In situ technology offers hope for better economic and environmental performance. High oil prices and government programs help.
Perry A. Fischer, Editor
Oil shale has been under development in the US since about 1900. The government established the US Naval Oil Shale Reserve in 1912. Since then, billions of dollars and millions of barrels of shale oil have been produced. Over the last century, periods of high oil prices and fears of oil shortage, followed by low prices and abundant oil, have caused a yo-yo effect on both public and private support of oil shale. With today’s very high prices, interest has once again surged.
In June 2005, the Bureau of Land Management (BLM) announced a program called RD&D that allowed companies or individuals to lease 160-acre tracts of BLM-managed land for a period of up to 10 years, the purpose of which was research, development and demonstration (RD&D) of oil shale recovery technologies. After successful completion of the required paperwork, six applicants were each awarded a 160-acre lease, with the potential to extend the lease for another five years. If R&D efforts are successful, each leaseholder will be given the opportunity to expand its lease to 5,120 acres, thus transitioning to commercial-scale operations.
In June 2007, the US Department of Energy published Secure Fuels from Domestic Resources: The Continuing Evolution of America’s Oil Shale and Tar Sands Industries, in which 27 companies were profiled that were active in R&D for oil shale development. This article draws on that report and other federal documents, as well as providing an update on the progress of some of these technologies. Rather than delve into the chemistry of the various surface mining retort schemes, I’ve limited the scope to just those eight technologies that are true in situ recovery processes.
BACKGROUND
Oil shale is a fine-grained sedimentary rock. It contains geothermally immature organic matter, called kerogen, that will yield substantial amounts of refinery input-grade liquid hydrocarbons and combustible gas when destructively distilled. An oil shale deposit having economic potential is generally at, or near, the surface, enabling development by open-cast or conventional underground mining, or by in situ methods. Oil shale is typically retorted, that is, heated in the absence of oxygen, to extract the hydrocarbons. On the surface, this is done in a large, sealed vessel. Underground, the retorting occurs in void spaces, and often results in upgrading the kerogen into valuable liquids and gases in the process.
Brazil and China currently produce significant quantities of hydrocarbon liquids from oil shale, while Estonia crushes it and burns it directly as fuel for its most valuable export commodity, electricity.
The US has the lion’s share of this shale in both quantity and quality, with some 2.0 trillion barrels. The largest known deposit in the world is the Green River oil shale in Colorado, Wyoming and Utah, Fig. 1. It contains an estimated 1.2 trillion US barrels in situ, and is one of the highest-quality oil shales in the world.
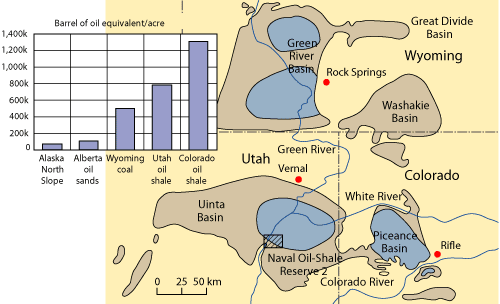 |
Fig. 1. Green River, Uinta, Pisceance and Washakie Basins comprise the major deposits of the kerogen-rich Green River Formation. For comparison, the inset shows barrels of oil equivalent/acre for various resources.2
|
|
POTENTIAL PROBLEMS
Some development issues are obvious, such as creating yet another boom mining town with thousands of people in an area that might not have the resources, especially water and power, to support it. Other problems are not so obvious, and not so easily overcome. Based on published reports on Shell’s in situ technologies, that company’s method requires about 1,200 MW of power for every 100,000 bbl of shale oil produced.1 Of course, if the necessary heat were supplied by something other than electricity, such as natural gas or gas produced by the process itself, the required electricity would be much less.
