|
|
|
By Petroleum Technology Transfer Council |
Air hammers cut Barnett Shale drilling time in half
In certain geological regions with mature, stable and relatively dry formations, advances in this drilling technique have resulted in better holes, often at double ROP and dramatic cost savings.
John Meyers, Diamond Air Drilling Services, San Angelo, Texas; and Michael Sagan, Hallwood Energy, Cleburne, Texas
To reduce drilling time and costs on Barnett Shale wells, Hallwood Energy used air hammers with diamond insert bits. For vertical wells, time from spud to total depth dropped from 12 – 14 days to 6 – 8 days, representing about $72,000 per well savings. In horizontal wells, time from spud to kick-off point has dropped from 10 – 12 days to 5 – 6 days. Costs associated with the air-hammer/ diamond-insert bit drilling approach (air compressor, fuel, hammer, hammer bit, supervision) are offset by saving on mud and fewer roller cone bits, stabilization, and/or mud-motor costs. In 6 of 12 wells drilled through June 2004, half were drilled with a single bit/trip. The drilling team expects that its goal of drilling 80%, or 8 of 10 wells, with a single trip, can be reached during 2004.
INTRODUCTION
In the past few years, the Barnett Shale has become a major play for independent producers within the Mid-Continent region of the US. The formation is found in the Fort Worth basin and can produce a significant amount of gas after hydraulic fracturing. Most of the drilling in past years has been in Wise, Denton and northern Tarrant counties north of Fort Worth, Texas, by large independents such as Devon Energy and EOG Resources, but more wells are now being drilled further south in Parker and Johnson counties with future drilling planned for Hood, Hill and Bosque County by numerous independents.
SITUATION
Barnett Shale wells are typically drilled to a depth of about 7,500 ft, with the 12-1/4-in. surface hole being drilled to 1,400 ft, and then either 7- 7/8-in. or 8-3/4-in. hole to total depth. Standard drilling practices with Roller Cone (RC) bits have had deviation problems because of the high Weight-On-Bit (WOB) that is required to make an RC bit drill fast. The deviation problems are typically caused by high-formation dip angles and are controlled conventionally by: 1) running light WOB, which reduces Rate Of Penetration (ROP); or 2) by running stiff, stabilized BottomHole Assemblies (BHAs), which increases torque; or 3) by using expensive directional tools (i.e., mud motors, MWD, etc.). Data from Hallwood's Rigby-1 is illustrative of drilling performance using conventional drilling techniques, Table 1.
|
Table 1. Bit record with conventional drilling techniques (Rigby-1 well, drilled in 13 days, 2/6/04 through 2/18/04). |
|
|
Bit size,
in. |
Bit type,
IADC |
Depth
out |
Footage |
Hours |
ROP,
ft/hr |
Deviation
(degrees) |
Reason
pulled |
Comment/
bit cond. |
|
|
|
|
|
12-1/4 |
517X |
1,423 |
1,383 |
18.5 |
74.8 |
< 2 |
TD |
2 / 2 / WT |
|
|
7-7/8 |
527X |
5,233 |
3,810 |
79.5 |
47.9 |
4 + |
PR |
6 / 8 / WT |
|
|
7-7/8 |
617X |
6,219 |
986 |
69.5 |
14.2 |
< 4 |
PR |
8 / 8 / BT |
|
|
7-7/8 |
537Y |
7,191 |
972 |
43.0 |
22.6 |
2.5 |
TD |
4 / 4 / TD |
|
|
7-7/8 |
Totals |
|
5,768 |
192.0 |
30.0 |
|
|
|
|
|
SOLUTION
When contemplating how to lower drilling costs and minimize drilling problems, Hallwood Energy thought that the low-pressured formations might be air drillable, and that using an air hammer might help reduce deviation problems even when using a slick BHA. Basic operation of an air hammer is shown in Fig. 1. Diamond Air Drilling Services recommended that diamond insert hammer bits (Fig. 2) could be used to drill the entire 7-7/8-in. interval with one trip, thus eliminating at least three RC bits. Drilling results from the first three wells showed that the ROP more than doubled from 40 – 50 ft/hr with RC bits, to 90 – 100+ft/hr with air hammers, Table 2. Deviation was controlled to less than 4° without sacrificing ROP.
