Maintaining asset integrity during hurricane season
(Editor’s note: We can think of no better time to feature this article than in the August issue, as the North American hurricane season builds to its peak in first-half September. This month also marks the one-year anniversary of vicious Hurricane Harvey, which plowed its way through the Gulf of Mexico and set all-time rainfall records in Houston and Southeast Texas.)
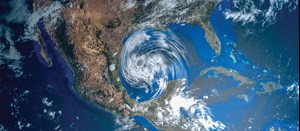
Over the past few years, the oil and gas industry has been rapidly embracing the benefits of a digital transformation. One aspect of the transformation is the emergence of digital twin models, which provide a virtual representation of physical systems that mirror the information embedded therein.
Most digital twin models for offshore floating facilities are focused on maintaining operational and inspection data. These digital twins can be linked through the life cycle of the system and allow for an unprecedented collection of asset information that reflects real-time conditions. As a subset of assorted digital twins, “simulation twins” add an additional layer of capability, by providing integrated physics-based analytical models and predicted responses, Fig. 1.
BENEFITS OF SIMULATION TWIN MODELS
Simulation twins are built on a foundation of physics-based analytical models, capable of accurately evaluating the response of a system. These physics-based models are ideal for situations where system response data are limited in terms of availability or accuracy. This scenario literally describes the reality of most floating systems. Data analytics solutions incorporating techniques, such as machine learning and artificial intelligence, can be extremely powerful, but are also inherently limited by the availability and quality of data. A highly capable simulation twin can be developed by using the foundation of physics-based models with an additional layer of data analytics to recognize the full potential of both techniques.
A perfect example of this challenge for a floating system is the difficulty in determining measured riser response. A typical riser has little-to-no instrumentation unless a particular area of concern is identified that warrants an expensive instrumentation campaign. This instrumentation, when installed, still provides coverage for only a relatively small region over the entire length of the riser. Although the measured response of the riser, itself, is typically correlated to the measured motion of the floating host facility, the correlation is only partial, and the quality of the measured motion data is often lacking. It is obvious that data analytic solutions applied to only these available, measured data will inherently be limited.
A powerful solution is to use a physics-based model to generate the responses of the entire system, based on the most reliable and accurate available data. Data analytic algorithms can then be applied to not only measured data, but also the augmented data provided by the physics-based model. In essence, a continuous cycle is developed, where the physics-based model and data analytics solutions are tied together, to provide an extremely accurate assessment of the system, as demonstrated in Fig. 2.
Obviously, a properly developed simulation twin model must accurately predict the system responses and must properly clean the measured data utilized by the model. A comparison of tendon tensions, predicted by a properly developed simulation twin and measured by a tendon monitoring system for a TLP during two hurricane events, is provided in Fig. 3. Without a proven ability to adequately clean the measured data and predict a system’s response, the benefits of a simulation twin are greatly reduced, if not eliminated completely, Fig. 4.
The accuracy and breadth of the simulation twin can be improved and optimized continually after the initial implementation. This improvement and optimization process can take the form of data analytics solutions, such as machine learning, a better understanding of the physics and assumptions utilized by the analytical engine, or expanding the simulation twin to evaluate other system components or phenomena.
For a floating system simulation twin model, the areas of concern are the floating host motions, mooring/tendon systems, riser systems, umbilicals and hull/topsides structure with appurtenances. An initial implementation may focus on a particular area of concern and may not cover the entirety of these components or systems; however, the additional items can be incorporated as the system is expanded over time.
Another aspect of the system that can be improved and optimized continually is the analytical engines and assumptions used in these engines. Every analytical model uses some level of assumptions for the practical purposes of efficiency or lack of known information. As information becomes available through the implementation of the simulation twin, these models and assumptions can be evaluated. The knowledge gained from this process can be captured and applied to the design and evaluation of other floating systems and components.
