Handling Produced Water
Produced-water chemical treatments enable environmental compliance
Many chemical types can produce similar results.
Ron Bosch and Eric Axcell, Champion Technologies
There are numerous misconceptions regarding the chemical treatment of oilfield produced water. This article helps overcome these by providing a general understanding of specialty chemical usage and by reviewing the chemistry of produced water. It discusses the chemicals used to modify these chemistries to overcome common oil production problems. Specific attention is given to emulsion-breaking, water-clarifying chemistries, the methods used to determine treat-water chemistries and trends in the produced water treatment.
INTRODUCTION
Oilfield specialty chemical companies treat produced water and often must overcome a negative reputation to demonstrate their value as a technical service provider. Most chemical companies aggravate this negative view by clouding their work in jargon and subterfuge in an attempt to prevent their competition from profiting from a technical advantage.
This article presents an overview of produced-water chemical treatment, while protecting intellectual property, and represents the authors’ views. As in all fields of chemistry, there are different data interpretations and many theories for the chemical mechanisms. The authors seeks to generate discussion of these mechanisms, and a more favorable understanding of the difficulties in designing effective chemical treatment programs. The article is limited to crude oil production chemistries after well completion.
There are three basic classes of chemistry used in the oil field: solids control, corrosion control, and demulsification/ clarification. For ease of presentation, these are discussed individually. Each class of chemistry, and the subclasses, has an effect on all the other programs. A single chemical can have effects in more than one class, and those effects can be positive or negative.
SOLIDS CONTROL
Solid control chemistries include scale inhibitors, paraffin inhibitors and dispersants, asphaltene inhibitors and dispersants, hydrate inhibitors, biocides in certain applications, clarifiers in certain applications, sand dispersants and wetting agents. This chemical class includes those used in “flow assurance.” They are divided into four types:
- Those that chelate, or sequester, the component molecules prior to nucleation
- Those that modify crystal growth
- Those that prevent nucleation
- Those that disperse solids and prevent them from accumulating.
Chelation. Chelation is reserved for scale inhibition. It is described by an equilibrium reaction between a metal ion and a complexing agent. Chelation reactions form more than one bond between the metal and a molecule of the complexing agent. Chelation results in a ring structure incorporating the metal ion. The typical chelating chemistry is shown in Fig. 1, ethylenediaminetetraacetic acid (EDTA).1
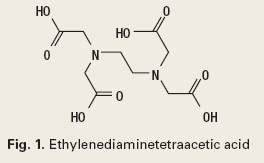 |
Crystal growth modification and nucleation prevention. Crystal growth modification is a threshold process, whereby a small number of growth inhibitor molecules can slow or prevent the growth of a number of crystals. Crystal growth inhibitors exploit the ability of certain molecules to replace a densely packed lattice of a crystal with a molecule that prevents close association. This is a heterogeneous effect, i.e. it affects the ions or molecules as they adhere to the lattice structure. Nucleation inhibition, on the other hand, results from a homogenous threshold effect at the beginning of crystal growth, as in Fig. 2.2
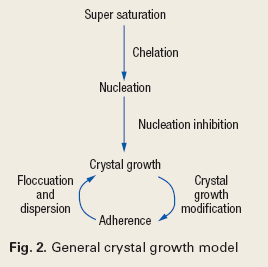 |
Many papers attempt to determine the effect of various chemistry types on scale deposition, and debate the method of effect.3 Chemistries are either oligomers of phosphonates or low molecular weight, free radical addition polymers. Although specific chemistries are subject to IP constraints, a Google search delivered the following structures from the Web page of Heriot-Watt University in Great Britain.4 Typical chemistries are phosphonates, and polymers, Figs. 3 and 4.
It is generally accepted that phosphonates function by crystal growth modification and require a slightly higher dosage, but are more forgiving in application, while polymers can function either way, but require significantly more care in application. These result in more failures in polymer programs, but a lower cost, if ideally applied.
