Artificial Lift
What’s new in artificial lift
Part 2 – Eighteen new downhole/surface system developments from 10 companies for electrical submersible pumping (ESP) and other artificial-lift operations
James F. Lea and Herald W. Winkler, Texas Tech University, Lubbock, Texas; and Robert E. Snyder, Executive Engineering Editor
Part 1, presented last month, covered 14 recent developments in four categories of artificial-lift technology: beam and progressing cavity pumping (PCP); plunger lift; and gas lift.
This concluding article introduces 18 new developments from 10 companies. Ten of the presentations include new downhole and surface ESP systems. The remaining items cover contributions for various artificial lift and production operation categories, such as: PCP equipment; motor controllers/monitors; and software and instrumentation for well/field management and optimization.
ELECTRICAL SUBMERSIBLE PUMPING
Described here are 10 equipment and instrumentation/software developments including: ESPs to handle gas and viscous fluids; applications in coalbed methane wells; CT-deployed systems; new sensor/control methods; software providing management/optimization opportunities; and ESP testing/repair.
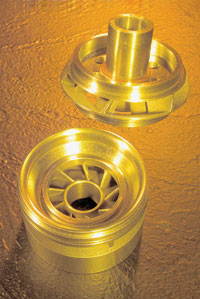 |
Fig. 1. Multi-vane impeller design delivers more head and increased production.
|
|
Multi-vane pump. Centrilift, a division of Baker Hughes, Claremore, Oklahoma, has introduced the MVP multi-vane pump. The new ESP design features a unique, patent-pending impeller that can lift more fluid or reduce horsepower in wells with high gas-to-liquid ratios. The pump handles higher free – gas – content fluids, prevents gas locking and maximizes lift compared to conventional ESP systems.
The improved multi-phase-fluid dynamic design improves performance by producing more free gas through the pump, utilizing the greater number of vanes, Fig. 1. The free gas then lightens the fluid column in the production tubing, reducing total dynamic head (TDH) and required horsepower. Therefore, it can lift more fluid with the same horsepower, or the same amount of fluid with reduced horsepower. In either case, the result is lower power cost per volume of fluid lifted. The pump can be used alone, or employed as a charge pump with a standard ESP. It can also be used in combination with rotary gas separators for high gas applications to reduce intake gas to acceptable levels.
The system can be sized using Centrilift’s Autograph PC sizing and simulating software. MVP performance was measured during development, with extensive testing in the on-site gas test loop facility. In an oil well in the western US, with a GOR greater than 16,000, the system was added to an existing ESP. Well drawdown improved and oil production increased over 75%, to 32 bopd from 18 bopd. At the same time, gas production nearly doubled.
ESP for high-viscosity fluids. VIPER, introduced by Centrilift, is the first and only ESP specifically designed to produce high-viscosity fluids. It features a unique, patent-pending pump stage design with radically different vanes that improve fluid shear and reduce surface friction, Fig. 2. As a result of this breakthrough technology, the pump optimizes production in wells with high-viscosity fluids. The design reduces power requirements and maximizes lift, compared to conventional ESP systems. It employs an inducer that improves fluid shear at the pump intake, and larger vane openings in the impellers to reduce internal friction. The result is higher total dynamic head, improved efficiency, and a lower horsepower requirement.
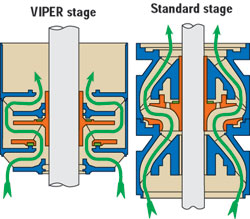 |
Fig. 2. The VIPER stage improves fluid shear with a shorter fluid path.
|
|
The technology gives operators a choice: it can lift more fluid with the same horsepower, or lift the same amount of fluid with reduced horsepower. In either case, the result is lower power cost per volume of fluid lifted. The system is designed to significantly improve ESP performance in high-viscosity fluids. As viscosity increases, performance improves, compared to conventional ESP technology. Performance of the ESP in adjustable-fluid-viscosity applications was measured in Centrilift’s test loop facility, allowing design optimization.