The amount of water used in the in situ process is hoped to be less than that used in surface processes, but still might be 1 to 3 barrels of water for every barrel of shale oil produced.1 More difficult is the potential for groundwater contamination, which could be the Achille’s heel for in situ processes. As groundwater levels rebound to their original condition after in situ operations cease, residual hydrocarbons and inorganics in rocks, and any chemicals used in the subsurface to enhance recovery, may be leached by the groundwater. Such leaching could be made worse due to the reduced volume of rock, now that the kerogen has been removed, and any vertical fracturing that might occur. This would allow the vertical flow of groundwater between previously isolated aquifers and could create a potential contaminant source that may affect groundwater and hydrologically connected seeps, springs and surface water bodies.3
No wellbore-related process has 100% recovery, and even if it did, leaching of residual contaminant into groundwater could be difficult to overcome. Laboratory work suggests that the use of CO2 for in situ retorting reduces the formation of base-forming (alkaline) materials.3 But most of these processes do not envision using CO2.
THE PLAYERS
The following nine companies are actively working on technology that might succeed in becoming commercial. They all use a true in situ recovery process.
Chevron USA subsidiary Chevron Shale Oil Co. was awarded a 160-acre R&D lease by the US Bureau of Land Management-tract T3S R97W Sec5 in Rio Blanco County, Colorado. The company plans to resume in situ development if its oil shale extraction technology. The possibility exists for commercial development, but the technology must be proven-and oil prices need to stabilize. Chevron’s Recovery and Upgrading of SHale oil (CRUSH) process is a true in situ conversion process that requires fracturing the shale into rubble using somewhat conventional fracturing processes and CO2 as the fracturing fluid. The CO2 might alternate between hot and cold to enhance the fracturing. This increases the surface area of the exposed kerogen. The hope is that the fractures will mostly be horizontal, and the fracture zone will remain with a minimum 200-ft layer of oil shale.4 Heat is applied to the rubblized shale by circulating hot gas or air to convert it into liquid hydrocarbons and gas. The hydrocarbon fluids are recovered through boreholes and upgraded at refineries. As many as 20 groundwater monitoring wells will be drilled, Fig. 2.
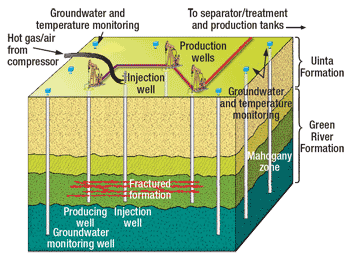 |
Fig. 2. Chevron’s CRUSH technology: Hot gas from a heater and compressor is injected into wells in a five-spot pattern.
|
|
EGL Resources subsidiary EGL Oil Shale, LLC is a privately owned independent oil company based in Midland, Texas. EGL holds a 160-acre BLM oil shale R&D lease in Rio Blanco County, Colorado. The company is developing an in situ oil shale recovery process and is proposing an oil shale research consortium to evaluate its viability. It is seeking partners that will have input on research direction; have individual rights to research results and licensed technology; and will contribute monetarily to the research. The consortium will focus on computer modeling; hydrologic studies; solutions to environmental challenges such as carbon management and mitigation of water impacts; the application and control of heat to shale in situ; and provide access to its accumulated knowledge and document base.
The EGL Oil Shale Process (patent applied for) involves the use of proven oilfield drilling and completion practices, coupled with EGL’s in situ heating and recovery technology. The EGL approach is a closed-loop in situ retorting process with advantages of energy efficiency and manageable environmental impacts. The oil shale is heated with superheated steam or other heat transfer medium through a series of pipes placed below the oil shale bed to be retorted. Shale oil and gas are produced through wells drilled vertically from the surface and vertically “spidered” (many sidetracks) to provide a connection between the heating wells and production system.
Earth Search Sciences subsidiary Petro Probe, Inc., has licensed a new processing system with great potential for recovering oil from oil shale deposits. Air is superheated in a burner on the surface and injected downhole. As the superheated air travels downhole, it heats the oil shale and brings hot, gaseous hydrocarbons to the surface, Fig. 3. The gases are then condensed to yield light hydrocarbon liquids and gases. The process achieves a controlled and relatively quick production of product. No mining is involved in the technology. Radiant heat in the inlet conduit produces a non-burning thermal energy front of predictable radius in the oil shale surrounding the borehole. High temperatures and correct pressures cause the shale to gasify; its gaseous hydrocarbon products are withdrawn as an effluent gas. Four products result: hydrogen, 45°API-gravity condensate, 1,000-Btu methane, and water.
