SATERIA SULAIMAN, RENE JANSEN and MANISH KUMAR, Brunei Shell Petroleum; RAYMOND TIBBLES, NICHOLAS MOSES, AMIRUL NORDIN and SAMYAK JAIN, Schlumberger; JOE ALEXANDER
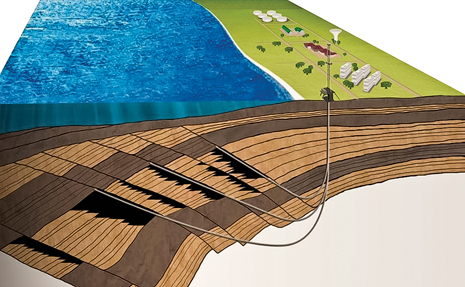 |
Welltec‘s Well Cutter electric-line intervention tool uses grinding pads made of a metal matrix composite with embedded diamonds. |
|
Innovative ideas and improvements to existing technologies are extending the ability to develop prospects in shallow waters from onshore drilling locations following the world’s first two successful shunt-tube, uphill gravel packs in fishhook wells. Drilled from surface locations on land in Brunei with subsea locations offshore, these uphill gravel pack completions, incorporating shunt-tube technology, improve recovery and extend the fishhook completion technique to wells with critical well trajectories.
SERIA FIELD
After more than 80 years of production, Seria field, extending 25 km along the coast of Brunei, is still yielding new oil discoveries, with more than 900 wells drilled and cumulative oil production exceeding 1.1 billion bbl. In 2004, new oil was discovered just under the shallow marine surf zone on the northern flank, called the Seria North Flank (SNF) area. These marginal targets are uneconomical when drilled from offshore, so drilling and completion was conducted from onshore beach locations using fishhook (FH) well technologies to allow commercial exploitation.
Since 2007, more than 50 FH wells have been drilled. Wells with inclinations less than 120° have been gravel packed using the reverse port gravel packing (RPGP) technique, a special tool setup that allows slurry to be pumped from the toe of the completion for gravel placement from the toe to the heel of the open hole.
DEPO WELL DEVELOPMENT
With the successful completion of the SNF wells, the Darat Early Production Opportunity (DEPO) Phase 1 kicked off in early 2009. Other offshore targets that hug the Seria coastline were identified and developed in August 2010, using existing onshore infrastructure for early production.
The focus of DEPO is the blocks in the offshore Anduki area shown in Fig. 1, as Cluster B and Cluster C, targeting 14 individual blocks. In the DEPO prospects, well targets became more challenging, pushing the well inclination up to 141°, with longer openhole intervals and some with shallow true vertical depth (TVD) of about 400 m, to optimally develop the field. All the SNF wells were drilled at well deviations less than 119°, and the RPGP technique was successfully applied in wells up to 115° of inclination.
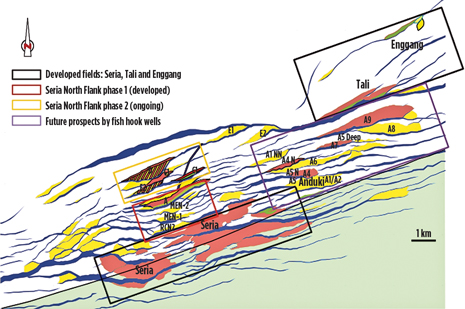 |
Fig. 1. Seria North Flank overview |
|
The DEPO project was projected to add early production from the mature Seria oil field. The thin sand-shale stacked reservoir accumulations are in fault-dip closures, near shore in water depths of 5 m or less, and are accessible from a land beach location. Successfully completed wells are tied into existing infrastructure for immediate production.
The DEPO wells required longer openhole intervals. At least seven wells required deviation angles greater than 120°, which posed a technical challenge of ensuring 100% annular pack of the pre-completion. Past experience in gravel packing intervals in the 50°–60° deviation range in various fields in Brunei demonstrated a low success rate in achieving a full pack using the standard completion techniques.
