Data-driven solutions improve oil field productivity
Eleven years ago, no one knew about smartphones; today, we can hardly imagine life without them—there are endless benefits, functions and usages. This, combined with third parties installing applications on smartphone platforms, quickly disrupted existing technologies. Many companies were left with yesterday’s products. Rapid advancements, along with development of electronic circuits, miniaturization and modifications in how we apply and use the technology, furthered this disruption.
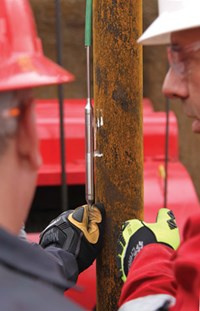
Advances in consumer electronics also benefit the oil and gas industry by allowing service companies to develop new, groundbreaking electronic-based devices. In general, advances facilitate solutions that could help meet industry challenges, such as increasing reliability at elevated temperature; improving serviceability; reducing the effects of vibration and shock; etc.
DOWNHOLE MONITORING
Since the first oil-producing well was completed, industry pioneers have invested in technologies meant to gather reliable information, in terms of the area of interest or “pay zone.” With advancing electronic technology reliability, the industry is now using multiple tools containing electronic devices. Permanent downhole monitoring sensors for a completion have become a standard requirement in most areas, because they monitor the well’s condition in real time and help increase the oil recovery rate by optimizing the oil output volume while reducing water production. Some governments mandate the use of monitoring technologies before sanctioning oil and gas development. For these permanently installed applications, reliability over time is the primary enabler.
A MORE RELIABLE METHOD
Halliburton understands that innovative technologies can create new possibilities for operators and continuously improve existing products, Fig. 1. Based on the quartz crystal measurement technology, ROC gauges demonstrate high reliability, excellent accuracy, and minimal drift at temperatures up to 160°C. The next step in this evolution is the DataSphere Permanent Monitoring suite—technologies and solutions capable of acquiring data from the entire wellbore.
Electronic components are becoming smaller and more powerful, translating to electronic devices more compact and robust with advanced capabilities. To increase reliability at higher temperatures for the DataSphere suite, the service company developed multiple application-specific integrated circuits (ASIC) and switched from ceramic to silicon capacitors. These improvements have reduced size and power consumption, and increased reliability above 160°C.
SYSTEM DESIGN
The company introduced the DataSphere Array system as the first product to use this new ASIC electronic design. It is packaged in a 5/8-in. outer diameter housing, compared to 3/4-in. for the slimmest ROC gauge. This allows these sensors to be placed in tight well constructions. As part of the manufacturing process, the sensors are connected and welded to the tubing-encased conductor (TEC) sheath at operator-selected depths along the downhole cable. This deployment method allows for an increased number of downhole sensors, providing operators with a better picture of the wellbore.
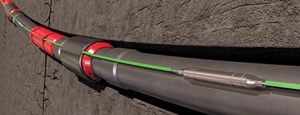
Traditionally, it has been a challenge to place more than eight pressure and temperature sensors along the completion string, because of the added rig time needed to make cable terminations and connect them to the sensor. By eliminating cable terminations and mandrels (Fig. 2), it is possible to deploy more sensors without adding to rig time. The array sensors measure pressure and temperature in the annulus space, closer to the reservoir, making it possible to combine with traditional tubing-ported ROC sensors, where needed.
Another benefit is the reduced potential HSE risks of working with trapped pressure on the rig floor. For conventional gauge installations, the gauge should either be connected using cable terminations to the TEC or to the mandrel on the rig floor, to help prevent turning the pipe after connecting to the TEC. After the appropriate connection is made, the service company should pressure-test the connection, which can take time if the temperature is declining at sunset or rising at sunrise. By eliminating these connections, the array solution removes the need to pressure-test at the rig floor; therefore, the potential HSE risk with people near a pressure test is eliminated for multiple connections while running in hole.
No special tools are associated with the array system to pick up and install on the tubing string; the operation is similar to installing regular control lines, including cross-coupling clamps (CCC). Array sensors provide an option to monitor all zones during the completion, or at multiple points in each zone. Swellpacker systems are recommended, when appropriate for well conditions, to isolate zones and help prevent any necessary splices along the completion. The system is well-suited to monitor hydraulic fracturing and works well with fiber-distributed temperature sensing (DTS) measurements. It can be deployed alongside gas lift valves in the A-annulus, used to optimize gas lift applications, and is ideal for deploying at the sand face to monitor production. Collaboration with the end-user helps ensure that the system is used to its fullest potential. Because of the small size and high resilience, sensors can be configured and delivered where needed, and in some of the most challenging wellbore regions.
ARRAY DEPLOYMENT
The DataSphere Array system is a permanent monitoring system that enables the operator to permanently deploy 50+ pressure and temperature sensors in the well. Each array provides a configurable number of discrete, real-time, annular, downhole distributed, multi-point temperature and/or pressure sensors. For multi-stage fracturing, the array can be deployed with the fiber-optic-based DTS and distributed acoustic sensing (DAS), to determine production efficiency of each stage after stimulation. Given the high resolution of the quartz crystal technology, flow backpressure and temperature data can be used in an operator’s long-term production strategy to increase recovery.