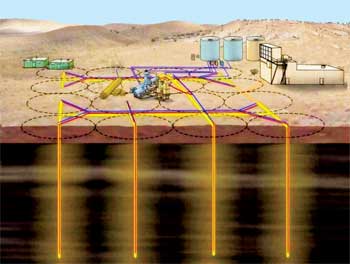 |
Fig. 3. Earth Search Sciences/Petro Probe hot-air injection gasifies kerogen around the borehole.
|
|
This is a self-sustaining system: effluent gas is transferred to a condenser where it is allowed to expand and cool; the gaseous fraction is separated from the liquid fraction and scrubbed to provide an upgraded synthesis gas; a portion of this gas is recycled and combined with other recycled feed stocks to create continuous fueling within the combustor, resulting in a significant product cost savings.
The process is environmentally sensitive: Produced CO2 is compressed, then pumped back into the oil shale body where, hopefully, it remains. Earth Search Sciences’ patented airborne hyperspectral remote sensing technology accurately reads the detailed chemical properties of the Earth’s surface from great altitudes, producing easily-interpreted maps and facilitating location of resources.
The in situ process can gasify and recover products from oil shale deposits at least 3,000 ft deep. The formation retains 94 to 99% of its original structural integrity once the kerogen has been gasified. The surface plant’s portable design allows it to be dismantled and moved to the next site. All surface structures are modularly designed and self-leveling, easily moved from one location to another without leaving permanent scars on the landscape. Each complete plant will cover about one acre of land and produce products for 10 to 20 years before depletion occurs.
Earth Search used remote sensing technology to identify an ideal test site and promising production site with infrastructure already in place on the Ute Reservation. A gas pipeline runs in front of the site to Salt Lake City. The site Earth Search has engineered is on the Naval Oil Shale Reserve. Petro Probe is focused on obtaining oil shale mineral rights in Wyoming, Utah and Colorado.
Earth Search Sciences just acquired General Synfuels International, Inc.-a private company that holds the patent to recover the oil and gas by this method. Petro Probe has been examining the process through a license and has completed due diligence. It claims there are indications that the value of the process may exceed all expectations.
Three areas of proven oil shale deposits have been chosen as the sites for proof-of-concept plants to be built in three stages: the first stage will prove the patented procedure using custom-designed equipment; the second stage will prove the economics of recovering multiple products from in situ oil shale; the third stage will test the capacity and operation of a complete plant. About $30 million is budgeted for the three stages. CH2M Hill will be the professional engineering firm of record during the testing and commercial stages.
Exxon Mobil Corp. has been engaged in the oil shale industry since the 1960s as a resource owner, technology developer and project developer. Although the company continues to evaluate advanced mining and retorting processes, ExxonMobil is focused on field testing and development of in situ technologies. Its leading candidate is the Electrofrac process for in situ oil shale conversion to producible oil and gas. As shown in Fig. 4, the method heats oil shale in situ by hydraulically fracturing the oil shale and filling the fracture with an electrically conductive material, forming a heating element. Depicted here is what might be a preferred geometry, using longitudinal vertical fractures created from horizontal wells and conducting electricity from the heel to the toe of each heating well. Other geometries are feasible.
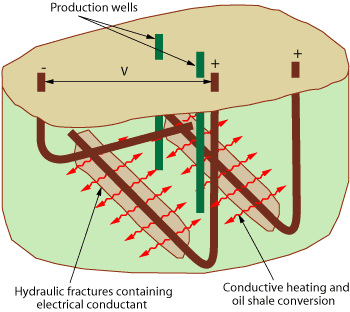 |
Fig. 4. ExxonMobil’s Electrofrac process.
|
|
The use of fracturing was motivated by early ExxonMobil screening of over 30 candidate technologies, which concluded that linear heat conduction from planar heat sources is likely to be the most effective method for heating organic-rich rock to convert it to oil and gas. Planar heaters such as these should require fewer wells than wellbore heaters and offer a reduced surface footprint.