Another application of crystal modification and nucleation inhibition for solids control is for the prevention of gas hydrate blockages. Kinetic hydrate inhibitors (KHI) prevent or delay crystal nucleation, and are effective with or without an oil phase. Anti-agglomerate hydrate inhibitors (AAHI) are crystal modifiers, and are effective in an oil phase. Both types of inhibitors are low-dosage hydrate inhibitors.5 The KHI’s are polymers such as poly(N-vinylcaprolactum), Fig. 5. The AAHIs are quaternary ammonium or phosphonium salts, Fig. 6.6
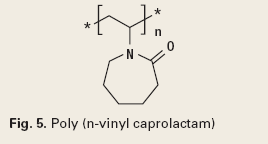 |
 |
Paraffins are aliphatic hydrocarbon waxes present in most crude oils. These will precipitate from a crude oil and deposit in production risers, subsea tiebacks, or any other production tubular or transportation pipeline where the temperature falls below the wax appearance temperature of the crude. Paraffin inhibitors function by interfering with the bonding of aliphatic wax molecules to each other. They are generally branched chain type polymers, Fig. 7.7
Asphaltenes are a solubility class within crude oil that are soluble in aromatics, but insoluble in aliphatics. They are considered large aromatic agglomerates composed of heterocyclic rings. Asphaltenes are thought to be held in solution by naturally occurring petroleum resins that adhere to the outer surface of the asphaltene agglomerate. Asphaltenes precipitate when these resins are disrupted. Asphaltene inhibitors are thus chemistries that either prevent the resins from being removed or function in the same manner as these resins.7
Dispersants. Dispersants are the most common form of oilfield chemistry. The surfactant industry is vast, and oil field chemical companies are just a small part of that spectrum. Many of the surfactants manufactured and used in other industries are also used in the oil field. Many of the chemistries manufactured by oilfield chemical companies are similar to surfactant materials used in other industries. A minimal review of the different surfactant types used would entail a much longer presentation. Therefore, a very general discussion with some illustrative examples is all that can be attempted in this setting.
Surfactants function by modifying the chemical interaction of liquids at a surface boundary. Surfactants form the majority of oilfield chemistries. Dispersants are surfactants that prevent the agglomeration and adherence of solids. Based on this, dispersants have efficacy in all oilfield chemistry. They are used in the manufacture of chemistries as well as in formulations of different raw materials throughout product lines. They are used in corrosion inhibition to prevent under-deposit corrosion. They are used to prevent solids from hindering production, whether the solids are from scale, paraffin or asphaltenes. They are also used to treat emulsions related to solids formation or accumulation. Many of the water clarification and emulsion problems in the oil field are a result of the introduction of these materials in the process, either in drilling, workover or production.8
Some commonly used dispersants are sulfonic acids and their salts (Fig. 8), phenolic ethoxylates (Fig. 9), ethoxylated alcohols (Fig. 10), and quaternary ammonium compounds, which are discussed under corrosion control.
CORROSION CONTROL
Corrosion control chemistries function by preventing solids deposition, passivation, a combination of solids prevention and passivation, or by gas scavenging. The mechanisms of these effects can be accomplished by numerous chemistry types. It should also be noted that gas scavenging may be used for environmental or health and safety concerns as well as corrosion.
The molecule types used have an aliphatic tail and a portion that will couple with the corroding metal. This creates a layer of chemical, which prevents electron transfer and interrupts the corrosion cell. Imidazoline is an example, Fig. 11.
In addition, some chemistries function as both passivating agents and solids dispersants. Examples of this chemistry are the quaternary ammonium chlorides, Fig. 12.
There are many other corrosion control chemistries. The latest research is focused around making more environmentally friendly molecules for use in sensitive environments.9
Gas Scavengers. Gas scavenging chemistries consist of inorganic salts of sulfur, nitrogen, or chloride, aldehydes or amine-aldehyde condensates. Sulfites scavenge oxygen as a corrosion control mechanism. Chlorites, nitrites, aldehydes and amine-aldehyde condensates scavenge hydrogen sulfide. A typical aldehyde is acrylaldehyde, Fig. 13. An example of an amine-aldehyde condensate is a triazine, Fig. 14.
When injected, these chemistries function by rearrangement for species that will scavenge hydrogen sulfide.10
DEMULSIFICATION AND CLARIFICATION CHEMISTRIES
Emulsion breaking. Emulsions, defined as water-in-oil emulsions, occur in oil production because of natural emulsifying agents in crude oil and the introduction of other emulsifying agents, like the chemicals identified above. These introduced chemistries address production problems, but cause emulsions due to their surfactant nature. For this reason, emulsion breakers are used in crude oil production. These emulsion breakers function by disrupting the stable surface between the bulk phase (crude oil) and the internal phase (water). It is generally accepted that high molecular weight surfactants will displace lower molecular weight surfactants at a surface boundary. Emulsion breakers are designed to be similar to the emulsifying chemistries, but have significantly higher molecular weight. This allows them to disrupt the surface layer, and destabilize the emulsion.1 There are many chemistry types used as emulsion breakers, but most are alkoxides of phenolic resins, Fig. 15.
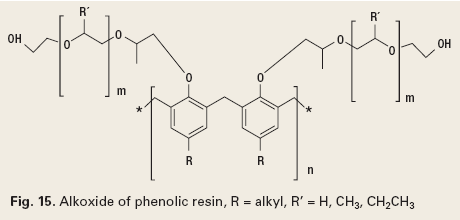 |
Reverse emulsion breaking. Reverse emulsions consist of oil in a continuous phase of water. They are created and stabilized by both physical and chemical means. The oil does not coalesce due to the electrostatic repulsion at the surface boundary between the oil droplets and the water.
