GRANT THOMPSON, RICHARD PATTERSON and JIM SLOAN, Baker Hughes
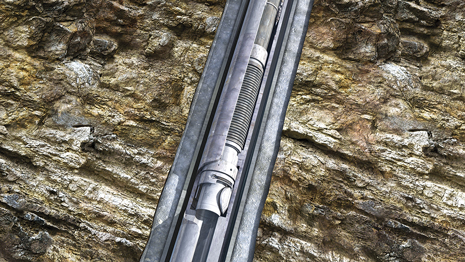 |
HPHT safety valve from Baker Hughes handles working pressures up to 25,000 psi and operating temperatures to 450°F for shallow set to ultra-deep applications. |
|
The number of high-pressure/high-temperature (HPHT) projects has increased significantly over the past couple of decades. Advances in drilling and completion technologies allow for extreme HPHT applications to be commercially viable. Increased customer collaboration with key operators, combined with significant investment by service companies in technology innovation, will commercialize products that make ultra-HPHT a reality in the not-too-distant future.
While there is a minimum industry-accepted designation of 15,000 psi as “high pressure,” and 350°F as “high temperature,” companies have widely accepted a tier structure for HPHT applications that categorizes these tiers, and provides detail to the limitations of completion technology within each, Fig. 1.
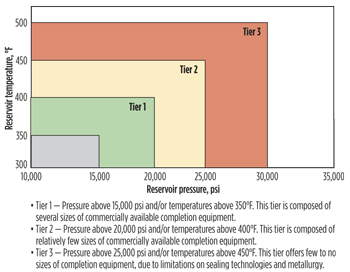 |
Fig. 1. Tier structure for HPHT applications. |
|
The HPHT tier technology limit designation serves to alert operators and manufacturers, alike, that equipment for such use requires a higher level of attention to adhere to new recommended industry practices with respect to design, qualification and testing. For example, additional focus is now considered for cyclic loading, internal and external loads, thermal gradients, system analysis and fatigue. Also, additional validation testing requirements are being considered for normative use within the existing industry standards, such as life-cycle testing at temperature extremes, vibration requirements, and ultra-high-rate gas flow.
Compared with conventional applications, where a long history of experience in the design of completion products, acceptable temperatures, pressures and loading conditions is widely understood, the margin for error in HPHT is greatly reduced, and the consequences of product failure are more costly and far-reaching. HPHT conditions require special considerations for equipment design.
BACKGROUND
The principal current HPHT locations around the world are in the Gulf of Mexico, Latin America, North Sea, Norwegian Sea, Thailand and Indonesia. Although the number of HPHT exploration and production wells still represents a small percentage of overall E&P, exploration in HPHT environments continues to be a growing trend, as more conventional plays are depleted, and drilling technology allows new sources of energy to be discovered in deeper formations.
Some key challenges for the development of HPHT equipment include:
While the HPHT designation typically applies to all completion equipment rated higher than 15,000 psi or 350°F, it is particularly critical within subsurface safety valves. These valves must perform throughout a well’s life, an extremely challenging requirement when operating in HPHT environments. Safety valves serve as the emergency, fail-safe, flow-controlling safety device within the completion, so they have a number of unique drivers, design considerations and regulatory requirements, Table 1.
Table 1. Sub-surface safety valve technical challenges. |
|
ISO and API requirements for a subsurface safety valve state that it must be a device controlled from the surface by hydraulic, electrical, mechanical or other means. A minimum level of design verification and design validation is defined, both within ISO 10432 and ISO 10417, stating these specific requirements for the subsurface safety valve, itself, in addition to the subsurface safety system. The latter also includes the control line, flow couplings, locks and other downhole components.
Although the ISO and API documents provide the general design verification requirements, the new PER 15K recommended practice addresses further considerations for the design of HPHT equipment, including safety valves. As a result, the design of Tier 1, 2, and 3 HPHT valves needs further analyses, including things like elastic-plastic strains, fatigue, metallic and nonmetallic material characterization, and control fluid compatibility results.
