ESSAM DAGHER, Apache Corp.; MOATAZ TAWAKOL and PHILIP NGUYEN, Halliburton
Khalda Production Company’s Shrouk #3 oil well, in Egypt’s Western Desert, was recently recompleted with hydraulic fracture stimulation. Initial production was around 1,000 bopd. The well produced large amounts of proppant, and within three days, solids output destroyed the production pump. The operator shut down the well while searching for a solution to the proppant flowback problem. Well parameters are shown in Table 1.
Table 1. Well parameters for Shrouk #3, in Egypt’s Western Desert |
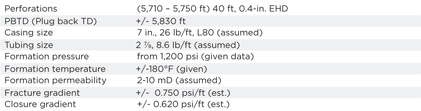 |
After the well was shut in for several months, the operator worked with the service company to implement a remedial treatment, using an aqueous-based resin consolidation and proppant flowback control (CPFC) material. The treatment proved that a well can be brought back to life with a higher drawdown pressure, once a remedial treatment has been implemented. Table 2 presents a history of events at the well. Figure 1 presents the well’s production results, showing the restored solids-free output.
Table 2. Well problems and production history, before and after CPFC treatment. |
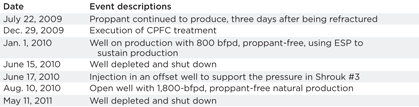 |
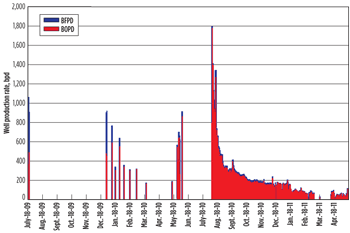 |
Fig. 1. Testing data for Shrouk #3. After production was restored, the well produced, proppant-free, until depletion. |
|
FLOWBACK PROBLEMS
Output of proppant and formation material is a pervasive industry problem that hinders production worldwide. When examining output losses, coupled with resultant expenditures caused by maintenance, equipment repair and replacement, this problem is one of the greatest detriments to an asset’s profitability and the operator’s return on investment.
Halting or minimizing proppant flowback after fracturing can increase productivity and reduce operating costs, thus turning marginally commercial fields into profitable assets. Wells are often shut in or abandoned when they become uneconomical to produce at the lowered production rates that are required to limit proppant flowback. In many cases, production of hydrocarbons becomes restricted when producing intervals are covered or partly covered with produced proppant and/or formation solids. Additionally, proppant flowback during production often causes damage to downhole pumps and surface production equipment. Removing proppant from the wellbore and repairing the equipment is expensive and results in lost productivity. Worse, simply cleaning the wellbore does not prevent recurrence of proppant flowback, and the cleanup process may have to be repeated several times to keep well output at desired rates.
Proppant flowback can result in a number of costly problems:
-
Production decreases, especially in mature and marginal reservoirs
-
Excessive damage to downhole pumps and surface production equipment
-
Repeated costly workovers and CT cleanouts
-
Intentionally choking back production to reduce sand production or proppant flowback
-
Wells shut in rather than operated uneconomically at low production rates
-
Lost revenue from choking back production and shut-in time during workovers.
AQUEOUS-BASED CPFC SYSTEM
Operators may now control proppant flowback, using an aqueous-based system that is applied after fracture-stimulation treatments. Being aqueous-based, the system is essentially non combustible and contains no solvent-based resins. The treatment service is normally a rig-less intervention procedure that requires no isolation packers, thus reducing the time, cost and higher risk associated with a conventional workover. This approach treats the existing proppant in the near-wellbore region of propped fractures to reduce or eliminate current and future proppant (and/or formation material) production.
Use of the aqueous-based CPFC system can provide several benefits:
-
High flash point
-
Minimal number of treatment stages and the ability to treat long intervals (can be foamed to enhance diversion into all intervals)
-
Economy—small fluid volumes required
-
Simple application (bullhead squeeze)
-
Easy surface equipment cleanup
-
Minimized potential of fluid contamination during placement (often a problem when using solvent-based resin).
Viscosity of the consolidation system is low, similar to that of water, i.e., ~ 3 cP at 70°F. Laboratory testing has verified that consolidation performance of the aqueous-based CPFC system is equal to, or superior to, solvent-based systems, indicating a strong capability to prevent proppant flowback in high-rate production wells.