ExxonMobil owns fee lands in the Piceance Basin in Rio Blanco and Garfield Counties in Colorado, covering more than 50,000 acres. These were acquired primarily for development by mining and retorting. ExxonMobil has conducted extensive laboratory research on Electrofrac including small-scale experiments, numerical modeling and resource description work addressing critical technical issues. Results to date have been encouraging. Plans are being developed for field experiments designed to test Electrofrac process elements on a larger scale. Multiple field sites are under consideration, including ExxonMobil’s Colony oil shale property in Parachute, Colorado.
ExxonMobil plans to continue research, development and demonstration efforts on the Electrofrac process, to determine its technical and economic feasibility for commercial-scale application. ExxonMobil is interested in research and commercial leases that would provide access to high-grade oil shale resources best suited to in situ development.
Independent Energy Partners (IEP) is based in Denver, Colorado, and is pursuing the development of unconventional hydrocarbon resources, including oil shale resources already under its control, by applying patented in situ production technology. IEP owns the exclusive rights to a broad, patented Geothermic Fuel Cell (GFC) technology, which could lower the cost of oil and gas recovery from oil shale, coal, tar sands and heavy oil deposits, while producing electricity as a byproduct. IEP is engaged in the oil shale industry as a resource owner, technology developer and project developer. IEP is actively pursuing mineral interests in oil shale and coal deposits in Colorado, Utah and Wyoming, on which to employ its technology.
In the IEP concept, rather than a burner or electric heater, a high-temperature metal-oxide fuel-cell stack is placed in the formation to heat the ground. As the ground is heated, hydrocarbon liquids and gases are released from the resource. Producing wells collect the hydrocarbons and a portion of the gases are processed and returned to the fuel cell stack, with the rest available for sale, Fig. 5. After an initial warmup period (during which the cells are fueled with purchased natural gas), the process becomes self-sustaining from gases liberated by its own waste heat. The system, in steady-state operation, produces oil, electricity and natural gases.
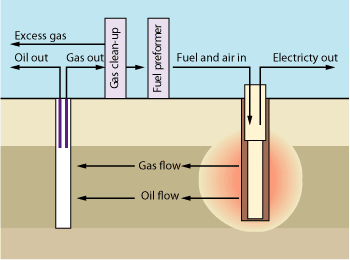 |
Fig. 5. IEP’s geothermic fuel cell process.
|
|
Fuel cells are normally designed to maximize electricity production, but the objective here is to maximize “waste” heat, although any excess electricity produced will still provide revenue. The geothermic fuel cell is designed to produce a net energy ratio of about 18 units of energy produced per unit used, when primary recovery is combined with residual char gasification and resulting synthesis gas.
Geothermic fuel cells heat formations by solid-to-solid conduction more efficiently than non-conductive applications. GFCs produce heat at a uniform rate along its length and, therefore, heat the formation uniformly from top to bottom, leading to much-improved yields and simplified production cycles. Raising the formation temperature increases fluid pressure in the heated zone by 100 to 200 psi over native pressure, which can be enough to fracture oil shale. Alternatively, the formation can be pre-fractured to enhance the hydrocarbon flow and communication between heating and producing wells.
Unlike some conductive approaches, geothermic fuel cells do not consume vast amounts of energy; rather, they become self-fueling. Geothermic fuel cells would yield about 174 kWh per barrel recovered. Capital and operating costs are estimated at $30/bbl, decreasing to about $14/bbl when offset by revenues from the sale of produced gases and electricity. The closed-loop system produces minimal air emissions and is nearly self-sufficient in process water. It produces steam as an exhaust, which is recirculated through fuel pre-reformers.
IEP entered into an agreement with private landowners in August 2005 to secure the exclusive right to produce energy from oil shale on property located in Rio Blanco County. According to Alan Forbes, chairman and CEO of IEP, the land has little or no water, which should help eliminate a huge environmental concern. The company has concluded negotiations with Battelle, operator of the DOE’s Pacific Northwest National Laboratory, for prototype development of IEP’s technology. It has also signed an agreement with one of the majors as a partner. Forbes is hopeful that the company can begin installing the technology within 24 months.
James Q. Maguire, Inc., is a small independent oil and gas development company located in Norman, Oklahoma. It is primarily engaged in oil and gas production and drilling operations. Maguire is involved in the oil shale industry as a technology developer with a patent-pending operation that he believes is superior to any described in situ method to date. He owns no shale oil acreage, but is looking for financial participants to develop his patent-pending method.
