Technology helps provide answers for market woes
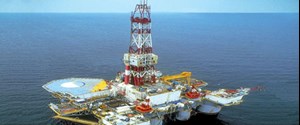
For complex rig systems, the impetus for change is felt across a full spectrum of technology, from components and processes to an entire rig design. New jackups are increasingly larger, or smaller, to better-fit niche markets; land rigs move themselves from well to well with remarkable agility. Drillers sit in ergonomic splendor, and advanced analytics provide new insights into drilling activities and efficiencies. It’s an impressive response. Here’s a sampling of the many innovations that are changing rig design, operations and economics.
ADAPTABLE JACKUPS
CDC Scotland. A pair of jackup designs from CDC Scotland Ltd, a UK design house, is offering a new take on reducing construction and operating costs. The designs are based on modular, mirror and form factor principles, to allow changes in vessel size and capacity without the cost of a major redesign. Moreover, the modules can be built and pre-outfitted at different locations for better control of construction costs and quality.
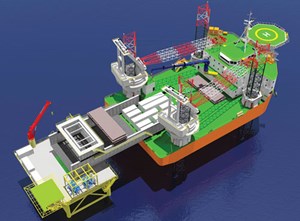
The innovative approach recently received World Oil Award nominations in two categories: Best Well Intervention (Chameleon) and Best New Horizons Idea (Heron). To date, patents have been granted in the U.S., Malaysia and Singapore. The company expects the first vessels to be available within the next 24 months. The vessels are rig-less, DP2 self-propelled jackups designed specifically for P&A, decommissioning, well servicing and well intervention. Naval architects Great Waters Maritime, Dubai, performed the drafting, analysis and modeling.
The Chameleon is configured for offshore oil and gas activities (Fig. 1), while the Heron can be configured for both oil and gas and renewables operations, Fig. 2. The vessels employ the same hull design, according to SNAME 5.5A, MODU and ABS MODU code, distinguishing them from lift boats. Heron and Chameleon versions are the same length, breadth and water depth. Both designs can house 120 people, and this can be extended by 400 beds with modular accommodations.
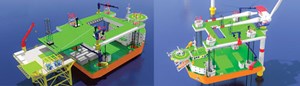
The Chameleon “Pocket MODU” is a cantilever jackup focused on a lightweight, fast in/fast out solution to a variety of activities. Its compact size and jackup capability are designed to make it a competitive alternative to existing jackups. In P&A and decommissioning activities, where CDC says only 20% of the equipment onboard a typical jackup may be used, the Chameleon design reduces costs by eliminating the need for a drilling jackup. The unit can be placed over older wellheads and platforms without adding weight or stress, while self-propulsion eliminates the need for tugboats.
General specifications provide for a vessel about 230 ft long and 137 ft wide. It has 17,728 ft2 of main deck space, and a main deck load rating up to 10 t/m2. Variants of both the Chameleon and Heron allow for a top speed of up to 10.5 knots and maximum water depth of 400 ft.
The Heron is a double-deck design for dual-industry service. Its second deck and extending platform result in up to 90% more deck space than alternative vessels. The main deck is 14,991 ft2, and the second deck adds 10, 962 ft2.
Switching between oil and gas, or renewables configurations, typically takes just a few days, involving exchange of a rig-less mast with the soft capture assembly for turbine masts, said CDC. For offshore renewables, the Heron design addresses the long-term, heavy maintenance of wind turbine nacelle components, gearboxes, generators, main hub shaft and blades. The work can be conducted in a safer “walk-to-work” environment, at height, without large cranes and hook-suspended loads subject to winds.
EXTRA-LARGE ANSWER
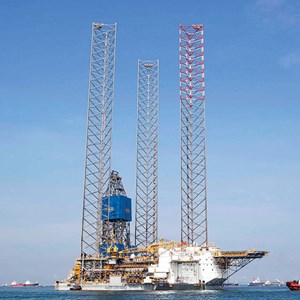
Sembcorp Marine. The world’s largest jackup rig is an ultra-high-specification, harsh environment unit delivered to Noble Corp. in July 2016, said manufacturer Sembcorp Marine. The Noble Lloyd Noble (Fig. 3), based on the GustoMSC CJ70 design and Statoil Category J specifications, is the seventh vessel completed for Noble. The rig is the first to fully comply with both Norwegian and UK regulatory standards, making it uniquely suited for operation over a very large platform or in a subsea configuration, said Sembcorp.