Design, development and qualification testing. Design methodologies for hydraulically controlled safety valves and their components in conventional, non-HPHT applications have progressed to a point, where a new tool may require some additional attention in analysis or testing for a particular feature or capability, but the basic safety valve and its components are conceptually well-understood. Analysis and testing to validate the non-HPHT tool design, while not trivial, can border on routine, as existing test procedures and equipment are defined and accepted within ISO / API standards, as well as additional agreements between end user and supplier. This design verification and validation process has served the industry very well in the past for these non-HPHT applications.
Since the design of safety valves and their components for HPHT applications is not so commonplace, end-users and suppliers, alike, sense the need for additional analysis and testing techniques, as the HPHT pressure and temperature limits go beyond what has been done before. As a result, it is especially important to have clearly defined specifications and constant communication throughout the design and development process, to contribute to a successful project that produces a reliable, high-performance safety valve that is appropriate for this challenging environment.
Design for HPHT applications requires consideration of the temperature effects on the mechanical properties of the selected materials, and the distortion of components from applied HPHT loads. Data regarding temperature effects on mechanical properties for many alloys is readily available for temperatures up to 350°F, which covers Tier 1 applications. However, the change in properties is not perfectly linear, and the need for data on certain materials at 400°F and higher requires extensive materials testing. For those Tier 2 and 3 applications, this information is absolutely necessary to account for material yield strength losses at temperature. Additionally, environmental compatibility for these materials at Tier 2 and 3 temperatures is not as well understood. Therefore, material selection for these HPHT applications requires the additional time and expense to perform this testing early in the design process. Without the actual material derating properties, it is not possible to move forward in finalizing the design to optimize the inner/outer diameter relationship.
With the material characterization information, stress analysis of the HPHT design must go beyond traditional methods. As such, analysis tools, such as finite element analysis (FEA), can be used to reveal areas of localized plastic deformation. While this is also done in non-HPHT applications, the FEA analysis can become more involved for HPHT situations to evaluate the effects of those localized plastic strains. Fatigue-and-creep studies are processes that can provide additional design verification to reduce risk and improve reliability and performance. The safety valve housings and closure mechanisms, in particular, benefit from this level of study, especially those in Tier 2 and 3 applications. These higher pressures tend to result in elastic wall deflections in housings—deflections that may become considerable and need evaluation with respect to their mating components or internal threaded connections. If done early in the design process, with the appropriate tools and experience, this can reduce the need for a redesign effort during testing. Interestingly, within the overall safety valve design, the closure mechanism, itself, doesn’t present significant difficulties in design for these HPHT applications. Of course, additional pressure loads result in thicker, more substantial closure mechanisms, but their loading and performance is well understood. Only redundant or resilient seals for low-pressure sealing in the closure mechanism may need extra evaluation at Tier 2 and 3 temperatures.
The design and selection of nonmetallic materials for use in HPHT environments poses a difficult challenge, especially for seals. The materials may need to be compatible with any combination of assembly chemicals, control fluids, completion fluids and wellbore fluids, depending on exposure. The degree of compatibility between a nonmetallic material and a given chemical can change significantly at elevated temperatures and pressures. Qualification testing performed at the material and component level provide a level of confidence to proceed to the safety valve prototype test stage, but it is not a guarantee of trouble-free performance in the later testing stages. Vendor partnership and early communication of the design needs are crucial for success. As the high temperatures, especially in Tier 2 and 3, push these nonmetallic compounds to their extreme limits, there may be more likelihood for a more iterative process within the particular seal design and qualification.
In summary, design methodologies for HPHT safety valves are not monumentally different than those for non-HPHT valves. Instead, additional analysis techniques utilizing FEA, nonlinear plastic stress-strain reviews and fatigue-and-creep studies create confidence in the future reliability and performance of the product at this early design stage. Also, material characterization for metallics early in the design process leads to better optimization and confidence in the design, as well. Finally, seal design for HPHT applications can be quite challenging. This can be managed through careful study, communication, and some iteration, to develop the most robust sealing systems.
Once the design of the HPHT safety valve is finalized, the project’s first half is complete. The next phase of the development involves validation of the design or prototype testing. ISO and API standards require a minimum level of testing to validate a product, and for non-HPHT safety valves, suppliers complete these tests, and possibly some additional tests, as needed or required by an end-user. However, for HPHT products, it is preferred to provide an additional level of qualification testing to fully validate a product. This is due to the additional risks involved in HPHT environments. While there are no current requirements for a test program specifically designed for HPHT equipment, there are several validation tests that are recommended to demonstrate reliable product performance under the variety of anticipated loading conditions in the HPHT service environment.