Maguire’s process for the production of shale oil involves drilling a “motherbore” vertical wellbore, from which are drilled six horizontal fracturing boreholes (radially spaced) and six injection boreholes above the fracturing boreholes and six production boreholes below, Fig. 6. The crux of the “Maguire Process” is a fracturing method that will end up creating a “spider web” fracture system so that a very large area is created to apply heat to the oil shale reservoir.
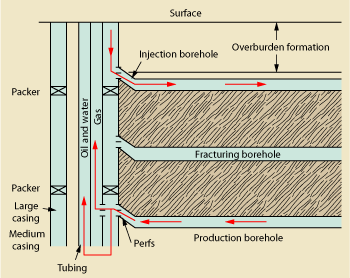 |
Fig. 6. Schematic cross section of Maguire’s three-stacked laterals with fracture network.
|
|
This fracturing process consists of injecting a very large amount of liquid nitrogen at very high rates into the horizontal fracturing boreholes. The idea is to get the liquid nitrogen to build up to pressures in excess of 12,000 psi. In fracturing, the fractures will grow, but if the volume of injected liquid nitrogen and the very fast injection rate exceeds the volume of propagating fractures, then pressures two to three times the propagation fracture pressure will result in perpendicular fractures which, in turn, will have perpendicular fractures so that a “spider web” fracture system is created.
Mountain West Energy (MWE) is developing In situ Gas Extraction (IGE) technology, a low-cost, scalable, fast, low-impact oil extraction process to produce oil from shale. In addition, IGE produces oil equivalent to Synthetic Crude Oil (SCO) produced from oil sands, without post extraction upgrading. MWE has demonstrated IGE in the laboratory and is ready to deploy the technology in the field.
MWE is focused on developing the vast oil shale resources of the Green River Formation in Utah, Colorado and Wyoming through technology development, exploration and operation. MWE, in collaboration with industry partners through technology licensing agreements, is working to achieve commercial operations. MWE’s IGE process uses high-temperature natural gas injected into the target oil shale layer to heat the oil shale to the decomposition temperature by convection. The gas sweeps the oil vapors to the surface, where the oil is condensed and separated. The gas is then recirculated, Fig. 7.
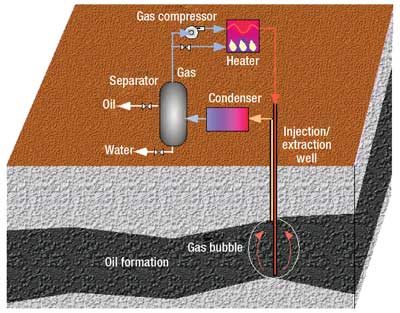 |
Fig. 7. Simplified schematic of the In-situ Vapor Extraction (IVE) process.
|
|
IGE takes advantage of single-phase gas flow, reducing the problems associated with the flow of viscous, liquid oil through the formation. The high-pressure gas bubble formed within the oil shale layer reduces groundwater flow into the extraction zone. IGE uses a single, vertically oriented well, which reduces costs, improves profitability and minimizes environmental impact. In addition, MWE’s IGE process can be used for Enhanced Oil Recovery (EOR) from conventional reservoirs, potentially doubling the amount of extractable oil. MWE is working with the Department of Energy’s Office of Fossil Energy, Rocky Mountain Oilfield Testing Center, to demonstrate IGE for EOR in the field (see World Oil, March 2008 for a detailed article).
MWE has obtained oil shale leases on 880 acres of Utah Trust lands in the Uintah Basin, Uintah County, Utah. The target Mahogany zone oil shale layer on its leases is approximately 2,800 ft below the surface and about 110 ft thick, averaging 22 gallons per ton. Each IGE well covers about 0.75 acres and should produce over 60,000 barrels of oil over one year. IGE is capable of cost-effectively extracting oil from oil shale at any depth greater than 500 ft and thicker than 25 ft, which makes oil extraction technically and economically feasible over most of the Green River formation.
