry’s extensive global presence, it can add up to create a measurable impact.
*Cat Reman sustainability statements represent U.S. environmental impacts comparing "gate-to-gate" remanufacturing and manufacturing processes for engines and components. Based on 2018 external study of Cat engines, alternators and turbochargers. Does not include impacts elsewhere in our value chain.
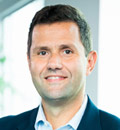