Value driven well integrity solutions also help reduce carbon footprints
When it comes to well integrity, innovative and environmentally aware solutions should be central to the planning and successful delivery of any forward-thinking project. With an increasing need to zoom in on sustainable strategies, more companies are examining their impact on the world in which they operate, and it’s now more important for them to look at how they can do their part.
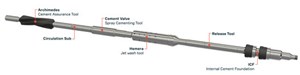
Driven by a relentless desire for technological advancement and a need to re-think existing well integrity operations, HydraWell’s team of innovators has combined its long history of technological innovation with global experience to carve out a strong track record in plug-and-abandonment (P&A) operations. The new initiative is underpinned by a well sustainability strategy and a deeper sense of responsibility. Offering smart, superior, sustainable options that exceed expectations lies at the heart of everything HydraWell does. A 98% plugging success rate means customers have confidence that environmentally conscious options can successfully combine optimum results, where they are needed, even on short notice.
As an inventive solutions provider with an environmental, social and governance (ESG) mindset fully embedded in all areas of the business, HydraWell is committed to reducing carbon footprint and waste generation, both internally and for all of its clients. A commitment to ESG best practices has been woven into corporate policies to ensure careful monitoring and improvement on performance across all technology development projects, operational performance, business activities and facilities management. The company has introduced annual improvement targets that are shared with stakeholders and encompass energy-saving initiatives, reduced travel requirements through IT upgrades, and choice of facilities to reduce its own carbon footprint.
From Stavanger to the world, the company has an in-depth understanding on how best to transform well operations by exploring new avenues and bringing to market innovative solutions. These increase efficiency and reduce environmental impact, and have the capability to reduce operating costs by millions of dollars, so it’s understandable that demand is on an upward trajectory.
PWC® SYSTEM
To achieve the objective, the company has designed, developed and tested a patented perforation, wash and cement (PWC®) portfolio for wellbore specialist applications, Fig. 1. While operators around the world are familiar with the technology and its benefits, close collaboration has facilitated significant enhancement in operational efficiency—and the identification of new applications for this flexible system which can be adapted to solve new challenges. From permanent P&A and slot recovery to restoring annulus integrity and casing show repair, HydraWell’s PWC® nimble method enables highly efficient installation of rock-to-rock barriers, Fig. 2.
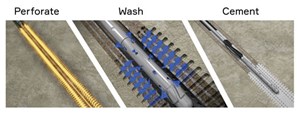
To date, more than 400 PWC® bespoke plugs have been installed for 20 operators in 14 countries. And this is just the start, as more companies seek safe, efficient, reliable and cost-effective P&A. And each barrier can be installed in as little as 36 hrs. Mark Sørheim, HydraWell Chief Executive Officer, said, “we pride ourselves on being true innovators—our forward-thinking team continually develops our range of systems in response to bespoke customer requirements to support industry challenges.”
PWC® technology offers a step-change in performance and has the potential to slash the operational sequence by up to six days when compared to the conventional section milling alternative. Based on reduced operating times of diesel-powered semi-submersible drilling units, that’s 720 MT of CO2 emissions—or the equivalent of 6 million km of car travel for every well that HydraWell’s technology helps to abandon. Furthermore, PWC® can report six-and-a-half years of LTI-free operations, and it produces zero swarf handling issues and zero metal shavings, creating a positive environmental benefit, due to the elimination of transportation needs, pollution risk and landfill capacity.
CASE STUDIES
Working with a North Sea operator, the PWC® system successfully allowed drilling to continue, thus enabling access to new reserves, avoiding costly well sidetracking and achieving the desired results within limited timeframes. Using a PWC® solution allowed the zonal isolation challenge to be solved, ten days of rig-time to be saved, and production to be delivered faster and at lower risk.