Finally, the enabling technology of a simulation twin is full automation of both the system assessment and the identification of useful insight. If labor effort is required to perform these activities, the cost-benefit of implementing the simulation twin model may be unrealized. This automation applies to all aspects of implementation: data cleaning, physics-based model assessments, data analytics, and the final presentation to the end-user of the insight generated.
The useful presentation of insight is especially important. There has been a vast amount of data collected throughout the industry over the past decades. Almost all of these data have remained unused, due primarily to a lack of the necessary technology to efficiently gather insight from the disparate data located in a myriad of different storage systems. Accessing this insight requires technology developed by a combination of subject matter experts, data analytics experts and information technology experts. This combination is needed to identify which information is truly valuable as actionable insight, and present this information to the end-users in a format that allows ease-of-use and provides sufficient information to determine the actions needed.
HURRICANE SEASON ASSET INTEGRITY MANAGEMENT
Simulation twins can provide system information, not only for real-time conditions, but also past and future conditions. These capabilities can be leveraged for many benefits, one of which is protecting the asset integrity of floating systems during hurricane events. The three primary facets that a simulation twin utilizes for hurricane event integrity management are:
- Hurricane season planning activities
- Real-time response during hurricane events
- Post event inspections and activities.
These facets all take advantage of the ability of a simulation twin to provide complete system responses, using relatively little available measured data. Even if measured data from the floating system are unavailable for a hurricane event—whether due to lack of instrumentation or lack of power to the instrumentation system during hurricane evacuation—the simulation twin can rely on other sources of data. Forecast and hind-cast data available from publicly available sources and private meteorological services can provide site-specific environmental data that can be utilized by the physics-based models. This additional layer of robustness ensures that the operator can rely on the actionable insight being generated, regardless of the level of instrumentation or data availability.
Hurricane season planning activities. Most operators rely on information generated during the design phase of a floating facility, to determine operational guidelines documented in the marine operations manual. The design phase typically considers a range of conditions meant to represent the lower and upper bounds of the facility configuration. For example, a minimum riser and maximum riser condition may be evaluated. Or a minimum topsides vertical center of gravity (VCG) and maximum topsides VCG may be evaluated. The operational guidance is then developed, based on the worst-case response of all these various conditions.
However, the as-is condition of a facility is almost never well-represented by the extreme bounding conditions. A simulation twin represents the best-known condition of the facility and can be used to determine the system response to expected environmental and operational loads. This capability can be leveraged in two manners to provide operational guidance during hurricane season:
- Evaluation of response, due to extreme event conditions, based on pre-determined metocean criteria (e.g., a 100-yr hurricane, as defined in API RP 2MET)
- Predicted response, due to named storms (e.g., using forecasted conditions of a hurricane moving into and through the Gulf of Mexico).
The operator can use the response of the as-is system to hurricane events, to optimize asset integrity management and operational plans. The response, due to pre-determined metocean criteria, can guide long-term plans, while the response for particular events will guide short-term plans. The primary benefits are derived from:
- Determining the ideal evacuation condition of the facility, to minimize strength and fatigue loading of components
- Understanding the strength and fatigue utilization of the floating system and components during hurricane events.
Evacuation procedures typically consist of activities, such as adjusting mooring line or tendon tensions; re-positioning the floating system; adjusting top-tensioned riser tensions; securing a drilling rig (mechanical lockdown); and re-ballasting or offloading equipment to maintain desired weight and VCG conditions. These procedures can be optimized, based on expected environmental conditions and as-is facility conditions, allowing only those activities that are necessary to maintain asset integrity to be performed.
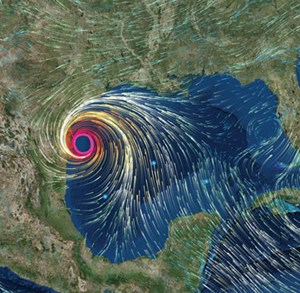
Determining which components and locations are critical, in terms of strength and fatigue utilization, is a long-term asset integrity management activity. The system response during hurricane events forms a portion of this activity. Understanding the actual utilization of components, during hurricane events experienced by the system, allows for more accurate estimations of long-term behavior. This understanding then informs the development of risk-based inspection plans and condition-based maintenance programs.