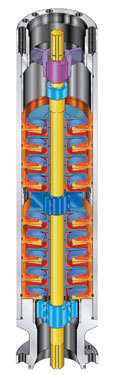 |
Fig. 3. Cutaway of new TD460 pump shows wider- vane- opening stages.
|
|
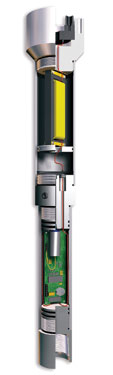 |
Fig. 4. Cross-section of SmartGuard downhole sensor to measure critical ESP performance data.
|
|
Wider-vane-opening pumps. Wood Group ESP, Inc. (WGESP), Oklahoma City, Oklahoma, offers two new, higher-efficiency, wider-vane-opening pumps that have recently been incorporated into its 400-series product line, the TD150 and TD460. In a commitment to continual improvement, the company has replaced one of its high-usage pumps with more-efficient stages. The new pump called TD460 offers wider-vane-opening stages which can help produce lower-gravity fluid, handle more gas and reduce the effects of scaling, Fig. 3. The ESP’s stages have highest efficiency and head per stage in its class in the industry.
Horsepower requirements for TD460 stages are about 15 – 22% less, compared to existing stages offered by different manufacturers in the 450-bpd range. Due to its high head coefficient, it requires fewer stages to generate the same lift. Development of TD460 was preceded by TD150 stages, which also had wider-vane-opening stages. Together with TD150, TD300 and TD460, WGESP offers a large choice for wider-vane-opening stages for 400-series pumps.
Downhole sensor with surface interface. Wood Group ESP, Inc., offers the SmartGuard, a downhole sensor and surface interface system for reliable, accurate, real-time monitoring of ESPs and reservoir conditions, Fig. 4. Operators should expect reliable information about equipment performance and vital downhole conditions. Now, a new family of monitoring systems can reliably/accurately track and retrieve real-time information related to critical performance parameters. Output control loads that respond to selected inputs are also available. This can lead to lower operating costs and longer run times.
Employing the latest state-of-the-art transducer technology and advanced linear calibrations, this new-generation monitoring system surpasses conventional pressure and temperature sensors. Engineers designed the sensor to be oilfield-rugged with no moving parts to wear out. It is resistant to vibration and has been field-proven. The strain-gauge technology used for pressure monitoring is robust and accurate. Wellbore, motor oil and motor winding temperatures are measured via platinum resistance temperature detectors (RTDs) and Type J thermocouples. The technology improves the accuracy/resolution of pressure/temperature data with 0.1% pressure accuracy and 0.6% downhole temperature accuracy. The system is programmable to sample data continuously with selectable recording capabilities.
New sensor technology. Schlumberger (Reda), Bartlesville, Oklahoma, has developed new sensor technology for coiled tubing – deployed ESPs. To further enhance the benefits of RedaCoil, the patented technology utilizing power cable inside the coil tubing, the company now offers real-time sensor data as part of the system. Like standard ESP monitors, the sensor transmits real-time data to surface through the power cable, Fig. 5. Data such as intake pressure/temperature, discharge pressure, motor winding temperature, vibration and current leakage data are collected. Once data arrives at surface, it can be transmitted, with other surface data, to any PC in the world through Schlumberger’s InterAct process.
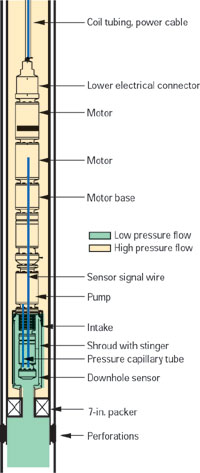 |
Fig. 5. Downhole sensor sends data to surface through power cable inside coiled tubing.
|
|
CT-deployed ESP. In many applications, it is not possible to flow production up the coiled tubing due to the high flowrates – up to 30,000 bpd in 7-in. casing – produced by some ESPs. Now, Schlumberger provides the patented CrossFlow system, coiled tubing – deployed ESP, for many difficult applications, Fig. 6. With the system, high-flowrate wells can be produced, as the system does not have fluids produced up the coiled tubing. For wells with high volumes of free gas, the system can incorporate the company’s high-flowrate gas separators.
