Natural gas-powered direct-drive turbines reduce GHG emissions, improve efficiency during fracing
Hydraulic fracturing has been practiced since the 1940s and has played a key role in making North America energy independent. The process, itself, has traditionally involved vast amounts of equipment powered by industrial diesel reciprocating engines to drive pumps, which inject large volumes of fluid and proppants at high rates and pressures deep underground. This process helps create targeted cracks (fractures) in low-permeability hydrocarbon-bearing reservoirs through which natural gas and oil can flow.
In North America, a conventional hydraulic fracturing fleet typically consists of 18 to 24 diesel-powered fracturing pumps and five to seven pieces of diesel-powered support equipment. Each frac fleet may consume upwards of 7 million gal of diesel annually, emitting 154 million lbs of carbon dioxide into the atmosphere.1 (Chapa, 2019).
The oil and gas industry has a history of innovation, stewardship and self-regulation. At present, increasing studies linking emissions as one of many contributing factors to climate impact, have increased the urgency for innovation that targets the reduction of fuel combustion and direct emissions. The focus on hydraulic fracturing emissions is largely centered around associated equipment and the corresponding emissions, comprised of both greenhouse gases (GHGs) and EPA-regulated pollutants.
Since 2018, BJ has devoted much of its R&D effort to developing and validating next-generation hydraulic fracturing technologies to support the industry’s transition into low carbon practice while maintaining operational efficiency and economics. The team concluded that, among all available technologies including next-generation electric fleets powered by a single large turbine, multiple small turbines, or natural gas reciprocating engines, the direct-drive turbine technology scored the highest in meeting these set objectives:
- Improvement of GHG and non-GHG emissions
- Equipment powered by natural gas, eliminating the use of diesel fuel
- Improved reliability
- Reduced equipment footprint
- Improved pad-to-pad mobility
- Reduced noise, capable of meeting the most stringent noise standards
- Reduced maintenance and personnel costs
- Competitive capital cost to compete in all market cycles.
DIRECT-DRIVE TURBINE TECHNOLOGY
The key component of the TITAN® direct-drive turbine technology is a 5,000-HHP dual-shaft direct-drive natural gas-fired turbine, capable of delivering one of the most efficient “power to pump” combinations available. Fueled by natural gas, TITAN supports the reduction of greenhouse gas emissions, reduced costs, improved mobility, and reliable operations while meeting the most stringent noise reduction requirements across North America.
The direct-drive turbine technology enables a wide variety of fuel options, including field gas, LNG, CNG, and even diesel when gas options are not available. The fleet contains “Matched Power” technology, providing BJ with ultimate control in customizing the amount of HHP rigged in on location to maximize both the pumping capability and power to reduce waste, while optimizing efficiency and fuel economy.
The industry had limited success in applying the direct-drive turbine technology to hydraulic fracturing applications in the past. Some of the technical obstacles included an unreliable turbine-to-pump power transfer mechanism, low power density, and lack of integrated engineering design. Advancements in both turbine machinery and speed reduction technology, coupled with the BJ engineering team’s in-depth understanding of operational parameters and equipment design knowledge, allowed for the successful development and validation of the direct-drive turbine technology.
The TITAN’s power train consists of a highly versatile turbine and robust, single-speed reduction gear box that connects to a 5,000-HHP continuous-duty power end, to deliver fracturing fluid and materials to the reservoir. Such arrangement provides TITAN with the highest-efficiency mechanical-to-hydraulic horsepower transfer, resulting in lower fuel consumption and greenhouse gas emissions.
EMISSION PROFILES
There are many factors that affect emissions from a hydraulic fracturing fleet, and they must all be considered to ensure an even comparison across the board. BJ Energy developed a methodology for evaluating existing and next-generation hydraulic fracturing technologies in the following manner to ensure a transparent, unbiased and factual comparison.
First, a model was developed for calculating the expected emissions released by the main types of hydraulic fracturing technologies used today. This model creates an emissions profile for each technology by considering the amount of fuel consumed, adjusted by the many engine characteristics and operating factors that come into play during a full operating cycle.
Next, comprehensive, certified third-party emissions testing was completed on the direct-drive natural gas turbine under actual operating conditions, following U.S. EPA methods. This testing also factored many engine characteristics and operating conditions that come into play during a full operating cycle.