Four of the wells in Phase 1 were selected for evaluation of openhole gravel pack (OHGP) technologies appropriate for the higher deviation angle wells above 120°, two of which utilized shunt tubes. The requirements for the pre-completion were primarily full annular packing along the screen interval and secondarily annular zonal segmentation. Inflow control valves (ICVs) were to be placed inside the screen base pipe to allow selective production.
GRAVEL PACK COMPLETIONS
Drivers for screen pre-completion methodology. Based on previous gravel packing experiences in conventional wells and the fishhook SNF wells, there was a high degree of confidence in obtaining good annular packs in wells with deviations below 120° and above 130°. There was, however, a degree of uncertainty for the wells in the 120°-130° zone.
For the trials, Wells #2 and #4 would be gravel packed using screen with shunt tubes to ensure full annular packing. Reservoir management of the fishhook wells required intelligent completions with zonal segmentation of the screen pre-completion.
Oil-swellable packers with shunt tubes were used with the shunted screen to achieve a gravel pack with segmentation in the open hole for zonal segregation. The success of these marginal prospects depended on high productivity of the wells through low-skin completions. Carrier fluid selection, drilling fluid filtercake removal and all other fluids were given importance. A front end engineering design (FEED) was initiated as a starting point for an in-depth discussion of the pre-completion, using the screen with shunt tubes. Several challenges were identified, with solutions proposed using both existing proven technologies and new technologies, in addition to innovative ideas applied for the first time.
Pre-completion design. The main components of the pre-completion and the workstring included:
A 5½-in. 2AF x 2AP horizontal eccentric wire wrap screen, commonly used for OHGPs. The 5½-in. base pipe enabled intelligent completions to be run inside the screen pre-completions.
A gravel pack (GP) packer set in an “upside down” position. This system was used previously in fishhook wells with deviations less than 100°. Typically, brass balls are used for packer setting in conventional wells to ensure the heavy ball drops to the bottom easily. For an uphill well, a much lighter Bakelite ball was used to ease the path of the ball to the ball seat. The packer setting operation was simulated in a yard test by pumping the Bakelite ball uphill to a GP packer assembly held at various angles between 120°-160°.
An off-the-shelf item (wash-down module with a ball retaining feature) used for a different application in OHGP treatments in West Africa, to ensure that the ball remained seated and did not fall back down into the string.
An 8.4-in. outside diameter (OD) oil swellable packer with shunt tubes (APS), located inside the casing above the top of the screen to have a bottom for the pack and to encourage heel-to-toe (or bottoms up) packing from inside the casing shoe.
Similar Alternate Path* System (APS) swellable packers with a smaller OD (8¼-in.), soaked in a diesel-based accelerating medium for 15 hr, located in the pre-completion string for zonal segregation of the 8½-in. openhole interval. The medium allowed the elastomer OD to swell to 8½-in. prior to gravel packing, which prevented the pack from sliding downhill during gravel packing.
Quasi Alternate Path (AP) blanks—a blank section with one of the packing tubes converted into a leakoff tube—placed adjacent to each APS packer to aid the APS swell packer in segmenting the open hole.
Diverter valves to short-circuit the wash pipe at various locations in the completion to avoid exceeding the fracture gradient. Diverter valves allow wash-down capability, while shortening the path for fluid returns during gravel packing, thus reducing the pressure experienced at the casing shoe. For the DEPO wells, three diverter valves were used on the 3½-in. washpipe string.
Fluids. A viscoelastic surfactant-based system (VES) was chosen as the optimum fluid for the fishhook APS completions after examining friction properties and gravel suspension at low shear rates. Additional considerations were shear recovery of fluid, cleanliness of fluids, and simple and easy mixing “on the fly.”
For this uphill, heel-to-toe gravel packing, the fast swell packers were allowed to swell prior to gravel packing. Swell was achieved by spotting the accelerating fluid across the swell packers for 15 hr. The fluid used was diesel-based with a 10% mutual solvent. Being a fishhook well, the lighter density diesel fluid did not pose any well control risk when spotted in the open hole.
