NILS REIMERS and MORTEN GRANHØY-LIENG, Tomax
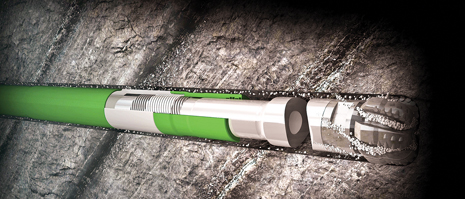 |
Tomax’s Anti-Stall Technology with its internal mechanism. The tool is typically placed on top of the non-magnetic portion of the BHA, and regulates the weight on bit, based on the level of torsion going through the tool. |
|
After completing a number of exploration wells, and making a new, promising discovery on the Norwegian Continental Shelf, one operator then set out to determine how best to mitigate the risk of significant vibration found in the Shetland Group portion of the discovery. Because the full appraisal phase on this project has yet to be completed, the names of the operator, field and wells cannot be revealed.
In the meantime, the company’s drilling engineers had already established the presence of some significant torsional vibrations, or stick-slip, repeatedly reported through the Shetland Group of sediments. In these layers of mudstone and limestone from the Cretaceous period, the vibration recordings from the downhole measurement-while-drilling (MWD) systems showed that the magnitude and duration of the problem were enough to constitute a significant risk of downhole tool failure.
Given the fact that the vibrations occurred in a formation just above the target pay, the amount of advanced logging tools in the bottomhole assembly (BHA) was often at its peak. In this situation, any electronics failures would require a bit trip for replacement to gather the required data from the pay. For the drilling itself, a drop in efficiency, and a slowdown in the rate of penetration (ROP), from the same vibrations was also suspected. With a significant number of wells in the pipeline, the operator decided to look into solutions to remove the vibrations, and the associated risk through the Shetland Group, sooner rather than later. The effort was supported by the likelihood of a need for longer, deviated wells in the development phase, where an unsolved vibration issue would not be a good starting point for timely well delivery.
ANALYSIS AND IMPLEMENTATION
The first well after the vibration challenge was presented is hereafter named “Well C.” For this well, the planning process included an evaluation of solutions that could remove or reduce the vibration issue. Well C was located between two previous wells, which for this article are named “A” and “B.” These wells were selected as reference wells. The similarity between the vibration responses through the Shetland group in the two reference wells gave good reason to believe that the same level of vibration could be expected through the Shetland Group in Well C, if nothing was done. Figure 1 shows the relative location of Well C between the two offset wells. In the same figure, the torsional vibration, or stick-slip data, from the offset wells is presented to the left. The stick-slip is expressed by the maximum downhole rotary speed variation, given in percent of the average or surface rotary speed. The risk levels are indicated in colors from green to red, with red being the most severe. Figure 2 shows the relevant, averaged rates of penetration for the same depth intervals. The color coding, itself, is provided by the MWD vendor, and is based on a combination of empirical and laboratory data.
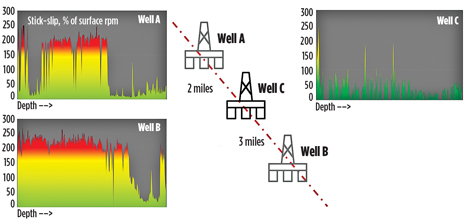 |
Fig. 1. Location and vibration data, with color coding for risk, in two offset wells (A and B), and Well C drilled with AST. |
|
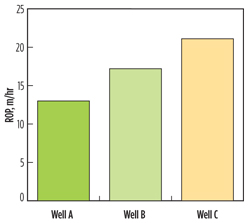 |
Fig. 2. Rate of penetration though Shetland and Cromer Knoll to core point. The runs are about the same length, and all bits are the same six-blade 16-mm cutters. |
|
The data from wells A and B both show the risk level is in the red (through the Shetland formations), and then it drops to green at the exit. The low levels of vibration seen below the Shetland in both wells indicate that the bottomhole assemblies (BHA), including the drill bits, are well-balanced, and not likely to be the source of the vibrations. For both wells, the standard practice for vibration mitigation through alternating drilling parameters was applied, without clear results.
