ED IZZI, Pentair Valves & Controls
The primary changes in early shale development involved larger size and scale. Advancements in drilling technology allowed for longer laterals, and increased segmentation during the drilling and hydraulic fracturing process. This resulted in a surge in demand for new equipment.
As the shale boom advanced, equipment manufacturers shifted from simply meeting immediate needs to developing technologies focused on driving overall extraction costs down, and improving economics. Valve manufacturers, armed with new field application experience, followed this trend.
In only a few years, the industry has grown much more complex. Today, multi-pad wellsites with 2–3-mi laterals are common. Increased horizontal distances require additional horsepower and, hence, higher pressures. Flow control has become more challenging, due to greater liquid volumes and pressures, as well as exposure to abrasive media and chemicals.
Operational considerations. From an operational standpoint, the concentration of activity in the major shale regions, coupled with economic, permitting and environmental factors, has had a profound effect on well-related operations. Changes have been manifested in the form of shorter drilling/completion cycles to improve efficiency.
Changing flow characteristics over time are also a major consideration, as there are often radical declines in both flowrates and pressures over the life cycle of an individual well. As a result, valves need to perform over a wide range of operating conditions.
The large quantity of frac fluid being pumped is a critical factor in shale stimulation. The proppants pumped with the fluids—including sand, ceramics, resin-coated sand and other materials—are hard, abrasive materials that cause wear on valves. Harsh fluid chemistries are often present, so valves must be selected to resist these aggressive components.
Reservoir diversity. Valve selection is further complicated by the diverse geological characteristics of shale reservoirs.
The oil-bearing Bakken shale in Montana and the Dakotas produces at initial production (IP) rates of 1,000–3,000 bpd at 2,000–4,000 psi and temperatures of 150–200°F. The Marcellus in western Pennsylvania has minimal oil production, but gas IP is 2–8 MMcfd with flow pressures of 850–3,500 psi.
In Texas, the Eagle Ford can have an IP flow pressure up to 7,000 psi, with temperatures to 350°F. It produces both oil and gas with residual H2S and CO2. Further east, the Haynesville shale can exhibit extremes of pressure and temperature that can reach 10,000 psi and 380°F.
Rapid pressure build-up and decline, high sand production, and H2S and CO2 content are common. All of these variations are significant in selecting a valve that delivers the best operational and economic performance. It is important to engineer for the application and not take a one-valve-fits-all approach.
VALVE DESIGN AND SELECTION
From wellhead drilling to gas treatment, a wide range of valve types is utilized.
Though it is difficult to capture all possible circumstances, due to the wide range of characteristics across different shale basins, we have summarized some design best practices and provided selection examples, Table 1.
Table 1. Valves used in drilling, fracturing, completion and production. (Click to enlarge) |
|
Choke valves. Choke valves are used on the well pad for flow control in gas lift and well fracturing, Fig. 1. For abrasive shale applications, a rotating disk design provides an alternative for longer service life and tight shut-off, even during pressure variations and drop-offs common in shale operations. The disc is spring-loaded to ensure that the valve is vibration-free during pressure fluctuations, while hard-coated components resist erosion by abrasive sand.
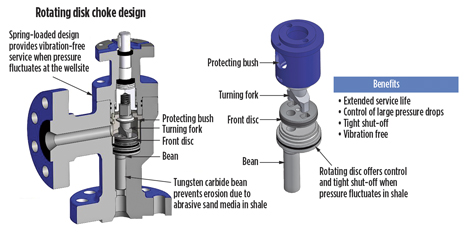 |
Fig. 1. Choke valves at the well pad. |
|
Butterfly valves. In truck and tank applications associated with drilling and completion, resilient, seated butterfly valves offer a reliable, cost-effective means of flow control and isolation, Fig. 2. The quarter-turn design is easy to install, operate and automate, and it performs well in a shale application, when applied correctly.
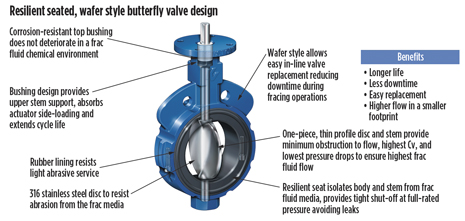 |
Fig. 2. Butterfly valves for drilling/completion. |
|
Tight shut-off is achieved via an interference fit, by which the elastomer liner is compressed around the disc edge. Media are isolated from the shaft journals with flats machined on the disc at the shaft-entry points, which mate with the rubber seat. Secondary stem seal is achieved, again, by compression of the seat around the shaft. The elastomer liner extends beyond the body, forming a gasket, so that additional flange gaskets are not required.
Butterfly valves are available in many configurations, styles and materials of construction. A number of features contribute to longer service life, including stainless steel discs, shaft bushings (which have the added benefit of lower operating torques), and elastomer seat options that offer enhanced resistance to abrasion and chemical attack from fracturing media and produced water.
One-piece shaft/disc designs are ideal for isolating/controlling the large amounts of abrasive media typical of fracturing operations. This geometry offers a larger effective flow area, resulting in higher flow capacity and lower pressure drop, thus saving energy. The thin disc produces less interference with the elastomer, further reducing the wear effects of abrasive solids, while lowering operating torques. Finally, the split body allows for easy maintenance, reducing downtime.
Triple offset valves. In gas processing applications, zero leakage is essential. Further, the valves need to provide many years of reliable, maintenance-free operation in relatively severe conditions. Considerations include:
Triple-offset valves (TOVs) are an excellent choice here, Fig. 3. The unique geometry produces a camming action, which eliminates rubbing between the seat and seal. Torque is applied to radially charge the seal ring that is fitted to the disc. The ring uniformly distributes torque to the seat. This design eliminates wear produced by metal-to-metal rubbing, while ensuring zero leakage to API 598 and API 6D standards. It also compensates for temperature extremes, from the cryogenic temperatures encountered on turbo-expander inlets to the very high temperatures on molecular sieve regeneration cycles and amine units, maintaining seal integrity.
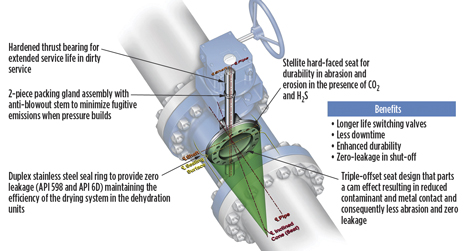 |
Fig. 3. Triple-offset valve design. |
|
Abrasion and corrosion resistance are further enhanced with a duplex seal ring and Stellite 21 seat overlay. Other useful features include bearing protectors to isolate the bearings from flow stream contaminants, such as molecular-sieve dust, and solid metal seal rings for higher pressures.
While carbon steel construction is acceptable for most applications, cryogenic temperatures or H2S/CO2 amine streams often require stainless steel. Typical applications for TOVs include:
CONCLUSION
The surge in shale gas activity has driven a broad understanding of valve applications backed by extensive field experience. The net effect has been continual improvement in system integrity through application of best practices. Proper research and valve selection, with consideration for the particular shale gas conditions, will help to ensure drilling and completion efficiency, process optimization and operational reliability. 
|