ARDIA KARNUGROHO, FIKRI IRAWAN, JULIUS SOSA and JULMAR SHAUN S. TORALDE, Weatherford
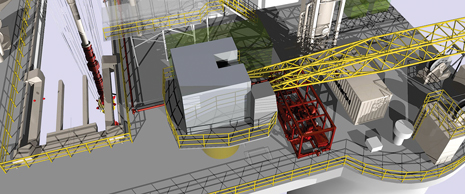 |
Managed Pressure Drilling (MPD) equipment (in red), enhances the capabilities of deepwater drilling rigs for dealing with events that might lead to well control situations, if undetected and left unchecked. Its main components are the rotating control device (RCD) that is integrated with the rig drilling riser, and the automated MPD choke manifold (at surface) that provides pressure management. |
|
Drilling difficult deepwater and high-pressure, high-temperature (HPHT) wells in Indonesia presents complex challenges that increase risk beyond what is typically experienced in most conventional wellbore construction operations. Extreme drilling environments present distinctive hazards, including riser gas (gas influxes in oil-based mud that later expand in the riser) and narrow mud weight windows (where small pressure changes during drilling could induce either a kick, or a loss), that hinder the ability to safely drill ahead.
These challenges to safety, efficiency, and reaching TD, have led to a shift from conventional drilling, to managed pressure drilling (MPD) methods and technologies. In its relatively short history, MPD has proven to be a highly effective tool in many difficult drilling applications.
With advances in methodologies and built-for-task technologies, MPD capabilities are being extended further to provide new options and solutions for deepwater and HPHT wellbore construction. In deepwater drilling, the use of MPD aboard a dynamically positioned (DP) drillship is mitigating the risks of kicks and losses, to safely and efficiently drill otherwise undrillable wells. Operating from a jackup rig, MPD methods have proved effective in HPHT conditions that feature narrow drilling windows, where conventional drilling efforts have struggled or failed.
DEEPWATER CHALLENGES
Limited pre-drill information, and the potential for severe kick/loss conditions, led to the selection of MPD to monitor and manage wellbore pressures in an Indonesian deepwater drilling program. In nine rank wildcats drilled to date, the system has successfully provided highly effective kick detection and mitigation, and managed wellbore pressures while drilling, making connections and tripping.
By identifying and controlling influxes deep in the well, MPD has also eliminated the occurrence of riser gas, which has long been a unique, and difficult, well control risk for deepwater drilling operations. In addition, the MPD system has provided formation pressures in real time, and allowed logs to be run in a safe, controlled manner.
The ability to transition between constant bottomhole pressure (CBHP) and pressurized mud cap drilling (PMCD) methods, as needed, has provided the versatility needed to specifically address the different drilling conditions presented by exploratory wells.
The use of CBHP methods enabled real-time monitoring and control for early kick/loss detection and mitigation. When drilling the first well, the system detected a 2-bbl influx that was then circulated successfully out of the wellbore, utilizing the rig well control system; in other wells, influxes as small as a single barrel have been detected. The MPD control system algorithms detected, minimized and managed at least five flow anomalies while drilling the wells.
When severe fluid losses occurred deeper in the wells, the MPD drilling mode was transitioned to PMCD, which enabled drilling with no returns, and allowed the wellbore to reach the planned TD, despite total loss of circulation.
RISER GAS MITIGATION
The elimination of riser gas occurrences when drilling these deepwater Indonesian wells is a significant achievement. Riser gas presents a long-standing well control risk that has been difficult to effectively mitigate using conventional methods.
Weatherford’s modeling of worst-case methane gas behavior shows that a gas influx entrained at depth, in an oil-based mud, typically breaks out of solution at a depth of 2,000 to 3,000 ft below the rotary table. Because this point is above the subsea BOP, which is typically 5,000 to 6,000 ft below the rotary table, gas breakout is above the BOP, and beyond conventional containment.
Standard methods of riser gas mitigation have proven less than satisfactory. The common practice is to close the BOP and vent the gas through the rig diverter system, but this typically limits control and increases the attendant risk.