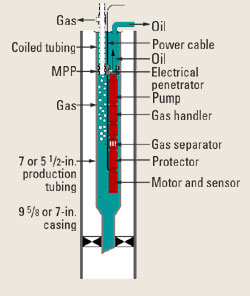 |
Fig. 6. Schematic of CrossFlow system for CT-deployed ESPs.
|
|
High viscosity oils can reportedly be produced more easily with the system and the number of pump stages are lowered by not pumping high-viscosity oil and emulsions up the CT. Access to the reservoir, and well treatment, is possible without retrieving the CT-deployed ESP. And the SPOOLABLE gas lift system, described in Part 1, can now be added to the CT-deployed ESP, providing back-up in case of ESP failure, or used in conjunction with the ESP to lower HP and fluid-lifting requirements.
Eliminating harmonic problems. With the release of Sine Wave Drive, Schlumberger provides technology that can eliminate harmonic problems on both the load side and line side of ESP applications. The new drive combines a built-in filter with advanced pulsed-width, modulation-VSD technology to provide near-sinusoidal current and voltage waveforms to the ESP motor, Fig. 7.
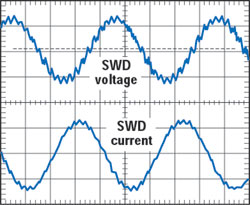 |
Fig. 7. New Sine Wave Drive provides near sinusoidal current/voltage waveforms to ESP motor.
|
|
The filter does not require any application-specific tuning or adjustment, making the system applicable for land-based VSD operations, which are commonly moved to multiple locations. Offshore operators will be pleased with the minimized footprint achieved by incorporating the filter section in the base of the system and not adding additional footprint or ancillary devices. Load-side harmonics and power issues are addressed with diode technology on the drive input. Use of diode front ends allow for line-side filters to effectively eliminate harmonics over the various operating frequency ranges desired in ESP operations.
Pump-monitoring system. Weatherford Artificial Lift Systems, Houston, has expanded its ESP range, adding a combined downhole ESP sensor and switchboard/variable speed drive motor controller. This rugged, downhole ESP sensor is attached at the rig site to the ESP motor and communicates well pressure/temperature and motor-winding temperature, vibration (two planes) and insulation quality to the surface using the ESP power cable, Fig. 8.
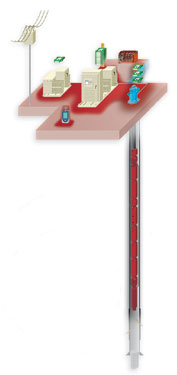 |
Fig. 8. Downhole ESP sensor and surface controller system.
|
|
At the surface, all high-voltage equipment is integrated within an existing switchboard, transformer or the Weatherford 2MV5. Fitted to the switchboard or variable speed drive, the New Weatherford Artificial Lift controller (a component of the system) for the first time combines all functions of a motor control, data logging unit and human machine interface for both downhole sensor data and motor running parameters. No separate motor controller is required.
The sensor is designed for in-country field re-dress and upgrade. Field upgrades may be optionally factory fitted. Available upgrades include discharge-pressure measurement and reservoir quality monitoring using a quartz sensor for well pressure. The surface controller is a complete Modbus-based unit with a flexible architecture to allow unlimited analog and digital input/output to be added. PC and PocketPC software is supplied. In addition, by using the company’s management software, this system handles all the data received and allows for easy utilization of the logged data.
ESP for coalbed gas wells. The coalbed methane gas industry has attempted to use ESPs to deliquify CB gas wells, with limited success. Weatherford determined that a new approach was needed that: offered extended run times, was cost effective, repairable and fully automated. As ESP pumps held the most potential for CB gas applications, the company focused on adapting its technology for these unique situations and created the patented CBM-ESP pump. The pump works in deep or shallow wells, with low or high water volumes, over a wide range of pressures/temperatures.
