When electric meets intelligence: Powering a new era in hydraulic fracturing
Halliburton has launched a series of novel technologies specifically designed to upgrade hydraulic fracturing operations. The company’s ZEUS electric fracturing system lowers emissions, slashes fuel costs and amplifies efficiency to drive down the total cost of ownership for operators. The Octiv intelligent fracturing platform has made the digital frac site a reality by enabling automation across our entire fracturing business—driving increased reliability and consistency in operations.
In the subsurface, our SmartFleet fracture monitoring system is changing the way our customers see and evaluate fracture performance, through real-time, actionable insights that optimize fracture designs and recovery. Electrification, automation, and real-time optimization—together these services usher in a new era in hydraulic fracturing that maximizes efficiency and performance while lowering the total cost of ownership for operators.
Making the switch to electric fracturing. A combination of factors has driven the increase in adoption of electric fracturing. First, the industry has committed to lower emissions through cleaner, more efficient frac operations. By eliminating diesel, operators achieve significant cost savings. Finally, the industry’s constant focus on efficiency further fuels demand for electric fracturing.
From the frac spread to the wireline unit, the ZEUS electric fracturing system delivers differentiated value on each of these drivers. It offers an integrated, all-electric frac site that lowers emissions, reduces fuel costs, and maximizes efficiency gains for our customers. In terms of lower emissions, the system offers flexibility and compatibility across multiple sources, including reciprocating engines, micro grids and grid power. Each of these power solutions results in lower emissions, compared to diesel and dual-fuel operations.
When powered by the grid, the ZEUS system can reduce overall emissions up to an estimated 45%, compared to Tier 2 diesel engines.1 When grid power is unavailable, reciprocating engines provide operators with mobile power generation, proven to deliver reliability, consume less fuel, and create fewer emissions, compared to other mobile power sources. While using reciprocation engines, the system reduces overall emissions by up to an estimated 30%, compared to Tier 2 diesel engines. The power density provided by reciprocating engines also allows operators to scale power supply to meet their specific job design, eliminating the need to pay for unused, stranded power.
In addition to lower emissions, electric fracturing significantly reduces fuel costs. During a simul-frac operation, the system can displace more than 900,000 gal of diesel per month or 11 million gal annually.2
Halliburton’s ZEUS system offers operators a differentiated value proposition, which reduces dollars spent per completed lateral foot. With the reliability and efficiency of its electric power train, it sets a new standard in managing increased service intensity. Every ZEUS pumping unit can achieve up to 5,000 HHP consistently, allowing operators to pump higher rates, using half the equipment necessary.
The electric power train provides faster rate response and more precise control. An electric system also eliminates non-productive time associated with diesel engines, transmissions and hydraulics. The company engineered the ZEUS system for high-service-intensity frac operations, with the ability to pump higher volumes, rates and pressures, right out of the box. The systems’ proven track record includes pumping more than 500 hrs in the first 30 days of operations for multiple operators across North America.
Halliburton’s success results not only from the ZEUS system, but also from the performance of its field crews and electrical teams, including the engineers that maintain the portfolio of leading technical solutions; the experts that evaluate unique power generation challenges; and the certified power distribution technicians at each electric fracturing job site. The result is an electric fracturing system that has delivered an average of 30% faster transition times and 11% more HHP hours pumped per month—this means more pumping hours, more lateral feet completed, and more cost savings for operators.
Frac automation: The new norm. Today’s frac site is more complex than just a few years ago. Crews need to monitor thousands of variables, manage thousands of control setpoints across equipment, and coordinate the exchange of information between systems, crews and operators—all to pump a single frac stage. These complex operations need intelligent systems that streamline and simplify operations, making them more efficient, reliable and consistent. This is what we have achieved through our Octiv intelligent fracturing platform.

Our entire U.S. land frac fleet has been upgraded with the Octiv platform. It has transformed our business to operate with automatically controlled and digitally integrated machines that optimize how we run our operations. The platform is more than simple task automation. It is built on three fundamental pillars: 1) spread automation; 2) digital operations; and 3) remote connectivity, Fig. 1. At its core is spread automation, which has transformed the way we run our frac fleet. Gone are the days of controlling frac pumps and blending equipment individually. With the platform, we conduct an entire frac spread as a single, fully automated system that delivers greater equipment reliability and operational efficiency.