Monitoring pressure and temperature along the sand face in a subsea well could be worth up to $12 million, according to operators. The sensor array design and deployment method reduce operator cost by lowering equipment investments, because a mandrel and terminations are not needed. It also saves rig time when installing the sensors. This comes in addition to lower operational costs because of a reduced number of interventions and well surveys, and the increased production efficiency enabled by reliable, accurate well data. For deepwater applications, the array system can withstand some of the most challenging and complex offshore scenarios. It can enhance production or injection efficiency when combined with interval control valves.
The first array system was installed in a test facility at Carrollton, Texas, as part of the product qualification process. The completed objectives are as follows:
- Successfully deployed a temperature sensor array
- Verified mechanical integrity of the system, using live temperature sensors
- Replicated the size of both the temperature sensor and the pressure/temperature sensor
- Validated the installation procedure and control line protection package by maintaining communication with the array while running in hole, and while pulling out of hole
- Detected differences in temperature profile while circulating fluid, as depicted in Fig. 3
- Demonstrated system compatibility with two different sheave wheel designs
- Tested the surface acquisition equipment with the array in real time.
The test well was successful, and objectives were accomplished; thus, the system was ready for field trials. Multiple systems have been deployed for various operators, and feedback has been positive.
IMPROVED SENSORS AND VISUALIZATION
To further enhance the DataSphere suite, an ASIC electronic technology design will be launched within the Opsis sensor, which will soon replace ROC gauges and provide standard permanent monitoring with increased reliability at higher temperatures. The Opsis gauge strives for longevity and reliability at high temperatures. It will be the first Halliburton permanent downhole gauge to follow the AWES recommended practice for downhole electronics.
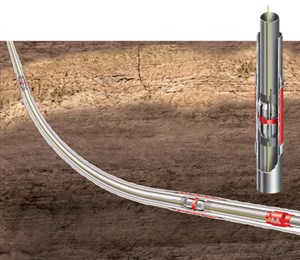
Another disruptive DataSphere suite technology is the LinX system, which allows sensors to be placed outside the casing, Fig. 4. Currently, powerful reservoir models are used to estimate reservoir pressure, based on algorithms and measured datapoints within the wellbore. Using a LinX inductive coupler to provide power to, and communicate with, quartz sensors in direct contact with the formation, allows for accurate, real-time data on well conditions. Primary areas of measurement are the reservoir, cap rock, stacked untapped reservoirs, overburden, or the B or C annuli closer to the wellhead.
DataSphere sensors pair well with the Completion Tools Voice of Oilfield visualization solution that incorporates Edge analytics to enable operators to perform comprehensive frac monitoring, and optimize production strategies in real time, to deliver immediate results. These products put data at the operator’s fingertips and in their offices. Just like the smartphone evolution, accessibility and data usage are the important pieces—what good is more data if it is difficult to work with, takes too long to decipher, or the sensors are placed in the wrong location?
The industry needs a quick, user-friendly interface with proper analysis to make sense of the data. Speed and clarity are fundamental when detecting frac hits and resolving the resulting damage. By installing array sensors in nearby wells to understand frac interference, operators can model fracture interaction across the field for more accurate forecasting and rate estimation. Additionally, long-term drawdown pressure and temperature data can be fed into the rate-transient analysis algorithms to optimize flow regimes and recommend various asset optimization techniques. Combining comprehensive frac monitoring, better rate estimation, and optimized production rate, and using drawdown monitoring with digital innovations, can decrease costs and increase ultimate recovery.
INCREASED EFFICIENCIES/ ECONOMIC BENEFITS
The DataSphere suite opens new monitoring possibilities with added economic benefit. Operators indicate that pressure and temperature readings in optimal locations will suffice for increasing long-term production. For example, before gauges were installed in cemented applications, the industry viewed in-cement monitoring as possible, only when performed with explosive charges fired after the cement set. Halliburton proved this is not necessary and that monitoring within the cement is effective in retrieving reservoir pressure data. Hence, the array system has been deployed on casing in an observation well and cemented in place to provide individual zonal pressure readings while monitoring through the cement.
This method for monitoring in cement was developed for LinX sensors behind casing monitoring applications, and the methodology has been transferred successfully to the array system. For other cases, operators can use a staircase approach to product acceptance by installing the array system behind casing in cement. Once accepted, the technology could be deployed into production wells to enhance the long-term efficiency of each well.
CONCLUSIONS
The service company continues to advance technologies that optimize production and increase overall recovery. The DataSphere suite of permanent monitoring products takes well monitoring one step further by providing accurate, reliable, and cost-effective multi-point temperature and pressure sensing. Because operators continue to push for more information from their reservoirs, these sensors may revolutionize extraction of hydrocarbons from the reservoir.
- Advancing offshore decarbonization through electrification of FPSOs (March 2024)
- Shale technology: Bayesian variable pressure decline-curve analysis for shale gas wells (March 2024)
- What's new in production (February 2024)
- Subsea technology- Corrosion monitoring: From failure to success (February 2024)
- U.S. operators reduce activity as crude prices plunge (February 2024)
- U.S. producing gas wells increase despite low prices (February 2024)