Real-time response during hurricane events. Floating systems in the Gulf of Mexico are evacuated in anticipation of named storm events, Fig. 5. Many floating systems can provide at least limited real-time instrumentation data to onshore facilities during these evacuation situations. These limited data often provide information for vessel motions, mooring line tensions and environmental data.
The simulation twin can utilize the measured data to determine the response of the floating system and all of its components (not only where instrumentation is installed). The simulation twin also can act as a “virtual sensor” to provide data where physical sensors either provide unreliable data or are completely unavailable.
For example, mooring line load cell tension data often have issues regarding quality and continuity. The “virtual sensors” provided by the simulation twin provide consistent, high-quality data along the entirety of the mooring line, and not just at the location of the physical sensor. The simulation twin can incorporate data available outside of the instrumentation system. For example, environmental data from meteorological forecasts or other weather models can supplement the measured instrumentation data.
The integrity of the floating system and its component can be inferred by comparing predicted and measured responses. Automated alarms can be established for discrepancies between predicted and measured responses, alerting personnel to issues that need to be examined with additional scrutiny. For example, if the measured pitch and roll response of a semisubmersible is significantly different than the predicted response for the measured environmental loading, this is an indication that the as-is condition does not match the condition prescribed in the evacuation procedures. Personnel can be alerted to examine the issue further and take appropriate action.
These pre-emptive alerts are in contrast to the typical methods that are based on key performance indicators (KPIs), which examine each data channel individually, in relation to a pre-set threshold rather than in a holistic view of the entire system response. This methodology cannot capture the anomalous response until after these limits have been reached, and the possibility of taking corrective actions is improbable.
Post-event inspections and activities. The third benefit of simulation twins for hurricane events is to expedite post-event inspections and activities. The simulation twin provides a real-time assessment of the response experienced by the floating system during the passage of the hurricane. This response encompasses the entirety of the floating system, including the mooring/tendon systems, riser systems, umbilicals, and hull/topsides structure.
Response of critical structural locations, such as deck-to-column connections, or events such as a mooring line breakage, can be identified. This provides the operator with a “punch list” of anomalies detected during the event, and identifies the components with the highest strength and/or fatigue utilization. This allows the operator to prioritize inspection and post-event activities. This information will be available, even before the facility is re-manned.
CONCLUSION
The digital transformation occurring in the oil and gas industry provides exciting new capabilities to improve safety and efficiency. An important piece of the transformation is simulation twins utilizing physics-based models. One specific benefit of these simulation twins is to provide a significant enhancement of floating systems asset integrity management during hurricane season.
This benefit is realized through the ability of the simulation twin to evaluate forecasted, real-time and previously measured conditions. The operator of a facility can efficiently determine the ideal evacuation conditions for a floating system, identify anomalous responses during the event, and provide an immediate post-event assessment of the floating system.
Previously, these activities were either not performed or preformed on a limited basis, due to the labor effort required. The automation of these activities greatly reduces, or even eliminates, the labor effort required to provide such extensive information. In conjunction with the ability to provide automated alerts of anomalous behavior, the operator can focus its hurricane season efforts, guided by a clear and complete picture of its assets’ integrity.
- Coiled tubing drilling’s role in the energy transition (March 2024)
- Advancing offshore decarbonization through electrification of FPSOs (March 2024)
- What's new in production (February 2024)
- Subsea technology- Corrosion monitoring: From failure to success (February 2024)
- Digital tool kit enhances real-time decision-making to improve drilling efficiency and performance (February 2024)
- E&P outside the U.S. maintains a disciplined pace (February 2024)