The rig has an operational air gap of 226 ft and can operate in a water depth of up to 492 ft, in harsh environmental conditions. Its maximum total drilling depth is approximately 33,000 ft. It was built at the Sembcorp Marine Jurong shipyard in Singapore. The rig is set for deployment at Statoil’s Mariner field development in the North Sea.
LIGHT-DUTY JACKUP
GustoMSC. The 2016 Offshore Jackup Middle East (OJME) conference in Dubai presented its Technical Innovation award for rig design to design and engineering firm GustoMSC for its light drilling jackup. The NG-3500X-LD model is the latest in the NG series, and was created to provide cost-effective, self-propelled service as a light drilling and well intervention rig for the Middle Eastern and Southeast Asian regions.
The NG-3500X-LD can operate in a water depth of up to 262 ft. The X-Y skidding system provides a large drilling envelope and additional deck space. Transverse reach with full, combined cantilever load provides more flexibility for drilling operations. GustoMSC’s NG series rigs are designed to provide a safe, stable and solid platform that allows them to remain offshore in adverse weather, along with agile maneuverability and 8-knot transit speed.
SEMI LIGHT
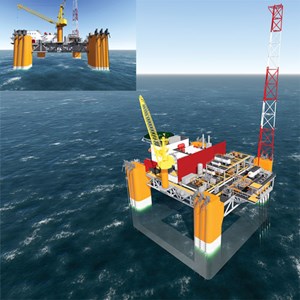
Aker Solutions. Created for harsh environments, a lighter-weight semisubmersible platform design from Aker Solutions provides a new option for developing marginal resources that are next to large fields with excess processing capacity. The new Lean Semi (Fig. 4) can help bring on stream fields that hold as much as 300 MMboe at water depths of 328 ft to 1,321 ft (100 m to 400 m). The topside weighs about 6,000 metric tons, which is 30% lighter than similar solutions, said the company. The platform incorporates elements from two proven designs to enable a 60,000-bopd production capacity at a lower investment cost. An unmanned hull, combined with a single flat top deck, provides high structural integrity. The topside is designed to use standardized equipment, allowing easy placement of equipment skids and small modules directly on the deck.
TREAD SOFTLY
Entro Industries. The latest well-to-well moving technology from rig walking experts at Entro allows the drilling rig to operate at much lower ground bearing pressures than the previous design. Their Super Stomper Walker permits multiple jack cylinders to operate over a single, large walking foot to allow the rig to operate over soft ground. It is the latest in the company’s line of King Pin Walker designs that it started in 1999. The walkers allow rig movement in any direction, and rotation in place. Entro said that its walking machines have been used on structures in excess of 12 MMlb.
WALKING TOP DRIVE
Patterson-UTI Energy announced in September that it will buy Warrior, a manufacturer of technically advanced rig components based in Calgary. Warrior is known for expertise in top drive engineering and operations. Patterson-UTI Drilling Co. is a significant innovator in walking rig technology for pad drilling applications. Its fast-moving APEX-XK walks with a full set-back of pipe in the mast, and averages 45 min. for 10–15 ft well spacing. The ability of the rig to provide full X-Y walking capabilities is designed for movement on multi-well pads.
CHINA GAS POWER
GE Power. The shift to natural gas rig power moved to China this year with GE Power’s deployment of their mobileFLEX gas engines for a drilling application. It is the first use outside the U.S., said GE. Hong Hua Group, China’s leading land rig manufacturer, commissioned three of the gas engines to power a 16,404-ft rated depth rig, drilling shale gas in Sichuan Province. The Waukesha units are being evaluated as an alternative to diesel engines, and are part of a nearly 3-MW, on-site power demonstration project between HongHua Electric, a subsidiary of HongHua Group Ltd., and rig owner Sinopec. Using the Waukesha units facilitates use of locally sourced natural gas fuel, instead of diesel that must be transported over long distances to wellsite.
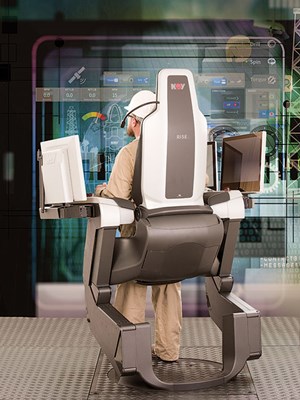
The Waukesha systems received EPA certification for mobile, non-road applications in 2013, and were used initially on rigs by Patterson-UTI Drilling. GE cited the technology’s capability to operate on a wide variety of field gases without derating the engine due to gas quality. The engines produce ultra-low emissions with a low-cost three-way catalyst, and application flexibility in altitude and temperature.