The chemistry of reverse breakers allows the coagulation of the oil in the water by bipolar protonation. This means that the surface-active emulsifying agents at the oil and water interface are neutralized. The chemistry must then allow the flocculation, or agglomeration, of the coagulated oil drops. The chemistry types used to accomplish this are metal salts (Fig. 16), addition polymers (Fig. 17), condensation polymers (Fig. 18) and emulsion/ dispersion polymers (Fig. 19).12
WATER CLARIFICATION
Water clarification is the removal of non-complying substances from water prior to disposal. These materials can be solids, gases or liquids. In the oil field, the most common contaminant is crude oil. The oil is removed using a combination of chemistries such as carbamates, Fig. 20, and/or solution polymers and emulsion/ dispersion polymers like those previously mentioned as reverse emulsion breakers.
Chemical programs are designed based on the production criteria at project startup. The solids control and corrosion control chemistries are selected using laboratory procedures prior to being implemented. General ideas for emulsion-breaking chemistry are achieved through inversion testing and EB bottle testing of drillstem fluids. Once production starts, the reverse emulsion breaker and water clarification programs can be selected.
The water clarity is measured after treating the produced water using chemistry-in-bottle testing, bench model float cell testing and jar testing to determine the optimum chemistry. Oil field chemists need to take particular care that the complete program produces discharge water that meets specifications.
The selection of all chemistries plays an important role in the final water quality at the end of the process. In addition, the selection of these necessary chemistries often involves a necessary sacrifice in water quality to avert consequences that are more serious. This results in using additional chemistry to prevent water quality problems.
TREATMENT TRENDS
Research and development of new chemistries for oil field application is driven by commercial constraints. This work can generally be divided into three categories. First, there are programs designed to produce the same chemistries at lower cost. This development work focuses on the manufacturing processes. Second, there are programs to research and develop new chemistry types, or structurally modify existing chemistries, which are designed to perform significantly better on a cost performance basis, i.e. at lower dosages.
Finally, there are research and development programs focused on finding existing or different chemistries to overcome formerly untreatable problems. Examples of this research include those focused on finding environmentally friendly materials for chemical treatment, treating those problems currently being treated stoichiometrically at threshold levels (water soluble organics), and designing multi-functional molecules for chemical treatments that currently use two different molecules.
In addition, oil field chemical companies also researching the fundamental chemical processes at work in oilfield systems. This is done to gain a better understanding of molecule design to increase the value added through oil field chemicals 
REFERENCES
1 Brady, J. E and G. E. Humiston, “General Chemistry, Principles and Structure,” p. 679, John Wiley and Sons, Inc, New York, New York, 1982.
2 Sorbie, K. S. and N. Laing, “How Scale Inhibitors Work: Mechanisms of Selected Barium Sulphate Scale Inhibitors Across a Wide Temperature Range,” SPE paper 87470, Society of Petroleum Engineers, 2004.
3 http://www.champ-tech.com/us/products/scale%20control.asp?P=prob8
4 http://www.pet.hw.ac.uk/research/fast1/research/cheminhi.htm
5 http://www.champ-tech.com/us/products/DiffTech/Low%20Dose%20 Hydrate%20Inhibitors.asp
6 US Patent No. 5,434,323
7 Becker, J. W., “Crude Oil Waxes, Emulsions, and Asphaltenes,” Pennwell, Tulsa, Oklahoma, 1997.
8 Porter, M. R., “Handbook of Surfactants,” 2nd edition, Blackie Academic and Professional, London, England, 1994
9 Endean, H. J., “Oilfield Corrosion Detection and Control,” Champion Technologies, Houston, Texas, 1989
10 Buhaug, J. B., “H2S Scavenging - Chemical Investigations of Triazine and Potential New Scavengers,” AICHE Paper 115e, LNG Treating and Transportation, New Orleans, Louisiana, 2002.
11 Bosch, R.O., et al., “A Novel Approach for Resolving Reverse Emulsions in SAGD Production Systems,” Canadian Journal of Chemical Engineering, v. 82, n. 4, Aug 2004.
THE AUTHORS
|
 |
Ron Bosch is an evaluations team leader in the Technical Support and Development Division of Champion Technologies, a specialty oilfield chemical manufacturer. He has worked in water and oil treatment since 1983, for both Champion and the US Navy.
|
|
 |
Eric Axcell is a section manager for phase separation in the Technical Support and Development Division of Champion Technologies, a specialty oilfield chemical manufacturer. He has held several positions relating to the treatment of oil and water since 1997. Axcell received his BS degree in chemistry from Texas A&M University. He is a member of SPE and the Produced Water Society.
|
|
|
|