CPFC SYSTEM TREATMENT
The CPFC systems’ consolidating and activator components are pre-blended and handled separately. If kept separated, these two solutions can remain stable for many months. During application, the two solutions are 1) metered together “on the fly” through a static mixer or 2) batch-mixed to form a homogeneous mixture just before they are injected downhole into the perforated interval. The system coats the proppant in the fractures and the formation sand surrounding the perforations. Injecting the treatment solution as a single component helps ensure that wherever the proppant pack is treated, consolidation will take place without the uncertainty often encountered with other externally catalyzed consolidation systems. Curing of the CPFC system takes place slowly, allowing complete placement of the treatment into the proppant pack.
The system can also be used to coat gravel placed behind eroded screens or slotted liners and the formation sand to help prevent production of solids from high-permeability formations.
Both successful placement of the treatment, and its effective coating onto the proppant, are recommended to help ensure reliable cohesion between the treated particles. This treatment’s objective is to treat the proppant near the wellbore rather than to treat the entire proppant pack in the fractures. Based on this principle, a volume of about 5 gal of consolidating fluid is used to help ensure treatment of each 1 ft of perforated interval (based on two fracture wings having ¼-in. fracture widths). This provides about 10 ft of penetration in each wing of a propped hydraulic fracture. The consolidating treatment fluid provides high cohesion between the proppant grains to keep them in place without causing plugging in the pore spaces of the proppant matrix, Fig. 2.
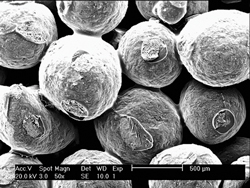 |
Fig. 2. The CPFC system provides cohesion between grains without damaging permeability or conductivity of the proppant pack. |
|
Treating long intervals presents special challenges:
-
Multiple perforated intervals with multiple fractures
-
Non-uniform placement of treatment fluids into different perforated intervals
-
Providing effective diversion, to ensure adequate placement of treatment fluids.
Field tests have shown that treatment fluids that have been foamed to a quality of 60 or more can be diverted effectively to treat relatively long intervals when dealing with propped hydraulic fractures.
Prior to placement of the CPFC system, it is imperative to clean out all proppant or debris that was left behind, to ensure that the wellbore is free of obstacles during the consolidation treatment. Such a barrier or proppant bridge could prevent complete placement of the consolidation treatment into all perforations and contribute to failure of the consolidation treatment.
Fluid sequence includes:
-
Preflush 1—Injection of a volume of mutual solvent solution to remove residual oil coating from the proppant or formation sand particulates.
-
Preflush 2—Injection of a volume of liquid or foamed brine that contains a surfactant to promote the wetting of the resin to the particulate surfaces in subsequently injected fluids. A foaming agent is metered and mixed into the liquid brine to be foamed with nitrogen.
-
Consolidation fluid—Injection of a foam volume generated from a homogeneous mixture of CPFC system and hardening components. This fluid mixture, premixed with a foaming agent similar to that used in Preflush 2 stage, enables a foam of 60- to 80-quality to be generated with nitrogen.
-
Postflush—Injection of nitrogen gas or other non-aqueous displacement fluid to displace consolidation fluid from the wellbore, perforations and the proppant pack near the wellbore.
During the treatment’s curing period, it is recommended that the well be shut in to 1) prevent or minimize fluid swabbing, backflow or crossflow (which may disturb cohesion between proppant grains), and 2) to allow the treatment to cure sufficiently. As recommended in the treatment procedure, the well should remain shut in for 24 to 48 hrs, depending on the bottomhole temperature. 
THE AUTHORS
|
ESSAM DAGHER has been a senior staff petroleum engineer at Apache Corp. since 2007. He is a team leader for the Egypt Western Desert acidizing and hydraulic fracturing stimulation team. He was a senior staff petroleum engineer for Khalda Petroleum Company from 1995 to 2007. Mr. Dagher received his BS degree in drilling and production from the Suez Canal University, Egypt, and an MS degree in petroleum engineering from Instituto Supervisor Del la Energía, Madrid, Spain, and Herriot Watt University, Edinburgh, Scotland.
|
|
MOATAZ TAWAKOL joined Halliburton in 2001. He is the sand control and hydraulic fracturing team leader in Egypt, as well as the sand consolidation champion for the Middle East/North Africa region. He is an expert in production optimization and maximizing recovery. He received a BS degree in electrical engineering from Ain-Shames University, Egypt.
|
|
PHILIP NGUYEN is a senior technical advisor in Technology at the Halliburton Technology Center in Duncan, Oklahoma. He has more than 20 years in the oil and gas industry. His current work focuses on curable and non-curable resins for hydraulic fracturing and sand control. He holds a PhD degree in chemical engineering from the University of Oklahoma.
|
|