On this basis, the operator was in need of a more profound solution to bring the vibrations out of the red, so the data were reviewed again. The data files from the MWD vibration sensors clearly indicate the strongest vibrations being in the angular or rotational direction. With this, the operator selected the Anti-Stall Technology (AST) as a suitable solution. The AST was known to the operator as a way to manage stick-slip from previous operations, some of them also in carbonates.
ANTI-STALL TECHNOLOGY
While being quite similar to a shock absorber in appearance, Tomax says its AST tool is less of an absorber, and more of a modern traction control system. All torque supplied to the bit goes through the AST, and the tool uses its internal helix mechanism to continuously regulate the weight fed, thereby adjusting the depth-of-cut at the bit, based on the torsional load.
On the basis of this working principle, Tomax claims that the AST prevents stalls and stick-slip. An illustration of the internal mechanism is used as the main illustration for this article. The tool also works the other way around, and feeds back weight, providng added depth-of-cut when the bit starts losing its cut or torsional load. Based on the latter ability, Tomax claims the tool will also optimize overall drilling efficiency. The company says it sees great potential for the AST solution in today’s operations, as it should have a nominal impact on the drilling speed, while at the same time significantly reducing the risk of costly round-trips to replace failed tools.
PLUG-AND-PLAY
The AST is presented as an autonomous, plug-and-play solution, with no added rig crew, surface equipment or changes in drilling practices. For the run in Well C, the same rig, fluids and MWD contractor, as in wells A and B, were used. The MWD contractor added the AST above the non-magnetic portion of the BHA, as recommended by Tomax. Figure 3 shows the AST tool made up in this position. With the rig and geological aspects discussed initially, the trial in Well C had a remarkably short list of factors that could affect the outcome, in terms of identifying the effect of the AST.
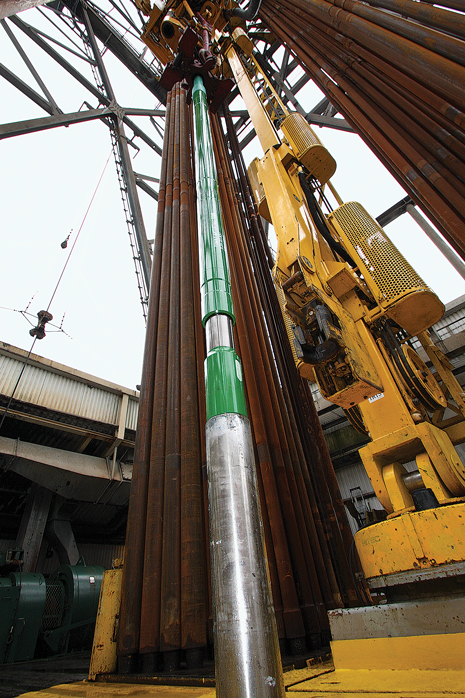 |
Fig. 3. The 6¾-in. OD AST tool made up on top of the BHA. |
|
CONCLUSION
In Well C, the results from using the AST show lower risk of tool failure and higher drilling efficiency, when comparing to offset wells. While no two wells can be identical, the conclusion is based on comparison of wells, as equal as possible, in a field operation. The operator consequently concluded that the AST will be evaluated for drilling similar formations in the future. Overlaying results are now being produced from new wells in the same program. 
ACKNOWLEDGEMENT
This article is based on an internal publication compiled by the engineers performing the planning and execution of the relevant exploration and appraisal campaign.
The author
NILS REIMERS holds a BS degree in petroleum engineering from the University of Stavanger, and serves as senior operations specialist at Tomax in Stavanger, Norway. Professionally, Reimers has a drilling and technology management background from Baker Hughes and, later, Aker Solutions.
MORTEN GRANHØY-LIENG holds an MS degree in petroleum engineering from the University of Stavanger, and serves as V.P. of Operations at Tomax in Stavanger, Norway. Professionally, he has an operations and sales background at DBS Security and Halliburton. |
|