Lastly, the emissions testing data were then compared to other hydraulic fracturing technologies in a comprehensive model to generate emissions profiles for each system during a typical day of operation. Factors within the operating cycle, such as engine idle time, pumping time, pumping pressures and rates, were based on historical data within the various basins of operation.
In April 2021, BJ Energy Solutions engaged a certified, third-party, emission testing company to complete the emission testing program in Granbury, Texas. A commercial TITAN unit was taken directly from operations without any maintenance or modifications being conducted. For the testing, a comprehensive, scientific emissions testing protocol was followed. All emissions testing was performed, using U.S. EPA methods described in the Code of Federal Regulations and in conformance with ASTM D7036, Section 15.3.15. All metering and monitoring equipment met or exceeded the uncertainty criteria contained in the testing method. Results from the testing were then inputted into the model for emissions calculations for TITAN. More detailed discussions are available for reference in BJ’s whitepaper on emissions, which is available at https://bjenergy.com/service/our-our-titan-platform/. The methodology and results also will be published in a peer-reviewed technical journal, which is in progress.
For the four different scenarios across selected basins, including the Haynesville, Permian, Eagle Ford and Montney/Duvernay, the TITAN direct-drive turbine technology demonstrated some of the best greenhouse gas emission profiles, despite the negative impacts of higher temperatures and altitudes encountered in basins, such as in the Permian. The average reduction in emissions ranges from 7.9% to 39.8%, Fig. 1.
TECHNOLOGY VALIDATION
In April 2020, BJ completed the 1,000-hr field trial of a direct-drive turbine prototype in the Haynesville, one of the most challenging basins for any hydraulic fracturing equipment. The prototype TITAN Pump met all pre-defined objectives for the field trial, including performance and reliability of the turbine and speed reduction gearbox, the use of various fuel sources (LNG, field gas, and diesel for contingency purposes), operating hours, and performance of the newly developed pump control platform. The field trial also identified several areas for improvement. Some of the areas for improvement included the power end, fluid end, turbine air intake and exhaust system, to name a few.
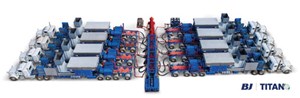
In March 2020, after finishing over 500 hrs of the prototype field trial, BJ signed a four-year contract for the first commercial TITAN fleet with Aethon Energy, for their operations in the Haynesville shale, in northern Louisiana and East Texas. The contract allowed the company to launch the direct-drive turbine technology to deliver on its commitment to reduce carbon emissions, increase operational efficiencies and improve the economics for its clients. The 40,000-HP TITAN fleet consists of eight 5,000-HP direct-drive turbine units (up to 5,500 maximum intermittent power), together with support equipment, which represents an over-25% GHG emissions reduction, compared to conventional diesel-powered pumps in the Haynesville, Fig. 2.
As of mid-December 2021, the TITAN fleet had completed more than 1,300 stages for a total of 25,000 combined pumping hours. The fleet displaced over 4 million gal of diesel by using on-site processed wellhead gas.
The company has seen increasing demand for its direct-drive-turbine technology. Since the deployment of the first commercial fleet, BJ has signed additional long-term contracts. The company now expects to have five operating TITAN fleets by the end of 2022/early 2023.
LOOKING FORWARD
BJ continues investing in R&D to optimize the power train performance of the direct-drive turbine technology, as it plans to enter basins with different operating and environmental conditions. Engineering design is well underway for concept to significantly enhance power end performance for lower pumping pressure with higher pumping rate operations.
REFERENCE
- Chapa, S., “Baker Hughes chooses Permian Basin to debut ‘electric frack’ technology,” April 30, 2019, retrieved from Houstonchronicle.com: https://www.houstonchronicle.com/business/energy/article/Baker-Hughes-chooses-Permian-Basin-to- debut-13808592.php
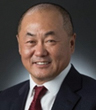
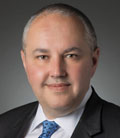
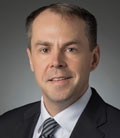
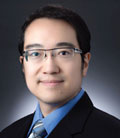
- To frac, or not to frac, that is the question (September 2024)
- U.S. drilling decreases on shale consolidation, technical advancements following record production (September 2024)
- Enhancing well efficiency through gas lift in the U.S. with qualified oilfield chemicals (August 2024)
- Frac sand’s incredible journey (July 2024)
- Annular safety valves advance flexibility, reliability and safety in completion operations (July 2024)
- Dawn of a new day in completions (May 2024)