HENRY TERRELL, News Editor
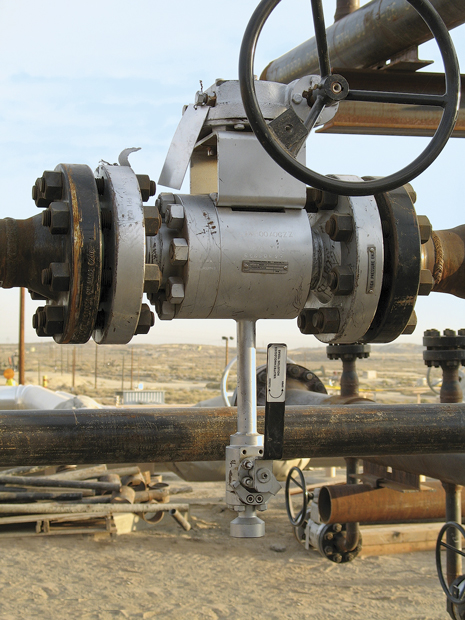 |
V1 series zero-leakage, metal-seated ball valve designed for 1,500 psi, 650°F in operation at a Bakersfield, Cal. production facility. Photo courtesy of ValvTechnologies. |
|
The first large-scale valves were used to control the flow of water in aqueducts and pipes in farming and city water supplies, and pressures were relatively low. Plug valves were the most common type, and changed little in design from ancient times up to the industrial revolution. The first time a valve had to meet a severe requirement was for high-pressure steam in early boilers and steam engines. Regulator valves capable of controlling the heat and pressure of steam had to be constructed of stronger material (brass, usually) and designed to much closer tolerances. These were the precursors of the valves that found their way into the petroleum industry.
Although it is a small minority of projects that involve high-pressure/high-temperature (HPHT) environments, the number has increased every year. Primarily in the Gulf of Mexico, South America, the North Sea and Southeast Asia, HPHT projects are growing in number as the “easy oil” gets harder to exploit. This places further demands on an already ruggedly designed product. This Valves & Actuators supplement presents three articles on recent developments in the technology, with an emphasis on increasingly harsh environmental extremes.
In shale gas operations, valves are subjected to many and varied flow-control challenges. In “Valve selection for optimizing shale gas operations,” the author describes how the boom in shale gas development, and the need to optimize economics, requires valves selected specifically for a shale environment. A one-size-fits-all approach to valve selection won’t work, because conditions vary so much from basin to basin. Effective and economic valve design and selection must consider the demands of HPHT environments, as well as the effects of corrosion and abrasive media.
Intelligent completions were introduced to address the special challenges that arise from highly deviated, extended-reach and multilateral wells. In “Second-generation interval control valves improve performance in harsh environments,” the authors explore how recent developments in exploration and drilling technology are allowing operators to target extremely complex reservoirs in deeper water, in subsalt formations, the Arctic and other extreme environments. This has required the development of a new generation of intelligent completion tools, including interval control valves (ICVs). The article describes how the requirements of extreme reservoir environments have driven the design and qualification of a new generation of ICVs for intelligent completions, with higher pressure and temperature tolerances to handle the new harsher environments, while simplifying the valves’ operating mechanism, improving performance and increasing debris tolerance.
Sub-surface safety valves serve as the emergency flow-control devices for a well. Because these tools must perform reliably over the life of the well, which is extremely challenging when operating in HPHT environments, traditional design and validation methods may not be sufficient. In “Design and development considerations for HPHT subsurface safety valves,” the authors discuss how every feature of a subsurface safety valve must be thoroughly evaluated and considered against regulatory requirements, and that additional validation techniques must be used early in the development process to ensure that the product is robust and suited to its purpose. The article also discusses specific components in regard to stress analysis and elastic displacement, use of metallic and nonmetallic materials, and the effect of control fluids on the life of the tool. 
|