In contrast, the MPD system quickly detects the gas influx downhole, while it is small. The application of annular backpressure immediately increases the equivalent circulating density (ECD), to stop and control the influx, while circulating it out of the hole. Because the influx size is small, it can be circulated safely out of the hole at high rates, instead of the slower rates and higher non-productive time (NPT) of conventional methods.
In the Indonesian wells drilled with the MPD system, there has been no incidence of formation gas breaking out of solution in the riser. Should that occur, safety protocol requires BOP closure, whether drilling conventionally, or with MPD. However, MPD methods enable a much more informed, precise response.
With the BOP closed, the MPD system quickly indicates whether the gas is above or below the subsea BOP. If the kick is below the subsea BOP, then the MPD system will no longer see it at the surface. If the gas is above the subsea BOPs, gas expansion will still be seen at the surface.
There has been only one instance recorded, similar to riser gas, when an influx was circulated out through the riser. The mitigation process began with isolating the influx by closing the subsea BOP and MPD annular BOP. Mud and the influx were circulated out through the automated MPD choke manifold, and sent to the MPD high-rate mud-gas separator.
Once the influx was circulated out of the riser, the mud system was weighted up, and the subsea BOP was opened. The well was then circulated to a higher mud weight, while applying MPD control.
PLANNING FOR DEEP WATER
For deepwater operations onboard a DP drillship, MPD deployment requires detailed planning. In addition to selection of key MPD equipment components, such as a rotating control device (RCD) and an automated MPD choke manifold, considerations may include a drillstring isolation tool (DSIT), a flow spool, a higher-volume mud-gas separator, and higher circulating rates and riser pressure capabilities. Changes may also be required to riser components, such as telescopic joints, flex/ball joints and tension rings.
In addition to equipment preparations, MPD deepwater operations also require careful definition through a stringent engineering process that describes how the MPD system will be operated to achieve well objectives.
HPHT AND NARROW WINDOWS
HPHT conditions experienced in an offshore Indonesian field had resulted in severe kick/loss conditions, and ended in several abandoned wellbores. The use of MPD mitigated the problems, and allowed the well to be drilled to TD. In addition to drilling operations, MPD was also used to develop a better understanding of pore pressure and the fracture pressure, through real-time dynamic formation integrity tests (FIT) and dynamic leak-off tests (LOT).
HPHT drilling operations in the area commonly experience a narrow mud weight window between the formation’s pore pressure and fracture gradient. In this environment, variations in BHP can heighten the risk of an underbalanced wellbore during static conditions, and the chance of fracturing the formation during dynamic conditions.
In conventional operations, staying in the window is made very difficult by limited information on downhole pressure and the delayed effect of mud weight changes. The uncertainty can result in costly kick/loss cycles, and even loss of the well.
With the MPD system, wellbore pressure fluctuations in the Indonesian well were quickly identified in both static and dynamic conditions. In response, annular backpressure was precisely manipulated to offset downhole pressure variations, and to stay within the drilling window. Accurate flow measurement was critical, to constantly monitor and identify flow differences. The measurements provided a critical real-time picture of the drilling window, as downhole hydrostatic pressure approached the fracture pressure gradient.
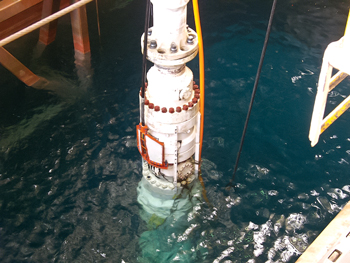 |
Fig. 1. In HPHT operations, the appropriate rotating control device and corresponding elements must be selected to effectively handle surface fluid temperatures of up to 250°F. |
|
Compared to deepwater MPD, the equipment used in HPHT operations differs primarily in the requirement that it be able to handle fluid temperatures at surface that can reach 250°F. This involves selection of the appropriate RCD elements that seal around the drill pipe, Fig. 1. Several elements are available to optimize performance, depending on the type of mud and temperature. Automated choke manifold components must also be specified for the high-temperature conditions. A surface RCD was used in the jackup application, of the type designed for high-pressure applications.
