Offshore in depth
The world was astounded in July 2015 by the images of Pluto transmitted 3 billion mi back to earth by NASA’s New Horizon space probe. This achievment was well beyond the capabilities of manned space flight. Though not on such a cosmic scale, the offshore oil and gas industry routinely uses unmanned, remotely operated vehicles (ROVs) to perform work in water as deep as 10,000 ft, well beyond the limits of human divers. And as ROV technology has evolved, it has replaced divers in shallower waters, enhancing safety and reducing the cost of underwater services.
Surface and saturation diving. The earliest offshore platforms were in relatively shallow water, and underwater construction and inspection activities could be carried out with surface air diving. Limited to water depths of 220 ft or less, surface divers work with air supplied by hoses from the platform or support vessel. Surface diving is still the most commonly used diving mode in the industry.
In the 1960s, as drilling extended into deeper waters, saturation diving was introduced. In saturation diving, once a project begins, divers live in a hyperbaric chamber—either on the surface or under water—between diving shifts and are decompressed to surface pressure only once at the end of their tour of duty. Saturation diving reduces the risk of decompression sickness, but also requires large diving crews and expensive support vessels. Saturation divers can work at water depths of up to 1,000 ft, but most projects are carried out in 300 ft to 500 ft of water.
ROVs for deeper water. ROVs controlled from the surface with cables were first developed for the U.S. Navy to perform deep-sea searches and to recover objects from the ocean floor. ROVs were introduced to the offshore industry as inspection vehicles in the 1970s, and by the 1980s had become essential as E&P activity extended to waters beyond the reach of human divers. Simultaneously, engineers designed platforms, subsea wellheads, umbilicals and pipelines, so they could be manipulated by ROV systems. ROVs are now utilized to help spud wells during deepwater drilling, conduct subsea construction, and carry out ongoing field inspection, maintenance and well intervention.
ROVs can decommission a subsea installation in deep water, cutting the jumpers and moving the subsea hardware so that it can be lifted to the surface.
Some divers still needed. “Diving activity is now confined to fairly shallow water,” said M. Kevin McEvoy, CEO of Oceaneering International, Inc., which was founded in 1964 as a diving services company. He said that with advancements in ROV technology, “there is a lot less saturation diving than there used to be.”
In the UK North Sea, saturation diving performs platform inspections, node cleaning and other routine tasks. In
Norway, however, because of safety concerns, “operators need special permission, even to put a diver in the water,” said McEvoy. Whenever possible, jobs there are carried out with ROVs and associated tooling, “even if it costs a bit more.”
Divers are still needed for tasks that require dexterity, like installation of floating production facility connections and hooking up pipe spools at the underwater riser hangoff for risers on production facilities.
After the series of hurricanes that struck the Gulf of Mexico from 2005 to 2008, ROVs augmented divers extensively, as they worked to clear damaged platforms. ROVs scouted the seabed, carried equipment, and placed cutting tools where divers could use them, McEvoy said. ROVs also operated cutting tools in situations where falling structures would have placed divers at risk.
New approaches for ROVs. There is an ongoing trend to replace divers with ROVs, even in shallow depths, to promote safety and reduce costs. For example, Oceaneering is developing an ROV to perform hull cleaning and inspection on FPSOs. The ROV will include cavitating nozzles to remove barnacles and other growth without damaging the paint, and also provide a wall thickness measurement on the hull. “This type of work is being carried out by diving teams of 15 people, and an ROV doing the same work could be operated by half that number, and operate more safely,” McEvoy said.
ROV systems that can operate at a 4,000-m water depth are available today, and operators continue to request technical advancements. Statoil has expressed the need for a “resident ROV” that would remain on the seafloor for a year, or more, to service a subsea field. The ROV’s tether would be plugged into a subsea panel with control lines leading to a nearby platform or shore base, and the unit could be operated from anywhere. While needed technology already exists, challenges include handling the tether without getting tangled in subsea components, and making the ROV robust enough to function for a year or more in a subsea environment.
Other technology can help projects like this, McEvoy pointed out. For example, detailed 3D models of subsea equipment, and its location and orientation, could superimpose on the video image captured by the ROV. Laser measurements and an inertial navigation system could provide precise control, in relation to subsea installations, to avoid snagging the tether.
There has been great interest in tether-less, autonomous underwater vehicles (AUV), but McEvoy considers these “developmental items.” AUVs are used to conduct surveys and military mine detection, but without a tether, data transmission is limited, and current torpedo-shaped systems can’t accommodate tools to perform actual work. There is a potential market for an AUV that could follow and inspect a subsea pipeline from beginning to end, hovering when needed to take high-resolution pictures and wall thickness readings of the pipeline, especially as systems age. Wide use of AUVs may have to wait for R&D investment, funded by higher oil prices.
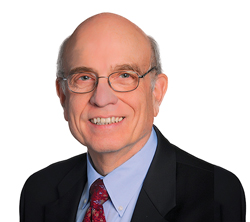