To date, MWE’s IGE technology has been tested on a bench-scale system in the company’s laboratory with positive results. MWE is working with the Petroleum Research Center at the University of Utah to simulate IGE on a computer model of an oil shale reservoir. It is also in the process of implementing IGE for EOR in the field on the Shannon Formation of the Teapot Dome oil field, which is part of the Naval Petroleum Reserve 3 (NPR-3). MWE is working to obtain an exploratory permit to drill a pilot well on its oil shale leases in Utah. The company plans to demonstrate profitable oil extraction from oil shale within the next two years. MWE plans to produce commercial quantities of oil from oil shale (16,000+ bopd) by 2011.
Phoenix Wyoming, Inc. is a Delaware corporation with offices in metro Denver, Colorado. The company is focused on the development of hydrocarbon resources in the Rocky Mountain region of the US. Its main interest, at present, is oil shale development. The company is one of three small, entrepreneurial companies that have banded together to form the Oil Shale Alliance, Inc. and intend to commercially develop oil shale quickly and efficiently. The other two companies in the alliance are Independent Energy Partners Inc. and Petro Probe Inc. (see above).
Phoenix wishes to help develop this oil shale, using its own advanced in situ technology. Phoenix Wyoming Inc. and its technology partners in Oil Shale Alliance Inc. are now seeking leases on 100,000 acres of oil shale that is estimated to contain at least 100 billion barrels of recoverable oil. The company uses borehole microwave technology that may result in the economic and environmentally friendly production of some of the oil shale reserves in the US. The three companies that comprise the Oil Shale Alliance will be using three different in situ technologies: solid oxide fuel cells, borehole microwave and hot-gas injection. All three technologies have significant advantages in oil shale development.
Phoenix Wyoming plans to field test its borehole microwave technology this year. In prior, smaller-scale, field tests, the borehole microwave approach heated the ground 50 times more quickly than electric heating rods.
Raytheon is a technology leader specializing in defense, homeland security and other government markets throughout the world. The company is an expert in radio frequency technology. Its Integrated Defense Systems business unit applied applications of radio frequency technology to facilitate production of oil shale and tar sands and heavy oil deposits nearly 30 years ago. The project was revived and dramatically upgraded a few years ago when Raytheon began to look at energy supply as a stability and security issue. The company is partnering with CF Technology of Hyde Park, Massachusetts, to offer its shale oil extraction technology for license. CF Technology is an expert in Critical Fluid (CF) technology and is the designer and manufacturer of the combined processing equipment.
The company has integrated its proven Radio Frequency (RF) technology and antenna design with CF’s technology for critical fluids. It intends to license the integrated technology to service companies and heavy oil, tar sands, and oil shale producers on a resource- and region-specific basis.
Raytheon and CF Technology have developed a patent-pending extraction methodology involving RF and critical fluids. Under this extraction scenario, oil wells are drilled into the shale strata using standard oil industry equipment. RF antennae, or transmitters, are lowered into the shale. The antennae then transmit RF energy to heat the buried shale, Fig. 8.
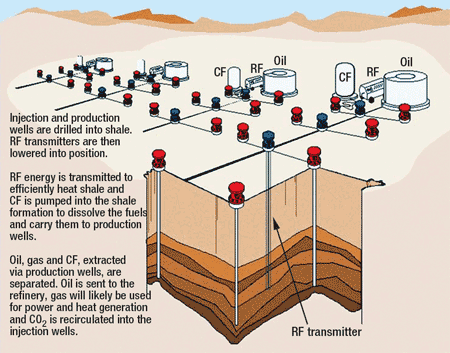 |
Fig. 8. RF/CF method of heating and extraction.
|
|
Super critical carbon dioxide is pumped into the shale formations to extract the oil from the rock and carry the oil to an extraction well. At the surface, the CO2 fluid is separated and pumped back into injection wells, while the oil and gas are refined into gasoline, heating oil and other products. Ultimately, a self-sequestration approach is expected to yield a neutral carbon footprint for process operations.
For oil shale, this technology may recover four to five barrels of oil for every barrel consumed; this compares favorably to other methods. For tar sands and heavy oil, this process could yield 10 to 15 barrels of oil equivalent per barrel consumed, due to the lower heating temperatures required. This extraction technology would start producing in only a few months compared to years of heating required by other in situ processes.