GE claims fuel cost reduction of 80%, as well as 95% lower emissions, compared to diesel. The units operate on LNG, CNG HD-5 propane, and high-BTU field gases with little treatment required. Acceptable natural gas ranges from 950 to 1,650 Btu/ft3 HHV without component changes: propane is 2,606 Btu/ft3 HHV. The systems provide flexibility in high altitudes up to 8,000 ft and temperatures up to 105°F without derating, and can be outfitted to handle greater extremes.
SITTING PRETTY
National Oilwell Varco. How’s your lower back? After a 12-hr tour cycling between monitors, controls and people, a modern driller might wonder how far we’ve really come. National Oilwell Varco intends to rectify driller fatigue with its RISE Workstation, Fig. 5. Ergonomic concerns include poor posture and position that can cause a range of problems, from lower back pain, to wrist and neck issues. For drillers performing crucial and complex tasks, there is the attendant risk that performance may affect the rig’s operation. The RISE Workstation is designed to improve driller comfort and performance by improving ergonomics in a sitting or standing position. Multiple user profiles can be stored and restored for easy individualization. The control components and layout include configurable buttons, encoder wheels and enhanced joysticks to optimize the human-machine interaction during different drilling processes.
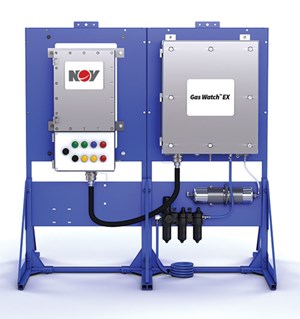
NAME THAT GAS
National Oilwell Varco. Gas trapped in drilling fluid returns can be a significant danger to drilling personnel. National Oilwell Varco’s Gas Watch EX system liberates trapped formation gases to identify dangerous gases and provide analysis, Fig. 6. The system can be used as the primary or backup gas-detection system. NOV said the patented technology and proprietary filters eliminate false readings caused by mud additives, using dual infrared (IR) sensors to read only formation gases. The sensors allow the system to distinguish light from heavy gas to support hydrocarbon characterization, while eliminating false high gas readings found typically in IR total gas systems. A hydrogen sulfide sensor can be added to improve safety. The system also can cut costs by delaying the use of mud-logging or replacement of those services with remote logging systems.
LOST AND FOUND
Baker Hughes. Understanding daily rig activity and how efficiently rig time is being spent is one of the oldest issues facing drilling operations. The answer is more than eliminating downtime, says Baker Hughes. As much as 15% of drilling time may be categorized as invisible lost time (ILT) related to drilling process inefficiencies. The company’s WellLink Performance Service is focused on understanding where those inefficiencies occur. Going beyond manual analysis of drilling records, the service uses automated operations recognition for performance analysis in real time, Fig. 7.
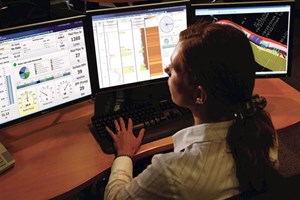
The service applies rule-based analytics to wellsite data, to provide comprehensive web-based dashboards for data interpretation and deriving root causes. It allows detection of ILT and helps resolve drilling inefficiencies quickly by comparing the data to plans and benchmarks.
With accurate real-time visibility of key performance indicators, decision-makers can look at individual rig performance and take appropriate actions to improve trip and connection times, gross ROP, and hole-conditioning times, while reducing flat-time on low-performing rigs, Fig. 8. The service also allows operational limits and controls to be set and monitored in real time, creating a closed loop to drive continuous improvement. WellLink Performance Service is part of the company’s Remote Operations Services portfolio for wellsite connectivity. It promotes real-time collaboration for faster, intelligent business decisions for efficiency and productivity.