By integrating with thousands of sensors across a spread, the Octiv platform helps ensure operations are executed to plan while running equipment at optimal levels for increased reliability and extended equipment life. Every day, across every well site, we are automating thousands of commands to control our equipment. This has reduced 95% of personnel touchpoints that can result in human error or variability during fracture execution. In doing so, the platform consistently optimizes how our equipment is run.
For example, it has reduced pump cavitation by up to 26%, resulting in longer pumping intervals between maintenance. We have also reduced infant failures in our equipment by eliminating the root cause of those failures—making our equipment more reliable. Using the platform, we can predict failures before they occur, thus extending the life of major components, including fluid ends, engines and transmissions.
The Octiv platform does more than just spread automation. Through digital operations, it connects people, processes and equipment, simplifying how we work every day. By streamlining workflows to control the spread, process data, and manage inventory, the platform maximizes our efficiency and performance at the wellsite.
However, the platform isn’t just changing how we operate. It helps our customers optimize their operations as well. Through the Octiv Connect remote operations portal, Halliburton introduces a new level of transparency that connects the frac site to the cloud, allowing our customers to interact with operations easier and faster than ever before. It provides instant visibility into job progress and analytics, while enabling collaboration on each design change, every stage, every well, across every asset.
In our industry, we often speak about automation, digital operations, and remote connectivity as separate, individual capabilities. Through the Octiv platform, we have integrated these capabilities into a single platform that optimizes how we run our business, how we execute our frac operations, and how operators control their assets. But this type of intelligent control doesn’t stop at the surface. It goes deeper.
Fracture monitoring, simplified. In unconventional shale, operators want to maximize return on capital, improve cash flow, and meet well performance expectations. However, only 2% of completion stages in North America are monitored. This results in high uncertainty and variability around completion outcomes versus its design and leads to variability in the performance of the asset.
The historical approach to answering these challenges consists of indirect subsurface measurements that lead to decisions based on uncertainty, and drawn-out processes across numerous wells to evaluate and validate performance effectively. Although permanent, distributed, fiber optic sensing is one of the most trusted fracture monitoring technologies for evaluating fracture performance and well interactions, the complexity during execution limits its usefulness across large-scale programs with hundreds of wells. The SmartFleet system combines a variety of downhole sensors, measurements and visualization into a single fracture monitoring system that lets you observe fracture performance in real time across the entire program.
SmartFleet also simultaneously provides measurements of fluid distribution along the treatment wellbore and interactions of the generated fractures with offset wells. With live visualization of fracture behavior, operators can measure interstage communication, effective stage distribution, fracture azimuth, growth rate and inter-bench communication. Ultimately, understanding fracture behavior enables the operator to ensure performance and control the completion’s interaction with the reservoir.
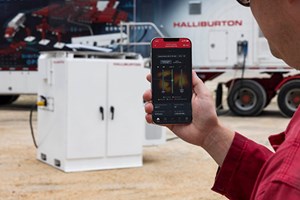
SmartFleet incorporates minimally intrusive diagnostics, such as the ExpressFiber disposable fiber service, enabling routine fracture monitoring. It also keeps you connected on the go with a mobile app that provides real-time access to fracture performance anytime, anywhere, Fig. 2. The fracture monitoring service is an operator's link to the subsurface. It allows them to take fracture monitoring to scale by giving them access to the actionable insight they want, minus the operational complexity.
With the SmartFleet system, we have simplified how to acquire, process, and streamline data, enabling operators to gain insights on every pad in real-time, without interfering with the existing operation. Using cloud processing, digital deliverability, remote connectivity, and data automation, operators can quickly and easily understand fracture performance and take control of their fracture outcomes. The systems’ ease of use and 10 times lower total cost of ownership, compared to permanent fiber, is why we continue to see repeat business from the majority of our system users.
Using SmartFleet to diagnose fracture geometry during simul-frac operations. An operator recently used the SmartFleet fracture monitoring system to diagnose fracture geometry during simul-frac operations. Simul-frac is a growing effort to improve operational efficiency but implies execution changes to both the surface and subsurface. In certain areas, it can be challenging to understand these changes given the numerous bedding planes, barriers, and other heterogeneities. By offering visibility of the generated fractures in real time on a pad level, the system can solve this challenge.