Three main operating challenges are: handling large and varying amounts of gases, dealing with abrasive coal fines, and rapid water decline accompanied by rapid gas increase. When pumping begins, these problems must either be diverted from, or handled by, the pump. A special effort was made to design a submersible pump that was easy to repair.
The new pump can be manufactured in many different types of gas-shrouding configurations to handle gassy fluids. These shrouds divert gas from around the pump and allow it to flow up the wellbore, Fig. 9. The tapered design compresses gas that enters the pump so that it passes into the liquid phase and is produced. The system uses compression stages that help with low-fluid-producing wells. And the pump is built with hardened shafts and support bearings that are tolerant of abrasive particles – unique intake screens capture/divert many of these fines.
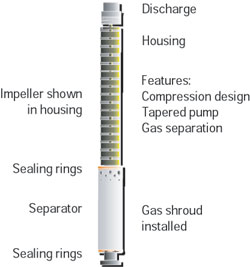 |
Fig. 9. Principal components of coalbed methane liquid removal ESP system.
|
|
ESP testing/reconditioning. Independent Testing Services of Midland, Texas, offers submersible equipment testing services to production operators in the Permian basin to help lower submersible pumping systems costs. For pumps, the service provides cleanup, acidizing and chemical cleanup. Once cleaned, each pump section is computer tested utilizing a horizontal test bench, Fig. 10. Test results are compared to the manufacturer’s performance curve. Over 65% of the used pumps test within satisfactory limits and require no expensive repairs.
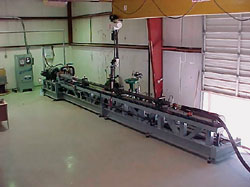 |
Fig. 10. Facility for testing/reconditioning ESP equipment.
|
|
For motors, a series of tests determine if motor insulation is dry and suitable for rerun. And a series of tests on the protector/seal section – including a load test on the thrust bearing and pressure tests across the mechanical seals – can be done. ITS provides an inventory stocking system for production companies to store their used equipment at no charge, along with providing adapters to enable operators to mix and match different manufacturers’ equipment. This allows operators to maximize the use of surplus inventory and lower the cost of equipment to be utilized. Minor repair on all types of equipment is also provided.
MISCELLANEOUS
Eight items under this category include support hardware for PCPs and capillary injection, plus advances in instrumentation and control with new sensors/software applications that stress ability to analyze artificial-lift performance as part of optimum well and field control/management.
Driveheads for rod-driven PCPs. The primary purposes of driveheads are to support a prime mover, provide a seal to contain well fluids, support the sucker rod string, provide safe control of rod recoil and to transfer energy from the prime mover to the rod string. Centrilift now markets the LIFTEQ line of driveheads for rod-driven PCPs (RDPCPs). The series is available in various configurations that support up to 300 hp. Safety features include hydraulic back-spin control that automatically regulates the speed of sucker rod recoil. Five models are offered for ratings of 50 to 300 hp. The LT100E, LT150E and LT300E share the same frame and can be configured in the field to match changing production requirements. Fig. 11 illustrates the LT150E model.
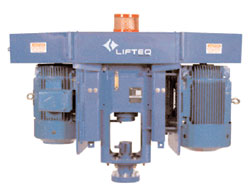 |
Fig. 11. LT150E drivehead for rod-driven PCPs.
|
|
Variable speed drives for PCPs. With the Electrospeed GCS and Electrospeed PC, Centrilift now supplies a complete line of variable speed drives (VSDs) to meet the needs of all LIFTEQ RDPCP and ESPCP systems. The PC model is designed primarily for RDPCP systems up to 125 hp. It features direct torque control (DTC), a motor control that allows control of both speed and torque without pulse encoder feedback. The GCS model will control systems of 100 hp and greater, Fig. 12. The GCS features the graphic control system for ease of use. The VFDs will shut down the system when conditions develop that could damage the pump. They operate with surface or downhole instrumentation. If neither of these is connected, the driver will operate based on motor torque.
