Drilling advances
Automated mud testing far from a pipe dream
Not so long ago, I visited with the long-retired head of a former mud company, who recalled how in the early 1970s his particular side of the industry went through a dramatic metamorphosis insofar as hiring practices were concerned. Back then, gender equality had become all the rage and many of the companies began employing and training mud engineers of the female persuasion. He remembered one such engineer in this male-dominated profession, who, while highly capable and seemingly dedicated to her craft, resigned abruptly. In order to root out any hint of discrimination, he flew her to the head office and asked why she had quit so suddenly. No, she said, the company was fine, she had no problems whatsoever with her co-workers or the rig crew and the pay was very acceptable. “Well, then why are you leaving?” he asked, a tad bit confused, to which she replied, “Sir, this job is not fit for a woman. Not fit for a man either.” Over the years, I’ve had the opportunity to tag along with any number of drilling fluid engineers (“mud men” is so 60s), including a couple of days spent on a rig off Equatorial Guinea, which is a story unto itself. In many ways I agree with her assessment. As most of you well know, their daily routine can be quite tedious, dirty and, when things aren’t going so good downhole, a little bit stressful. By the same token, many of the men, er persons, who’ve been checking drilling fluid properties for years, have told me there is no job they’d rather be doing. Nevertheless, if some of the drilling fluid companies have their way, these engineers could swap coveralls and hard hats for khaki pants and shirts and carry out their often monotonous assignments in a clean, comfy office onshore. That would appear to be a considerable step up from trekking a few times a day from the pit to the mud lab where rheological profiles and other fluid properties are analyzed, often with testing equipment and techniques that have changed little over five decades or so. With the full support of operators, who have forever, it seems, sought ways to reduce the number of rigsite personnel, drilling fluid providers are looking more closely at automated real-time monitoring of key drilling fluid properties. In recent years, drilling fluid providers like M-I SWACO and Baroid have made impressive strides toward making this ambitious objective a reality, developing myriad automated fluid monitoring technologies designed to not only continuously measure fluid properties while drilling, but do so with far more precision than that afforded with manual testing. A number of projects have been initiated over the years to develop the discrete sensor packages critical for automating rig-based drilling fluid engineering. One of the more ballyhooed endeavors was the European THERMIE project in the early 1990s, which operators and drilling fluid companies jointly sponsored. The project managed to develop a number of automated technologies that were recognized as quite ingenious at the time. All the same, none of those purported ingenious developments were ever commercialized, thanks largely to an absence of the high-speed data transmission and interpretation capabilities required to get the collected fluid information from the rig to the onshore operations centers that were starting to spring up, particularly along the North Sea and Gulf of Mexico. There, operators can monitor drilling activities from rigs working much farther away. Subsequent advancements in high-speed data transmission capable of trans-porting large sets of information re-energized the automation development efforts. What’s more, technically demanding drilling environments such as deepwater, with often narrow fracture and pressure gradients, extended-reach wellbores, slim-hole wells and other challenging applications, mandated much more frequent and accurate data measurements than those humanly possible with manual testing. Typically, the active drilling fluid system is only checked two to four times over a 24-hour period, meaning by the time properties are tested and analyzed the data does not reflect the fluid’s current condition. This could prove inefficient and hazardous if serious downhole problems were to occur in the meantime. M-I SWACO has been working on automated fluids measurement for the better part of a decade and recently introduced an array of sensor packages for automatically monitoring fluid parameters, including density and temperature, oil-base mud electrical stability, multi-temperature rheological properties, X-ray fluorescence elemental analysis to replace traditional titrations and retorting, solids content and others. Schlumberger says it has completed yard tests and is now evaluating the all-inclusive automated fluid measurement system in the field with trials underway on a semisubmersible and platform in the North Sea. Halliburton’s Baroid, meanwhile, introduced its Real-Time Density Viscosity system early last year, which is described as a fully-automated unit that measures the density and six-speed rheology of drilling fluids. The system is installed near the mud tanks where measurements are performed at an average frequency of one test every 20 minutes with the ensuing collected by the company’s Insite data acquisition system. Both of the companies contend automated real-time systems not only produce data that is much more accurate than physically collecting and analyzing a fluid sample, but likewise is much safer and healthier. They point to the chemicals and vapors that drilling fluid engineers are exposed to everyday in the lab, not to mention the explosion risks when using high-pressure testing equipment. All of this leaves me thinking what’s next. Could robotic drillers and computerized mechanics be far behind? |
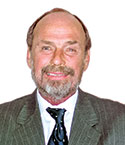
- Coiled tubing drilling’s role in the energy transition (March 2024)
- Using data to create new completion efficiencies (February 2024)
- Digital tool kit enhances real-time decision-making to improve drilling efficiency and performance (February 2024)
- E&P outside the U.S. maintains a disciplined pace (February 2024)
- Prices and governmental policies combine to stymie Canadian upstream growth (February 2024)
- U.S. operators reduce activity as crude prices plunge (February 2024)
- Applying ultra-deep LWD resistivity technology successfully in a SAGD operation (May 2019)
- Adoption of wireless intelligent completions advances (May 2019)
- Majors double down as takeaway crunch eases (April 2019)
- What’s new in well logging and formation evaluation (April 2019)
- Qualification of a 20,000-psi subsea BOP: A collaborative approach (February 2019)
- ConocoPhillips’ Greg Leveille sees rapid trajectory of technical advancement continuing (February 2019)