When applied in tar sands, the combined RF/CF technology performs a mild upgrading in situ, yielding an attractive, light, sweet crude oil. The process is “tunable,” facilitating production of various product slates. Raytheon does not own or control any oil resources; rather the company (partnered with CF Technologies) is focused on licensing its technology to qualified energy resource development companies or oil field service companies.
Raytheon’s RF technology was commercially proven for oil shale applications in the 1970s. Since then, the company has continued to perfect the technology, focusing on antenna design and system integration. While the combined technology has not been tested at commercially representative scale, Raytheon and CF Technologies consider the integrated technology to be demonstrated in the laboratory. This technology was recently sold to Schlumberger. Ratheon still consults on the technology in a minor role, while CF technology continues to be actively involved in furthering its development.
Shell Oil Company has been pioneering in shale oil research for more than 25 years. On its Mahogany Research Project in Rio Blanco County, Colorado, has been ongoing since 1996 to evaluate its In situ Conversion Process (ICP), Fig. 9. The Bureau of Land Management granted approval of Shell’s three, 160-acre oil shale RD&D leases on BLM land.
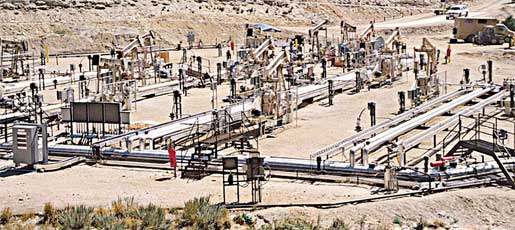 |
Fig. 9. Shell’s field research in Rio Blanco County, Colorado. Courtesy Shell Exploration & Production.
|
|
Shell’s ICP generates more oil and gas from a smaller surface pad area than previous oil shale processes. Shell’s in situ technique requires establishing a freeze wall by conventional refrigeration means as is done in the coal mining industry, which will take a period of months to years. This prevents subsequent migration of groundwater into the project area. The interior of the project area is then dewatered through pumping. Wells drilled in the interior of the project area have electric resistance heaters in them, which slowly heat the formation (kerogen) to 650 to 700°F over the course of one to two years or more.
Target depth is typically from 1,000 to 2,000 ft. Products are pumped to surface using traditional methods and boreholes. The method produces about one-third natural gas and two-thirds light oil. Resulting liquids require fewer processing steps to produce high-quality transportation fuels.
On its private property, Shell is currently conducting the Freeze Wall Test, an environmental study to mature the technology designed to keep groundwater out of subsurface production areas using a frozen, underground barrier, Fig. 10.
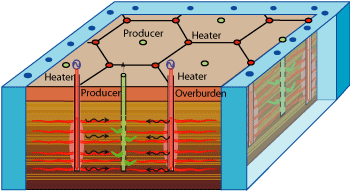 |
Fig. 10. Schematic showing the principal components of Shell’s in situ shale oil process. A blue ice wall surrounds and contains the field.
|
|
On only a 30 × 40-ft testing area, Shell successfully recovered 1,700 bbl of high-quality light oil plus associated gas from a short interval of shallow oil shale layers, with less-than-optimal kerogen content, thus determining their technological design works.
Any future Shell commercial development in Colorado will depend on the economic viability and environmental sustainability of its ICP. Shell hopes to make a decision on a commercial project in the next decade. 
LITERATURE CITED
1 Bartis, J. T. et al., Oil shale development in the United States, prospects and policy issue, The Rand Corporation, Santa Monica, Calif., 2005. 2 Dammer, T., Strategic significance of America’s oil shale resource, presented at 2005 EIA Mid-term Energy Outlook Conference, US Department of Energy, Washington D.C., April 12, 2005. 3 Oil shale and tar sands draft programmatic Environmental Impact Statement, Vol 2, Chapter 4, December 2007. 4 DES 07-60, Draft Oil Shale and Tar Sands Resource Management Plan Amendments to Address Land Use Allocations in Colorado, Utah, and Wyoming and Programmatic Environmental Impact Statement, Vol. 3, Chapters 7, 8, & 9, Appendix A, December 2007.
|