For filtercake dissolution, a slow reacting solution for removing the starch and CaCO3 components of filtercake was spotted inside the screen and allowed to soak. This solution has been successfully applied in both sandstone and carbonate formations with good results. Laboratory filtercake dissolution rates of the fluid designed for these fishhook wells were 86% and 90% after 72 hr (three days) and 96 hr (four days), respectively.
GRAVEL PACK PUMPING DESIGN
Due to the uniqueness of the fishhook well OHGPs and the use of diverter valves, the standard numerical simulator could not be used on its own. Instead, the simulator was used as a preprocessor, and then augmented with a spreadsheet simulator for predicting surface and downhole pressures.
The simulator is divided into three modules. First, the volumetric and hydrostatic pressure calculations are completed for each segment. In the second module, the friction pressures are determined. These pressures are calculated for various flow configurations in the well, using existing information from a database consisting of test data and downhole gauge data. The bottomhole pressure (BHP) data obtained from the first fishhook well (Well #2) were used to revise the model for a reasonably accurate simulation of the second job, Well #4, where the simulation matched the actual job pressure.
The job execution went as planned, and screen out was achieved. Screen-out pressure allowed the estimation of the openhole size. Packing of the entire screen interval was clearly observed in both wells. The pumping schedule for the Well #2 appears in Table 1, while treatment summary is shown in Table 2.
Table 1. Pumping schedule for Well #2 |
height="580" width="790," scrollbars="yes," resizable="yes,">
|
Table 2. Treatment summary for well #2 |
|
POST-TREATMENT ANALYSIS
One design objective for Well #4 was to initiate heel-to-toe packing to minimize the chance of bridge movement or sliding. To promote this action, diverter valves and swell packers were placed at various points in the completion. The diverter valves were designed to short-circuit the wash pipe and allow packing to begin at the heel, Fig. 2. If heel-to-toe packing occurs, the distance the fluid travels down the shunt tubes and the corresponding friction in the shunt tubes will increase linearly, as long as the OH diameter and pumping rate remain constant.
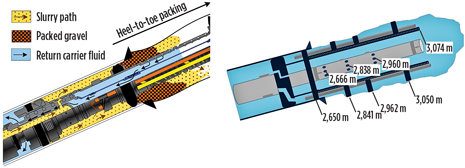 |
Fig. 2. The gravel pack design used heel-to-toe packing with diverter valves and swell packers to minimize the chance of bridge movement or sliding. |
|
Once packing begins (gravel arrival at the screens), the pressure increases linearly until about 354 bbl, when the screens are completely covered. This is a relatively simple means for tracking the pack from the heel to the toe. Another method for tracking the pack is to look at the evolution of differential pressures between the various gauges. This differential pressure represents changes in friction pressure that occur as the pack proceeds from the heel to the toe.
OH DIAMETER AND PACK PROGRESSION ESTIMATES
Figure 3 shows a plot of the differential pressures, with the x-axis as the only estimated location of the pack leading edge. The calculation of the pack front is based on an assumed openhole diameter of 8.7 in. The plot shows the locations of the diverter valves (dashed yellow lines) in addition to the pressure differentials. Note that the last dashed line is the approximate end of the screens. The pressure trends mentioned previously match up very well with the diverter valve locations and the end of the screens.
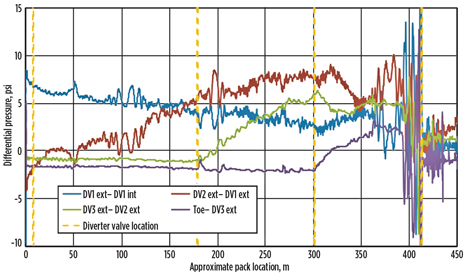 |
Fig. 3. Plot of differential pressure vs. pack location shows progress of the heel-to-toe packing. |
|
In summary, operational objectives of the OHGP were achieved. The bottomhole pressure during the job was very low and well below the fracture pressure at the casing shoe. The minimum fracture margin was about 550 psi. Heel-to-toe packing was achieved as per plan. Establishing flow through the successive diverter valves was also achieved. Calculated friction pressures indicated that similar jobs can be completed with screen intervals up to 1,600 m.