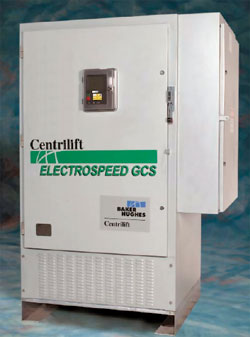 |
Fig. 12. The Electrospeed GCS features a graphic control system for ease of use.
|
|
Doppler-effect fluid level finder. Wilson, Houston, Texas, a business unit of Smith International, is introducing a revolutionary, patented fluid-level control system called the FM1100, in conjunction with the Wilson VFD1000, Fig. 13. This system will give the operator the ability to monitor and control the fluid level in many wells on a real-time basis without need for any downhole sensors. It will use multiple sensors highlighted by doppler-effect radar to measure empty space in the well annulus. A frequency generator creates doppler-frequency waves in the annulus; the wave harmonics change form as the fluid level changes. A system of highly sensitive sensors at the surface recognizes the harmonic changes and sends the data to a processor, which creates a fluid column height on a real-time basis.
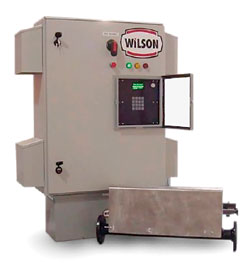 |
Fig. 13. Fluid level finder using doppler-effect radar.
|
|
This system can be utilized with standard rod pump, PCP and ESP systems. In standard rod pump applications, it can be utilized to set shut-down and start-up fluid levels. In both PCPs and ESPs, the system can be utilized with the VFD to maintain a constant fluid level by changing the motor speed. As a reservoir management tool, it can monitor fluid level changes in producers as injection rates change in supporting injection wells. The system will also monitor flowrate, temperature, pressure, amperage, and actually optimize the fluid level to maximize production.
New motor/capacitor combination. A new tool for engineers is projected to lower electrical costs. Electrical power is a major economic factor in mature oil fields and is often the greatest single cost for upstream operations. Low VA-efficiency motors, characterized by low power factor and low efficiency, contribute to high electrical costs. NEMA D, high-slip, high-torque motors characteristically used in beam pump applications exhibit low efficiency and low power factor. Annual operating costs for these motors can be 50 times their installed cost. Thus, transmission, reception and power conversion inefficiency adds up to the high electrical cost of production.
Load-based solutions can significantly reduce electrical costs. However, frequent phase-leg losses and variably cyclic beam-pump loads are generally incompatible with load-based shunt capacitors. PACCAP, Inc., of Odessa, Texas, is developing a new set of load-based solutions. It has developed a new capacitor implementation. These durable, continuous duty electrolytic capacitors provide AC capacitor size reduction. They are suitable for series applications. Series capacitors, Fig. 14, provide voltage support, and power factor correction. They allow and require optimal electrical motor designs. Financial payback is targeted at one year, but will vary with electricity cost, utility billing practice, annual run time and motor designs.
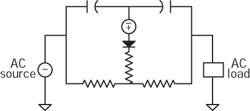 |
Fig. 14. Biased anti-series capacitors.
|
|
Capillary string application. In the past, operators have had limited methods to determine proper applications for capillary tubing. Recent software developments, at Dyna Coil Inc. and Stim Coil Inc., Kilgore, Texas, have dramatically reduced the risk of installing a capillary string, Fig. 15, and achieving an economic return. Dyna-Soft uses many factors to evaluate a well’s performance and determine if a given well would benefit from a capillary string to solve the problems of fluid loading. The software can also aid in determining useful life of a capillary system to a given well. Presently, the new software is achieving a success rate of 96% on screening for candidate-selection criteria.
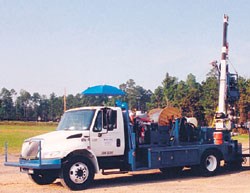 |
Fig. 15. Delivering/installing capillary-string tools.
|
|
Adjustable back-pressure valves. Operators now have the benefit of using an adjustable back-pressure valve. For capillary injections from a surface pump, many operators have had difficulty keeping the string completely loaded. The typical hydrostatic head of a fully loaded string exceeds the bottomhole pressure of these fluid-loaded wells. Since the surface pumps are typically intermittent in operation, the fluid in the string has a tendency to run out of the string during the off cycle of the pump. This continual gravity unloading often leads to a loss of prime production and waste of chemicals.