The SmartFleet system measured far-field fracture-induced strain and microseismic activity. These real-time insights diagnosed several completion techniques to differentiate how changes in completion design affected fracture geometry. The tests included changes in perforation friction, cluster count, slurry volume, and simul-frac operations.
During the 23-day pad, continuous fiber measurements provided live diagnostic results. The operator validated which simul-frac treatments communicated with observation wells and determined how the total treatment fluid volume influenced fracture growth and communication to offset wells.
These real-time insights can help drive design improvements, such as adjusting stage length while maintaining uniformity, optimizing perf designs, improving time to rate and breakdown, adjusting proppant schedules to reduce pump time, and identifying impacts of well sequencing.
Using SmartFleet to understand parent-child relationships. Many E&P companies seek avenues to maximize recovery from both parent and child wells utilizing various completion and asset development strategies. In the past, operators have relied on surface pressure measurements to characterize fracture behavior. These point sensors provide a limited understanding of the volume to the first response. On the other hand, distributed fiber optic strain measurements can pinpoint the overall extent of fracture coverage from offset fracs to distinguish interaction pathways and multiple fracture responses from individual treatments. In addition, processed fiber optic data simultaneously generate a microseismic map in three-dimensional space, providing growth behavior of the far-field fracture network.
On a recent operation, the SmartFleet system monitored fracture behavior across three adjacent well pads and eight simultaneous disposable fibers. This was the largest cross-well project for the system to date and resulted in no operational interference or disruptions to efficiency.
The monitor wells and offset treatment wells were landed across five different benches of varying depths. Each of the treatment wells was treated as a simul-frac zipper, with individual well pairs treated concurrent to one another. Offset microseismic activity was gathered and processed from four of the eight monitoring wells, alongside offset strain activity from all eight fiber-optic monitoring wells.
The project’s key objective was to understand the impact of offset depletion and to optimize fluid loading to mitigate any negative production impact from child wells. To understand fracture containment, the team mapped the strain response from the various benches within the high and low lateral elevations. Then, they evaluated the strain coverage across each monitor well to understand fracture growth rate and far-field complexity. The system detected and mapped over 600 fracture interactions and 20,000 microseismic events throughout the project. These results accelerated the learning curve, allowing the operator to adjust their assumptions while optimizing data-driven decisions on future developments.
Charting a new benchmark in performance. In this new era of hydraulic fracturing, the convergence of technology, service quality and diagnostics is propelling the industry towards unparalleled efficiency and also establishes a new benchmark for performance. Through the adoption of electric fracturing, Halliburton moves beyond conventional boundaries to lower emissions, reduce fuel costs and enhance operational efficiency.
Complimenting this with intelligent automation, Halliburton redefines the approach and execution of fracture operations by making them more reliable and consistent. By further simplifying the way we evaluate and understand the subsurface, we can empower more operators with real-time insights that contribute to increased recovery. As the industry navigates this transformative landscape, the combination of these elements becomes the cornerstone, paving the way for an energy future defined by sustainability, reliability and performance.
REFERENCES
- Estimates based on the ERCOT grid.
- Simul-Frac example, based on 160 bpm, 8,500 psi, 500 pumping hours per month.
Lead photo: The new ZEUS electric pumping system is the industry’s first pumping unit capable of achieving sustained activity at 5,000 hydraulic horsepower.
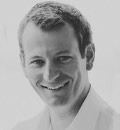
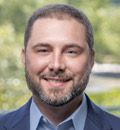
- Shale technology: Bayesian variable pressure decline-curve analysis for shale gas wells (March 2024)
- U.S. oil and natural gas production hits record highs (February 2024)
- Next-generation electric fracturing system improves efficiency, ESG performance (January 2024)
- Going global with unconventionals (December 2023)
- Singlet oxygen-generating treatment technology achieves sustainable operations, helps operators meet production goals (November 2023)
- Rig electrification drives down emissions, bolsters efficiency while improving onshore drilling economics (October 2023)
- Applying ultra-deep LWD resistivity technology successfully in a SAGD operation (May 2019)
- Adoption of wireless intelligent completions advances (May 2019)
- Majors double down as takeaway crunch eases (April 2019)
- What’s new in well logging and formation evaluation (April 2019)
- Qualification of a 20,000-psi subsea BOP: A collaborative approach (February 2019)
- ConocoPhillips’ Greg Leveille sees rapid trajectory of technical advancement continuing (February 2019)