In Malaysia, a ten-well P&A campaign required shallow surface casing leak remediation to address annular integrity issues. With more than 30 successful operations in the region, HydraWell was ideally placed to provide superior technology and engineering expertise to efficiently deal with these severely corroded wells. To manage surface handling risk, due to shallow perforating tubing shock, a customized system with mechanical perforating system was used. An integrated approach to design addressed unplanned well conditions while pre-operation system tests determined operating parameters. The outcome achieved all desired abandonment objectives and saved an estimated five days per well, compared with section milling.
Another recent example of the PWC® system’s ability to increase operational efficiency was recorded in the Norwegian North Sea in April 2020, when a major oil and gas operator had scheduled a large amount of activity to plug and abandon assets. HydraWell was tasked with the project to deliver multiple isolation barriers in a single well, to meet a NORSOK-approved standard. The client had been using PWC® for years and worked together with the service company to introduce additional improvements in the delivery of isolation barriers. The project delivered record-breaking performance, resulting in savings through planning and operational excellence in challenging conditions, as well as minimizing environmental impact.
Each well required a total of four plugs across the reservoir and upper formations. Traditional section milling activities in this field have taken 10 days, on average, per isolation barrier to be installed, resulting in over 40 days of rig time for these operations. However, the historical benchmark from previous PWC® operations has been four isolation barriers installed in 23 days, when all other necessary activities where included. HydraWell’s challenge was to introduce further savings to deliver improved economics for the planned P&A scope of activity.
HydraWell had been working closely with the client for three years prior, to evolve its understanding of key operational parameters and drive down the time taken to install isolation barriers. This focused on three key areas:
- Computational fluid dynamics (CFD) modelling to aid understanding of fluid interfaces and displacements, to improve operational parameters and minimize time in hole.
- Improved system design to enhance perforating, fluid, cement and PWC®, to work together to deliver quality barriers.
- Quality assurance monitoring to determine job performance data and improve repeatability of efficiency improvements.
HydraWell’s offshore crews managing of customer and third-party suppliers to incorporate these changes incrementally resulted in a consistent improvement of operational times. In the latest well, HydraWell delivered four isolation barriers (from bridge plug installation prior to plug number one to final pressure test of plug number four) in a record breaking 8.8 days. All isolation barriers are tested and qualified, using QA processes supported by CFD and previous cement evaluation logs. This resulted in:
- Savings of $4.65 million per well versus section milling.
- Savings of $2.1 million per well versus 2015 PWC® performance.
“By harnessing PWC® technology, we are working to lower the risk of long-term environmental damage to continue our commitment to transform well operations around the world,” continued Sørheim. “We are experiencing an upward trend in companies seeking safe, efficient, reliable and cost-effective P&A, and we want to be at the forefront of delivering this technology.”
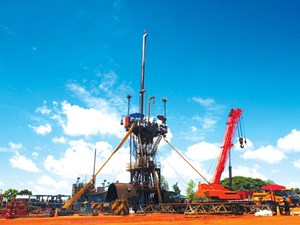
ONSHORE CASE STUDY
In an onshore continental Europe application, another major oil and gas operator implemented HydraWell technology in 2020. The client logged a successful onshore single- and dual-casing PWC® campaign from a hydraulic work-over unit (HWO), Fig. 3. The client faced a growing portfolio of mature wells reaching the ends of their lifecycles, and a substantial P&A campaign to permanently abandon these wells was undertaken. Several wells being plugged and abandoned require annular remediation and, in order to comply with internal and regulatory requirements, a rock-to-rock cement barrier is needed in the cap rocks above the reservoirs.
The biggest challenge was that several wells had insufficiently cemented annuli across the cap rock formations. The governing bodies require a rock-to-rock cement barrier across an impermeable cap rock, as close to the reservoir as practically possible. To minimize cost, the client elected to use HWO units to reduce costs, footprint and noise disturbance. However, these types of units are not readily adapted to section milling, due to torque and RPM limitations. Limitations on speed of drill pipe connection make-up, and tripping speed running singles, also increases operational time, negating the potential cost-savings from using an HWO. In addition, avoiding section milling reduces environmental impact by eliminating swarf and mud disposal, therefore reducing emissions with a shorter scope duration. The HydraWell solution commenced with three wells, which were identified as PWC® candidates, all with two casing strings in the target PWC® interval.