The new, patent-pending adjustable back-pressure valves from Dyna Coil Inc. can be pre-set to a known pressure and prevent gravity unloading. An additional benefit prevents contaminants from entering the string from the bottom and causing plugging. The valves are manufactured from several noble alloys for task-specific applications. The dimensions of the valves are the same as the standard injection mandrels, 5/8- and 3/4-in. OD.
Integrating real-time surveillance. Case Services, Inc., Houston, Texas, has recently introduced LOWIS (Life of Well Information Software), its latest suite of web-enabled software applications designed to seamlessly link the different processes used in oil/gas production operations through a common interface. The software assists oil/gas producers in identifying opportunities for production improvement and cost savings throughout the life of a well by combining real-time well monitoring and production optimization functionality with well-service planning, workover histories and evaluation of past service events. With the ability to store this data in its own database, or provide access to any necessary data from a number of data sources already in place, extracting value from the data in a productive manner is simplified.
It eliminates need for production data users having to perform complex database queries and repetitive data quality checks. And it simplifies opportunity recognition by organizing the continual operational improvement process into a logical workflow. Some tools available in the product that facilitate the improvement process include: flexible graphing and charting tools, pre-built work-planning templates that can be easily modified, integrated wellbore sketches detailing equipment changes over time, AFE status summaries, links to document, bitmap and JPEG files, and review summaries detailing well service effectiveness.
Using the software, an operator can now work through a single software interface to diagnose and identify lift performance problems, prioritize and schedule well service work to remedy those problems, and establish best practices and procedures by reviewing well-work results. The system is scaleable to be deployed as a large, enterprise-wide system for a major E&P company or serve as a stand-alone system for a single field or small independent.
Improved pressure transient data. Echometer Co., Wichita Falls, Texas, has implemented enhanced pressure transducer technology to eliminate measured casing pressure changes caused by the pressure transducer being sensitive to changes in daily temperature. Use of high-speed, portable notebook computers, state-of-the-art, sigma-delta modulation, analog-to-digital converters and modern sensors allows the acquisition of pressure, load, acoustic signals, acceleration, motor power, motor current and other data with greater accuracy than previously possible. Modern sigma-delta, analog-to-digital converters have a resolution better than one part in a million at data-acquisition rates commonly used in oilfield analysis. Pressure transient (PT) analysis is the primary beneficiary of this new enhanced technology.
PT data was acquired on a well using a pressure transducer with the enhanced technology. The data was collected over a period of 4.9 days. Over the duration of the PT tests, data plots show maximum temperature peaks during the day and minimum temperature valleys at night. Fig. 16 displays the casing pressure measured during the test, but no or unnoticeable, pressure swings caused by daily temperature change due to heating during the day and cooling during the night. 
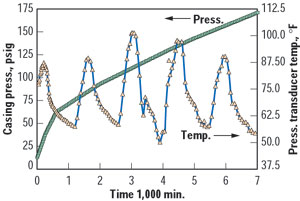 |
Fig. 16. Pressure transient data collected using enhanced technology.
|
|
THE AUTHORS
|
|
James F. Lea, Professor, Chairman of Petroleum Engineering, Texas Tech University, Lubbock, holds BS/MS degrees in ME from the University of Arkansas, and a PhD in ME from Southern Methodist University. He worked for Sun Oil Co. as a research engineer from 1970 to 1975; from 1975 to 1978, he taught engineering at the University of Arkansas; and from 1979 to 1999, he was leader of optimization and artificial lift at Amoco EPTG. He assumed his present position in 1999. Mr. Lea is a registered professional engineer in Texas; he has authored/co-authored several patents, as well as publications on artificial lift.
|
|
Herald W. Winkler is former chairman, now professor emeritus and research associate, in the Department of Petroleum Engineering at Texas Tech University in Lubbock, Texas. He is presently working as a consultant in artificial lift, specializing in gas lift.
|
|
|
|
Part 1 |
|
|