One of the first things to consider for HPHT validation is control fluid selection and qualification. While there is a limited number of available and qualified fluids for Tier 1 type applications, there are few-to-none available for Tier 2 and 3 applications. As such, considerations for HSE, long-term thermal stability, viscosity and flash point data from the fluid supplier can serve as criteria for winnowing the options. The few remaining fluids must then be subjected to acceptance and compatibility testing at the appropriate pressures and temperatures, to evaluate their effects on nonmetallic sealing materials and metallic operating system components. Ideally, early selection of a control fluid can facilitate elevated temperature compatibility testing with the various other candidate materials.
In addition to control fluid qualification, a prototype validation program should include additional tests beyond ISO and API requirements. These tests should demonstrate such things as the anticipated life cycles of the product, the ability of the housings to handle the combinations of internal and external loads, and the ability of the closure mechanism to withstand violent closures against catastrophic openhole flow conditions. These are significant tests that validate the product to give a high level of confidence for reliable performance. The only additional considerations for these test programs may involve HSE or test facility limitations, especially for Tier 2 and 3 products. As such, additional scheduled time and effort may be required to set up facilities for the test program.
To demonstrate the ability of the HPHT safety valve to peform reliably over its anticipated life, a life-cycle test should be developed and completed successfully. This test should encompass performance of the product throughout its minimum to maximum temperature ratings, and maximum pressure ratings. Operating cycles should be performed throughout the test that are equivalent to, or greater than, the number of cycles anticipated for the life of the product in service. Throughout the test, both the operating system and closure mechanism should also be evaluated for integrity along the way. When completed successfully, this test lends a high degree of confidence to the reliable performance of the product.
Another important validation test to consider is a combined loading test. In this validation test, the body sections and internal threaded connections of the safety valve are evaluated under the combined effects of internal and external pressure, along with applied tension and compression. Typically, this test is completed at ambient temperatures, but for HPHT equipment, it is recommended that the loading evaluations be completed at the maximum rated temperature to provide additional confidence in performance. By completing this test with load points in all four quadrants of the valve operating envelope, success demonstrates that the valve body and internal connections can reliably contain wellbore fluids and gases under any anticipated loading scenarios.
One of the most crucial validation tests to complete is one that evaluates the closure mechanism during closure of the safety valve at very high flowrates. In these HPHT environments, the likelihood of high flowrates is greater, and the safety valve needs to demonstrate that it can close and still maintain pressure integrity to safely control the well. Typically, gas wells produce higher flow velocities and, therefore, the high-rate gas closure test is the preferred evaluation. In this test, gas flows are produced through the valve at sequentially higher velocities, and the valve is allowed to close against the flow. As the velocities reach rates above those anticipated by potential open-hole flow conditions, successful closures and maintainence of pressure integrity demonstrate that the product can reliably contain the well in the event of a catastrophe.
In summary, testing to qualify a tool design for an HPHT application requires careful attention to the specific temperature and loading cases, and anticipated duty cycle of the tool. While some basic tests will fall under the scope of existing regulatory requirements, it is certain that additional testing will be needed to fully prove the design. Final determination of the test program depends on the results of discussions and negotiations between the manufacturers, those conducting the tests, and the end-user. Consultation with the end-user regarding specific areas of potential concern and test acceptance criteria are crucial to developing a test program and individual test procedures that qualify the design to the satisfaction of all parties.
CONCLUSION
As the demand for products designed for HPHT applications increases, it will only be through the collective participation of end-users, service companies, and both material and testing vendors that practical solutions for real-world challenges and applications will be found. Organizations willing to participate and share their expertise will gain the knowledge and experience to unlock innovative step-change technologies that will allow for ultra-HPHT exploration and production in the future. 
ACKNOWLEDGEMENT This paper was prepared for presentation at the Offshore Technology Conference, held in Houston, Texas, April 30–May 3, 2012.
|