Downhole specifics. The first two wells were deemed to have competent barriers in place outside the second 9 5/8-in. casing string. Therefore, only the inner, 7-in. x 9 55/8-in., annulus required remediation to establish a rock-to-rock barrier. The third well required cement to be placed in both annuli and had sustained annulus pressure of ±5 bar in the 9 5/8-in. x 13 3/8-in. C annulus. Sixty meters of single casing HydraHemera PWC® barriers were placed in the 7-in. x 9 5/8-in. annuli in the first two wells. For the third well, the dual-casing HydraHemera system was run to place a cement barrier in both the 7-in. x 9 5/8-in. annulus and in the 9 5/8-in. x 12 ¼-in. open hole annulus in one operation.
For the single-casing applications, together with the client, the HydraWell team used the TCP system that would also penetrate the outer 9 5/8-in. casing. The verified barrier behind the 9 5/8-in. casing was sufficiently competent to potentially temporarily lose its integrity in the PWC® interval during execution of the washing operation. The perforation channels were filled with cement and barrier integrity restored when the PWC® operation was successfully completed.
In collaboration with four major oil and gas service providers, HydraWell flawlessly installed the first two PWC® plugs in the 7-in. x 9 5/8-in. annulus across the salt formation caprock, using the HydraHemera single-casing PWC® one-trip system. The wells were perforated over 60-m intervals and subsequently washed and cemented. Any perforation channels created in the outer casing strings were cemented in the same process, re-establishing a competent barrier in the 9 5/8-in. x 13 3/8-in. annulus.
For the third well, the dual-casing PWC® operation was successfully executed, and the sustained C-annulus pressure was cured. All three wells have since been completely abandoned successfully. “HydraWell is proud to have been key to the positive start of a long P&A campaign and strengthen the collaborative relationships between all the parties involved.”
NEW STANDARD
HydraWell welcomed good news in early 2021, as an internationally recognized set of guidelines endorsed the company’s technologies and verification process. Norway’s well integrity standard, NORSOK D-010, was updated in January, and the revised document has been well-received by regulators and operators. One of the most significant changes is a new chapter focused on defining and endorsing the PWC® process as a beneficial and sustainable method of P&A.
The question is—how can you verify the quality of the plug? This is by far the most commonly asked question. To help rectify this situation, NORSOK D-010 was updated to approve the Barrier Element Acceptance Criteria List. Verificationis extremely important, as industry regulators need to have confidence in the procedures carried out by the operators—which is where HydraWell comes in. The PWC® Qualification Matrix has been recognized as an acceptable alternative to drill out and log. For the PWC® verification process to be defined as a sufficient method for barrier acceptance criteria, in an industry-recognized standard, is highly valuable to the company, in addition to the wider energy sector. This is a win-win situation for regulators and operators alike; it ensures a widely accepted, standardized method of plug verification. The ultimate goal of the performance improvement initiative is to achieve sector-wide accelerated positive change, which will help to protect and improve the world we live in, Fig. 4. “PWC® is just one of the many ways we are working hard to fulfill HydraWell’s vision of continuing to improve our solutions, operations and approach,” Sørheim concluded.
- Coiled tubing drilling’s role in the energy transition (March 2024)
- Advancing offshore decarbonization through electrification of FPSOs (March 2024)
- Digital tool kit enhances real-time decision-making to improve drilling efficiency and performance (February 2024)
- E&P outside the U.S. maintains a disciplined pace (February 2024)
- U.S. operators reduce activity as crude prices plunge (February 2024)
- Drilling advances (January 2024)