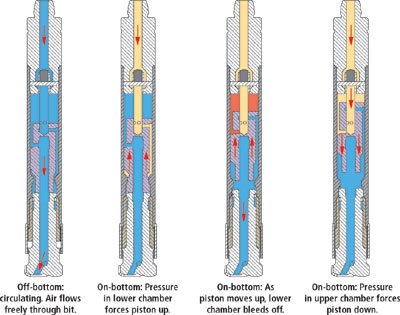 |
Fig. 1. Drilling hammer sequence schematic.
|
|
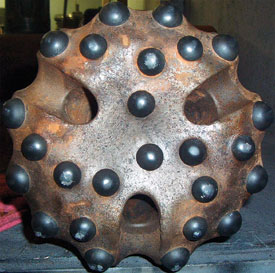 |
Fig. 2. This hammer bit with polycrystalline diamond inserts drilled from 1,445 to 7,330 ft in Hallwood's Cooper-2 in 60.5 hrs (97.3 ft/hr).
|
|
|
Table 2. Bit record with air hammers (Cooper-2 well, drilled in 7 days, 2/23/04 through 2/29/04). |
|
|
Bit size,
in. |
Bit type,
IADC |
Depth
out |
Footage |
Hours |
ROP,
ft/hr |
Deviation
(degrees) |
Reason
pulled |
Comment/
bit cond. |
|
|
|
|
|
12-1/4 |
117 |
1,445 |
1,405 |
11.0 |
127.7 |
1/4 |
TD |
? |
|
|
7-7/8 |
C673G |
7,330 |
5,885 |
60.5 |
97.3 |
< 4 |
TD |
1 / 1 / TD |
|
|
Proper supervision is essential for operational success. Because the operational parameters are significantly different for air hammer drilling (Fig. 3.) versus conventional mud drilling, Diamond Air provides an experienced driller (often a former rig tool pusher) to train the rig's drillers about the proper operating conditions. This hammer supervisor is not only on location to help ensure good hammer and bit performance, but also teaches rig personnel unfamiliar with the differences in annular hole cleaning with air, as compared to mud drilling. Understanding proper hole cleaning, with air as the circulating fluid, is the major difference that rig personnel must realize to stay out of trouble. Improper hole cleaning can lead to getting stuck or a down-hole fire (burn-off), which can create a lost-in-hole BHA and eventual side-track of the well.
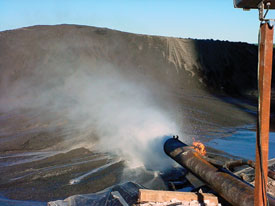 |
Fig. 3. Air volumes should be in the 3,000 to 5,000 ft/min range, 30% higher for misting and/or directional applications. Hammer choke should result in 350 psi differential across hammer.
|
|
Success rate. Data from Cooper-2 (Table 2) confirms that one can drill the entire production section, or at least to the kickoff point, with one bit/trip. Thus far, after drilling 12 wells through June 2004, this was accomplished on six wells (50% success rate). Although not achieving one-trip performance in all wells, it should be noted that all 12 wells were drilled at a lower cost per foot and/or less number of days than conventional mud-drilling techniques. The Hallwood/ Diamond Air drilling team has a goal of completing 8 of 10 wells (80% success rate) with one bit/trip performance, which the team believes can be achieved in 2004.
Cost savings. It is estimated that an average of six days are saved on each well, which, with daily costs running about $12,000 per day, translates to savings of $72,000 per well. The additional costs of the air compressors and fuel, as well as the hammer, diamond-insert hammer bit and supervision are offset by the mud cost savings, as well as the reduced number of RC bits, stabilization and/or mud motor costs.
Additional advantage. It has also been noted that the diamond insert hammer bits have kept the hole in gauge, while the use of air has eliminated the mud-filter cake on the hole wall, which has reduced the amount of cement contamination. Thus, both have contributed to better cementing operations and improved cement bonds. It is felt that these have proven to be critical factors in accomplishing an effective Barnett Shale hydraulic fracture-job and well completion. 
THE AUTHORS
|
 |
John Meyers, sales/ product engineer with Diamond Air Drilling Services, has responsibility for Design and Application Engineering. His experience includes 20 years within the drilling industry working as a field and applications engineer for roller cone and PDC bits, mud motors and MWD equipment. He has been working in the Air and Hammer drilling segments of the oil and gas market since 1996. He has a BS degree in mechanical engineering from Louisiana State University. He may be contacted at jmeyers4@houston.rr.com.
|
|
|
|
Michael Sagan, drilling and production manager with Hallwood Energy, has responsibility for all drilling, completion and production engineering as well as operations. His experience includes 29 years in all parts of Texas, Louisiana, Oklahoma and the Gulf of Mexico. He has a BS degree in petroleum engineering from Pennsylvania State University. He may be contacted at msagan@hallwoodenergy.com.
|
|
|
|