MPD operational procedures for HPHT applications are also similar to those used in deepwater MPD. A detailed engineering process was necessary, to ensure that operations were conducted safely and efficiently in drilling the Indonesian well. The MPD process focused on maintaining constant BHP conditions throughout the operations, including drilling, making connections and tripping pipe.
MPD CONTROL SOLUTIONS
The International Association of Drilling Contractors (IADC) defines MPD as “an adaptive drilling process used to precisely control the annular pressure profile throughout the wellbore.” The objectives are to ascertain the downhole pressure environment limits, and to manage the annular hydraulic pressure profile accordingly.
MPD is based on a closed-loop drilling (CLD) circulating system, versus a conventional rig system that is open to the atmosphere. The change is achieved using a few key technologies, including an RCD and an automated MPD choke manifold.
In a closed-loop system, these devices provide a real-time ability to understand and respond to minute changes in downhole pressure. Pressure changes, such as those caused by an influx, loss or ballooning, are rapidly detected and controlled in increments as small as a single barrel. Accurate fingerprinting of these pressure oscillations quickly identifies the event, which both informs an effective response, and avoids misdiagnosis that can exacerbate the condition.
Manipulating annular backpressure at the surface enables management and control of downhole pressures, while drilling, and during static conditions. A variety of specialized solutions are achieved by applying a suite of MPD methodologies that is focused on CBHP and PMCD methods, and returns flow control used in the Indonesian wells.
Building on the inherent characteristics of a CLD system, these MPD methods are providing unique solutions to many of the complex challenges present in conventional technologies and practices. This is especially true in reducing the risks and NPT associated with deepwater and HPHT drilling operations.
MPD reduces well control events and pressure-related wellbore problems by addressing two key challenges associated with conventional methods: the uncertainty of the pre-drill model, and the inflexibility of the resulting well design and mud regimes. These challenges are overcome by a dynamic capability that is counter to static pre-drill models.
Uncertainty is reduced by very precise measurements of wellbore pressure in real time. Equally important, MPD complements this information with equally precise, real-time control. This dynamic solution is the key to MPD’s success in enhancing drilling safety, efficiency and operational capabilities.
TECHNOLOGY FOR CHANGE
MPD methods are enabled by a relatively small number of core technologies. They include an RCD, which contains and redirects annular returns to create the prerequisite CLD circulation system, and an automated MPD choke manifold used to create annular backpressure and integrate the MPD system with the rig. These components have grown significantly more specialized and automated, with advanced designs and the addition of advanced monitoring, analysis and control capabilities.
Weatherford’s SeaShield Model 7875, Below-Tension-Ring (BTR) RCD was introduced to enable deepwater MPD. The device is the first RCD made up below the tension ring, and integral to the riser to support operations from DP vessels. It was used for the first time in the Indonesian deepwater exploratory drilling program.
In onshore or jackup rig deployments, where the BOP system is at the surface, the RCD is made up directly above the annular BOP. However, in deepwater operations, the RCD must be located in the riser, between the seafloor BOP and the diverter below the rig floor.
To accommodate rotation of the DP drillship, the new RCD is made up as part of the marine riser below the tension ring, about 150 ft below the rig floor. The BTR location eliminates the need for modifications to the riser’s telescoping slip joint or the rig’s mud return system. With the system in place, drilling operations can easily shift between conventional drilling and MPD methods. Because it is integral to the riser, the RCD has a tension rating similar to the riser, and meets subsea marine standards for hydraulic and electrical connections.