WELL PERFORMANCE
At publication time, Well #2 had been flowing for over 26 months at a stable and expected rate without sand production. Well #4 had also been producing sand-free at expected rates for more than 20 months. Subsequently, seven more fishhook wells have been completed using this technique.
Several innovative new ideas and improvements to existing technologies were applied in this uphill gravel packing of fishhook wells. These successful OHGPs extend the application range of fishhook completion technologies in wells with critical deviations that previously were not attempted. This capability extends the ability to develop hydrocarbon prospects in shallow waters from onshore drilling locations.
Diverter valves were introduced successfully for the first time in long, measured-depth, shallow-TVD wells, and gravel packing was achieved well below the fracture pressure margin. With the effectiveness of diverter valves, combined with the low-friction pressures attainable with VES fluids, it is now possible to gravel pack similar fishhook wells through shunt tubes for openhole intervals up to 1,600 m. The use of fast-swell elastomers and pre-swelling of swell packers prior to gravel packing enabled more effective zonal segmentation in fishhook wells in the 120°-130° deviation range than could be achieved with other methods.
The ideas applied successfully in these OHGPs have other applications in conventional wells. In one such case, a completion was installed with stand-alone screens in the lower two zones, with the top zone gravel packed in a single trip using a diverter valve. APS swell packers, fast-swell elastomers, and weighted accelerating fluids can be used in multi-zone, stand-alone screen/ICD and OHGP completions, where the zone to be gravel packed is not the uppermost zone.
CONCLUSIONS
Fishhook wells continue to be an important well design for Seria North Flank. An alternative method for gravel packing fishhook wells has been developed and successfully tested in two different wells. This method uses conventional service tool configurations and results in very low friction pressure during the treatment, making it applicable to wells with narrow frac/pore-pressure windows. Downhole pressure gauges provided valuable information for understanding the packing mechanism and fine-tuning the designs. Analysis of the gauge data provided the confirmation of a complete annular pack and confirmed that the packers did swell, as per plan. 
*Mark of Exxon Mobil; technology licensed exclusively to Schlumberger.
The author
SATERIA SULAIMAN is a production technologist for SWA Main field at Brunei Shell Petroleum (BSP). He graduated with degrees in mechanical engineering from Nottingham University, UK. He has been a member of the BSP Production Technologist team since 2005.
RENE JANSEN is a development lead at a large oil and gas field in Brunei. Mr. Jansen received an MS degree in petroleum engineering from the Delft Technical University. In 2000, he joined Schlumberger as a completions engineer in Nigeria, and subsequently worked in Mexico and New Orleans. In 2007, he joined BSP as the head of Completions.
MANISH KUMAR is currently the rig superintendent for a HTHP jackup rig working for BSP. Mr. Kumar graduated with an MS degree in petroleum technology from Curtin University, Australia, and an MS degree in well engineering from Robert Gordon University, UK. He has worked for Shell since 2003.
RAYMOND TIBBLES is an adviser for Schlumberger in Kuala Lumpur. He is an SPE distinguished member, who holds a BS degree in chemical engineering from Michigan Technological Institute. He has spent his 33-year career working for Schlumberger in sand control and stimulation in various positions around the world.
NICHOLAS MOSES is a Sand Management Services engineer for Schlumberger in Brunei. Mr. Moses graduated with a BS degree from University Tenaga Nasional (UNITEN), Malaysia, and has been part of Schlumberger Well Services since July 2007.
AMIRUL NORDIN is a sandface completion technical engineer in Kuala Lumpur. In 2007, he received his BS degree in mechanical engineering from University Tenaga Nasional (UNITEN), Malaysia.
SAMYAK JAIN is a senior engineer with Schlumberger based in Brunei, working primarily on sand control applications. He graduated with a MS degree in petroleum engineering from the University of Oklahoma, and has been working for more than 10 years in sand control and stimulation.
JOE ALEXANDER graduated with a BT degree in mechanical engineering from the Loughborough University of Technology, UK. Mr. Alexander worked for Schlumberger worldwide between 1981 and 2011 in the Completions and Well Services segment. He is currently consulting for Cairn India in Rajasthan.
|
|