UPS AND DOWNS
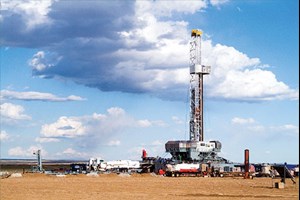
Ingersoll Rand. Safely lifting people on the rig is the focus of Ingersoll Rand’s Man Rider winches. Their latest LS2-150 model is designed for land rig applications and has a variety of features to protect personnel. An overload protection device prevents the winch from operating, if it detects a load that exceeds 125% of the 330-lb safety rating. A slack line prevention system helps prevent the rider from falling, if the winch line gets caught or snagged. The winch has two independent braking systems, and a press roller to press the wire rope onto the drum, to help prevent bird nesting. And just in case, there’s an emergency stop button.
MAKING THE CONNECTION
Weatherford. The LinkMaster tong adapter was introduced this year as a key component of Weatherford’s rig integration solutions. The adaptor provides compatibility between the company’s tongs and drilling package positioning devices for tubular running operations. In a recent application, the adapter was used to integrate a high-torque tubing tong into a jackup’s existing tubular running equipment. A 7.6-50 hydraulic tubing tong was integrated with the rig’s NOV ARN-200/270 HydraTong positioning device.
The pre-assembled adaptor and tong are installed in one lift for efficient rig-up or rig-down. To increase efficiency when running pipe of varying heights and gripping area, the adapter can be adjusted vertically to the height of the tong.
WIRELESS CEMENTING
Blackhawk Specialty Tools. A wireless top drive cement head introduced by Blackhawk eliminates the need for a hydraulic umbilical line and operating console. The fully wireless, automated Hawkeye system has been deployed for offshore and onshore operations. It features Quik-Lock connections for fast plug, dart, and ball reloads that lower rig floor downtime. An interchangeable cage in the cement head is designed to prevent deformation of dart fins, and reduce fluid bypass and displacement volume discrepancies. The cement head has a maximum hookload of 2.25 MMlb, a maximum pump rate of 35 bpm through the top drive, and a maximum operating distance of
650 ft.
Post-removal testing confirms robustness of top tension riser systems
RYAN KAVANAGH, Anadarko Petroleum and MICHAEL TRICARICO, Vallourec USA
After approximately 10 years of service in the GOM’s Green Canyon region, Anadarko decided to recover components of the top tension riser (TTR) system from the Constitution truss spar, following the abandonment of two wells in approximately 5,000 ft of water. The recovery would give Anadarko an opportunity to assess expected in-service wear that occurred on the TTRs, as well as estimate the remaining service life. Along with Vallourec providing 12¾-in. T95 pipe, the primary connector was the VAM TTR, used as the outer production riser. The first production TTR was run in 2006 and 2007.
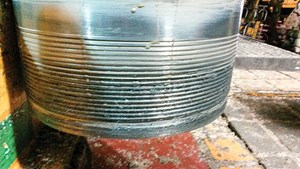
As an outer production riser, the VAM TTR is a threaded and coupled connection. It is designed to withstand the critical concerns of top tension production riser systems directly in sea water, including fatigue due to waves, heave, vortex induced vibration, surface and loop currents, in addition to water ingress into the threads, causing corrosion.
WEAR TESTING
First designed and validated in 2004, the VAM TTR incorporated these critical design requirements into fatigue enhanced threads, metal-to-metal internal and external seals, and special coupling features. Together, the two companies developed a plan to evaluate the condition of the pipe and connections after removal. The inspection methods included visual examination, wet magnetic particle, and ultrasonic assessment of the pipe and connections. The non-destructive evaluation (NDE) indicated that the pipe and connection had performed as expected, with very little wear, corrosion, or cracking in the harsh deepwater environment. One of the specific areas examined was the external seal on the connection, which was designed to keep water from entering the threads and causing corrosion. Visual inspection of the connections, during removal, showed corrosion-free connections behind the external seal, Fig. 1.
In addition to NDE, engineers decided to re-evaluate the capability of the connection by testing it to ISO13679:2002 fatigue standards. The connections were made-up again and then tested for tension, compression, internal/external pressure, bending capacity and fatigue. The analysis was similar to qualification testing performed prior to service in 2004. The equipment successfully passed the ISO13679 evaluation, meeting all requirements of CALIII testing. The tools also passed fatigue testing, showing excellent results and durability in both the pipe and connection.
This premium connection is one of the first in the world to be re-tested after being exposed to harsh conditions in the GOM. The positive results document the robustness of the provider’s threaded and coupled top tension riser systems.