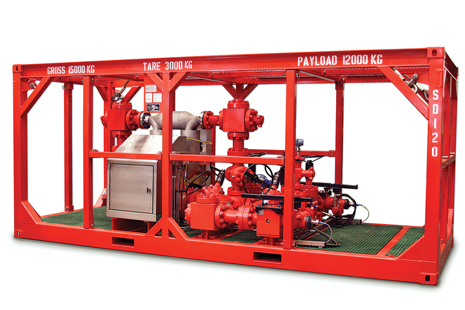 |
Fig. 2. The Microflux Control (MFC) automated MPD choke manifold manages annular pressure throughout the wellbore and in the marine riser, to keep gas in solution and prevent riser gas breakout. |
|
The other major component of the deepwater MPD system is the Microflux Control (MFC) automated MPD choke manifold, Fig. 2. The device is a 5,000-psi manifold equipped with dual chokes, and instrumented with a Coriolis mass flowmeter and precision pressure sensors. The automated MFC system manages annular pressure throughout the wellbore and in the marine riser. Its speed and precision enable an effective control response to rapid pressure oscillations that can lead to a well control event. These wellbore fluctuations typically exceed manual capabilities. Precise management of annular pressure achieved with the MFC choke also controls pressure in the marine riser, to keep gas in solution and prevent riser gas breakout.
In automatic mode, the choke manifold is operated by the MFC data acquisition and control system. The computerized system, which includes operator interfaces, databases and software, automatically executes various control processes, according to predefined parameters, including kick/loss detection, kick control and circulation, and kill-weight mud circulation. It also has the ability to execute pump ramp up/ramp down calculations during pipe connections.
Influxes and losses are detected, using comparisons of actual and predicted flows, and pressures, and trend recognition. Once a change is detected, the system executes a driller’s method response. Conventionally, this involves the application of constant BHP and two circulations—one to remove the influx and the second to kill the well. The automated MPD response circulates the influx out of the wellbore, but does not require time-consuming conventional slow circulation processes and changes in mud weight.
The system is also able to fingerprint pressure behavior during connections and pipe movements, to determine whether a kick is being swabbed, or if the well is statically underbalanced. Surge and swab pressures are easily tracked and their consequences, usually swabbing a kick or inducing a fracture, are very quickly identified and confirmed. This not only provides a more effective response, but also avoids the sometimes-significant repercussions of misdiagnosing a pressure flux and exacerbating, rather than mitigating, the situation.
PIONEERING SOLUTIONS
Through the continuous development of technology, MPD methods have advanced significantly and, today, provide new options and solutions for the extremes presented by deepwater and HPHT operations. The operations in Indonesia are pioneering the MPD applications enabled by the most recent technology advances. As the water depths increase, pressures rise and temperatures get even hotter, the successful deployment of MPD systems ensures that operations can be conducted safely and efficiently, to reach the desired target depth. 
The author
ARDIA KARNUGROHO graduated from Swiss German University in Indonesia with a BS degree in mechatronics engineering. Mr. Karnugroho started with Weatherford as a field engineer for Secure Drilling Services, and currently holds the position of Indonesia engineering coordinator.
FIKRI IRAWAN graduated from Bandung Institute of Technology in 2008, and earned an MS degree in 2010 from Universiti Teknologi Petronas, both degrees in petroleum engineering. He previously worked as an SDS field engineer for two years, and was then promoted to his current position, technical and sales engineer.
JULIUS SOSA graduated cum laude from Palawan State University in the Philippines, with a BS degree in petroleum engineering. Mr. Sosa has more than seven years of experience in managed pressure drilling (MPD), and currently holds the position of business unit manager for Secure Drilling Services in Indonesia. He previously held the positions of field engineer and senior supervisor, specializing in the MicroFlux Control (MFC) System – Automated MPD Choke Manifold. He is knowledgeable and experienced in underbalanced drilling, aerated drilling and MPD techniques, such as returns flow control (RFC), pressurized mud cap drilling (PMCD) and controlled bottomhole pressure (CBHP).
JULMAR SHAUN S. TORALDE received a BS degree in geothermal engineering from Negros Oriental State University (NORSU) in the Philippines in 1999. He is now sales manager for Asia-Pacific Secure Drilling Services at Weatherford.
|
|